Investing in a small hydraulic press brake can be a game-changer for workshops looking to enhance their metal bending capabilities without breaking the bank. These compact yet powerful machines offer a range of benefits, from precision and versatility to cost efficiency. Whether you are a small business or a large-scale manufacturer, a small hydraulic press brake can provide the perfect balance of performance and affordability, making it an essential tool for achieving high-quality metalworking results.
Introduction
Brief Overview of the Importance of Metal Bending in Manufacturing
Metal bending is a crucial process in manufacturing, used across various industries to create precise, durable, and functional components. From automotive parts to structural elements in construction, the ability to bend metal accurately ensures the production of high-quality products that meet exact specifications. Efficient metal bending enhances the structural integrity of products and allows for innovative design and customization, making it an indispensable aspect of modern manufacturing.
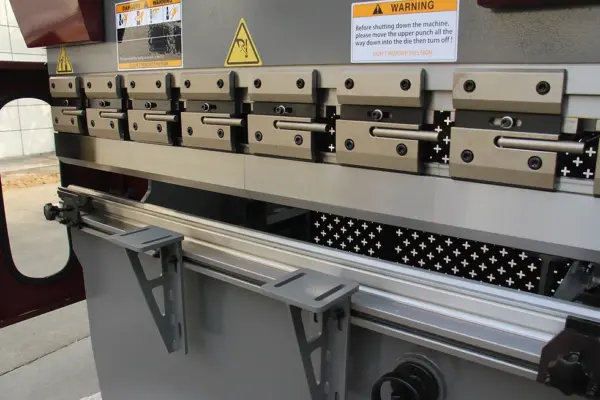
Introduction of the Small Hydraulic Press Brake as a Cost-Effective Solution
In the realm of metal bending, the small hydraulic press brake stands out as a cost-effective and versatile solution. Unlike larger, more expensive machines, small hydraulic press brakes offer a compact design that fits seamlessly into workshops of all sizes. They provide the power and precision needed for a wide range of bending tasks, from simple bends to complex shapes, without the hefty price tag associated with larger industrial equipment.
This article explores the key benefits of incorporating a small hydraulic press brake into your workshop. From its cost-efficiency and precision to its versatility and productivity-enhancing features, a small hydraulic press brake proves to be an essential tool for businesses aiming to optimize their metal bending operations while maintaining budgetary constraints.
What Is A Small Press Brake
A small hydraulic press brake is a compact machine designed for bending and shaping sheet metal and plates. Available in hydraulic, electric NC, and CNC configurations, these machines offer affordability and high efficiency. Small press brakes typically support bending lengths ranging from 1600mm to 2500mm and are capable of handling capacities ranging from 40 tons up to 300 tons.
From the automotive industry to aircraft manufacturing, and from kitchen appliances to construction, press brakes are extensively used for shaping metal parts across various industrial applications. These machines are renowned for their precision and efficiency, making them indispensable in modern manufacturing. Press brakes come in various models, ranging from manual to advanced CNC (Computer Numeric Control) machines, each offering distinct advantages depending on specific requirements.
The performance and efficiency of a press brake are highly dependent on its components. To fully grasp how these machines bend and shape metal with such precision, it is crucial to understand their structure and the different parts that make up a press brake.
Main Components
Frame
The frame is the main structure of the press brake, providing the necessary support and stability for the entire machine. Made from high-strength steel or other durable materials, the frame ensures that the machine can withstand the substantial forces generated during the bending process. A robust frame is essential for maintaining the machine's accuracy and longevity.
Hydraulic System
The hydraulic system powers the press brake, delivering the force required to perform bending operations. This system typically consists of a hydraulic pump, cylinders, and fluid reservoirs. The hydraulic pump generates pressure by moving hydraulic fluid through the cylinders, which then apply force to the punch. This hydraulic pressure allows for precise control over the bending process, enabling the creation of consistent, high-quality bends.
Punch and Die
The punch and die are the primary tools used to shape the metal. The punch, attached to the ram, descends into the die, which is mounted on the press brake's bed. There are various configurations of punches and dies available, each designed for specific bending requirements. Common types include V-dies for standard bending, radius dies for creating curved bends, and hemming dies for folding edges. The versatility of these tools allows for a wide range of bending operations to be performed with a single machine.
Back Gauge
The back gauge is a mechanism that positions the metal accurately for consistent bends. It consists of adjustable stops that hold the workpiece in place, ensuring precise alignment with the punch and die. The back gauge can be manually adjusted or controlled by a computer system, allowing for quick and accurate positioning of the metal. This feature is crucial for achieving consistent, repeatable bends in production runs.
Control System
The control system allows operators to set and adjust parameters for precise bending operations. Modern small hydraulic press brakes often feature computerized numerical control (CNC) systems, which provide advanced programming capabilities and automation. Operators can input specific bend angles, material thicknesses, and other parameters into the control system, which then precisely executes the bending process. This automation reduces the likelihood of human error and increases production efficiency.
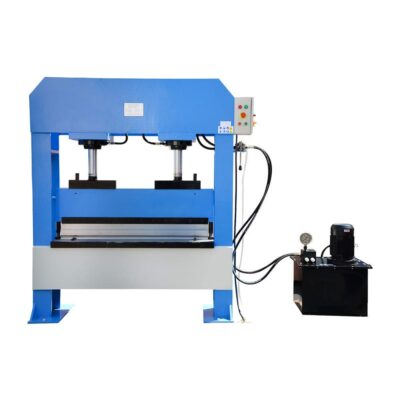
Understanding Cost-effectiveness of Small Hydraulic Press Brake
Initial Investment vs. Long-Term Savings
When considering a small hydraulic press brake, the initial investment is relatively modest compared to larger, more complex machines. Typically, a small hydraulic press brake can cost between $10,000 and $50,000, depending on the brand and features. This lower upfront cost makes it an attractive option for small to medium-sized businesses looking to expand their metal bending capabilities without a significant financial burden.
Over time, the efficiency and precision offered by a small hydraulic press brake can lead to significant long-term savings. For instance, businesses may experience up to a 20% reduction in material waste due to the machine's accuracy. Additionally, the ability to complete jobs more quickly—often 30% faster than with manual or older machines—contributes to lower overall production costs. These factors collectively enhance the machine's cost-effectiveness, making it a smart investment for businesses aiming to improve their bottom line.
Maintenance and Operational Costs
Small hydraulic press brakes are designed to be durable and reliable, which helps minimize maintenance costs. Regular maintenance, such as oil changes, lubrication, and component inspections, is straightforward and inexpensive compared to the upkeep required for larger machines. On average, annual maintenance for a small hydraulic press brake might cost between $500 and $2,000, significantly less than the $5,000 to $10,000 required for larger models.
Furthermore, these press brakes typically consume less energy, reducing operational costs. For example, a small hydraulic press brake might use 30% less energy than a larger, less efficient machine, translating to substantial savings on electricity bills over time. The combination of low maintenance and operational expenses further enhances the cost-effectiveness of small hydraulic press brakes, ensuring that they remain an economical choice for businesses over their lifespan.
Return on Investment (ROI) for Small Businesses
For small businesses, the ROI of a small hydraulic press brake can be substantial. The machine’s ability to perform a wide range of bending tasks with high precision and consistency leads to increased productivity and the potential to take on more projects. For example, businesses using small hydraulic press brakes often report a 15-25% increase in production capacity, enabling them to fulfill more orders and boost revenue.
The versatility of small hydraulic press brakes allows businesses to diversify their offerings and attract a broader client base. By reducing material waste and operational costs, companies can achieve faster ROI, often within 1-2 years of the initial purchase. Additionally, the increased efficiency can lead to labor cost savings of up to 20%, as fewer man-hours are required to complete the same amount of work.
Investing in a small hydraulic press brake can significantly boost a small business's profitability and competitive edge in the market. For instance, a company that invests $30,000 in a small hydraulic press brake and experiences an annual cost savings of $10,000 from reduced waste, energy savings, and increased productivity can expect to recoup their investment within three years. Beyond that, the continued savings contribute directly to the company's profit margins, illustrating the significant financial benefits of this investment.
Precision and Versatility of Small Brakes
Precision in Metal Bending and Its Importance
Precision in metal bending is crucial for producing high-quality components that meet exact specifications. A small hydraulic press brake offers exceptional accuracy, often achieving tolerances as tight as ±0.01 inches. This high level of precision ensures that each bend is consistent, reducing the likelihood of errors and rework. In industries such as aerospace and automotive, where precision is paramount, the ability to consistently produce accurate bends is vital for maintaining product integrity and safety.
Versatility in Handling Different Materials and Thicknesses
A small hydraulic press brake is not only precise but also highly versatile, capable of handling a wide range of materials and thicknesses. These machines can bend various metals, including steel, aluminum, copper, and stainless steel, making them suitable for diverse applications. The versatility extends to handling different material thicknesses, from thin sheet metal to thicker plates, typically ranging from 0.5 mm to 10 mm.
Applications in Various Industries
Automotive Industry: Producing body panels, chassis components, and brackets with high precision to ensure safety and performance.
Aerospace Industry: Creating lightweight yet strong components that must adhere to strict tolerances for optimal performance and safety.
Construction Industry: Fabricating structural elements, such as beams and supports, which require precise bends to ensure structural integrity.
Electronics Industry: Manufacturing enclosures and frames that protect delicate electronic components, requiring precise and consistent bends.
Kitchen Appliances: Crafting parts for appliances like ovens, refrigerators, and dishwashers, where both functionality and appearance are important.
Enhancing Productivity
How Small Hydraulic Press Brakes Improve Workflow Efficiency
Small hydraulic press brakes integrate advanced CNC (Computer Numerical Control) systems to automate bending operations efficiently. Operators can program specific bend angles, dimensions, and sequences, minimizing manual adjustments and significantly reducing human error. This automation not only enhances productivity by optimizing cycle times but also ensures precise and consistent bending results across various production tasks.
These machines also feature sophisticated setup capabilities, including tooling libraries and automatic tool changers. Tooling libraries facilitate quick retrieval and setup of bending configurations, while automatic tool changers enable rapid changeover between different bending tasks. This versatility allows operators to maximize machine uptime and streamline production throughput, adapting swiftly to changing manufacturing demands.
Moreover, small hydraulic press brakes are engineered for precision and reliability in metal bending. Their precise control mechanisms guarantee consistent bending outcomes, even during extensive production runs. This reliability minimizes material waste and rework, optimizing material usage and overall operational efficiency. Integrated safety features such as light curtains and emergency stop buttons further enhance operational safety, protecting operators and minimizing downtime due to potential accidents or injuries.
Features that Contribute to Faster Setup and Operation
Small hydraulic press brakes incorporate advanced features that enhance efficiency and precision in metal bending operations. CNC (Computer Numerical Control) systems empower operators to digitally input bending parameters, significantly reducing setup time and ensuring accurate, repeatable results. This capability not only streamlines production processes but also minimizes the potential for human error, enhancing overall productivity on the shop floor.
Additionally, these machines are equipped with automatic back gauges that precisely position the workpiece, minimizing the need for manual adjustments and improving setup efficiency. By automating this critical aspect of the bending process, small hydraulic press brakes optimize workflow management, allowing operators to focus more on production tasks and less on setup logistics.
Furthermore, small hydraulic press brakes feature advanced tooling libraries that store multiple tool setups digitally. This feature enables quick retrieval and setup of preferred bending configurations, facilitating seamless transitions between different jobs. Combined with programmable tooling capabilities that automate tool changes and adjustments based on job requirements, these machines reduce downtime between tasks and maximize machine uptime for enhanced operational efficiency.
Moreover, these press brakes are designed with user-friendly interfaces, including intuitive controls and touchscreen interfaces. These features simplify machine operation, making it easier for operators to learn and operate the equipment efficiently. This intuitive interface design not only improves operator proficiency but also enhances overall workplace productivity by minimizing training time and maximizing operational uptime.
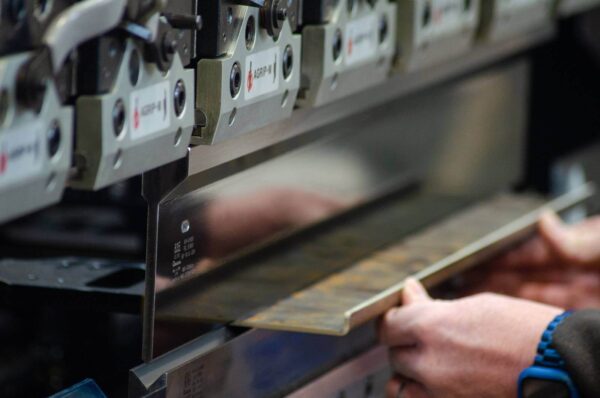
Why Invest in a CNC Small Hydraulic Press Brake?
Steel and metal products are ubiquitous in daily life, mostly crafted using CNC brake presses. Investing in a new CNC mini press brake machine is crucial for boosting productivity and efficiency.
Our focus lies in manufacturing advanced automatic CNC hydraulic press brakes, hybrid servo press brakes, and robotic press brakes. Upgrading to cost-effective CNC hydraulic press brake machinery elevates automation levels, saving valuable working hours and reducing labor costs. This enhancement not only bolsters your company's image and capabilities but also promises substantial benefits.
By adopting cutting-edge technology, you streamline production processes, ensuring precision and consistency in metal bending. This strategic investment optimizes operational efficiency, paving the way for sustained growth and competitive advantage in your industry.
How Do Small Press Brakes Differ from Larger Models?
Size and Footprint
Small press brakes are compact and occupy less floor space compared to larger models. For instance, a typical small press brake might have dimensions around 2 meters in length and 1 meter in width, while larger models can exceed 6 meters in length and 3 meters in width.
Tonnage Capacity
Small press brakes generally range from 20 to 100 tons of bending force. This capacity is suitable for bending thin to medium-thickness materials like 3 mm to 10 mm steel sheets. In contrast, larger press brakes can handle from 100 tons up to over 1000 tons, capable of bending thicker materials up to 20 mm or more.
Precision and Accuracy
Despite their smaller size, small press brakes maintain high precision in bending operations. They often achieve bending accuracies within ±0.1 mm, crucial for industries requiring exacting standards such as aerospace and automotive manufacturing.
Setup and Operation Efficiency:
Small press brakes feature advanced CNC (Computer Numerical Control) systems that streamline setup and operation. Operators can program bending sequences digitally, reducing setup times by up to 50% compared to manual setups. This efficiency translates into higher productivity and reduced production costs.
Cost-effectiveness:
Small press brakes offer a cost-effective solution for small to medium-sized workshops. They typically cost between $20,000 to $100,000, depending on specifications and features. In contrast, larger press brakes can range from $100,000 to over $1 million, making them a significant investment for large-scale manufacturing operations.
Application Versatility:
Small press brakes are versatile tools suitable for various industries and applications. They are commonly used in sectors such as electronics, signage, and custom fabrication. Their ability to handle diverse materials including aluminum, stainless steel, and mild steel makes them adaptable to different production needs.
Top Small Hydraulic Press Brake Supplier
1. AMADA (https://www.amada.com/)
Brand: Japan, Founded in 1946
AMADA press brake manufacturer is a large international company in sheet metal processing machinery. They provide sheet metal machinery, Amada press brake, cutting machines, grinding machines, stamping presses, and precision welding machines.
Amada is a Japanese company founded in 1946 with a long history. Amada’s products have a comprehensive and reasonable mechanical structure, providing users with the best quality guarantee.
2. Trumpf (https://www.trumpf.com/)
Brand: German, Founded in 1923
Germany Trumpf is an innovative high-tech company, divided into three parts: Machine tools(Trumpf press brake, shear), laser technology, and electronics. It is one of the best manufacturers of sheet metal fabrication machinery, industrial lasers, and industrial application electronic products in the world.
TRUMPF is guiding the technological development trend with continuous innovation, establishing new technical standards, and is committed to developing and updating more products for the majority of users.
3. Accurpress (https://www.accurpress.com/)
Brand: Canada, Established in 1973
Accupress is a professional manufacturer of CNC machine tools, established in Canada in 1973. It mainly manufactures Accurpress press brakes, shearing machines, tooling, and other peripheral products.
Accupress specializes in large-tonnage, tandem press brake, and robot automation. Accupress is known for its high manufacturing quality and advanced technology.
4. Bystronic ( https://www.bystronic.com/)
Brand: Italy, Established in 1964
Bystronic is a world-famous provider of sheet metal processing solutions, established in Switzerland in 1964.
The company focuses on the automation of the complete material and data flow of the cutting and bending process chain.
Bystronic mainly provides laser cutting machines, press brakes, automation systems, and related software.
5. Durma ( https://www.durmark-machinery.com/ )
Brand: Turkey, Established in 1956
Durmazlar Machinery was established by Ali Durmaz in 1956. Durma press brake manufacturer is a world-renowned metal sheet processing base.
Durma’s products include Durma CNC press brakes, turret presses, punching machines, all-solid-state fiber lasers, shears, ironworkers, plate rolls, angle rolls, and saws.
6. LVD (https://www.lvdgroup.com/)
Brand:Belgium , Established in 1950
LVD press brake manufacturer founded in Belgium in the 1950s, LVD is a leading enterprise in laser, punching, and bending technology.
It is a world-famous manufacturer of metal forming equipment, with the most comprehensive press brake production line. LVD offers customized multi-axis CNC plate bending machines with Easy-Form laser angle measurement technology.
Where to Buy the Best Small Hydraulic Press Brake
Explore the range of hydraulic CNC press brake machines available at KRRASS Machinery! Share your sheet metal plate details (thickness, length, and material type) along with your contact information. KRRASS Machinery will assist in selecting the optimal press brake machine model for your needs and provide a quotation promptly.
We offer a diverse selection of hydraulic CNC press brakes. Our inventory includes the 20-ton mini press brake, 30-ton mini press brake, 40-ton small press brake, and 63-ton small press brake, all available for immediate purchase at competitive prices with discounts. If you require a larger machine model or a customized solution, feel free to reach out via email at [email protected].
This approach ensures you find the perfect metal press brake to enhance your production capabilities efficiently and affordably with KRRASS Machinery.
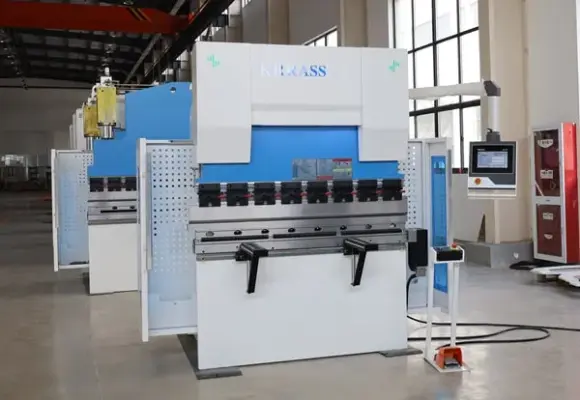