Stamping presses are indispensable machines in the manufacturing industry, facilitating the creation of various products through the process of metal stamping. This article delves into the essential principles behind stamping presses, exploring their functionality, types, and applications across diverse industries.
https://www.youtube.com/watch?v=F7IpxchOusk
Introduction to Stamping Presses
Stamping presses, also known as stamping machines or stamp presses, are mechanical devices designed to shape or cut metal sheets into specific forms or patterns. They exert immense force to deform or remove material from metal blanks, resulting in the production of components used in automotive, aerospace, electronics, and numerous other sectors.
The Stamping Process
The stamping process unfolds through a meticulously orchestrated series of key steps, each pivotal in ensuring the attainment of precise and uniform outcomes:
- Blanking: The initial step where a flat metal sheet, known as a blank, is placed into the stamping press.
- Die Setup: The die, a specialized tool with a cavity or cutout, is set in place within the press. The die determines the final shape or pattern of the stamped part.
- Stamping: The press applies force to the metal blank, forcing it into the die cavity. This action shapes or cuts the metal according to the die's specifications.
- Ejection: Once the stamping is complete, the formed part is ejected from the die, ready for further processing or assembly.
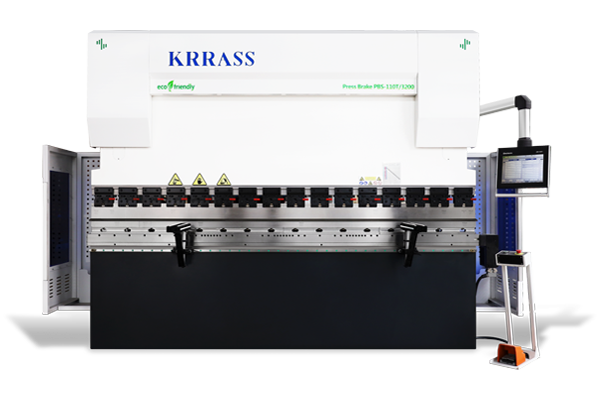
Types of Stamping Presses
Stamping presses come in a myriad of configurations, each meticulously designed to cater to specific applications and production demands across diverse industries. From mechanical presses harnessing mechanical linkages for high-speed operations to hydraulic presses offering unparalleled control over force and precision, the spectrum of options is vast.
- Mechanical Presses: These presses utilize mechanical linkages, such as crankshafts and flywheels, to deliver force to the metal blank. They are suitable for high-speed operations and can handle a wide range of materials and thicknesses.
- Hydraulic Presses: Hydraulic presses use hydraulic cylinders to generate force, offering greater control over speed and pressure. They excel in applications requiring precise force control or forming of complex shapes.
- Servo Presses: Servo presses incorporate servo motors for precise control over force, speed, and position. They are highly versatile and suitable for intricate stamping operations with demanding accuracy requirements.
- Pneumatic Presses: Pneumatic presses utilize compressed air to exert force on the metal blank. They are ideal for light-duty stamping tasks or applications where rapid cycling is essential.
Applications of Stamping Presses
Stamping presses are indispensable tools across a multitude of industries, serving as the cornerstone of manufacturing processes for an extensive array of components. Their versatility and efficiency make them integral in industries ranging from automotive and aerospace to electronics, consumer goods, medical equipment, and beyond.
- Automotive Industry: Producing body panels, chassis components, brackets, and other structural parts.
- Electronics Manufacturing: Fabricating enclosures, connectors, and contacts for electronic devices.
- Aerospace Sector: Manufacturing aircraft components such as fuselage panels, wing brackets, and engine parts.
- Consumer Goods: Creating appliances, hardware, and decorative metal items for household use.
- Medical Equipment: Crafting precision parts for medical devices, surgical instruments, and diagnostic equipment.
Stamping Press Comparison Table
Below is a comprehensive comparison table delineating the distinctive features and functionalities of various types of stamping presses. This detailed overview serves as a valuable resource for industries seeking to identify the most suitable press configuration to meet their specific production requirements.
Press Type | Operating Principle | Force Control | Speed Control | Accuracy | Application |
Mechanical Press | Mechanical linkage | Limited | Limited | Moderate | High-volume production |
Hydraulic Press | Hydraulic cylinders | Precise | Precise | Very high | Intricate stamping tasks |
Pneumatic Press | Compressed air | Limited | Limited | Moderate | Light-duty stamping |
Conclusion
Stamping presses indeed serve as the backbone of modern manufacturing, revolutionizing the production of intricate metal components with efficiency and precision. As technology advances, the evolution of stamping machines is paramount to meeting the dynamic demands of industries, fostering innovation, and advancing metalworking processes.
Recommendation
In this context, KRRASS emerges as a prominent player in the field of metalworking machinery. Renowned for its dedication to excellence and innovation, KRRASS offers a comprehensive range of high-quality products designed to cater to the diverse needs of contemporary manufacturing. Whether you seek cutting-edge servo presses for intricate stamping tasks or robust mechanical presses for high-volume production, KRRASS provides tailored solutions that epitomize reliability and performance. Their unwavering commitment to customer satisfaction and continual improvement ensures the delivery of machinery that excels in efficiency and accuracy. For businesses aspiring to elevate their metal stamping operations and remain at the forefront of the competitive landscape, KRRASS emerges as the trusted ally for success. Explore their product portfolio and witness firsthand the difference in quality, reliability, and technological advancement that KRRASS brings to the table.