Technological advancements have driven remarkable progress across industries globally, with significant improvements seen in manufacturing. One crucial tool that has greatly contributed to this progress is the CNC press brake machine. Understanding what is a CNC press brake and how it functions is essential for anyone involved in fabrication or manufacturing.
A CNC press brake is an advanced machine used for bending and shaping metal sheets with high precision. Its role is fundamental in modern manufacturing, providing the capability to create complex and accurate bends in various materials. In this article, we will explore what a CNC press brake is, how it operates, and the key features that make it an indispensable tool in the industry. If you're looking to deepen your knowledge of CNC press brakes, you're in the right place—let’s get started!
What Are the Two Main Types of Press Brakes?
There are two primary types of press brakes: hydraulic and electronic.
Hydraulic press brakes are the oldest press brakes and as such are more common than their electronic counterparts. Hydraulic press brakes can handle the heaviest workloads. While 100-300 tons is the commonly found tonnage, they have been manufactured in sizes up to 3000 tons and 50 feet in length.
Electronic press brakes are less common than hydraulic press brakes as they are newer to the scene. However, they offer many features not found in hydraulic brakes. Being completely electronic, there is no need for hydraulic oil and therefore no oil leaks. Operating costs are further reduced as energy needs are lower, because motors are not continuously run. Electric brakes tend to be more accurate, quicker, and smaller in size coming in under 50 tons, although machines can range in sizes up to 300 tons.
What Is the Purpose of a Press Brake?
A press brake is a crucial piece of manufacturing equipment designed to bend sheet metal with precision. Its narrow and elongated structure allows it to handle large sheets of metal, making it an essential tool in various fabrication processes. The primary function of a press brake is to create precise bends in metal sheets by clamping them between a movable punch and a stationary die. This mechanism ensures that the metal is bent accurately according to the desired specifications, enabling the production of complex and precise metal components.
What Is a CNC Press Brake Machine?
A CNC press brake machine is an advanced version of a traditional press brake, incorporating Computer Numerical Control (CNC) technology. This integration allows the machine to perform precise and efficient bending and shaping of metal sheets, whether they are just a few millimeters or several meters long.
Structure of CNC Press Brake
- Down Forming Type:
- Description: In this configuration, the machine features a fixed bottom bed with a V-shaped tool attached. The top beam, which is also V-shaped, moves downward to apply force. As the top beam presses the metal sheet against the bottom tool, the sheet is bent into the desired shape. This type is particularly effective for various bending tasks and is commonly used in production environments.
- Up Forming Type:
- Description: The up forming type operates similarly to the down forming type but with a key difference. Here, the top portion of the machine remains fixed, while the bottom section is the moving part. The metal sheet is bent as the moving bottom part presses it against the fixed top tool. This configuration can be advantageous for certain applications, providing flexibility in handling different material thicknesses and shapes.
What Is the Meaning of CNC
Computer Numerical Control (CNC) is an automatic technology that uses a computer program to control mechanical tools. A single tool can perform multiple functions with a custom computer program. Changes and modifications in the outcome are possible with changes in the program without modifying the equipment.
‘Numerical’ in the CNC denotes the ability of this technology to use numbers for maneuvering the tools. Numbers may refer to cartesian coordinates, speeds, degrees, or many other denominations. Machine tools interpret these numbers based on the commands in the program.
CNC has diversified production processes in all industries. This technology applies to all types of industrial processes, be it machining, welding, cleaning, grinding, or 3D printing.
Origin and History of CNC Technology
Numerical Control (NC) technology, the precursor to Computer Numerical Control (CNC), has its origins in the 1940s. This early technology laid the groundwork for what would become modern CNC systems, even before the advent of contemporary computers. The initial NC systems utilized punched tape as the means of inputting commands and instructions into machines.
In these early systems, mechanical devices known as cams—similar to those used in music boxes—were used to interpret the punched tape. While these cams enabled automation of machinery, they lacked the flexibility and programmability of later computer-based systems. The limitations of this early automation led to the development of more advanced computing concepts in the subsequent decades.
Who Invented CNC Technology
John Parsons and Frank Stulen are credited with the invention of Computer Numerical Control. Their pioneering work focused on optimizing the helicopter manufacturing process for Sikorsky. Their innovative CNC method significantly advanced the precision and efficiency of manufacturing, marking a pivotal moment in the evolution of automated machinery.
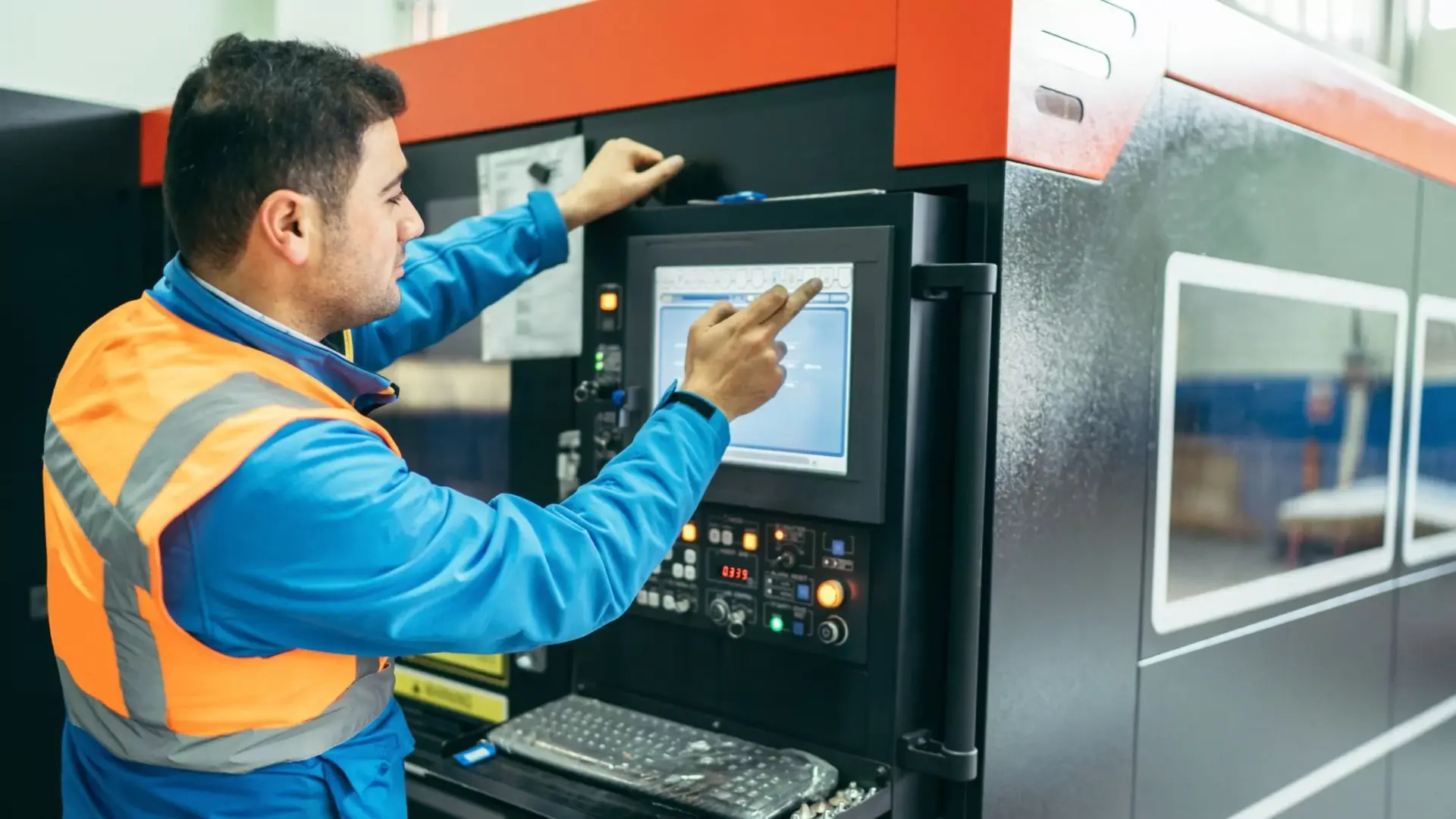
What Are Essential Elements of a CNC System
The CNC (Computer Numerical Control) system in a press brake serves as the machine's operational brain, orchestrating precise and automated metal bending according to specific instructions. This sophisticated system integrates several key components to ensure accurate and efficient performance. Here’s a breakdown of what constitutes a CNC system:
1. Control System
The control system is central to the CNC operation, encompassing both hardware and software that interpret programmed instructions and convert them into precise movements of the press brake. It typically includes a control panel or interface where operators input bending parameters and manage machine functions.
2. Programming
CNC press brakes execute bending operations based on programmed instructions. Operators use specialized software to create these programs, specifying details such as bend angles, lengths, tooling, and material thickness. The CNC system translates these instructions into machine-readable code, such as G-code or a proprietary language unique to the press brake manufacturer.
3. Axis Control
Press brakes operate along multiple axes to achieve accurate bends. The CNC system manages these axes, including:
- Ram Axis: Controls the vertical movement of the bending ram, which applies force to the metal sheet to perform bends.
- Backgauge Axis: Manages the horizontal movement of the backgauge, positioning the metal sheet in relation to the bending tool.
- Crowning Axis (optional): Adjusts the curvature of the bed to counteract deflection during bending, ensuring uniformity across the workpiece length.
4. Feedback Systems
To maintain precision, CNC press brakes are equipped with feedback systems that provide real-time data on the machine's position, speed, and other critical parameters. These systems may include linear encoders, rotary encoders, scales, or sensors that monitor moving components, allowing the CNC system to make necessary adjustments and uphold tight tolerances.
5. Safety Features
CNC systems incorporate various safety mechanisms to safeguard operators and prevent accidents. These features can include safety interlocks, light curtains, emergency stop buttons, and collision detection systems. The CNC system continuously monitors these safety elements and enforces protocols to halt operations or mitigate risks.
6. Networking and Connectivity
Modern CNC press brakes are often equipped with networking capabilities for seamless communication with other machines, CAD/CAM systems, and enterprise software. This connectivity supports data exchange, remote monitoring, and integration into automated manufacturing processes, enhancing productivity and operational efficiency.
In summary, a CNC system is a complex integration of control mechanisms, programming, axis management, feedback systems, safety features, and networking capabilities. Together, these components enable CNC press brakes to perform precise and efficient metal bending operations.
What Is the Applications of CNC Press Brakes
Manufacturing and Fabrication:
- Custom Metal Parts: Fabricators use press brakes to create custom metal components for machinery, equipment, and structures.
- Prototype Development: Press brakes are essential for producing prototypes and test pieces in the early stages of product development.
Automotive Industry:
- Vehicle Components: Press brakes are used to manufacture parts such as chassis components, brackets, and panels for cars and trucks.
- Body Panels: They shape and form complex body panels and structural elements required in automotive production.
Aerospace Industry:
- Aircraft Parts: Aerospace manufacturers use press brakes to bend and shape aluminum and other metals for aircraft wings, fuselages, and structural components.
- Precision Components: High precision and reliability are required for aerospace components, making press brakes an essential tool in this industry.
Construction and Architecture:
- Structural Elements: Press brakes are used to create bent metal components for buildings, bridges, and other infrastructure projects.
- Architectural Features: They shape metal sheets into architectural details, such as decorative panels and structural supports.
Consumer Goods:
- Appliance Parts: Press brakes are used to produce parts for household appliances, including washing machines, refrigerators, and ovens.
- Furniture Components: They help fabricate metal components for various types of furniture, such as frames and supports.
Sheet Metal Fabrication:
- Enclosures and Cabinets: Press brakes are used to form metal enclosures, cabinets, and racks for electronics, telecommunications, and industrial equipment.
- HVAC Systems: They shape metal components for heating, ventilation, and air conditioning systems, including ducts and vents.
Electronics and Electrical Equipment:
- Panel Fabrication: Press brakes are used to manufacture metal panels and housings for electronic devices and electrical equipment.
- Mounting Brackets: They produce brackets and supports for mounting electronic components and systems.
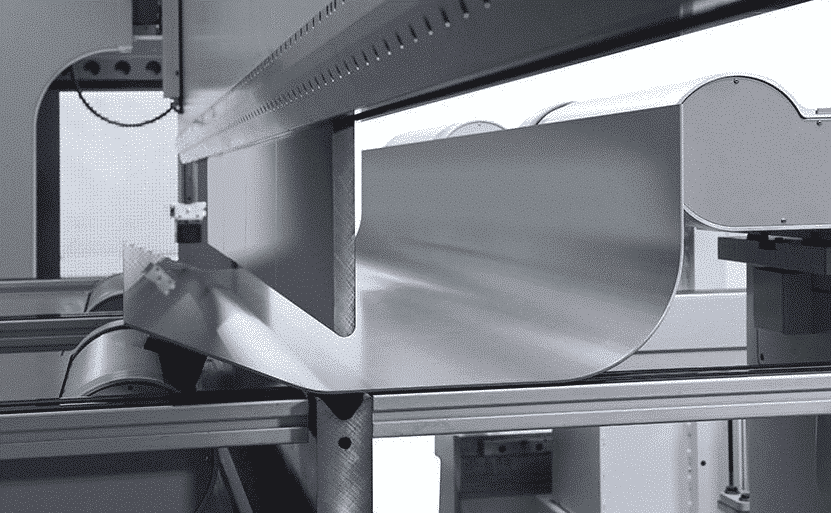
What Are the Benefits of CNC Press Brake Machine?
Precision Engineering
CNC press brakes epitomize precision engineering, offering unparalleled accuracy in bending metal sheets to exact specifications. The integration of CNC systems allows for precise control over bending parameters, including bend angles, lengths, and depths. This level of precision is indispensable in industries where tight tolerances are non-negotiable, such as aerospace, automotive, and electronics manufacturing.
Automated Operation
One of the most significant advantages of CNC press brakes is their ability to automate bending processes. The CNC system interprets programmed instructions, eliminating the need for manual adjustments and minimizing the risk of human error. With automated operation, CNC press brakes deliver consistent results across various workpieces, ensuring uniformity and repeatability in production.
Versatility in Applications
CNC press brakes excel in accommodating diverse metalworking tasks, thanks to their versatility and programmability. From simple bends to complex geometries, these machines can handle a wide range of materials, including steel, aluminum, and stainless steel, with ease. The CNC system allows operators to program bending sequences and tooling setups, facilitating efficient production of diverse components and parts.
Enhanced Efficiency
The integration of CNC systems enhances the efficiency of press brake operations by streamlining workflow and reducing setup times. With CNC press brakes, operators can quickly switch between bending tasks, load predefined programs, and execute bending sequences with minimal downtime. The automation of repetitive tasks minimizes manual intervention, maximizing productivity and throughput in metalworking facilities.
Real-time Monitoring and Control
CNC press brakes offer real-time monitoring and control capabilities, enabling operators to track bending processes and make adjustments on the fly. The CNC system continuously collects data from feedback sensors and monitoring devices, providing insights into machine performance and workpiece quality. Operators can intervene as needed to optimize bending parameters and ensure optimal results.
Integration with CAD/CAM Systems
CNC press brakes seamlessly integrate with CAD/CAM systems, enabling efficient programming and simulation of bending operations. Design files can be imported directly into the CNC system, allowing operators to visualize bending sequences, simulate tooling setups, and validate part designs before production. This integration streamlines the design-to-production workflow, reducing lead times and minimizing errors.
What Are the Disadvantages of CNC Press Brakes
High Initial Cost
- CNC press brakes are expensive to purchase and install. The advanced technology and precision components contribute to a significant initial investment, which can be a barrier for smaller businesses or startups.
Complex Operation and Maintenance
- Operating a CNC press brake requires specialized training and expertise. The complexity of programming and maintaining the machine can lead to a steep learning curve for operators. Additionally, routine maintenance and troubleshooting can be more complicated compared to manual press brakes.
Software and Programming Costs
The cost of CNC software and ongoing updates can add to the overall expense of using a CNC press brake. Specialized programming skills are needed to create and modify machine codes, which may require additional training or hiring skilled personnel.
Limited Flexibility for Custom Jobs
- While CNC press brakes are highly efficient for repetitive tasks and standardized bends, they may be less adaptable for quick changes or highly custom jobs compared to manual press brakes. Adjustments to machine settings or tooling can be time-consuming.
Maintenance and Downtime
- CNC press brakes rely on electronic components and advanced systems that can be prone to malfunctions or breakdowns. Any issues with the control system, feedback mechanisms, or electrical components can lead to costly downtime and repair expenses.
Space and Infrastructure Requirements
- CNC press brakes are often larger and heavier than manual press brakes, requiring more space in the workshop. They may also need additional infrastructure, such as robust power supplies and environmental controls, to operate effectively.
Energy Consumption
- The sophisticated technology and high precision of CNC press brakes can lead to increased energy consumption compared to simpler manual machines. This can result in higher operating costs and environmental impact.
Over-Reliance on Technology
- Dependence on advanced technology can be a disadvantage if technical issues arise or if there's a need for manual intervention. In such cases, production can be delayed, and the reliance on technology can create challenges when troubleshooting.
In summary, while CNC press brakes provide exceptional precision and automation, they also present challenges such as high costs, complex operation, and maintenance requirements. Evaluating these disadvantages against the benefits is essential when considering the integration of CNC press brakes into a manufacturing process.
Is a Press Brake Hard to Operate?
In some respects, operating a press brake seems straightforward: you insert the tooling, and the ram moves up and down to bend the parts. However, in reality, the press brake is arguably the most challenging machine in the trade to master. Bending lies at the heart of any sheet metal operation, requiring a deep understanding of both the machine and the material.
Mastering the press brake involves more than just knowing how to operate it. Operators must understand the properties of different metals, including their tensile strength and elasticity, to predict how they will behave during bending. Precision is crucial, as even minor deviations can result in parts that do not fit correctly or meet specifications.
What Are the Golden Rules of CNC Press Brake Operation?
Read the User Manual Thoroughly:
Operators should carefully read the CNC press brake user manual before use. Familiarize yourself with the machine’s specific features, controls, and recommended operating procedures. Always follow the manufacturer’s guidelines for maintenance and troubleshooting to ensure safe and efficient operation.
Prioritize Safety:
Safety should always be the top priority when operating a CNC press brake. Operators can only start the foot pedal once they have ensured that no unsafe conditions exist, especially when multiple operators are working on the machine. Familiarize yourself with the machine’s safety features, such as emergency stop buttons and safety guards, and always adhere to safety protocols.
Tooling Setup:
Properly install and secure the appropriate tooling for the desired bending operation. Follow the manufacturer’s instructions for tooling setup, including proper alignment, clamping, and adjustments. Ensure that the tooling is in good condition and free from damage or wear to maintain bending accuracy and safety.
Comprehensive Training:
Ensure that all operators receive thorough training on the operation of the CNC press brake. Training should cover safe machine handling, tooling setup, programming, and maintenance procedures. Regular refresher training should be provided to keep operators up to date with best practices and new machine features.
Material Inspection:
Before bending any material, carefully inspect it for defects or abnormalities. Verify that the material thickness is within the machine’s capacity and that it is suitable for the specific bending operation. Remove any debris or foreign objects that could interfere with the bending process to prevent damage and ensure quality results.
Step-by-Step Operation:
Follow a systematic approach when operating the CNC press brake. This typically includes the following steps:
- Set the machine to the correct operating mode (manual or automatic).
- Program or adjust the machine’s parameters for the desired bend, such as bend angle, bend length, and back gauge position.
- Position the material securely and accurately on the machine’s bed and back gauge.
- Activate the machine using the appropriate control or foot pedal, ensuring that operators keep their hands clear of the bending area.
- Monitor the bending process closely, checking for any abnormalities or issues.
- After completing the bend, carefully remove the finished workpiece and inspect it for quality.
By adhering to these operation rules, you can ensure safe and efficient use of the CNC press brake, leading to high-quality bending results and prolonged machine life.
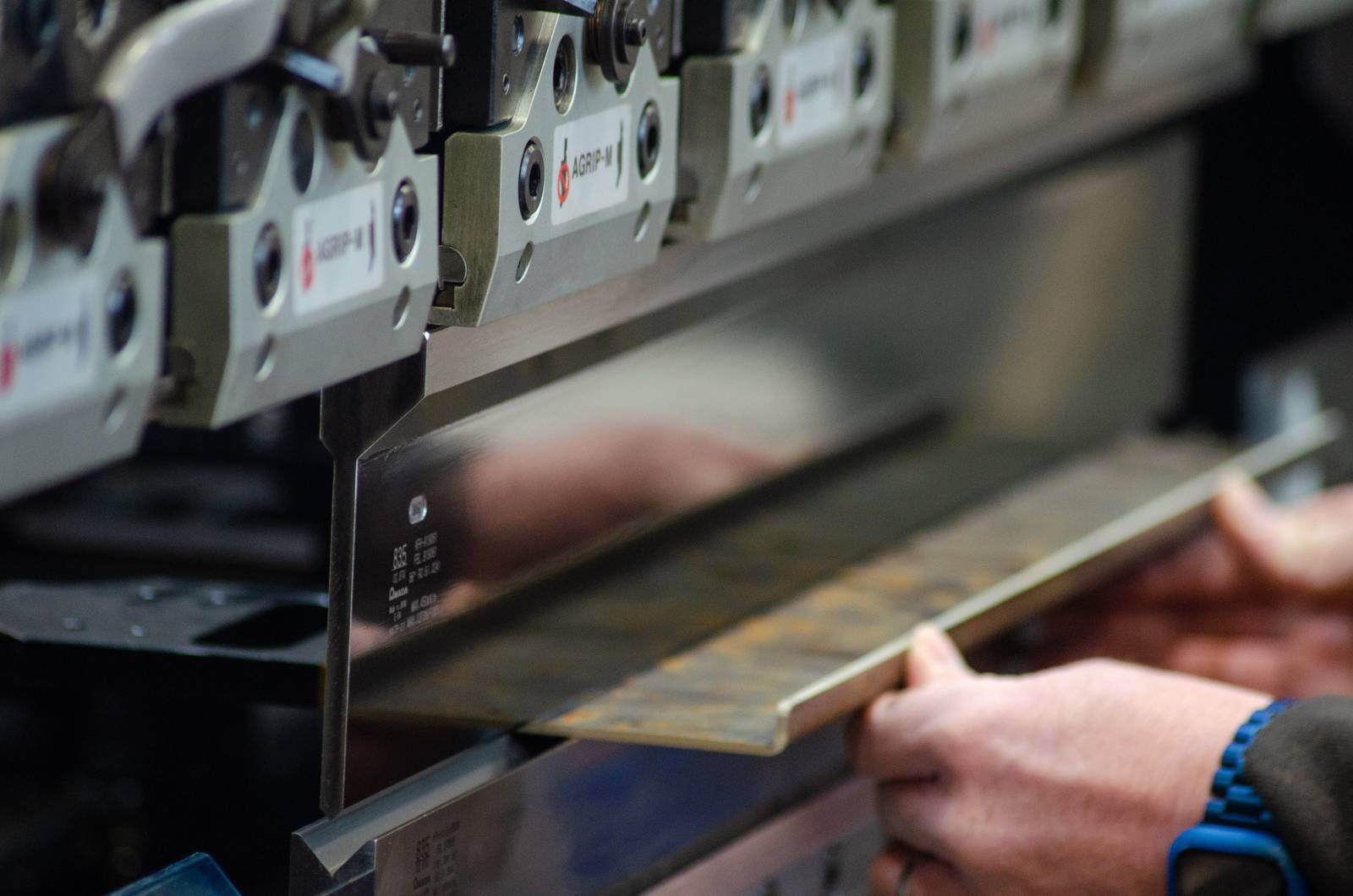
How do I Choose a CNC press brake?
Before you select a press brake, you must know what kind of metal you wish to bend (stainless steel, aluminum sheet, etc.).
You will then have to specify the specific properties to consider in calculating the bending of the component; this includes, for example:
- The tensile strength
- The thickness and length of the metal
- The press brake’s folding or bending length
- Width of V
- The inner radius of the parts
Once these properties have been determined, you will have to calculate the weight needed for bending.
Cargo is the compression force of the pressure brake. It determines how much pressure the punch can exert during the bending operation.
- High tonnage makes it possible to bend heavy and hard metals.
- Low weight applies to thin metal.
Warning: Incorrect loading (too high or too low) may damage the press brake or the part that you are bending. Please refer to the Operator’s Manual or tonnage table to calculate your pressure brake tonnage.
Which types of technique you want to choose for your press brake?
In general, press brake will have three different types of technology:
Hydraulic press brake
- A hydraulic cylinder system moves the punch.
- It has a high bending capacity (bending length up to 8 meters and bending force up to 1500 tons).
- It operates continuously, even if not bending, generating electricity costs.
- It requires significant maintenance regularly.
- It’s stronger than an electric press brake.
- It is also cheaper.
- It is suitable for simple bending operations.
Electric press brake
- It is equipped with more energy-efficient servo motors instead of hydraulic cylinders.
- It achieves more significant productivity gains.
- The servo motor only consumes energy when the machine needs to bend.
- There is no need to be more maintenance.
- The machine offers more flexibility.
- It is more expensive than the hydraulic press brake, but operating costs are lower.
Hybrid press brake
- It is a hydraulic press brake equipped with electric motors.
- Having electric motors reduces the use of the hydraulic system.
- It combines the advantages of electric and hydraulic press brakes.
What Type of Bending Should You Choose?
There are two primary types of bending techniques used in sheet metal fabrication: air bending and bottom bending. Each method has its own advantages and is suitable for different applications. Let's explore when to choose each type.
Air Bending
In air bending, the punch tip and the two sides of the V-die come into contact with the sheet metal, allowing for the bend to occur. This method, however, leads to a spring-back effect, where the workpiece slightly returns to its original shape once the punch is removed. To achieve the desired angle, you must adjust for this spring-back. For example, to achieve a 90° bend, the punch might need to go down to around 85°.
When calculating this adjustment margin, factors such as the punch blade's thickness, the length of the fold, and the opening of the V-die must be considered. Air bending is commonly used for sheet metal work because it requires less force compared to bottom bending, making it suitable for machines with reduced capacity.
When to Choose Air Bending:
- When working with thinner sheets of metal.
- When using machines with limited force capacity.
- When some degree of flexibility and adjustability is acceptable.
Bottom Bending
Bottom bending involves applying high force (3 to 5 times more than air bending) to bend the metal sheet, significantly reducing or even eliminating the spring-back effect. The process starts with air bending and is followed by cold forging at the bottom of the V-die, ensuring a high degree of angular accuracy.
This method is ideal for thicker metal sheets, typically over 2 mm in thickness, and is used when precise bends are required without any spring-back.
When to Choose Bottom Bending:
- When working with thicker sheets of metal (over 2 mm).
- When high precision and angular accuracy are crucial.
- When the machine can handle the higher force requirements.
By understanding the specific needs of your bending project, you can choose the appropriate method—air bending for its flexibility and suitability for lighter work, or bottom bending for its precision and suitability for thicker materials.
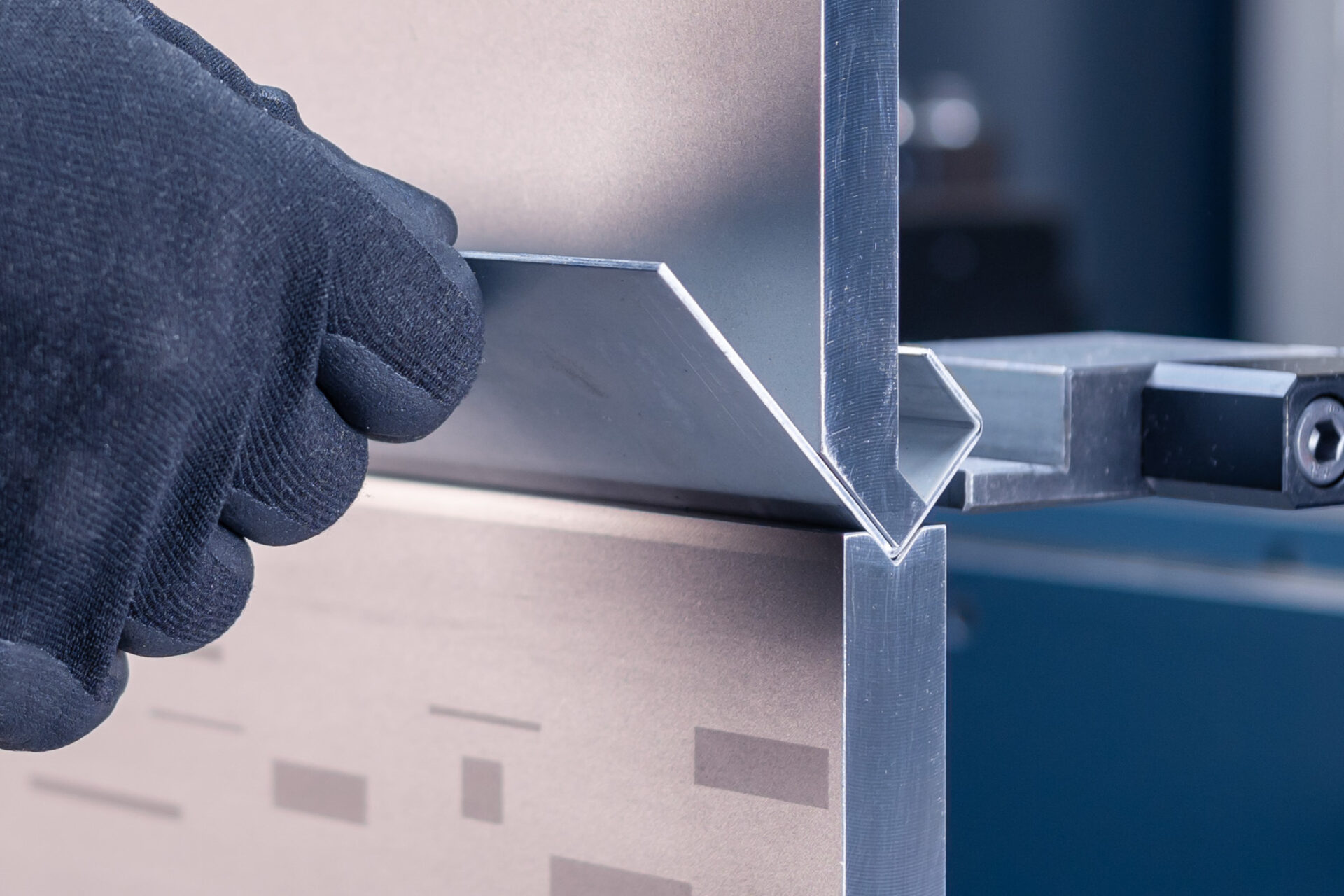
What Are the Other Selection Criteria for a Press Brake?
When selecting a press brake, several key criteria should be considered to ensure optimal performance and suitability for your specific needs. Here are the critical factors to take into account:
CNC Control System
The CNC (Computer Numerical Control) system is the core component of a press brake, acting as the brain of the machine. It issues precise control commands based on the parameters set by the user and feedback data during operation. A powerful CNC control system is essential for achieving accurate and efficient bending operations.
Back Gauge
The back gauge is an adjustable component used to position the metal sheet accurately, ensuring the bending line aligns correctly with the V-die. This component is crucial for maintaining consistency and precision in the bending process.
Angle Control
Angle control compensates for any inaccuracies during the bending process. This can be achieved through manual crowning or CNC motorized crowning systems. Proper angle control ensures that bends are precise and meet the desired specifications.
Tools
The choice of tooling is critical for the press brake's performance. Quick clamping systems can significantly reduce tool change times, enhancing productivity. Additionally, the length and quality of the clamping affect the accuracy of the bends.
Operator Safety
Operator safety is paramount when selecting a press brake. Beyond the commonly used optical safety systems, advanced control safety systems are available. These systems include programmable safety controllers that integrate all relevant control, safety, and monitoring functions into a single system. This integration simplifies the design process, eliminates the need for third-party components and software, and enhances both the performance and safety of the press brake.
By considering these criteria—CNC control system, back gauge, angle control, tooling, and operator safety—you can select a press brake that meets your operational needs and ensures efficient, accurate, and safe bending operations.
What Are the Best CNC Press Brake Manufactures
Best CNC Press Brake Manufacturers
Selecting the right CNC press brake manufacturer is crucial for ensuring high-quality bending operations and long-term reliability. Here is a list of some of the best CNC press brake manufacturers known for their innovation, quality, and customer support:
Manufacturer | Overview | Strengths | Popular Models |
---|---|---|---|
Amada | Japanese manufacturer specializing in sheet metal processing equipment. | High precision, innovative technology, robust construction. | HFE-M2 Series, HG Series |
Trumpf | German manufacturer known for advanced technology and high-performance machines. | Cutting-edge technology, high automation levels, efficient production processes. | TruBend Series 5000, 7000 |
Bystronic | Swiss company, a global leader in sheet metal processing solutions. | User-friendly interfaces, high precision, excellent customer support. | Xpert Pro Series, Xpert |
LVD | Belgian company known for comprehensive range of sheet metalworking machinery. | Versatility, high productivity, advanced control systems. | Easy-Form Series, Strippit PX |
Accurpress | North American manufacturer specializing in reliable and efficient press brakes. | Robust build, easy maintenance, customizable options. | Advantage Series, Accell |
KRRASS | Known for high-quality and cost-effective sheet metal processing equipment. | Competitive pricing, excellent performance, comprehensive after-sales support. | MB8 Series, PBS |
Salvagnini | Italian manufacturer recognized for innovative automation solutions. | High automation, flexible manufacturing solutions, energy-efficient machines. | B3 ATA Series, B3 |
Durma | Turkish manufacturer offering a wide range of metalworking machinery. | Affordability, reliable performance, extensive product range. | AD-S Series, AD-R |
Mazak | Known for precision engineering and advanced technology in manufacturing. | High accuracy, innovative technology, extensive service network. | Optiplex Series, Syncrex |
MC Machinery Systems | Subsidiary of Mitsubishi, offering a wide range of CNC machinery. | Advanced technology, high performance, robust support services. | Diamond BB Series, Diamond Elite |
This table presents an overview of the top CNC press brake manufacturers, highlighting their strengths and popular models.
Choosing the right CNC press brake manufacturer depends on your specific needs, budget, and desired features. Each of these manufacturers offers unique strengths and a range of models to suit various applications. By considering these top manufacturers, you can find a CNC press brake that delivers precision, efficiency, and reliability for your sheet metal fabrication needs.
Are CNC Press Brake Expensive?
Yes, CNC press brakes are generally more expensive compared to traditional press brakes. Several factors contribute to their higher price:
- Advanced Technology: CNC press brakes incorporate sophisticated computer numerical control systems that allow for precise and automated bending operations. The integration of advanced hardware and software increases production costs.
- Superior Performance: These machines offer high precision, repeatability, and efficiency in metal bending, which makes them highly desirable for complex and high-volume production tasks.
- Durability and Reliability: CNC press brakes are built to last and can handle rigorous use over extended periods. Their robust construction and high-quality components contribute to their longevity and reliability, justifying their higher price.
- Customization and Flexibility: CNC press brakes can be programmed to perform a wide range of bending operations, accommodating various materials and thicknesses. This versatility adds to the overall cost.
- Efficiency and Productivity: The ability to automate and streamline bending processes reduces manual labor and increases productivity, leading to higher initial investment but long-term cost savings.
- Safety Features: CNC press brakes are equipped with advanced safety features such as light curtains, safety interlocks, and emergency stop buttons, which enhance operator safety but also add to the machine's cost.
From Entry-Level to High-End: What Are the Prices of CNC Press Brake
The prices of CNC press brakes can vary significantly based on several factors. Here’s an overview of the key price ranges and influencing factors:
Entry-Level CNC Press Brakes:
- Price Range: $20,000 - $50,000
- Features: Basic CNC control systems, smaller bed sizes, and lower bending capacities.
- Suitable For: Smaller workshops or businesses with less demanding bending needs.
Mid-Range CNC Press Brakes:
- Price Range: $50,000 - $150,000
- Features: Advanced CNC systems, larger bed sizes, higher bending capacities, and improved accuracy.
- Suitable For: Medium-sized businesses requiring a balance between performance and cost.
High-End CNC Press Brakes:
- Price Range: $150,000 - $500,000+
- Features: Top-of-the-line CNC controls, large bed sizes, high bending capacities, advanced automation, and custom features.
- Suitable For: Large manufacturing facilities or businesses with high-volume and complex bending requirements.
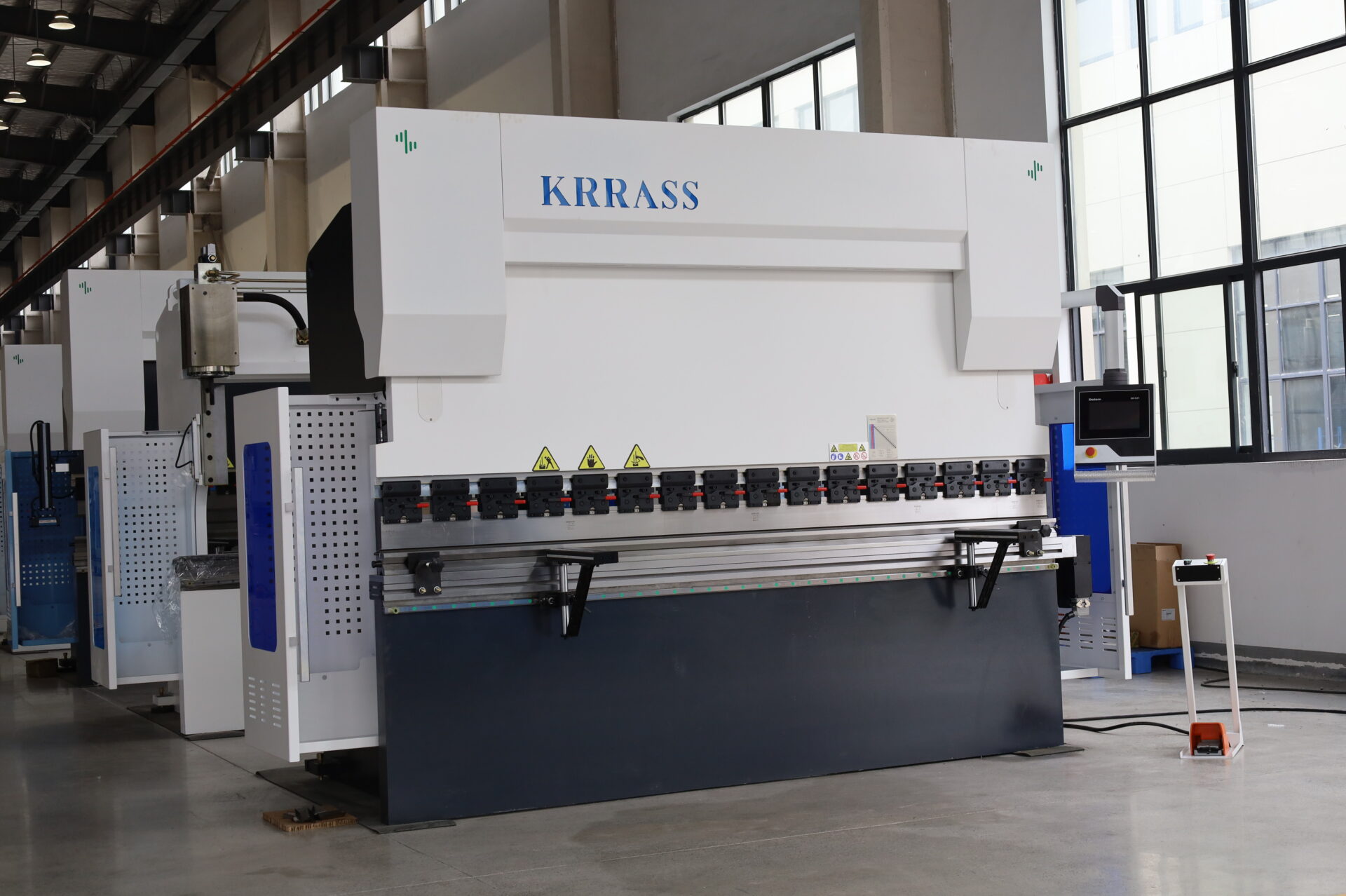
Final Thought
When considering the overall costs of purchasing, maintaining, and operating a sheet metal equipment setup, choosing a reliable brand is crucial. For this, KRRASS stands out as your best choice. Known for its focus on consistency and quality at the most competitive prices, KRRASS has earned a tremendous reputation in the market.
So, what is a CNC press brake? A CNC press brake is an essential piece of equipment for any sheet metal fabrication service. With KRRASS, whether you need a press brake or any other application equipment, our team of experts combines industry knowledge with the latest tools to provide you with the best products and services available.
Moreover, KRRASS distinguishes itself with an advanced, completely online system. Simply inform us of your product needs, request a quote, and start the process seamlessly. Trust KRRASS to meet your sheet metal fabrication needs with precision and reliability.
Reviewed by 2 users
This great guide let me know what there is difference between the Krrass and the other brands, it is good to choose the mb8 press brake
cnc press brake
We got the machine from KRRASS and it is great and we have been using it.