The power level of a fiber laser, such as a 1kW fiber laser, plays a crucial role in determining its cutting capabilities and suitability for different tasks. The wattage of a laser directly impacts the thickness of materials it can effectively cut and the speed at which it operates. A 1kW fiber laser is particularly effective for cutting thinner materials and smaller-scale projects with high precision. Understanding the power levels helps in selecting the appropriate fiber laser for specific cutting needs, ensuring optimal performance and efficiency in various applications.
What Is Laser Cutting
Laser cutting is a non-contact process that uses a laser beam to slice materials. It is characterized by its precision, speed, and versatility, making it a popular choice for various industries. The term ‘laser’ stands for “Light Amplification by Stimulated Emission of Radiation.” Essentially, it involves the use of a concentrated laser beam to melt, burn, or vaporize the material, resulting in cleanly cut edges.
Types of Laser Cutter
CO2 Laser Cutters use a CO2 gas mixture as the laser medium and are among the most common types of laser cutters. They are well-suited for cutting and engraving a wide range of materials, including wood, acrylic, plastics, textiles, and some metals (with the right setup). These lasers are ideal for detailed engraving and cutting of non-metal materials, making them frequently used in signage, craftwork, and decorative items.
Fiber Laser Cutters utilize a fiber optic cable to generate the laser beam, known for their high efficiency and precision. They are particularly effective for cutting metals such as steel, stainless steel, aluminum, brass, and copper, as well as some non-metals. Fiber lasers are commonly used in high-precision applications within industries like automotive, aerospace, and manufacturing, providing excellent performance for both thin and thick metal sheets.
NdLaser Cutters use a neodymium-doped yttrium aluminum garnet (Nd) crystal as the laser medium, offering high peak power and energy efficiency. They are suited for cutting and welding metals, including stainless steel, aluminum, and titanium, as well as some ceramics and plastics. These lasers are often employed in applications requiring high-energy pulses and high-strength materials.
Disk Laser Cutters utilize a laser beam generated by a solid-state laser with a disk-shaped medium, known for their high power and efficiency. They are used for industrial applications that require high cutting speeds and precision, suitable for thick metal sheets and heavy-duty manufacturing tasks. Disk lasers are comparable to fiber lasers in terms of material versatility, focusing primarily on metal cutting.
Ultrafast Laser Cutters employ ultrafast laser pulses, ranging from femtoseconds to picoseconds, providing high precision with minimal thermal impact on materials. They are ideal for micro-machining and fine-detail cutting, working effectively with metals, ceramics, and polymers. These lasers are commonly used in electronics and medical device manufacturing due to their precision and minimal heat-affected zones.
Excimer Laser Cutters use a gas laser with an excimer as the medium, emitting ultraviolet light and serving highly specialized applications. They are primarily used for non-metal materials such as plastics and thin films. Excimer lasers are prevalent in the semiconductor industry for precise micro-cutting and etching tasks.
Pulsed Laser Cutters generate laser beams in pulses rather than continuous waves, allowing for controlled energy delivery and high precision. They are suitable for cutting and engraving delicate or high-precision materials, including metals, ceramics, and polymers. Pulsed lasers are ideal for applications requiring intricate designs and minimal thermal impact.
Fiber Lasers Overview
Fiber lasers represent a significant advancement in cutting technology, utilizing a solid-state laser source to produce a high-power, highly focused beam of light. This technology offers several advantages, including exceptional energy efficiency, precise cutting capabilities, and reduced operational costs compared to traditional CO2 lasers. Fiber lasers are known for their ability to cut a wide range of materials with high accuracy and minimal maintenance requirements, making them a popular choice in various industrial applications.
Benefits
Fiber lasers have established themselves as a preferred choice in the industry due to their numerous advantages:
High Energy Efficiency: One of the standout features of fiber lasers is their exceptional energy efficiency. With a wall plug efficiency exceeding 40%, fiber lasers convert a greater proportion of electrical power into laser light. This high efficiency translates to lower power consumption and reduced energy costs, making fiber lasers a cost-effective choice for long-term operations.
Precision in Cutting: Fiber lasers are renowned for their unparalleled precision, particularly when working with reflective materials such as metals. Their finely focused beam ensures accurate and clean cuts, which is highly valued in industries requiring meticulous detail and high-quality results. This precision makes fiber lasers ideal for applications in aerospace, automotive, and high-precision manufacturing where accuracy is critical.
Cost-Effectiveness: Although the initial investment in a fiber laser may be higher compared to some other laser types, the lower operating and maintenance costs contribute to a favorable total cost of ownership. Fiber lasers require less frequent maintenance and have a longer lifespan, which helps offset the initial expenditure over time. Their efficiency and reduced energy consumption further enhance their cost-effectiveness, providing a good return on investment for businesses looking to optimize their cutting operations.
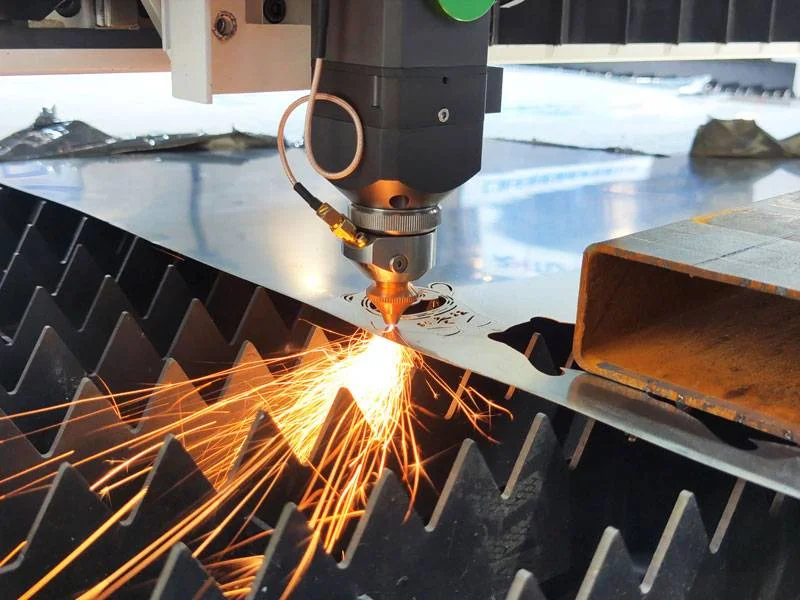
Fiber Laser Operation Principle
Step 1: Light Generation in Laser Diodes
Fiber lasers start with laser diodes, which transform electrical energy into light (photons) to be introduced into the fiber-optic cable. Known as the "pump source," these diodes use two differently charged semiconductors: one positively charged, seeking an extra electron, and one negatively charged, with a surplus of electrons. When these charges meet, the excess electron is released as a photon. As electrical current flows through the diodes, the photon production increases rapidly. This light is then pumped into the fiber-optic cable, setting the stage for laser beam generation.
Step 2: Light Guidance in the Fiber-Optic Cable
The fiber-optic cable guides the light by utilizing two key components: the core and the cladding. The core, made of silica glass and embedded with rare-earth elements, is where the light travels. The cladding surrounds the core and ensures the light stays within by utilizing total internal reflection. This occurs because the cladding has a lower refractive index than the core, causing light to bounce back into the core rather than escaping. This principle is similar to how light bends when transitioning between different media, such as air and water, but in fiber optics, it results in a controlled reflection that keeps the light focused and confined.
Step 3: Light Amplification in the Laser Cavity
As the light progresses through the fiber, it enters the laser cavity—a specialized region of the fiber that has been doped with a rare-earth element. Here, interactions between the light and the doped particles cause the particles' electrons to move to higher energy states. When these electrons return to their original state, they release additional photons. This process, known as "electron excitation" and "electron relaxation," amplifies the light. The laser cavity also includes fiber Bragg gratings, which act as mirrors: one reflecting light back into the cavity and the other selectively allowing some light to exit while reflecting the rest. This setup enhances the light amplification through stimulated emission, resulting in the formation of a coherent laser beam.
Step 4: Creation of Laser Light of a Specific Wavelength
The wavelength of the laser light produced depends on the doping element used in the laser cavity. Different dopants, such as erbium, ytterbium, neodymium, or thulium, generate specific wavelengths suited for various applications. For example, ytterbium-doped fiber lasers produce a wavelength of 1064 nm, which is ideal for tasks like laser marking and cleaning. The specific photons released by each doping element determine the wavelength, ensuring that the laser light generated is consistent and precise for its intended use.
Step 5: Shaping and Releasing the Laser Beam
The laser light exiting the resonant cavity is extremely well-collimated, or straight, due to the fiber's guiding properties. To achieve the desired beam shape and focus, additional components such as lenses and beam expanders are used. For instance, a 254 mm focal length lens might be employed for applications requiring deep penetration into materials, like laser engraving and texturing. This lens focuses more energy onto a smaller area, enhancing the laser's effectiveness. Different lenses provide various advantages, so selecting the appropriate lens is crucial for optimizing the laser's performance for specific applications.
Introduction to 1kw Fiber Laser Cutting Machine
The Krrass 1KW fiber laser cutting machine features a robust gantry structure with an aluminum alloy beam, imported grinding gear frame, high-precision linear guide drive system, advanced CNC laser cutting control, and a high-performance servo motor. This state-of-the-art machine integrates cutting-edge technologies in laser processing, precision engineering, and numerical control.
The Krrass 1KW fiber laser cutter is a top-selling model and is widely recognized for its versatility and performance. It is commonly used in various applications, including the production of stainless steel kitchen utensils, storage cabinets, and other cabinet components. The machine efficiently cuts a range of metal plates and pipes, including stainless steel, carbon steel, galvanized plates, electrolytic plates, brass, aluminum, various alloys, and rare metals.
Krrass offers a broad spectrum of power options for metal sheet fiber laser cutting machines, ranging from 1000W to 20000W, to accommodate diverse cutting needs and ensure optimal performance across different applications.
Various Industry Applciation By 1kw Fiber Laser
Manufacturing
- Metal Fabrication: Ideal for cutting and engraving stainless steel, carbon steel, aluminum, and other metals used in the production of machinery, tools, and components.
- Automotive Parts: Used for precision cutting of automotive components, including brackets, panels, and intricate designs for vehicle customization.
- Aerospace: Efficient for cutting high-strength alloys and precision parts required for aircraft and spacecraft.
Signage and Advertising
- Signage: Perfect for creating detailed and custom signs from various metals and materials, offering high precision and clean cuts for both indoor and outdoor use.
- Engraving: Suitable for engraving logos, text, and intricate designs on metal plaques, nameplates, and promotional items.
Home Appliances
- Kitchen Utensils: Used for cutting and engraving stainless steel and other materials used in the production of kitchen tools and appliances.
- Furniture: Helps in crafting and customizing metal components for furniture, such as cabinet handles, frames, and decorative elements.
Electronics
- Component Manufacturing: Enables precise cutting of metal and non-metal components used in electronic devices, including casings, connectors, and mounting brackets.
- Heat Sinks: Utilized for cutting and engraving heat sinks and other cooling components essential for electronic and computer hardware.
Medical Devices
- Surgical Instruments: Provides accurate cutting for high-precision surgical instruments and medical devices made from metals like stainless steel and titanium.
- Prosthetics: Used in the production of metal parts for prosthetic limbs and other medical aids.
Advantages of the 1kW Fiber Laser Machine
CypCut Control System
The 1kW fiber laser machine features the CypCut control system, which provides a vertical screen display offering enhanced response speed, contrast, and a wider viewing area compared to traditional horizontal screens. This advanced system also boasts low power consumption and high resolution. CypCut software supports various graphic data formats, including DXF, PLT, and LXD, and includes essential editing and typesetting functions. It automatically distinguishes between internal and external modes, features automatic typesetting, precise edge-finding methods, and a unique processing sequence browse function. One-key cutting path setting further streamlines operations and boosts efficiency.
Max Fiber Laser Generator
The Max fiber laser generator utilizes a modular design to offer exceptional beam quality and stability. Its compact structure and water-cooling system ensure reliable performance. The generator allows for continuous beam adjustment and transmits the laser through an optical fiber and QBH connector, making it suitable for laser cutting, welding, and other applications. It integrates well with robots or machine tools and is used in fields such as electronics, automotive parts, aerospace, and 3D printing.
Efficient Water Chiller
The water chiller includes a high and low-temperature control system that cools both the fiber laser and QBH crystal optics simultaneously. This design optimizes space and reduces costs.
Raytools Cutting Head
The machine is equipped with a Swiss Raytools autofocus cutting head, ideal for medium to high-power industrial applications. The cutting head features an imported closed-loop motor that enables high-speed perforation and cutting of various material thicknesses. It automatically adjusts to the best focus without manual intervention, enhancing processing efficiency and accuracy.
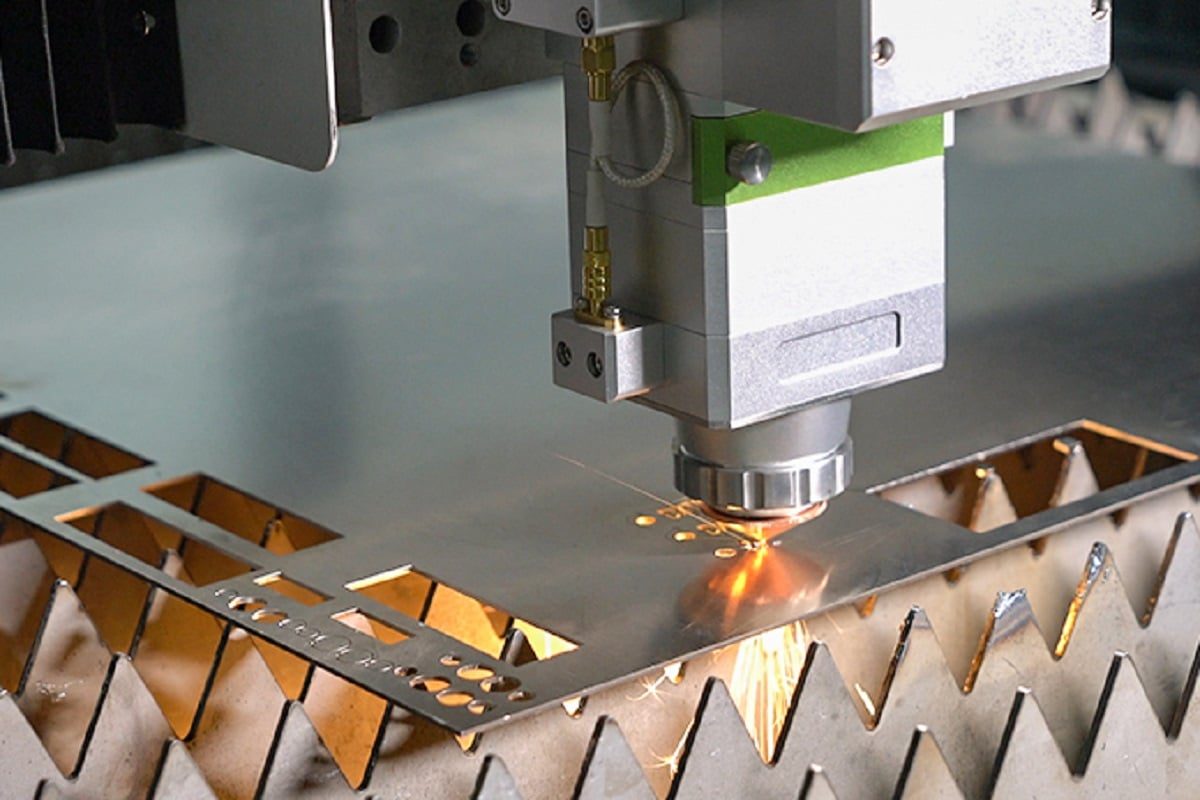
What Can a 1kW Fiber Laser Cut?
A 1kW fiber laser is capable of cutting a variety of metals with precision and efficiency. It can handle stainless steel up to 0.75 inches thick, carbon steels up to 0.5 inches thick, and mild steel up to 0.6 inches thick with high-quality results. Additionally, it can cut aluminum and aluminum alloys up to 0.4 inches thick, as well as copper and copper alloys up to 0.2 inches thick. This versatility makes the 1kW fiber laser suitable for applications in manufacturing, signage, home appliances, electronics, and more, delivering clean and accurate cuts across a range of metal materials.
Fiber lasers are renowned for their exceptional ability to cut metal with remarkable precision, efficiency, and cleanliness. Here's an overview of various metals that fiber lasers can effectively cut, highlighting their cutting depths and efficiency ratings:
- Stainless Steel: Fiber lasers can cut stainless steel up to 0.75 inches thick with an impressive efficiency of 95%. This demonstrates the laser’s powerful beam and precise cutting capability, making it ideal for manufacturing applications.
- Carbon Steels: Known for their robustness, carbon steels can be cut up to 0.5 inches thick with a 90% efficiency rating. Fiber lasers handle these materials with ease, producing smooth, high-quality cut edges.
- Mild Steel: With a cutting capability of up to 0.6 inches thick and an efficiency of 92%, fiber lasers effectively manage mild steel, which is commonly used in various industrial processes.
- Galvanized Steel: Fiber lasers can cut galvanized steel up to 0.5 inches thick, achieving an efficiency of 88%. This highlights the versatility of fiber lasers in handling different steel types.
- Aluminum and Aluminum Alloys: Aluminum, including its alloys, can be cut up to 0.4 inches thick with an efficiency rate of 85%. This showcases the laser’s ability to manage lightweight yet strong materials with precise power control.
- Copper and Copper Alloys: Despite their reflective nature, fiber lasers can cut copper and its alloys up to 0.2 inches thick with an efficiency of 80%. This reflects the advanced technology of fiber lasers in minimizing reflections and achieving clean cuts.
- Titanium: Renowned for its strength and lightweight properties, titanium can be cut up to 0.3 inches thick with an efficiency of 87%, making fiber lasers suitable for aerospace and other demanding applications.
- Nickel Alloys: Fiber lasers are also capable of cutting nickel alloys, which are essential for their high-temperature and corrosion-resistant properties. The efficiency of cutting these alloys is notable, demonstrating the adaptability of fiber laser technology.
What Max Thickness Can a 1kw Fiber Laser Cut
A 1kW fiber laser can typically cut metals to a maximum thickness of:
- Stainless Steel: Up to 0.75 inches
- Carbon Steel: Up to 0.5 inches
- Mild Steel: Up to 0.6 inches
- Aluminum and Aluminum Alloys: Up to 0.4 inches
- Copper and Copper Alloys: Up to 0.2 inches
These thicknesses can vary based on the specific machine and its settings, but these figures represent the general cutting capabilities of a 1kW fiber laser across different metals.
What Advantages of Fiber Laser For Metal Cutting
The use of fiber lasers for metal cutting offers several notable advantages, significantly improving both efficiency and cutting quality.
Precision is a key benefit, as fiber lasers deliver exceptionally accurate cuts with smooth edges and intricate details, making them ideal for complex designs and tight tolerances.
Speed is another advantage, with fiber lasers operating faster than traditional cutting methods. This capability greatly decreases processing times and boosts productivity.
Efficiency is also enhanced with fiber lasers, as they have high metal absorption rates, which translates to reduced power consumption and greater energy efficiency.
Their versatility allows them to handle a wide range of metals and be adjusted for various thicknesses and material types, enhancing their adaptability in different applications.
Low maintenance is a significant benefit, as fiber lasers have fewer moving parts and do not require mirrors or alignment procedures, unlike CO2 lasers, making them easier to maintain.
Safety is improved with fiber lasers due to their enclosed beam path, which minimizes direct exposure to the laser beam and enhances operational safety.
Finally, cost-effectiveness is achieved through the combination of high speed and efficiency, leading to lower operational costs and reduced material waste over time.
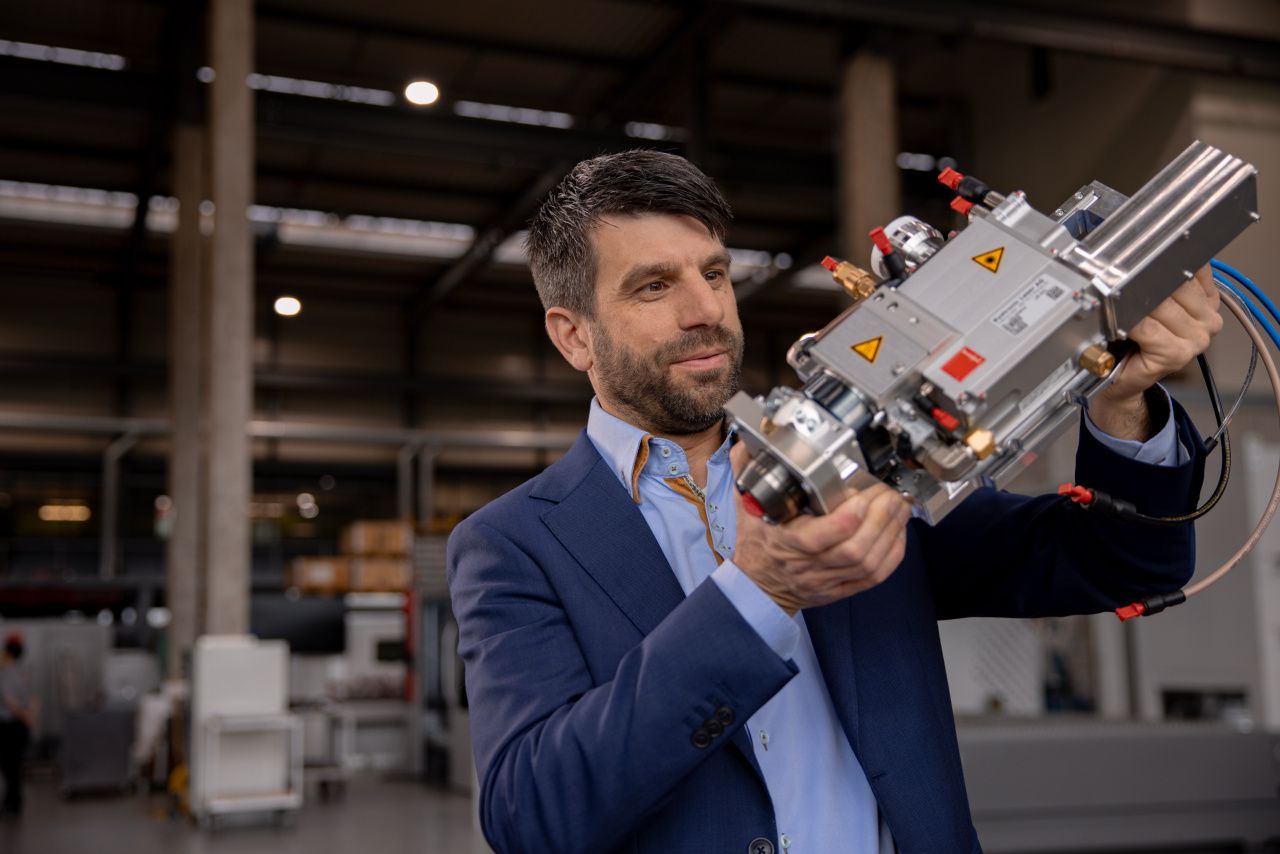
How to Optimize Fiber Laser Usage for Various Materials
Optimizing fiber lasers for cutting various materials requires understanding their unique characteristics and reactions to the laser cutting process. Proper preparation and handling enhance the efficiency and quality of cuts while extending the lifespan of the laser equipment. Below are essential preparation techniques for achieving optimal cutting results with a fiber laser.
Material Preparation Techniques for Optimal Cutting
Acrylic: Keep the protective film on to prevent burn marks. Use air assist to blow away fumes and molten particles, achieving a glossy edge finish. Fine-tune power and speed settings to avoid excessive melting.
Aluminum: Securely clamp the aluminum to prevent movement due to thermal expansion. Adjust the focus slightly above the surface to enhance cut quality and speed. Use a smaller diameter nozzle for a more concentrated cutting beam.
Wood: Ensure the wood has consistent, low moisture content to reduce variability in cutting performance. Clean areas with high resin or sap concentrations to prevent burning. Apply masking tape on the surface to reduce smoke staining.
Polycarbonate: Keep the protective film on both sides to protect from heat and reduce flare. Use strong air assist to blow away melted particles and prevent them from reattaching to the cutting edges. Operate at faster cutting speeds to minimize heat buildup and avoid melting.
Fabric: Stretch and secure the fabric flat to avoid movement or buckling during cutting. Conduct initial test cuts to determine the optimal frequency and power settings to prevent burning and maximize speed. Enhance exhaust systems to effectively evacuate smoke and particulate matter.
Conclusion
This guide has explored the capabilities of a 1kW fiber laser for cutting different materials. By understanding the unique properties of each material and adjusting the laser settings accordingly, operators can enhance cutting precision, speed, and quality.
The 1kW fiber laser is crucial in modern manufacturing, offering versatility and efficiency unmatched by traditional cutting methods. As this technology continues to evolve, it will undoubtedly continue to significantly impact the manufacturing landscape, driving innovations and improvements in various industries. If you are hesitating what power you really need, you can ask Krrass sales team for instant help.
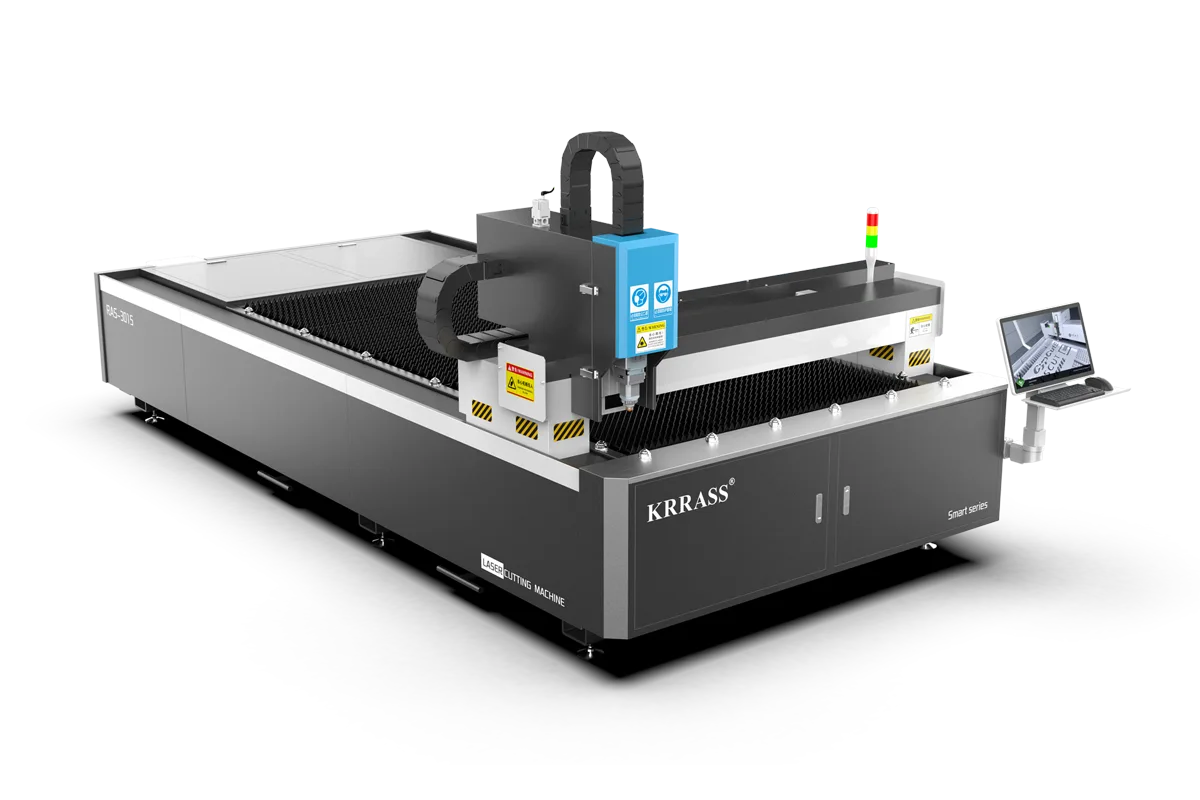