In the intricate landscape of modern manufacturing and fabrication, one indispensable tool stands out – the press brake machine. Whether you're shaping metal sheets with precision or bending them to exact specifications, the press brake machine is the silent hero behind countless products we encounter in our daily lives.
Modern press brakes have increased automation and CNC controls, allowing for greater precision and repeatability compared with traditional machines. It’s not unusual for contemporary devices to come with multi-axis computer-controlled back gauges, optical sensors, and programmable controls that use real-time data to inform the machine when to make adjustments without an operator needing to intervene.
Introduction To Press Brake Machines
What is a Press Brake Machine?
A press brake is a fabrication machine that shapes metal sheet and plate. It works by creating predetermined bends in material placed between an upper and lower die. Force is applied to the die and the metal bends at the desired point. Depending on the machine and the type of die being used, there are a variety of shapes that can be created.
The basic design of most press brake machines starts with a robust press frame made up of two outside uprights, a worktable across the bottom and connecting plate across the top. There are two tools, one attached to the table and the other attached to the ram. The ram consists of a whole steel plate positioned above the worktable between the uprights; the upper die is attached to the ram’s lower edge and cycles downward to force the workpiece into the lower die and initiate the desired angle. A press brake is usually described by the type of force that’s being applied; there are mechanical, pneumatic, hydraulic and servo-electric press brakes.
Lorem ipsum dolor sit amet, consectetur adipiscing elit. Ut elit tellus, luctus nec ullamcorper mattis, pulvinar dapibus leo.
Basic Understanding About Typical Press Brakes
(1) A mechanical press brake, which was the most popular option until the 1950’s, uses a flywheel with an electric motor. The operator employs a clutch that engages the flywheel and powers the crank mechanism forcing the ram down. Mechanical presses offer both speed and accuracy, making them an efficient machine for simpler jobs.
(2) A hydraulic press brake employs two synchronized hydraulic cylinders that are attached to the uprights and move the ram. A servo-electric press has a servomotor that propels a ball screw or belt drive, which then applies pressure to the ram. Finally, a pneumatic press operates thanks to air pressure that forces the ram into the workpiece.
(3) Among modern machines, pneumatic and servo-electric press brakes are best suited for applications that require a lower amount of force. Hydraulic press brakes are extremely accurate and do not consume a lot of energy, making them a good option when sustainable operations are a priority. Another benefit is that the action of the ram can be halted on command, making them extremely safe.
(4) Modern press brakes have increased automation and CNC controls, allowing for greater precision and repeatability compared with traditional machines. It’s not unusual for contemporary devices to come with multi-axis computer-controlled back gauges, optical sensors, and programmable controls that use real-time data to inform the machine when to make adjustments without an operator needing to intervene.
What Types of Dies Can Be Used With Press Brakes?
In addition to the different types of mechanics, a great deal of variety in press brake metal fabrication comes from the type of die that is employed. The most common dies are known as V-dies, in which the bottom of the die has a V-shaped depression. V-dies can come in many different sizes and angles, allowing for a wide diversity of finished bends. machines are the silent enablers behind the creation of everything from sleek car bodies to aerodynamic aircraft components. Other types of dies include the following:
- Rotary bending dies
- 90 degree dies
- Acute angle dies
- Gooseneck dies
- Offset dies
- Hemming dies
- Seaming dies
- Radius dies
- Beading dies
- Curling dies
- Tube- and pipe-forming dies
- Four-way die blocks
- Channel-forming dies
- U-bend dies
- Box-forming dies
- Corrugating dies
- Multiple-bend dies
- Rocker-type dies
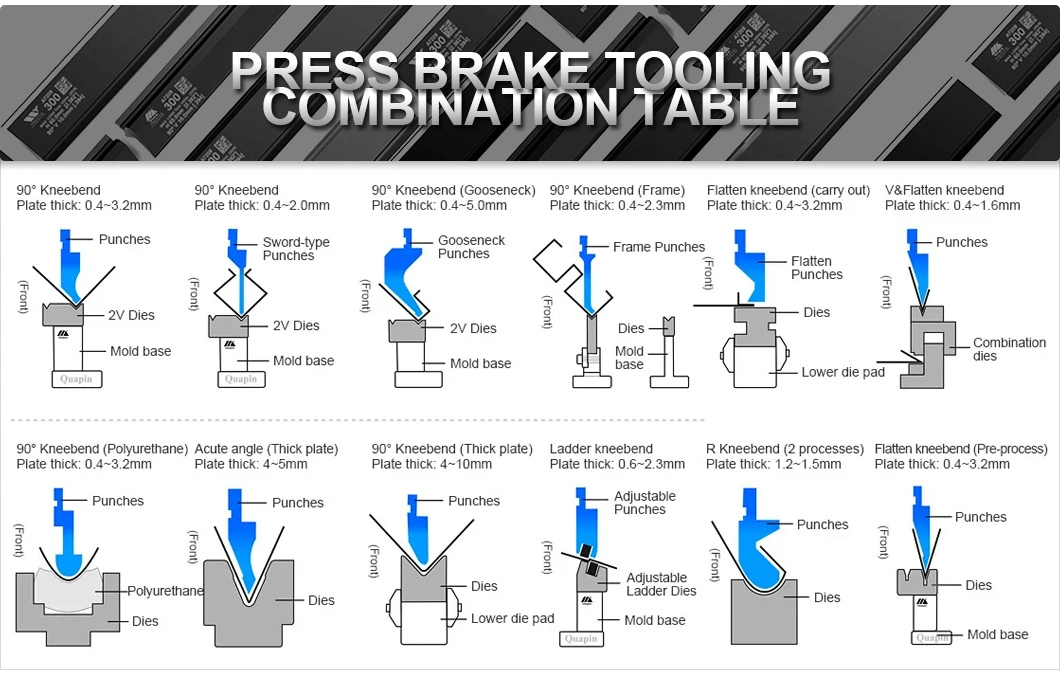
Functionalities and Applications of Press Brakes
Unveiling the Versatility of Precision Bending
1. Precision Bending:
Press brakes excel in precision bending, offering unmatched accuracy in shaping metal sheets to desired angles and dimensions. With hydraulic or mechanical force, they exert controlled pressure on the workpiece, guiding it through precise bends to achieve intricate shapes and profiles.
2. Versatile Tooling Options:
One of the key strengths of press brakes lies in their adaptability to various tooling options. By interchangeably using punches and dies of different sizes and shapes, operators can customize bending operations to suit specific requirements, from simple bends to complex forms.
3. High-Speed Production:
Press brakes boast impressive speed capabilities, enabling rapid production of bent components with minimal downtime. Whether it's high-volume manufacturing or just-in-time production, these machines offer the agility and efficiency needed to meet demanding production schedules.
4. Forming Complex Geometries:
Beyond standard bends, press brakes are adept at forming complex geometries with multiple bends and curves. With the right tooling and programming, operators can achieve intricate designs and contours, unleashing creative possibilities in product design and manufacturing.
5. Consistency and Accuracy:
Consistency is key in manufacturing, and press brakes deliver on this front with remarkable precision and repeatability. Advanced CNC controls ensure that each bend is executed with consistent accuracy, minimizing deviations and ensuring uniformity across production runs.
Applications Across Industries
1. Automotive:
Press brakes play a crucial role in automotive manufacturing, forming structural components such as chassis frames, body panels, and brackets with precision and reliability.
2. Aerospace:
In the aerospace industry, press brakes are used to fabricate intricate components for aircraft structures, including fuselage sections, wing ribs, and landing gear parts.
3. Construction:
Press brakes contribute to the construction sector by shaping metal components for architectural structures, including beams, columns, and façade elements, with tailored precision.
4. Electronics:
In electronics manufacturing, press brakes are utilized to produce casings, enclosures, and mounting brackets for various electronic devices, ensuring both functionality and aesthetics.
5. Machinery and Equipment:
From heavy machinery to precision instruments, press brakes are instrumental in fabricating components that form the backbone of industrial equipment, ensuring durability and performance.
Benefits of a Press Brake in Metal Fabrication
1.Increased Efficiency
One of the most important advantages of using a press brake in metal fabrication is increased efficiency. With less manual labor required and quicker production times, press brakes are intended to speed up the metal fabrication processes. This translates into the ability to produce more goods in less time, increasing productivity and cost savings.
The quick and precise bending of metal sheets into desired shapes is one way press brake robot increase productivity. Traditional metal fabrication techniques, like hand bending with hammers and blocks, can be labor-intensive and time-consuming. On the other hand, a press brake can bend metal sheets consistently and precisely, lowering the need for manual labor and raising production efficiency.
Press brakes can perform multiple tasks, which is another way they boost productivity. In order to further decrease the need for manual labor and boost production efficiency, press brakes can be used for a variety of tasks like punching, shearing, and forming. Metal fabricators can perform multiple tasks with just one machine thanks to its versatility, which lowers the need for additional equipment and boosts output.
2.Precision
Precision is one of the main benefits of using a press brake when fabricating metal. The likelihood that the products produced by press brakes will meet customer requirements and industry standards is higher because they are designed to deliver precise and consistent results.
Using computer-aided design (CAD) software is one way press brakes offer precision. With the help of this software, metal fabricators can enter precise dimensions and angles for the desired product, and the press brake will use this data to bend the metal sheets precisely. By doing this, the possibility of human error that can happen when manually measuring and bending metal sheets is eliminated.
3.Versatility
Using computer-aided design (CAD) software is one way press brakes offer precision. With the help of this software, metal fabricators can enter precise dimensions and angles for the desired product, and the press brake will use this data to bend the metal sheets precisely. By doing this, the possibility of human error that can happen when manually measuring and bending metal sheets is eliminated.
- Bending is one of the main tasks that press brakes are useful for. Metal sheets can be bent into precise shapes and angles using press brakes and a punch and die. By applying pressure to the metal sheet, the desired line is bent along as a result of the bend. Press brakes are adaptable tools for metal fabrication because they can be used to bend a variety of materials, such as steel, aluminum, and copper.
- Punching is yet another task that press brakes are useful for. A punch tool that is used to punch holes in metal sheets can be added to press brakes. This is accomplished by pushing the punch tool through the metal sheet by applying pressure to it. Press brakes are adaptable tools for metal fabrication because they can be used to drill holes in a variety of materials, such as steel, aluminum, and copper.
- Another task that press brakes can be used for is shearing. A shear tool that is used to cut metal sheets into specific sizes can be added to press brakes. By exerting pressure on the shear tool, which cuts through the metal sheet, this is accomplished. Press brakes are adaptable machines for metal fabrication because they can be used to shear a variety of materials, such as steel, aluminum, and copper.
4.Cost Savings
The cost savings of using a press brake in metal fabrication is one of the main benefits. Press brakes can reduce the need for manual labor and increase production efficiency, which can lead to long-term cost savings. Because fewer workers are required to produce the same amount of product, costs are reduced. The versatility of press brakes minimizes the need for additional equipment and maximizes cost savings.
5.Improving safety
These machines have safety features like sensors and guards that shield the operators from potential dangers, lowering the possibility of accidents and injuries. This is particularly crucial in the fabrication of metal, where there are numerous potential dangers like sharp edges, large machinery, and high-pressure tools.
Additionally, press brakes permit a high degree of customization. These devices can be set up to accommodate a metal fabrication shop’s unique requirements, regardless of the sector or application. This enables metal fabricators to create products that precisely match the requirements of their clients, increasing client satisfaction and encouraging repeat business.
Last but not least, press brakes are renowned for their longevity and robustness. These devices are long-lasting and can produce high-quality goods for many years with the right maintenance. For small and medium-sized metal fabrication shops, this can be especially advantageous as it reduces the need for pricey replacements.
Factors To Consider When Choose A Press Brake Machine
There are many factors to consider before purchasing a bending machine. Below I will provide some practical guidelines from the most basic aspects.
How To Select A New Press Brake
- Tonnage: This is referred to as the bending capacity of a press brake. Hence, is the most important consideration to be made while selecting the press brake for your facility:
- Type of Material
- Thickness of Material
- Length of the Material
- Process Employed
- Die Opening
If you are unable to calculate the tonnage of the machine then it is always better to approach the manufacturer whom you are considering. They will help you calculate the bending force of every task.
- Length of the Material to be Processed: Next, consider the maximum length of the sheet metal to be processed. If you wish to bend the sheet metal by employing multiple stations on the press brake then you need to alter the length of each station. For maximum efficiency, you can select a press brake that allows you bending short and long sides effectively through two stations. This will reduce your processing time.
- Daylight or Open Height: The choice of open height will depend on several factors such as the type of metal bending to be performed, the sheet metal bending tools used, and the stroke needed for the activity. For instance, if a customer is using a press brake with standard daylight, he may find difficulties to move the finished part while bending flanges that are large in size.
- Deflection: You must consider the deflection that a machine may undergo. For instance, a 5-foot machine will endure four times less deflection in the ram and bed than a 10-foot machine when subjected to the same load.
In addition to the above-mentioned factors, it is important to check on other factors such as the desired angular accuracy, type of tooling used, flange width, and the workpiece used. By now you might have understood how a press brake can be an asset to your facility. Hence, it is important that you source it from a reliable manufacturer or supplier.
TOP 10 Goloble Press Brake Machine Manufactures
No. | Manufacturer | Features | Location | Established |
1 | Amada | High-tech, high-quality machines offering hydraulic, electric, and hybrid press brakes. | Kanagawa, Japan | 1946 |
2 | Trumpf | Global leader in industrial machine manufacturing, focused on automation and efficient precision press brakes. | Ditzingen, Germany | 1923 |
3 | Bystronic | Innovative press brakes with user-friendly interfaces and cutting-edge technology for high performance and precision. | Niederönz, Switzerland | 1964 |
4 | LVD | Provides robust, precise press brakes with advanced control systems, catering to various industrial needs. | Gullegem, Belgium | 1952 |
5 | KRRASS | Known for durability and performance, offering a variety of hydraulic and electric press brakes and CNC Press Brake. | Nanjing, China | 1998 |
6 | Accurpress | Reliable and versatile press brakes, emphasizing ease of use, maintenance simplicity, and precise bending capabilities. | Rapid City, South Dakota, USA | 1973 |
7 | Salvagnini | Specializes in flexible automation solutions, including press brakes that integrate seamlessly into automated production lines. | Sarego, Italy | 1963 |
8 | Durma | Offers cost-effective, high-quality press brakes with advanced technological features suitable for various applications. | Bursa, Turkey | 1956 |
9 | Ermaksan | Provides innovative press brakes with energy efficiency, precision, and advanced software integration. | Bursa, Turkey | 1965 |
10 | Prima Power | Known for high precision, advanced technology, and adaptability to different production environments. | Turin, Italy | 1977 |
How Does Press Brake Machine Cost
Type of Press Brake | Specifications | Price Range (USD) |
Pneumatic Press Brake | Light-duty, suitable for thin materials | $10,000 - $50,000 |
Mechanical Press Brake | High-speed, repetitive tasks | $20,000 - $70,000 |
Hydraulic Press Brake | Medium to heavy-duty, versatile | $50,000 - $150,000 |
Servo-Electric Press Brake | High precision, energy-efficient | $100,000 - $300,000 |
CNC Press Brake | Advanced automation and control | $100,000 - $500,000+ |
High Tonnage Press Brake | Heavy-duty, large workpieces | $200,000 - $600,000+ |
Used Press Brake | Variable condition and technology | $5,000 - $150,000 |
This table provides a general overview of press brake prices. For precise pricing, it is recommended to contact manufacturers or distributors directly, as prices can vary based on specific requirements and market conditions.
Additional Notes:
- Entry-Level Machines: Generally simpler, pneumatic, or basic mechanical press brakes, are suitable for small-scale or light-duty operations.
- Mid-Range Machines: Include hydraulic press brakes with moderate capabilities and some automation features, suitable for medium-scale operations.
- High-End Machines: Include advanced CNC and servo-electric models with high precision, automation, and capabilities for heavy-duty tasks.
- Used Machines: Prices vary widely based on condition, age, brand, and specifications. They can be a cost-effective option but may come with risks regarding wear and outdated technology.
Technological Advancements in Press Brake Machines
Over the years, press brakes have undergone significant advancements in technology, allowing for greater efficiency, precision, and versatility in metal fabrication. These advancements have revolutionized the manufacturing process, enabling faster and more accurate metal bending. Let’s take a closer look at some of the key advancements in press brake technology:
1. Computer Numerical Control (CNC) Systems
One of the most notable advancements in press brake technology is the integration of Computer Numerical Control (CNC) systems. These systems have completely transformed the way press brakes are operated, providing increased automation and precision. With CNC systems, operators can program the machine to perform complex bending sequences with utmost accuracy. This eliminates the need for manual adjustments and reduces the risk of human error, resulting in higher productivity and consistent quality.
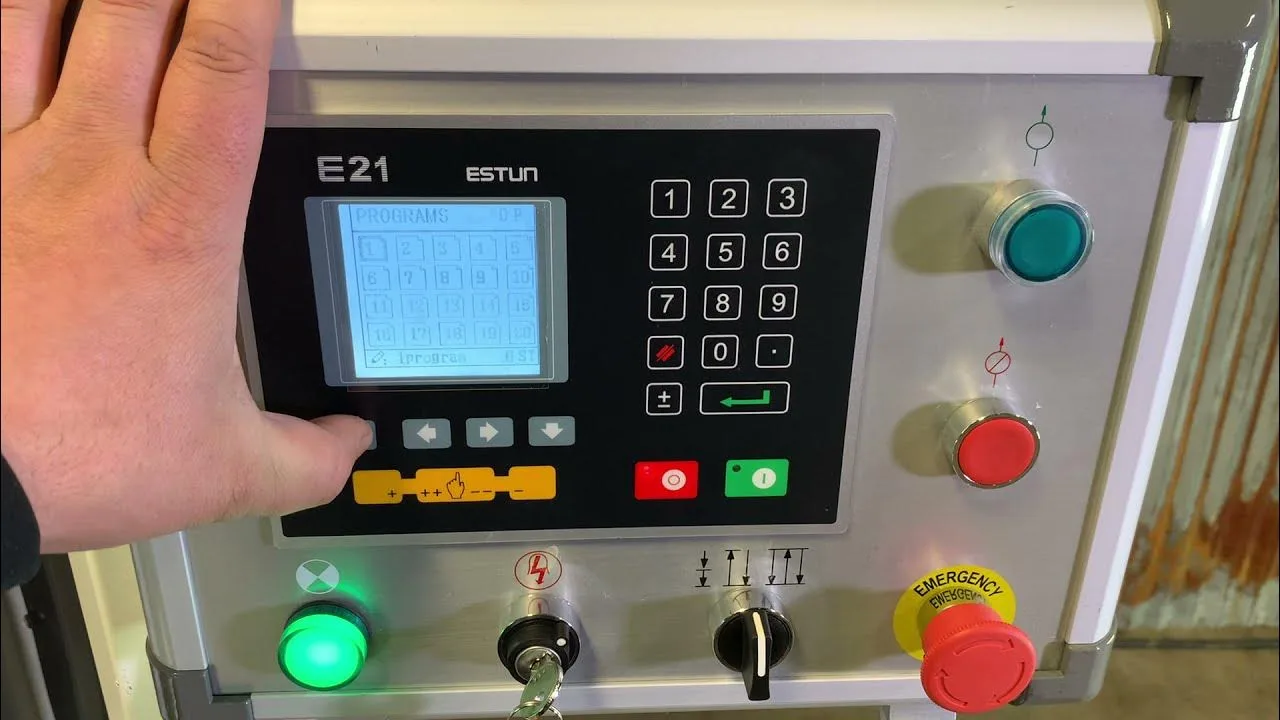
Estun E21 Press Brake Controller Programming
For how to choose the CNC press brake controller, pls click here to read more.
2. Advanced Automation Features
In addition to CNC systems, press brakes now come equipped with a range of advanced automation features. These features include robotic arms, material handling systems, and automatic tool changers. Robotic arms can be used to load and unload materials, reducing the need for manual labor and improving efficiency. Material handling systems streamline the workflow by automatically transferring the metal sheets to the correct position for bending. Automatic tool changers allow for quick and seamless tool setups, minimizing downtime and maximizing productivity.
3. Safety Enhancements
Press brake manufacturers have also prioritized operator safety in their advancements. Modern press brakes are equipped with safety features such as light curtains, safety interlocks, and ergonomic controls. Light curtains create a protective barrier that stops the machine if any object enters the sensing field, preventing accidents. Safety interlocks ensure that the machine cannot be operated until all safety guards are properly in place. Ergonomic controls make it easier for operators to interact with the machine, reducing the risk of strain or injury.
4. Integration With CAD/CAM Software
To further enhance efficiency and accuracy, press brakes now seamlessly integrate with CAD/CAM software. This integration allows for the direct transfer of design files to the press brake, eliminating the need for manual programming. The software also provides simulation capabilities, allowing operators to visualize the bending process before it is executed. This ensures that any potential errors or collisions are identified and rectified beforehand, saving time and material costs.
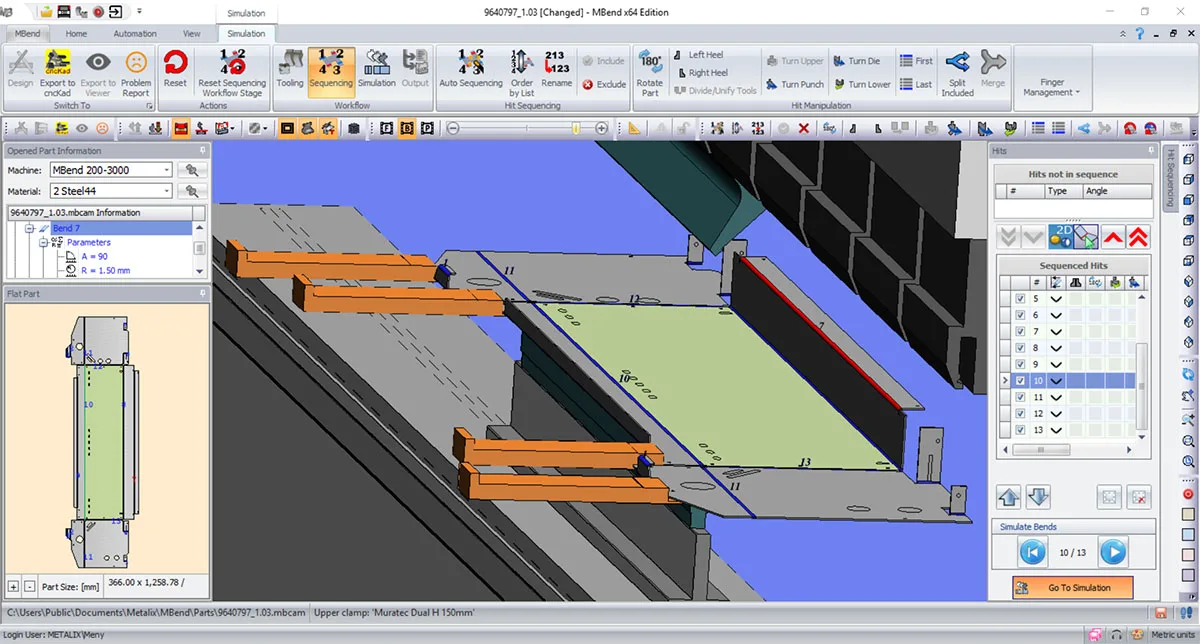
The advancements in press brake technology have transformed the metal fabrication industry, enabling manufacturers to meet the growing demands for precision and efficiency. From CNC systems to advanced automation features
Transformative Influence of CNC Systems in the Press Brake Industry
In the realm of metal fabrication, the advent of Computer Numerical Control (CNC) systems has ushered in a profound revolution within the press brake sector. By seamlessly integrating CNC technology, press brake operations have experienced a paradigm shift, marked by heightened efficiency, precision, and adaptability.
1. Automation: Redefining Operational Efficiency
CNC systems epitomize automation, fundamentally reshaping press brake operations. By executing pre-programmed instructions, these systems orchestrate a symphony of movements with unparalleled precision, eliminating the margin for human error. The consequence is a streamlined, error-free bending process that yields consistently accurate results.
2. Precision: Elevating Quality Standards
At the heart of CNC press brakes lies an unparalleled capacity for precision. Through meticulous control over the bending process, CNC systems achieve levels of accuracy that surpass traditional methods. This precision is indispensable in industries where intricate, flawlessly crafted components are the standard, ensuring each bend meets exacting tolerances.
3. Versatility: Unleashing Creative Potential
The versatility afforded by CNC technology empowers press brake operators to transcend boundaries. By storing and recalling diverse bending programs, CNC press brakes effortlessly adapt to a myriad of tasks. This flexibility not only expedites production but also obviates the need for frequent tooling changes, thereby enhancing operational efficiency.
4. Advanced Features: Catalyzing Productivity Surge
Beyond automation, precision, and versatility, CNC systems introduce an array of advanced features that catalyze productivity gains. Integration with robotic arms and material handling systems streamlines material handling, minimizing downtime and maximizing throughput. Furthermore, automatic tool changers expedite setup, ensuring rapid transitions between bending tasks.
KRRASS Press Brake: Innovative, Precise, Reliable
KRRASS is a leading manufacturer of press brake machines renowned for their precision engineering, advanced technology, and commitment to quality. With years of industry experience, KRRASS has established itself as a trusted name in metal fabrication equipment worldwide.
Advantages of KRRASS Press Brake:
- Precision Bending: KRRASS press brake machines are equipped with advanced CNC controls and dynamic crowning systems, ensuring precise and consistent bending results with tight tolerances. This precision is crucial for industries requiring high-quality, accurately formed metal components.
- Versatility: KRRASS press brakes offer versatility to handle a wide range of bending applications. With customizable bending programs and tooling options, they can accommodate diverse materials, thicknesses, and bending geometries, making them suitable for various industries, including automotive, aerospace, and construction.
- Efficiency and Productivity: Featuring automation and advanced features, KRRASS press brakes streamline workflows, reduce setup times, and increase productivity. Integrated robotic arms, material handling systems, and automatic tool changers optimize operational efficiency, enabling manufacturers to meet production demands effectively.
- Reliability and Durability: KRRASS press brake machines are built to withstand the rigors of industrial environments. Constructed from high-quality materials and components, they offer exceptional durability, reliability, and long-term performance, minimizing downtime and maintenance costs.
Contact us now to schedule a consultation with one of our experts and explore how KRRASS press brakes can empower your business. Experience the difference that precision engineering and advanced technology can make in your manufacturing operations. Don't settle for ordinary bending solutions – choose KRRASS for extraordinary results.
Reviewed by 1 user
press brake machine
Very excellent press brake machine production factory, we have purchased equipment from your company for 5 years, today on the Internet accidentally found the company’s website, very good products.