Tubes and profiles are used everywhere – from mechanical engineering and system construction to the furniture industry. Lasers have opened up new design possibilities, leading to a significant increase in demand as more designers take advantage of the benefits of laser-cut tubes and profiles. Discover all-round solutions for the world of laser tube cutting and find out more about the capabilities of a fiber laser tube cutting machine.
Introduction
If your manufacturing job requires automation, precision, and flexibility with metal tubes, and you need complex patterns cut with high accuracy, a fiber tube laser cutting machine could be the ideal solution. This technology delivers high-quality cuts and intricate designs, perfect for assembly and construction tasks. For strong, clean cuts that need no additional finishing, a fiber tube laser cutting machine is your best choice. To help you determine if this technology is right for your operation, we've compiled a comprehensive guide. Dive into our insights to understand the benefits of fiber tube laser cutting machines and make an informed decision for your metal tubing projects.
What Is Tube Laser Cutting
Laser tube cutting is the process and technique used to cut tubes, structural shapes, or channels. The process will cut these items to the length needed. It can also cut out holes or designs in the tubing.
It is a precise cutting technique. It can also be used on a wide variety of materials in all shapes and sizes. When considering using laser tube cutting, look for a metal fabricator with years of experience in laser cutting.
2-Axis or 3-Axis
Laser tube cutting equipment comes in a variety of types that can handle different cutting needs.
A 2-axis machine cuts tubes in 2 dimensions. They are good for cutting to length. They also work well for producing features and joints to use between tube pieces in structures.
A 3-axis laser tube cutter cuts in 3 dimensions. These machines are used for chamfering or tilt cutting.
What Is Fiber Laser Tube Cutting Machine
A fiber laser tube cutting machine is an advanced tool designed to cut metal tubes with exceptional accuracy and speed using fiber laser technology. This machine employs high-intensity fiber lasers that generate a focused beam of light, which is directed onto the metal tube to achieve precise cuts. The laser beam heats the metal to the point of melting or vaporization, enabling clean and accurate cuts. The machine’s sophisticated control system then guides the laser along the desired cutting path, making it ideal for industries that require intricate and precise cuts in metal tubing.
Why Use Tube Laser Cutter
Tube laser cutting offers several advantages over traditional methods. It is more precise, faster, and can easily cut complex shapes and patterns. It also produces less waste material and is more environmentally friendly.
Automated laser tube cutting machines can run high-volume parts with automatic loading and part unloading while also being able to cost-effectivenessly cut a low-volume component because of the fast setup and changeover times.
The most significant value of laser tube cutting becomes apparent when considering the laser’s capabilities during a product’s design stage. Speed, quality, flexibility, and repeatability are benefits that can be used to the designer’s advantage.
When Use Tube Laser
Knowing when to use laser tube cutting is important. If pieces of tube need to be welded at a later stage in manufacturing, a laser tube cutter offers the best solution.
Laser tube cutting is precise, so it works well when precise and clean welding of pieces is needed.
For tubes that need to be bent before welding, laser tube cutting offers the cuts you need. The cuts allow tubes to be manually bent. It reduces the number of parts needed as well as the amount of welding you'll have to do.
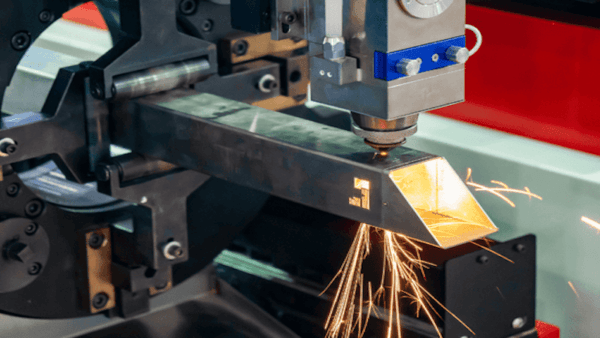
Types of Laser Cutting Machines
UV Laser Cutting Machine
UV laser machines use ultraviolet light to cut through materials like glass and ceramics. These machines are widely used in industries such as electronics, semiconductor manufacturing, and solar energy due to their precision in handling delicate and high-tech materials.
Fiber Laser Cutting Machine
Fiber laser machines utilize a solid-state laser to cut through metals including steel, aluminum, and copper. They are highly popular in automotive manufacturing, aerospace engineering, and metal fabrication industries for their efficiency and accuracy in cutting various metals.
CO2 Laser Cutting Machine
CO2 laser The machines use a gas laser to cut materials such as acrylic, wood, paper, leather, and fabrics. They are commonly used in signage production, woodworking, and textile manufacturing, offering versatility and high-quality cuts for a range of non-metal materials.
Nd Laser Cutting Machine
machines employ a crystal laser to cut through metals, plastics, and ceramics. Known for their precision and versatility, these machines are often used in the medical, dental, and jewelry industries, where detailed and accurate cutting is essential.
Advantages of FIber Laser Tube Cutting Machine
Laser tube cutting offers numerous benefits that make it a popular choice for various applications. Here are some key advantages:
Flexibility
Laser tube cutting machines accommodate a wide range of tube sizes and shapes. They can handle tubes with diameters from less than an inch up to 9 inches, including rectangular tubes of the same width. Length is not an issue either, with standard tubing lengths of 24 feet easily managed. These machines can cut through carbon steel up to 0.25 inches thick, stainless steel of the same thickness, and titanium up to 0.04 inches. Whether dealing with round, rectangular, or irregular profiles, laser tube cutting machines offer remarkable versatility.
Materials
Laser tube cutting is effective on a variety of materials. It can efficiently cut carbon steel, aluminum, stainless steel, and titanium. For reflective materials, fiber lasers are preferable over CO2 lasers. Additionally, laser tube cutters can handle non-metal materials such as wood, plastic, and even styrofoam, expanding their utility beyond metals.
Efficiency
The precision of laser tube cutting ensures that the cuts are clean and exact, eliminating the need for additional processing. Complex designs and precise cuts are achieved with a single machine, which streamlines the workflow by reducing the need for extra tools or parts. This efficiency minimizes material waste and lowers project costs, as parts fit together seamlessly and secondary construction is simplified.
Precision
Laser tube cutting delivers high precision, allowing parts to be used or assembled immediately after cutting. This eliminates the need for further operations, ensuring that the components are ready for immediate use.
Cost
The automation and precision of laser tube cutters lead to reduced manual labor and shorter production times. By simplifying the production process and minimizing waste, laser tube cutting helps lower overall costs and enhances the efficiency of the production line.
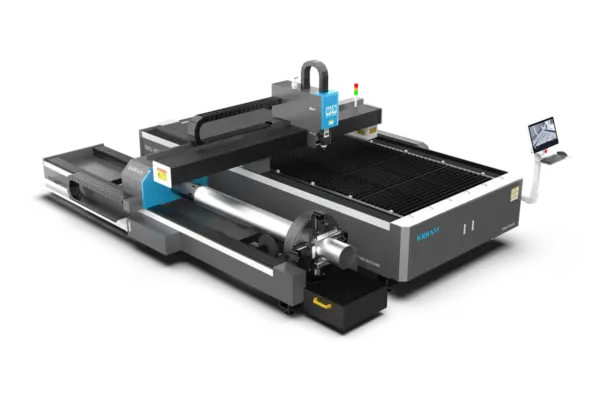
How Does Tuber Laser Work
Laser Generation
The cutting process starts with generating a high-intensity laser beam using a fiber laser. This involves a fiber laser source, which produces the beam by stimulating a doped optical fiber with a laser light source. Known for its efficiency and exceptional beam quality, the fiber laser amplifies the light within the fiber, significantly increasing its intensity. This amplification is essential for cutting through various metal thicknesses, providing the power and precision needed to handle different materials and achieve clean, accurate cuts.
Beam Delivery and Focusing
The focused laser beam is then directed through a series of optical components, including mirrors and lenses, to achieve precise delivery and focusing. These components guide the beam accurately onto the metal tube, concentrating it into a small, intense spot. This focused beam is crucial for cutting various profiles, as it allows for detailed and intricate designs by melting or vaporizing the metal with high precision. The control system, managed by advanced software, automates the cutting process, ensuring that the laser follows the programmed path with exceptional accuracy, translating design specifications into precise cuts without manual intervention.
Cutting Process
The cutting process involves the interaction of the laser beam with the metal tube. When the focused laser beam contacts the tube, it rapidly heats the material to the point of melting or vaporization. This high temperature allows the laser to cut through the metal efficiently. The machine's sophisticated clamping and feeding systems secure and position the tube accurately, ensuring that it remains stable and aligned throughout the cutting process. This precision prevents any movement, which could affect the quality of the cut, and allows for consistent, high-quality results.
Control System
To maintain optimal cutting conditions, the machine utilizes cooling and extraction systems. The cooling system, often using air or liquid, dissipates the heat generated during the cutting process, preventing overheating of both the material and the machine. This ensures that the quality of the cut remains high and that the machine operates efficiently. Simultaneously, the extraction system removes fumes, smoke, and debris produced during cutting, keeping the work area clean and free from contaminants that could affect the cut surface. This integrated approach helps to maintain a clean and effective cutting environment, ensuring precision and enhancing the machine’s performance.
Tube Handling
Once the cutting process is complete, the finished parts are ready for immediate use or further processing. The high precision of the fiber laser tube cutting machine means that the components often require minimal post-processing. The clean, accurate cuts ensure that parts fit together precisely, which simplifies assembly and reduces the need for additional adjustments. This efficiency not only streamlines the production workflow but also contributes to cost savings by minimizing material waste and reducing the time required for secondary operations.
Cooling and Extraction
To maintain optimal cutting conditions, the machine employs both cooling and extraction systems. The cooling system, using either air or liquid, dissipates the heat generated during cutting, preventing overheating of both the material and the machine and ensuring high-quality cuts. Simultaneously, the extraction system removes fumes, smoke, and debris produced during the cutting process, keeping the work area clean and preventing contamination of the cut surfaces. This integrated approach helps maintain a precise and efficient cutting environment.
Post-Cutting
After the cutting process, the parts are immediately ready for use or further processing due to the high precision of fiber laser cutting, which typically requires minimal post-processing. The components cut by a fiber laser tube cutter fit together precisely, simplifying the assembly process and enhancing overall production efficiency. This ensures that the cut parts are ready for immediate integration or assembly, streamlining the workflow and reducing the need for additional adjustments.
By combining advanced laser technology, precise control systems, and efficient material handling, fiber laser tube cutting machines deliver high-quality results across a broad range of materials and tube dimensions. Their versatility and accuracy make them an essential tool for industries requiring intricate and precise cutting.
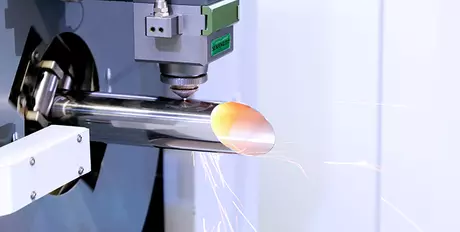
Tube Laser Cutting Process
The Thick and Thin of Laser Tube Cutting
In the past, there was a belief that fiber lasers were only effective for cutting thin materials. Unlike CO2 lasers, which have a larger wavelength and create a wider kerf (the gap left by the cut), fiber lasers struggled with thicker materials because they couldn't produce a wide enough kerf for efficient material removal.
However, advancements in technology have changed this. Modern fiber laser machines now use collimating technology, which allows them to produce a wider beam. This wider beam creates enough space for removing material from thicker pieces. Plus, these machines can switch between a wider beam for thick materials and a narrower beam for thin materials. This flexibility enables efficient cutting of various material thicknesses on the same fiber laser cutting machine.
We haven’t yet covered cutting speed, which can reach up to 500 inches per minute on a tube. However, this speed isn’t always practical. In laser tube cutting, the key consideration is the overall part-processing time. This includes loading the tube, positioning it correctly for cutting, piercing and cutting, and then unloading the finished part. The focus is more on the efficiency of the entire process rather than just the cutting speed. Effective part-processing time is crucial for optimizing productivity with laser tube cutting machines.
Laser Tube Cutting Material
A laser cutting machine for sheet metal can change out a sheet in seconds, but for a laser tube cutting machine, the process is different. There are no standard material towers for these machines. Instead, bundle loaders, the most efficient tube material handling option, feed one tube at a time from a bundle into the tube laser using a singularizing system. This mechanism doesn’t work with open profiles like angles or channels because they interlock in a bundle and don’t come free easily. For these profiles, step loaders are used, which sequence a section one at a time into the machine while maintaining the correct orientation.
These tubes are not small. In the U.S., standard lengths are 24 feet, with some on the West Coast using 20-foot lengths as standard sizes. Variety is a reality for any job shop, including those operating a tube laser. It’s common to see parts of various sizes come from one tube, requiring the machine to unload laser-cut parts ranging from as small as 2 inches to as long as 15 feet, one after the other. The machine must do this without damaging the parts, which can be challenging with softer metals like aluminum.
Due to the nature of a tube, tube laser cutting machines do not need a very high-powered laser. While flat sheet laser cutting machines can have lasers as powerful as 12 kW, tube laser cutting machines usually require a maximum of 5 kW. This is because a more powerful laser would blow through the opposite side of the tube during cutting. For beams or channels, this concern is less relevant, but for most tubes, the power of the laser must be carefully managed to avoid damaging the opposite side.
Considerations in Tube Cutting: The Weld Seam
Positioning of the Weld Seam:
Aesthetic and Functional Concerns: For laser cutting, the weld seam’s position must be carefully managed to avoid interference with pins or holes. For aesthetic applications like furniture, it's essential to hide the weld seam as much as possible.
Detection and Scanning: Traditional laser tube cutting systems use an optical sensor to scan the tube and locate the weld seam. However, tubes covered in oil or rust can make the weld seam difficult to distinguish. For stainless or galvanized tubes, the weld seam might only be visible internally. To address this, some manufacturers now incorporate cameras into their systems, enabling the machine to scan both the outside and inside of the tube. This helps detect obscured weld seams and position parts accurately in relation to them.
Weld Seam Composition and Cutting:
Adjusting Cutting Parameters: Weld seams are made of different compositions and cut differently compared to the rest of the tube. Traditionally, operators needed to slow down or increase power for all operations on a tube to account for the weld seam. Nowadays, some OEMs have developed control technologies that allow the machine to single out the weld seam and adjust parameters specifically for those sections. This enables the machine to process parts more efficiently. The control system automatically adjusts power, frequency, and duty cycle as the laser cuts through the tube and its weld seam. This innovation means the operator no longer needs to manually create perfect parameters and can focus on the material flow in and out of the machine.
File Formats for Laser Cutting
Laser cutting involves precision and accuracy, often requiring specialized programming software to automate the process from initial design to production. This is usually achieved through a CAD/CAM interface, which helps in creating and managing the designs to be cut. Various file formats are commonly used in laser cutting to facilitate this process. Here are some of the most popular ones:
.STP (STEP)
- Description: Standard for the Exchange of Product Data (STEP) is a widely used format for 3D modeling.
- Applications: Ideal for transferring data between different CAD programs and ensuring consistency in design.
.IGS (IGES)
- Description: Initial Graphics Exchange Specification (IGES) is used for representing 2D and 3D models.
- Applications: Commonly used in industries like aerospace, automotive, and manufacturing for sharing complex designs.
.X_T (Parasolid)
- Description: Parasolid files are used for precise geometric modeling.
- Applications: Frequently used in engineering and manufacturing due to their high accuracy and compatibility with many CAD systems.
.IFC (Industry Foundation Classes)
- Description: A comprehensive file format for Building Information Modeling (BIM).
- Applications: Particularly useful in architecture, engineering, and construction for sharing information about building components and structures.
These file formats ensure that laser cutting machines can interpret and execute designs accurately, facilitating efficient and precise cutting processes. The right format can enhance the compatibility and functionality of the software, leading to improved productivity and quality in laser cutting projects.
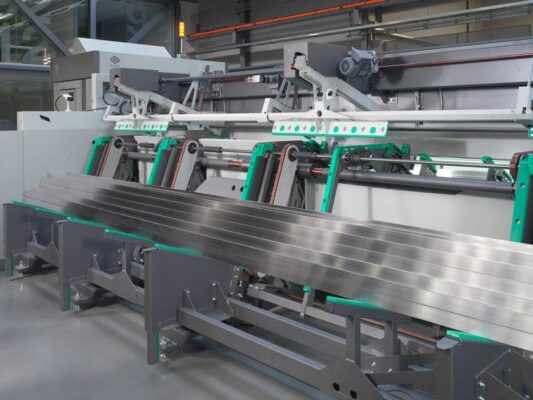
Choosing the Right Tube Laser for Your Needs
If you’re an engineer, metalwork professional, or supplier, working with lasers is likely a common part of your tasks. Whether it's for welding, cutting, machine shop operations, or precision measurements, lasers play a crucial role in various manufacturing processes.
To ensure you select the best laser for your needs, consider these key factors:
- Wavelength: Different applications require different wavelengths, so understanding your specific needs is crucial.
- Power Output: The power output of a laser determines its ability to cut or weld various materials effectively.
- Beam Quality: High beam quality ensures precise and clean cuts or welds.
After identifying these factors, you can start researching lasers that meet your requirements. It's essential to balance both price and performance when making your decision. Additionally, consider any extra features that could benefit your application.
Consulting with our tube laser cutting experts can also be helpful. They can provide tailored advice and save you time in finding the most appropriate laser for your work.
Criteria for an Excellent Fiber Laser Tube Cutting Machine
1. Power and Wattage
The power of a laser cutter provides key insight into the capability and capacity of the machine. Typically, laser tube cutting machines are available in the range of 1500-6000 W. Contrarily, more isn’t always better. You need a proper feasibility report covering design complexity, material type, thickness, and compatibility to help you with power rating.
2. Laser Source Type
The main laser sources available in tube cutting machines are CO2 laser and solid-state laser cutting systems. These days, fiber laser cutting machines, an upgrade to solid-state, offer high productivity, precision, and efficiency.
3. Material Compatibility
Not all lasers are built the same. Different laser sources emit varying wavelengths of laser beam intensity, resulting in differences in compatibility with tube material types and thicknesses.
4. Bed Size and Work Area
The bed size of a laser cutting machine provides vital information about the maximum dimensions of a workpiece the machine can handle efficiently. Having an optimal bed size is critical for efficient production.
5. Software and Control System
A highly functioning cutting machine is nothing without its software. Ensure the manufacturer provides high-end laser cutting software capable of efficiently running the hardware. Also, it should be user-friendly.
6. Value Added Service
A good laser tube cutting machine also provides convenient value-added services such as free machine training, repair services, and after-sales customer support.
Tube Laser Cutter Manufactures Recommendation
Sr. | Brand | Machine Model | Power (W) | Thickness (mm) | Max. Tube Diameter (mm) |
---|---|---|---|---|---|
1 | Baison Laser | All-round tube cutter G22 | 1500-6000 | 0.8-10 | 220 |
2 | Trumpf | TruFiber 3001 | 3000 | 4-8 | 152 |
3 | LightObject | Pro Fiber Tube Cutter | 3000 | 5-15 | 210 |
4 | Bystronic | ByTube Star 130 | 4000 | 10-15 | 130 |
5 | Bodor Inc. | Q0 Pro Tube Cutter | 3000 | 10-60 | 10-60 |
6 | Golden Laser Co. | S12 Plus Tube Cutting Machine | 3000 | 10-15 | 10-120 |
7 | Krrass | RAS-B | 3000-6000 | 10-15 | 12-610 |
8 | LVD | LVD TL 2665 | 3000-4000 | 10-15 | 20-160 |
9 | StyleCNC | ST-FC60M Laser Tube Cutter | 1000-3000 | 10-15 | 20-220 |
10 | ManTech | Titan Metal Tube Cutter | 1000-3000 | 10-20 | 20-220 |
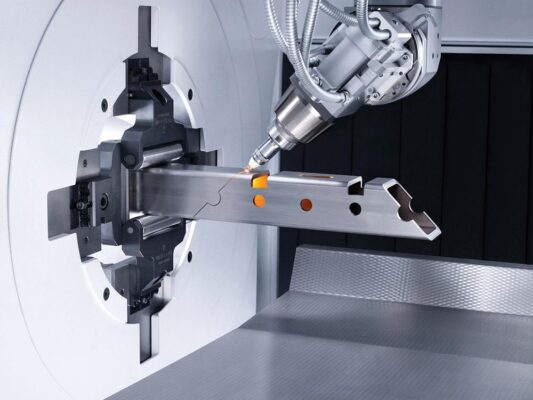
What to Expect When Using a Fiber Laser Tube Cutting Machine
Using a tube laser in your work environment can greatly enhance your manufacturing process, offering speed, precision, and high-quality results. Here are some key points to keep in mind:
Selecting the Right Laserre
Choosing the right type of laser for your specific needs is crucial. KRRASS provides an excellent solution for personalizing your operation techniques. Their machines are designed to meet various industrial requirements, ensuring that you get the most suitable equipment for your tasks.
Performance and Efficiencyere
Once you’ve selected the appropriate laser, you can expect:
- Fast and Accurate Results: Tube lasers cut through a variety of materials quickly and with high precision, reducing production times.
- High-Quality Output: The cuts produced by tube lasers are clean and require very little post-processing, making them ideal for industries that demand high-quality finishes.
- Versatility: Tube lasers can handle different materials and thicknesses, making them a popular choice across various sectors.
Streamlining Your Process
mplementing a tube laser can significantly streamline your manufacturing process. By reducing the need for additional finishing work and improving cutting accuracy, these lasers can help increase productivity and lower operational costs.
If you’re interested in learning more about how to optimize your manufacturing process with KRRASS tube lasers, consider consulting with their experts to tailor a solution that fits your needs.