Understanding panel bender price is crucial for businesses looking to invest in this technology. The panel bender price can vary widely based on factors such as type, brand, specifications, and additional features. By comprehensively understanding these pricing dynamics, businesses can make informed decisions, ensuring they choose a panel bender that meets their production needs while aligning with their budget. This knowledge can lead to significant cost savings and increased operational efficiency in the long term.
What Is A Panel Bender
A panel bender is an advanced machine used in the sheet metal forming industry to bend and shape metal sheets into various forms. It serves a similar function to the traditional press brake but offers enhanced automation and additional features, making it a highly efficient and versatile tool for modern manufacturing processes.
Key Functions and Features
- Automated Bending: Unlike manual and semi-automatic bending machines, panel benders are designed for fully automatic operation, which significantly reduces the need for manual intervention.
- Precision and Accuracy: Panel benders can produce highly accurate bends with consistent quality, ensuring that the finished products meet exact specifications.
- Efficiency: The automation capabilities, including automatic loading and unloading of tools, feeding, measuring, bending, and outputting, contribute to higher productivity and faster production times.
- Versatile Bending Capabilities: These machines can perform complex bends such as crimping, offset bending, and forming flanges in multiple directions without leaving marks on the material, resulting in cleaner and more aesthetically pleasing workpieces.
- Specialized Tools: Panel benders can be equipped with special tools to handle a wide range of bending tasks, making them suitable for various applications.
Applications of Panel Bender Machine
Panel benders are valued for their accuracy, repeatability, and efficiency, making them essential in industries that require high-quality metal forming.
- Automotive Industry:
- Fabricating parts for car bodies, chassis, and other components.
- Producing complex geometries required for modern vehicle designs.
- Appliance Manufacturing:
- Creating parts for household appliances such as refrigerators, ovens, and washing machines.
- Ensuring consistent and precise bends for better assembly and functionality.
- Electronics and Electrical Enclosures:
- Manufacturing enclosures for electronic devices and electrical panels.
- Ensuring tight tolerances and clean bends for effective protection and aesthetic purposes.
- HVAC Industry:
- Producing components for heating, ventilation, and air conditioning systems.
- Bending metal sheets for ducts, panels, and other HVAC parts.
- Furniture Production:
- Crafting metal parts for furniture frames, legs, and supports.
- Creating intricate designs and maintaining structural integrity.
- Aerospace Industry:
- Fabricating lightweight and strong components for aircraft and spacecraft.
- Meeting the high precision and quality standards required in aerospace applications.
- Construction and Architecture:
- Producing panels and parts for building facades, roofing, and structural components.
- Enabling custom architectural designs with precise metal bends.
- Signage and Display Manufacturing:
- Creating metal frames and supports for signs and displays.
- Allowing for custom shapes and designs for branding and informational purposes.
- Industrial Equipment:
- Manufacturing parts for machinery, industrial enclosures, and equipment housings.
- Ensuring durability and precision for industrial applications.
- Custom Fabrication Shops:
- Providing custom bending services for various projects and clients.
- Meeting diverse needs from small prototypes to large production runs.
Development History Of Panel Bender
In Europe and the United States, businesses often face significant human resources costs, particularly in Northern Europe where labor expenses are notably high. Consequently, these companies prioritize enhancing production efficiency and reducing labor reliance. Over the years, many have adopted automated and intelligent systems, increasingly investing in advanced machinery and unmanned production lines to mitigate these costs.
The introduction of the world's first P4 panel bender by Salvagnini in 1977 marked a significant milestone in this regard. This innovative machine featured universal bending tools and robotic integration, pioneering flexible and automated sheet metal forming technology. Salvagnini's P4 panel bender transformed the industry by offering a solution that greatly improved production efficiency and reduced the need for manual labor.
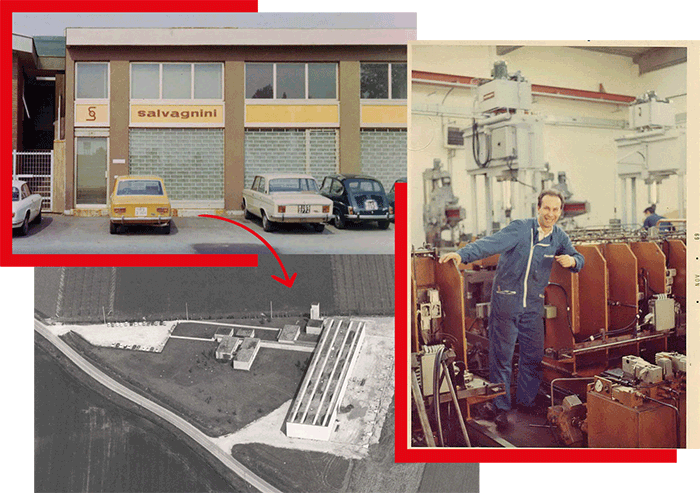
Evolution of Metal Bending: From Manual to Automated Panel Benders
In the past, metal bending relied heavily on manual bending machines. However, as technology has advanced, the field of sheet metal forming has embraced automation. Today, sheet metal bending can be categorized into manual bending, semi-automatic bending, and fully automatic bending centers. The advent of automatic tool changing systems and measuring systems has significantly enhanced the efficiency of metal bending processes.
A notable innovation in this field is the panel bender, which offers similar functionalities to the traditional press brake but with more automation and advanced features. The panel bender's blade can form flanges horizontally while the blank holder keeps the material stable in another direction. This machine uses standard bending blades capable of producing various radii, and the bending process leaves no marks on the material. Consequently, the resulting workpieces are more aesthetically pleasing and cleaner compared to those produced by a press brake.
The panel bender stands out due to its labor-saving and high-speed capabilities. It can perform fully automatic bending processes, including automatic loading and unloading of tools, feeding, measuring, bending, and outputting. With a short bending stroke and fast feeding speed, the panel bender produces highly accurate workpieces. Additionally, it can utilize special tools for complex bends such as crimping and offset bending.
Despite its advantages, the panel bender is not suitable for all types of workpieces. It excels in producing box-type workpieces, as it can bend the sides of an entire box simultaneously. While modern automation allows both panel benders and press brakes to be connected to robots for full automation, they do not match the comprehensive capabilities of a robot bending center.
How Does Panel Bender Work
Panel benders utilize advanced technology and automation to efficiently bend and shape metal sheets. Understanding their operation involves an exploration of their key components and the sequential process by which they perform bending tasks.
Components of a Panel Bender
- Blade: The blade of the panel bender is responsible for bending the metal sheet. It can form flanges horizontally, and its movement is controlled by the machine's programming.
- Blank Holder: The blank holder stabilizes the metal sheet during the bending process, preventing it from shifting or buckling.
- Control System: The control system of the panel bender manages the machine's operations, including tool changing, feeding, measuring, and bending, ensuring precise execution of bending tasks.
- Specialized Tools: Panel benders can be equipped with various specialized tools to perform specific bending tasks, such as crimping and offset bending.
Operation Process
- Material Preparation: The metal sheet to be bent is loaded onto the panel bender's work surface.
- Programming: The operator inputs the bending specifications, including dimensions, angles, and bend sequences, into the machine's control system.
- Tool Setup: If necessary, the panel bender automatically selects and sets up the appropriate bending tools based on the programmed specifications.
- Feeding: The machine's feeding mechanism positions the metal sheet accurately beneath the bending blade and blank holder.
- Bending: The bending blade moves horizontally, exerting pressure on the metal sheet against the blank holder. This action causes the metal sheet to bend according to the programmed specifications.
- Unloading: Once the bending process is complete, the finished workpiece is automatically unloaded from the panel bender's work surface.
Automation and Precision
Panel benders excel in automation and precision, offering several advantages over traditional bending methods:
- Fully Automatic Operation: Panel benders can perform bending tasks without manual intervention, resulting in higher productivity and reduced labor costs.
- High Accuracy: The machine's control system ensures precise execution of bending tasks, resulting in consistent quality and dimensional accuracy of the finished workpieces.
- Reduced Setup Time: The automated tool changing system and programming capabilities streamline the setup process, minimizing downtime between bending tasks.
Configuration of Panel Bender and Parameters
NO. | Functions | Descriptions |
1 | High-grade Cast machine body | High-grade QT500-7 and gray iron 250 castings are used to effectively ensure stability under high tonnage impact forces |
2 | Multi-axis synchronization control system | Self-developed multi-axis synchronization numerical control system. It precisely realizes the perfect matching of concurrent linkage of allaxes of the equipment, running smoothly and naturally. Its comprehensive speed reaches the highest efficiency in the industry. Perfect acceleration control, smaller machine body vibration, and prolong the machine parts life time as well. Self-designed hardware circuit board with no welding, and immersion gold surface treatment. |
3 | Advanced Instructions | Users can customize the design and control of complex workpieces according to their needs. |
4 | Arc command | Call the arc command directly and input the radius to realize the bending of the arc |
5 | Y-axis double-lift five-foot positioning | Y-axis double-lift five-foot positioning. Avoid positioning errors caused by manual positioning, with higher accuracy |
6 | Error-proof inspection of metal panel | When the metal sheet is used incorrectly, the system will automatically give an alarm, which can effectively avoid the damage to the machine due to the wrong use of metal size and type. |
7 | Oil supply self-lubricating system | Automatic alarm for oil shortage to ensure safe operation of the machine |
8 | Unbalanced load detection system | When the pressing tool press down, there are foreign objects at the bottom or other conditions that cause the two sides of the pressing tools to be not on the same horizontal line. At this time, the system warns and terminates the operation to effectively protect the mechanical structure. |
9 | Panel thickness detection system | The thickness of the workpiece is detected in real time during the pressing process of the pressing tool. When the actual thickness is inconsistent with the programmed thickness, the system will immediately terminate and give an alarm. |
10 | Graphical visualization error detection programming | The user only needs to input the bending size and instructions, the system automatically completes the programming and displays the molding results, and the user can compare to ensure consistency. |
11 | Automatic loading and unloading control module | The system reserves wide ranges of Industry 4.0 interfaces, which can be connected to the robotic arm to realize automatic loading and unloading. Equipped with the self-propelled integrated mechanical arm which use the same control system with the bending center. No secondary programming is required when change the workpiece. The system automatically generates the robotic arm movements command according to the bending instructions, with higher efficiency and better coordination. |
12 | High-speed control module | The system can realize collaborative work under high-speed operation |
13 | Flattening function | Flatten the workpiece |
14 | Press the dead edge up and down | Realize the dead edge of the workpiece up and down |
15 | Handle controller | The system has an anti-collision tool function, and the user can control each axis to any desired position through the handle controller. |
16 | Cloud end operation and maintenance management interface | It can be connected to the enterprise operation and maintenance management system to detect the operation of the machine in real time, and can carry out all-round customized management of the company's business |
17 | Automatic production line interface | It can be connected with upstream and downstream production equipment to realize automatic production |
What Are Types of Panel Bender
A panel bender is a type of machine that helps in the process of bending sheet metal. There are various types of panel benders available in the market, each with its own unique features and advantages.
Manual Panel Benders: These are the simplest form of panel benders, requiring manual operation and control. Ideal for smaller workshops or low-volume production, manual panel benders offer simplicity and affordability. However, they do require skilled operators and are not as efficient for large-scale production.
Semi-Automatic Panel Benders: Offering a blend of manual and automated features, semi-automatic panel benders reduce the need for constant manual intervention. They are equipped with some automated controls for bending operations, making them suitable for medium-scale production with improved accuracy and speed.
Fully Automatic Panel Benders: At the forefront of technology are fully automatic panel benders. These machines are designed for high-volume production, offering the highest level of precision and efficiency. With advanced programming capabilities, they can handle complex bending tasks with minimal human intervention, significantly boosting productivity.
CNC Panel Benders: CNC (Computer Numerical Control) panel benders represent the pinnacle of panel bending technology. These machines are fully automated and controlled by computer programs, allowing for intricate and precise bends with high repeatability. CNC panel benders are ideal for industries requiring high precision and customization in their panel bending tasks.
What Is Panel Bender Price
Panel benders are invaluable assets for businesses needing precise bends on various materials like steel and aluminum. Their popularity is soaring due to their ability to streamline bending processes. So, what's the price tag on these machines?
The cost of a panel bender hinges on its quality, specifications, and brand. While simpler models can start at around $1,500, more advanced ones with specific features can range from $25,000 to well over $100,000.
Panel benders differ in functionality, especially regarding the thickness and width of the material they handle. Smaller machines are adept at bending thinner metal sheets, while larger and more specialized ones tackle thicker and wider sheets. Accordingly, prices vary based on these factors.
Beyond the machine itself, there are other financial considerations like warranties, installation, training costs, and post-purchase service. Opting for a cheaper machine might lead to unforeseen expenses, such as frequent maintenance or part replacements down the line.
Before committing to a purchase, thorough research is crucial to find a machine that aligns with the business's requirements and budget. Seeking insights and advice from industry experts and manufacturers can be invaluable.
Why Panel Bender Price Is Higher Than Press Brake
Both press brakes and panel benders are used for bending sheet metal, they differ in terms of their versatility, specialization, design, applications, and precision. Press brakes are more versatile and suitable for a wide range of bending tasks, while panel benders excel at folding large and thin panels with complex geometries. Panel benders generally command higher prices compared to press brakes, before figure out why panel bender price is higher, we should learn about the differences between them.
Differences Between Panel Bender and Press Brake
Efficiency and Operator Requirements
Panel Bender:
The panel bender stands out for its efficiency, both in terms of hourly workpiece production and the quality of each bend. It excels at swiftly producing small batches or entire sets of precision workpieces.
With its streamlined design, the panel bender requires fewer personnel compared to the press brake. A semi-automatic panel bender can be managed by a single operator, while the fully automatic variant eliminates the need for personnel altogether.
Operators of panel benders typically only need to handle workpiece loading and unloading, resulting in lower operator requirements and smoother production flow.
Press Brake:
In contrast, operating a press brake often demands multiple personnel and may even necessitate robotic assistance for optimal performance.
The press brake's reliance on manual adjustments after each bending cycle adds complexity and can slow down production compared to the automated processes of panel benders.
Capabilities and Flexibility
Press Brake:
Press brakes offer a wide pressure range, from 40 tons to several thousand tons, catering to diverse bending needs. However, they typically feature a lower degree of automation compared to panel benders.
They boast capabilities such as angle correction, automatic tool change, and deflection compensation, enhancing their versatility in handling various tasks.
While press brakes offer flexibility in modifying workpieces according to design drawings, achieving satisfactory results may require longer setup times compared to panel benders.
Panel Bender:
Panel benders operate based on the thickness of the sheet metal rather than tonnage. They involve positioning the workpiece on the centerline and bending each side after positioning from all four sides.
With a bending tolerance of 0.008 inches, panel benders produce highly precise and easily assembled workpieces, particularly those requiring sliding or snapping together.
Panel benders feature minimal setup times and can automatically adapt to the shape of the sheet metal, streamlining the production process.
Bending Process
Press Brake:
The press brake utilizes an upper die set and a corresponding lower die set, typically in a V shape. Driven by pressure, the upper die presses the metal plate into the lower die, completing a single bend.
The size of the V-shaped die opening varies based on factors such as plate thickness, bending radius, and angle.
Over time, the press brake's tooling will experience wear and require replacement, adding to maintenance costs.
Panel Bender:
In contrast, the panel bender employs upper and lower blades along with a blank holder for the bending process. The panel bender's counter blade aids in securely holding the metal plate during bending.
A notable feature of the panel bender is the blank holder's ability to assist the blade in clamping the plate, enabling flexible and precise bending.
The upper and lower blades, counter blades, and blank holder of the panel bender operate without the need for manual stopping or adjustment. They are automatically controlled throughout the entire bending process based on the thickness and shape of the sheet metal.
Bending Quality
Challenges with Press Brake:
Bending metal plates with a press brake can present challenges such as wrinkles or kinks, particularly when bending backward. The process of pressing the plate into the lower die using the punch can also result in scratches on the plate surface, especially with coated plates.
Prolonged use of the press brake can lead to wear and tear on the mold, necessitating regular replacement. Moreover, when bending large plates, operators may struggle to keep up with the bending speed, resulting in material waste.
Advantages of Panel Bender:
In contrast, the panel bender offers a higher degree of automation, accuracy, and repeatability compared to the press brake. Its sensors can automatically adjust the bending force and angle based on changes in temperature and material thickness. This ensures consistent and precise bending results, minimizing the risk of defects or material waste.
Advantages of Panel Bender Over Taditional Press Brake
Automation and Precision: Panel benders are highly automated machines designed to perform complex bends with minimal manual intervention. They often feature advanced CNC systems, robotic handling, and automated tool changers, which enhance precision and efficiency but also increase the cost.
Production Efficiency: Panel benders can perform multiple bends in a single handling of the workpiece, which significantly speeds up the production process. This efficiency is particularly valuable in high-volume production settings, making the initial investment more justifiable for large-scale operations.
Versatility and Capability: These machines are capable of producing complex bends that might be challenging or impossible for traditional press brakes. This versatility makes panel benders suitable for a wider range of applications, especially in industries that require intricate metal forming.
Advanced Features: Panel benders often come with a range of advanced features, such as automatic angle correction, intelligent bending sequences, and integration with CAD/CAM software. These features enhance the machine's functionality and contribute to higher accuracy and consistency in the final products.
Reduced Labor Costs: The high level of automation in panel benders reduces the need for skilled labor. Operators can oversee multiple machines or focus on other tasks, leading to overall savings in labor costs over time.
Quality and Durability: The construction and engineering of panel benders often involve high-quality materials and components to ensure durability and long-term performance. This build quality contributes to their higher price but also ensures a longer service life and lower maintenance costs.
Market Demand and Niche Applications: Panel benders cater to specific industries and applications where precision and efficiency are critical. This niche demand can drive up prices, as the machines are tailored to meet the stringent requirements of sectors like aerospace, automotive, and high-end manufacturing.
Top Rated Manufactures, Best Panel Bender Price
Salvagnini is a leading manufacturer known for its innovative and highly automated panel benders. Their machines are renowned for flexibility and efficiency, capable of handling various material types and complex bending requirements. Salvagnini's B3 series, for instance, offers high precision and versatility, making it a top choice in the market .
Amada is another prominent name, offering a range of high-quality panel benders like the EP-2500. Amada focuses on maximizing production speed and efficiency, with features like automated tool changes and a robust frame design that allows for bending thicker materials. Their machines are designed to handle complex shapes and offer extensive automation options
Prima Power offers advanced panel benders that are praised for their speed, accuracy, and ease of use. Their panel bending solutions are designed to reduce setup times and improve production throughput, making them suitable for a variety of industrial applications
Artizono provides panel benders that emphasize precision and reproducibility. Their machines, like the 2500P model, are capable of fast and accurate automated bending, making them ideal for mass production. Artizono is known for its user-friendly interfaces and high degree of automation
Krrass Machinery offers competitive panel benders with advanced features like servo electric drives and multi-axis control systems. Their PB series is noted for its high precision, productivity, and cost-effectiveness compared to some high-end competitors.
How To Choose A Right Panel Bender
Selecting the right panel bender for your specific needs can be a daunting task, given the variety of options available in the market. In this comprehensive guide, we’ll walk you through the essential considerations and steps to help you choose the perfect panel bender for your fabrication requirements.
Understanding Your Fabrication Needs
Assessing the Type and Volume of Work:
Understanding your fabrication needs begins with a thorough assessment of the type and volume of work you’ll be handling. Consider whether your projects primarily involve small-scale production runs, custom one-off pieces, or high-volume manufacturing. This assessment will help you determine the level of automation, precision, and throughput required from your panel bender.
Identifying the Materials and Specific Requirements:
Different materials present unique challenges in panel bending, so it’s essential to identify the types of materials you’ll be working with. Whether you’re bending aluminium, stainless steel, mild steel, or other alloys, each material has its own characteristics that influence bending capabilities and techniques. Additionally, consider any specific requirements such as tight tolerances, complex geometries, or surface finishes that may impact your choice of panel bender.
Considering Workflow Constraints and Preferences:
Take into account your workflow constraints and preferences when selecting a panel bender. Evaluate factors such as available floor space, layout efficiency, and ergonomic considerations to ensure seamless integration into your fabrication process. Consider whether you require a standalone machine or a fully automated cell with material handling and auxiliary equipment. Understanding your workflow preferences will help you choose a panel bender that optimizes productivity and minimizes downtime.
Assessing Panel Bender Capabilities
Bending Capacity and Material Thickness Capabilities:
One of the primary considerations when assessing panel bender machines is their bending capacity and material thickness capabilities. Different machines are designed to handle varying levels of bending force and material thicknesses. It’s crucial to match the machine’s capacity with the requirements of your fabrication projects. Whether you’re bending thin gauge sheets or thick plates, choose a panel bender that can accommodate the material thicknesses you commonly work with to ensure optimal performance and efficiency.
Bend Accuracy and Repeatability:
Another critical aspect of machine capabilities is bend accuracy and repeatability. Precision is paramount in sheet metal fabrication, especially when producing complex parts with tight tolerances. Evaluate the machine’s ability to achieve consistent bend angles and dimensions across multiple parts. Look for features such as advanced CNC controls, back gauge systems, and precision tooling that contribute to superior bend accuracy and repeatability. A panel bender with excellent precision will help minimize rework and ensure the quality of your finished products.
Versatility in Handling Various Sheet Metal Sizes and Shapes:
A versatile panel bender is essential for accommodating a wide range of sheet metal sizes and shapes. Consider the flexibility of the machine’s tooling and bending capabilities to handle diverse fabrication requirements. Look for machines that offer quick and easy setup for different part geometries, as well as the ability to switch between bending operations efficiently. Whether you’re producing simple straight bends or complex multi-bend parts, choose a panel bender that offers the versatility to meet your evolving needs without compromising on quality or efficiency.
Additional Features Such as Automation and CNC Controls:
Beyond basic bending capabilities, consider the additional features and technologies offered by panel bender machines. Automation features such as robotic part loading and unloading, automatic tool changing systems, and integrated bending cells can significantly enhance productivity and efficiency in your fabrication workflow. Similarly, advanced CNC controls with intuitive user interfaces, simulation capabilities, and programming flexibility provide greater control and customization options for optimizing bending processes. Evaluate the available features and functionalities to determine which ones align best with your specific fabrication needs and workflow requirements.
Determining Space and Budget Constraints
Evaluating Available Workspace:
When determining space constraints for your panel bender, start by evaluating the available workspace in your facility. Measure the dimensions of the area where the machine will be located, taking into account clearance requirements for safe operation and maintenance. Consider factors such as aisle space, access to utilities (such as power and compressed air), and proximity to other machinery or workstations. Ensuring adequate space for the panel bender will promote efficient workflow and minimize disruptions in your fabrication process.
Setting a Realistic Budget Based on Financial Resources and Expected ROI:
Setting a realistic budget is essential when investing in a panel bender. Consider your financial resources and cash flow projections to determine the maximum amount you can afford to spend on the machine. Factor in not only the initial purchase price but also ongoing operating costs, such as maintenance, tooling, and energy consumption. Additionally, assess the expected return on investment (ROI) from the panel bender in terms of increased productivity, reduced labor costs, and improved product quality. Balancing your budget constraints with the expected ROI will help you make a financially sound investment decision.
Exploring Financing Options and Lease Agreements:
If budget constraints pose a challenge, explore financing options and lease agreements to spread out the cost of acquiring a panel bender over time. Many manufacturers and equipment suppliers offer flexible financing solutions tailored to meet the needs of small businesses and startups. Evaluate different financing plans, lease terms, and interest rates to find the most favourable arrangement for your budget and cash flow situation. Leasing can be a cost-effective way to acquire the equipment you need while preserving capital for other business expenses.
Considering Long-Term Cost Savings and Benefits:
While upfront costs are an important consideration, don’t overlook the long-term cost savings and benefits associated with investing in a quality panel bender. A higher initial investment in a reliable and efficient machine may translate into lower operating costs, reduced downtime, and higher productivity over the machine’s lifespan. Consider factors such as energy efficiency, maintenance requirements, and durability when comparing different panel bender options. Investing in a machine that offers long-term value and performance can ultimately yield greater returns and contribute to the success of your fabrication business.
Introduction To Krrass Panel Bender
As the leading panel bender manufacturer in China, KRRASS always provide the best panel bender machine to manufacturers around the world. A panel bender machine is a piece of equipment used in the manufacturing and fabrication industries to bend and shape sheet metal or other flat materials into various shapes and configurations. These machines are commonly used in industries such as HVAC (Heating, Ventilation, and Air Conditioning), automotive, aerospace, and general metalworking.
We equip the machine with a suction cup design that enables sheet metal fabrication with a maximum bending size of 2000mm x 2000mm. Its remarkable bending speed of only 0.2 seconds per bend significantly enhances productivity and helps reduce labor expenses.
KRRASS Servo electrical fully-automatic panel bender machine
The intelligent CNC automatic panel bender machine/press brake machine is equipment for processing thin plates. The machine’s structure mainly includes a tool holder, a worktable, a clamping feeding device, and a CNC operating table. The machine’s worktable comprises a base and a clamping piece feeding structure.
- Rotary part manipulator: The rotary part manipulator secures the blank and rotates it to the required position completely independently.
- Two axes, limitless possibilities: The 2-axis part manipulator positions the sheet metal and even enables negative bends.
- Precise angles: First part, perfect part – with the ACB laser
- Programming in the blink of an eye: The easiest and fastest offline programming among panel benders: TecZone Fold.
- Integrated tool change: Set up the right upper blank holder tools automatically with the integrated tool changer ToolMaster Bend.
- Every component under control: Various gripper systems help to hold the components.
- Automatic loading and unloading: Higher productivity due to loading and unloading that is parallel to production.
- On-Demand Servo Drive: The on-demand servo drive works quickly, quietly, and in an energy-efficient way.
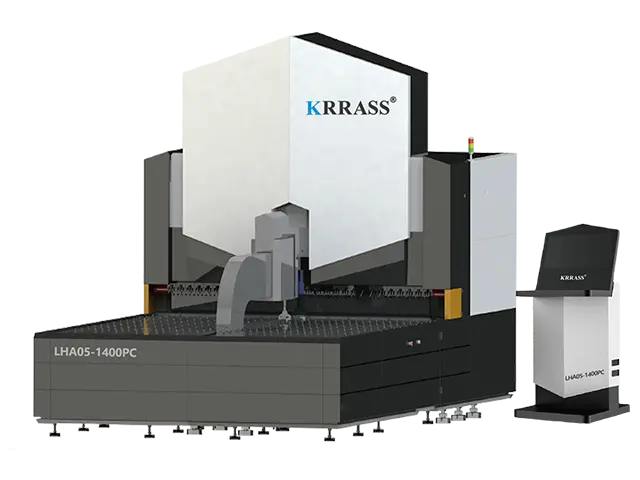
Model | RAS-1500/RAS-2000/RAS-2500 |
---|---|
Minimum continuous bending speed | 0.5s/knife |
Bending thickness | 201 stainless steel 0.8mm, 304 stainless steel 1.0mm cold steel 1.2mm, aluminum steel 1.6mm |
Max bending length(mm) | 1500/2000/2500 |
Max bending height(mm) | 170 |
Min molding size of four sides (mm) | 280*280 |
Bending angle | 0-180 |
Max feeding speed(m/min) | 120 |