Cutting operations are fundamental to part fabrication in the manufacturing industry, with sheet metal laser cutting being one of the primary techniques used. This process is highly effective for cutting a wide range of materials, including metals, alloys, and non-metals. Sheet metal laser cutting, a thermal process that utilizes beams of light (lasers) to precisely melt or vaporize the material on the workpiece, is known for its efficiency in achieving the desired shape. In this article, we'll explore the key aspects of using a sheet metal laser cutting machine, providing you with essential knowledge before employing this advanced technology. Let's dive in!
What is Sheet Metal Laser Cutting?
Subtractive manufacturing processes are critical for the modification of materials for part fabrication. Sheet metal laser cutting is one of the standard methods for cutting and removing components from a workpiece. The technique involves cutting out pieces of material using laser beams.
The laser cutting technique runs on computer numerical control (CNC) technology, which accounts for its impeccable precision. Before the CNC cutting or laser cutting operation, the operator must have input codes or programs detailing designs or patterns into the computer.
Sheet Metal Laser Cutting Process
Laser cutting metal involves the precise use of laser beams to melt and cut through metals and alloys, resulting in smooth, sharp edges. The process relies on two synchronized operations working together to achieve these results.
First, the material absorbs the concentrated laser beam, which provides the energy necessary for cutting. Simultaneously, a cutting nozzle, aligned with the laser beam, delivers process gas that plays a crucial role. This gas not only shields the processing head from vapors and splashes but also aids in clearing away excess material from the cutting path.
There are three primary methods employed in laser cutting sheet metal:
- Laser Beam Fusion Cutting
In laser beam fusion cutting, an inert gas, typically nitrogen, is used. This gas continuously vaporizes the cutting gap of the material in a low-reactivity environment. As the molten material is expelled, the inert gas prevents oxidation at the cutting edge, ensuring a clean finish without interfering with the cutting process. This method is particularly well-suited for cutting flat, thin sheets of aluminum alloys and stainless steel, where high aesthetic quality and minimal post-processing are desired. - Laser Beam Sublimation Cutting
Laser beam sublimation cutting, as the name suggests, involves the immediate transition of the material from a solid to a gaseous state, bypassing the liquid phase entirely. Instead of melting the material like other laser cutting processes, it evaporates. Inert gases are again employed to blow the vaporized material out of the kerf, ensuring no oxidation occurs on the cutting edge. This technique is often used for cutting organic materials like wood, leather, and textiles. - Laser Beam Flame Cutting
Laser beam flame cutting utilizes a combustible gas, such as oxygen, to expel molten material. The laser heats the workpiece, causing it to ignite spontaneously and continue burning, thanks to the oxygen gas. The exothermic reaction provides additional energy for the cutting process through oxidation. Flame cutting is ideal for materials like mild steel and fusible ceramics. However, because the process involves oxidation, it can lead to burns on the cutting surface. Optimizing process parameters is essential to minimize the formation of burrs and achieve clean cuts.
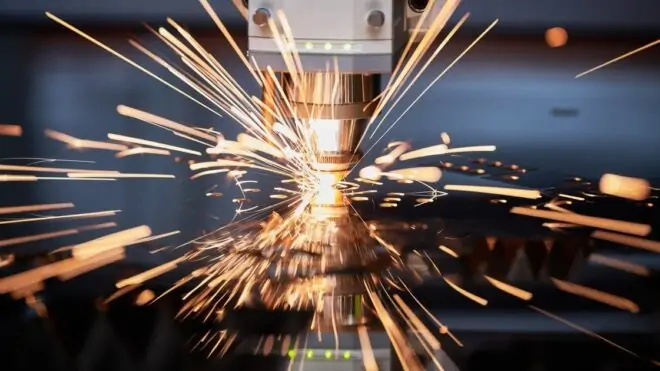
Types of Lasers for Sheet Metal Cutting
Manufacturers utilize three main types of lasers for cutting materials, each with unique characteristics suited to specific applications. Here's an overview of these laser types used in sheet metal cutting:
- Fiber Lasers
Fiber lasers employ fiberglass to generate high-powered, precise cuts. Originating from a "seed laser" and amplified by specialized glass fibers, these solid-state lasers are versatile, capable of cutting nearly all materials, including metals, alloys, and non-metals like wood, glass, and plastics. Beyond cutting, fiber lasers excel in operations such as annealing and engraving. Known for their durability, they boast an extended service life exceeding 25,000 hours and require minimal maintenance, making them a popular choice in various industries. - CO2 Lasers
CO2 lasers create laser beams by passing an electric current through a tube filled with a mixture of inert gases, predominantly nitrogen and helium. These lasers are widely used due to their efficiency, cost-effectiveness, and ability to cut a variety of materials at high speeds. However, they generate less cutting power compared to fiber lasers, making them less ideal for cutting sheet metal. Instead, CO2 lasers are typically used for cutting non-metals and organic materials like wood, paper, and acrylic. - Crystal Lasers (Ndor Nd)
Crystal lasers derive their beams from either Nd(neodymium-doped yttrium aluminum garnet) or Nd(neodymium-doped yttrium orthovanadate) crystals, with the latter being more commonly used. These lasers produce powerful beams suitable for cutting plastics, metals, and non-metals such as ceramics. However, they are expensive and have a shorter lifespan, typically lasting between 8,000 and 15,000 hours. Due to their high cutting power but limited durability, crystal lasers are employed selectively in applications requiring their specific capabilities.
What Type of Laser is Best for Cutting through Metal?
If you need to cut through metal, a fiber laser is your best option. Fiber laser cutters are among the most efficient tools for quickly slicing through tough materials like steel, stainless steel, galvanized steel, copper, aluminum, and more. Whether you're working on large-scale projects or creating small, personalized items, a fiber laser cutter is an excellent choice for achieving precise and perfect cuts!
Why Fiber Lasers
Fiber lasers are widely recognized as the best choice for cutting through metal due to a combination of advanced technological features and practical benefits that set them apart from other cutting methods. Here's an in-depth look at why fiber lasers excel in metal cutting:
- Unmatched Precision and Speed:
Fiber lasers are known for their ability to produce extremely precise cuts, thanks to their narrow and focused laser beams. This precision allows for intricate designs and complex shapes to be cut with remarkable accuracy, making them ideal for applications where detail is paramount, such as in the aerospace, automotive, and electronics industries. The high-speed operation of fiber lasers also means that large quantities of metal can be processed quickly, enhancing overall productivity. - Versatility Across Materials:
One of the standout features of fiber lasers is their ability to cut through a diverse range of metals. Whether you're working with stainless steel, carbon steel, aluminum, copper, brass, or even reflective materials like gold and silver, fiber lasers deliver consistent and high-quality results. This versatility makes them an invaluable tool for manufacturers who need to work with multiple types of metal without compromising on quality. - Energy Efficiency and Sustainability:
Fiber lasers are highly energy-efficient, converting a substantial percentage of the electrical input into laser output. This efficiency not only reduces energy consumption, lowering operational costs, but also contributes to a more sustainable manufacturing process. The reduced energy footprint is particularly beneficial for industries looking to minimize their environmental impact while maintaining high production standards. - Low Maintenance and Durability:
Fiber lasers are built to last, with fewer moving parts and no delicate mirrors or lenses that can become misaligned or damaged over time. This robust design results in significantly lower maintenance requirements compared to CO2 or crystal lasers. Additionally, fiber lasers have an impressive operational life, often exceeding 25,000 hours, which means less downtime and more continuous production. This reliability is a key factor in industries where consistent operation is critical. - High Power Density for Thick Metals:
The high power density of fiber lasers allows them to cut through thicker and denser metals with ease. This capability is particularly important in heavy industries such as shipbuilding, construction, and machinery manufacturing, where materials like thick steel plates are common. The ability to cut through these tough materials without sacrificing speed or accuracy gives fiber lasers a significant edge over other cutting technologies. - Cost-Effectiveness Over Time:
While the initial investment in a fiber laser cutting machine may be higher than other options, the long-term benefits make it a cost-effective choice. The low operating costs, including reduced energy consumption and minimal maintenance, quickly offset the initial expense. Over time, the durability and efficiency of fiber lasers lead to substantial savings, making them a smart investment for businesses focused on long-term growth and sustainability. - Enhanced Cutting Quality:
Fiber lasers produce clean cuts with minimal burring and reduced need for post-processing. The precision of the laser beam ensures that the material's edges are smooth and free of distortions, which is particularly beneficial in industries where the aesthetic quality of the cut is as important as its functional quality. This superior cutting quality reduces the need for secondary finishing processes, saving both time and resources. - Safety and Ease of Use:
Modern fiber laser cutting machines are designed with user safety and convenience in mind. They often come equipped with advanced control systems that allow for easy operation and precise adjustments. Safety features such as enclosed cutting areas, automatic shutoffs, and real-time monitoring ensure that the cutting process is not only efficient but also safe for operators.
In conclusion, fiber lasers represent the pinnacle of metal cutting technology, offering a blend of precision, versatility, efficiency, and durability that is unmatched by other methods. Whether you're engaged in large-scale industrial production or specialized manufacturing, fiber lasers provide the tools necessary to achieve high-quality results with minimal effort and maximum efficiency. Their ability to handle a wide range of materials and thicknesses, coupled with their long-term cost-effectiveness, makes them an indispensable asset in the modern manufacturing landscape.
How Accurate is Sheet Metal Laser Cut?
Laser cutting can achieve incredible accuracy, reaching as precise as ± 0.0005 inches—thinner than a human hair! This exceptional precision makes laser cutting perfect for industries that demand intricate and detailed work. It’s especially well-suited for applications such as manufacturing precision parts or creating complex components like the fine, jagged teeth used in medical instruments.
Laser cutting is an efficient, safe, and extremely accurate method compared to other traditional sheet metal-cutting techniques. The laser-cutting process leverages a computer-operated program to carefully cut materials within an acceptable accuracy range. The laser-cutting process can also be integrated with CAD software that guides the laser to make its cuts. Ideally, laser cutting can focus on about 25 microns, which is about ¼ of the width of a strand of human hair. Additionally, the cut width can be extremely small, at less than 0.001 inches.
Factors That Affect Laser Cutting Accuracy
To achieve a higher level of impeccability with laser cutting, consider the following factors:
- Material Type: A smoother or thinner material can give you a more exact cut. You should use appropriate machine settings for each type of material and material composition.
- Laser Beam Spot Size: Using a smaller laser beam spot size guarantees more meticulous cuts compared to wider spot sizes.
- Laser Power Level: Consider using more powerful laser beams with higher intensity to cut through thicker materials for flawless, even cuts.
- Workbench Accuracy: How you position the workpiece material on the bench can also affect the veracity of the cuts. A workbench that is not well stabilized can cause vibrations, making the process lose its fidelity to the original design.
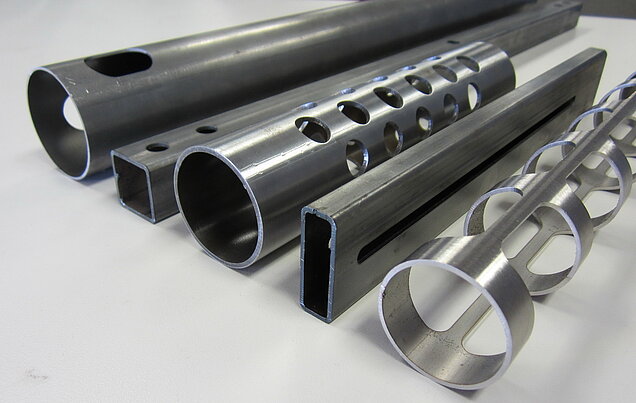
Achieve Supreme Accuracy with KRRASS Machinery
For unmatched laser cutting precision, trust KRRASS Machinery. As a leading provider of advanced metal fabricating equipment, KRRASS offers top-of-the-line fiber laser cutting machines renowned for their accuracy.
KRRASS’s high-powered lasers are engineered to deliver exceptional precision with their fine spot size and rapid cutting speeds. Whether you're cutting sheet metal for automotive parts or crafting intricate designs for jewelry, our machines consistently produce outstanding results.
Seize this opportunity to elevate your production capabilities! Contact us today to discover how KRRASS Machinery can enhance your laser cutting accuracy and transform your manufacturing processes.
Advantages of Sheet Metal Laser Cutting Machine
High Precision and Accuracy
Laser cutting is ideal for sheet metal cutting due to its exceptional precision. These machines are capable of making intricate cuts with remarkable accuracy, making them the preferred choice for industrial applications where detailed designs and tight tolerances are required. Some laser cutters can achieve precision cuts with an accuracy of up to 0.0005 inches, which is why they remain a staple in manufacturing. The laser melts the metal during cutting, resulting in minimal to no burring and leaving a clean, smooth, and sharp edge.
Automated Process
Laser cutting is driven by Computer Numerical Control (CNC) systems, which means that once the operator inputs the necessary program, the process runs automatically. This automation reduces the need for human intervention and overall labor, while also minimizing the margin for error and enhancing cutting efficiency.
Damage Prevention
Contrary to the misconception that laser cutting can cause warping, the process actually minimizes the risk of material distortion. The heat generated by the laser only affects very small areas of the material, preserving its overall tolerance. Additionally, because laser cutting is a fast process, the heat is concentrated on the specific areas being cut, preventing any significant impact on the surrounding material. This ensures that there is little to no distortion or warping of the materials being cut.
Compatibility with Various Materials
One of the key advantages of laser cutting is its versatility in handling a wide range of materials. Whether you're cutting copper, aluminum, stainless steel, or even titanium, laser cutting can efficiently slice through each material. This capability is due to the use of high-temperature lasers that can melt through various types of metals with ease.
Cost-Effectiveness
While laser cutting machines may come with a high upfront cost, they are more economical compared to other CNC machines in the long run. A single laser cutting machine can handle all your cutting operations without the need for modifications, making it a versatile tool for various tasks.
Additionally, these machines are highly durable; since the laser doesn’t physically contact the material, there’s minimal friction and wear, resulting in lower maintenance needs. With fewer components and reduced servicing requirements, the operational costs of using a laser cutter are generally lower compared to traditional manufacturing tools.
High Versatility
Laser cutting is not only compatible with a wide range of materials but also boasts impressive versatility. It can handle various cutting tasks, from simple and straightforward cuts to complex shapes and designs requiring tight tolerances. This adaptability makes laser cutting an ideal choice for diverse applications across many industries.
Low Energy Consumption
While laser cutters do require energy to heat and melt materials, they are generally more energy-efficient compared to other cutting methods. The laser cutting process involves fewer moving parts, which translates to lower energy consumption. Additionally, the high cutting speed of laser machines contributes to quicker processing times, further enhancing their energy efficiency.
What Are the Cons of Sheet Metal Laser Cutting Machine
Requires a Skilled Operator
Using a laser cutting machine effectively requires a skilled operator who is knowledgeable about its features and capable of identifying and resolving issues promptly. Incorrect setup or operation can lead to damage to both the machine and the materials being cut. Therefore, if you plan to run a laser cutting service, hiring a professional with expertise in operating these machines is essential.
Limitations on Metal Thickness
While laser cutters are highly effective for most materials, including sheet metal, they do have limitations when it comes to metal thickness. Typically, laser cutters can handle aluminum sheets up to 15mm thick and steel sheets up to 6mm thick. For cutting thicker metals, alternative methods may be more appropriate.
Release of Harmful Fumes and Gases
The laser cutting process involves heating materials to the point of melting, which releases harmful fumes and gases. To ensure safety, it is crucial to operate laser cutters in well-ventilated areas or use proper ventilation systems to manage and mitigate these emissions.
High Initial Investment
Acquiring a high-quality laser cutter involves a significant initial investment, often exceeding $2,000—about twice the cost of other cutting machines like water jet cutters. If you plan to invest in a laser cutter for your business, be prepared for this substantial upfront cost.
To meet the precision and quality specifications of laser cutting for your parts, adhere to the following guideline.
Guidancen for Laser Cutting for Parts
1. Choose the Right Materials
The choice of material is essential for any manufacturing process. The material you select for your part depends on the properties you want for the final product. Besides metal sheets like aluminum and zinc, plastics and other polymers are good options for part fabrication, depending on your needs. Some properties manufacturers look for when choosing a material include flexibility, malleability, ductility, rigidity, etc.
2. Design With Software That Creates Vector Files
Laser cutting machines only work with vector files. Therefore use software like Adobe illustrator to vectorize your designs. These files have formats like .ai, .step, .eps, etc.
3. Remember the Kerf
Kerf is the portion of the material that evaporates as the laser beam focuses on the workpiece. When designing your part, you must factor the kerf into your designs.
4. Details Shouldn’t be Smaller Than Metal Thickness
Metal thickness is an essential factor to consider with laser cutting service. The thicker your metal sheets, the less likely the lasers penetrate.
5. Minimum Distance Between Cutting Lines
Adequate spacing is vital for obtaining the best outcomes of laser cutting. The minimum distance in sheet metal laser cutting should equal your material’s thickness. For instance, if you are cutting a 2 mm metal sheet, you should leave a space of 2 mm.
Applications
1. Medical Equipment
Trolleys, beds, surgical equipment, orthopedic pins, rods, etc., all contain laser-cut metals. Though many surgical instruments are now 3D printed, laser cutting is the go-to technique for fabricating them.
2. Jewelry Production
Most jewelry designs contain intricate designs which laser cutters can easily map out. Often, jewelry pieces are designed from thin materials. Hence, laser cutting is a good fit for jewelry fabrication.
3. Interior Design
Laser-cut sheet metals are an excellent choice for room dividers which can help improve the overall outlook of a room and create more space. Leveraging the precision of laser cutting with the manufacturer’s creativity can give you that custom looks you want for your room.
4. Aerospace Industries
Because of the high dimensional accuracy, the aerospace industry is one of the most significant users of laser cutting technology. Most of the parts of airplanes, and other devices like metal detectors, trolleys, conveyors, etc., undergo some cutting operations during manufacture.
Which Material Should You Never Cut in the Laser Cutter?
PVC, vinyl, and artificial leathers
they release chlorine gas, which can absolutely ruin your laser cutter’s optics, metal parts and control system, not to mention that it is pretty nasty for humans too. Chlorine gas is horribly irritating to the lungs, and in high concentrations can kill within 30 minutes.
Thick polycarbonate
This is pretty likely to catch fire, and the long thin trails of soot that are given off from polycarbonate fires can cause severe damage to your laser cutter. Any type of smoke inhalation isn’t good for your lungs, and there is the danger of the fire spreading from your machine to other parts of your workshop too.
ABS
the tough, super strong material that we all recognise and love as Lego should never be used in your laser cutter. Not only is it prone to catching fire (with all the related damage to the optics and so on that can be caused), but it will also leave a nasty mess on the cutting bed of your machine. Add to that the fact that it can release the poisonous gas hydrogen cyanide – which can be deadly pretty quickly – you’re going to want to avoid attempting to cut this one.
HDPE (milk bottle plastic)
while it can be tempting to use your laser cutter to repurpose or upcycle old milk bottles, it isn’t worth the risk. HDPE is highly likely to catch fire and melt in your machine, causing damage to the cutting bed if it melts, with potential damage to almost every other part of the machine from the smoke.
Polystyrene foam
another material that catches fire and burns quickly, with the related damage that is likely to be caused, such as damage to the optics. After a polystyrene foam fire, there are often melted deposits left on the cutting bed of the machine – so it really isn’t worth the risk.
Polypropylene foam
there are many uses for polypropylene foam, but many of these require cutting it to specific shapes, which is why so many people think that cutting it with their laser cutter is a great idea. But it catches fire fast, and during the fire, it is likely to drip, and those drips continue to burn, causing further damage. After the fire is extinguished, any drips set rock solid, meaning that the cutting bed of your laser cutter is ruined, alongside any other damage to the optics or other parts.
Epoxy
this is another material that burns, it is best to avoid getting epoxy anywhere near your laser cutter. It doesn’t just risk fire either – when epoxy burns, it releases poisonous fumes that can cause damage to the lungs too.
Fibreglass
since fibreglass is made up of epoxy (which we just mentioned as being bad news for both you and your laser cutter) and glass, which also doesn’t cut well in a laser cutter, it is best to avoid cutting fibreglass. The risk of fire, potential damage to the optics of your laser cutter, as well as poisonous gases – it simply isn’t worth trying to cut fibreglass with your laser cutter.
Coated carbon fibre
while some thin carbon fibre mats can be cut with lasers (albeit with the risk of material fraying, but that won’t ruin your laser cutter), any coated carbon fibre should be kept away from your machine. Aside from the risk of toxic fumes being released, where the material that coats the carbon fibre is unknown, you’re risking fire, burning material drips and damage to all parts of the machine.
Materials with sticky glue backing
cutting materials with any types of glue are likely to be bad news for the lens of your laser cutter. When glue vaporises as the material is cut, it can start to coat the laser lens – which then heats, and can potentially crack the lens. Add that to the increased risk of fire, and it is just not worth the risk.
Foodstuffs
while you could cut food in a laser cutter, with just the increased risk of fire to worry about, it isn’t worth the risk to your machine. Different types of food will release smoke, oil and may catch fire when it is being cut, which can cause a mess on the cutting bed that can be hard to clean, and depending on the food, you might also cause damage to optics. On top of that, if you have cut any materials that are potentially toxic prior to cutting whatever food you’ve put in there, then you risk cross-contamination, with dodgy tummies (and worse) occurring by cutting food with your laser.
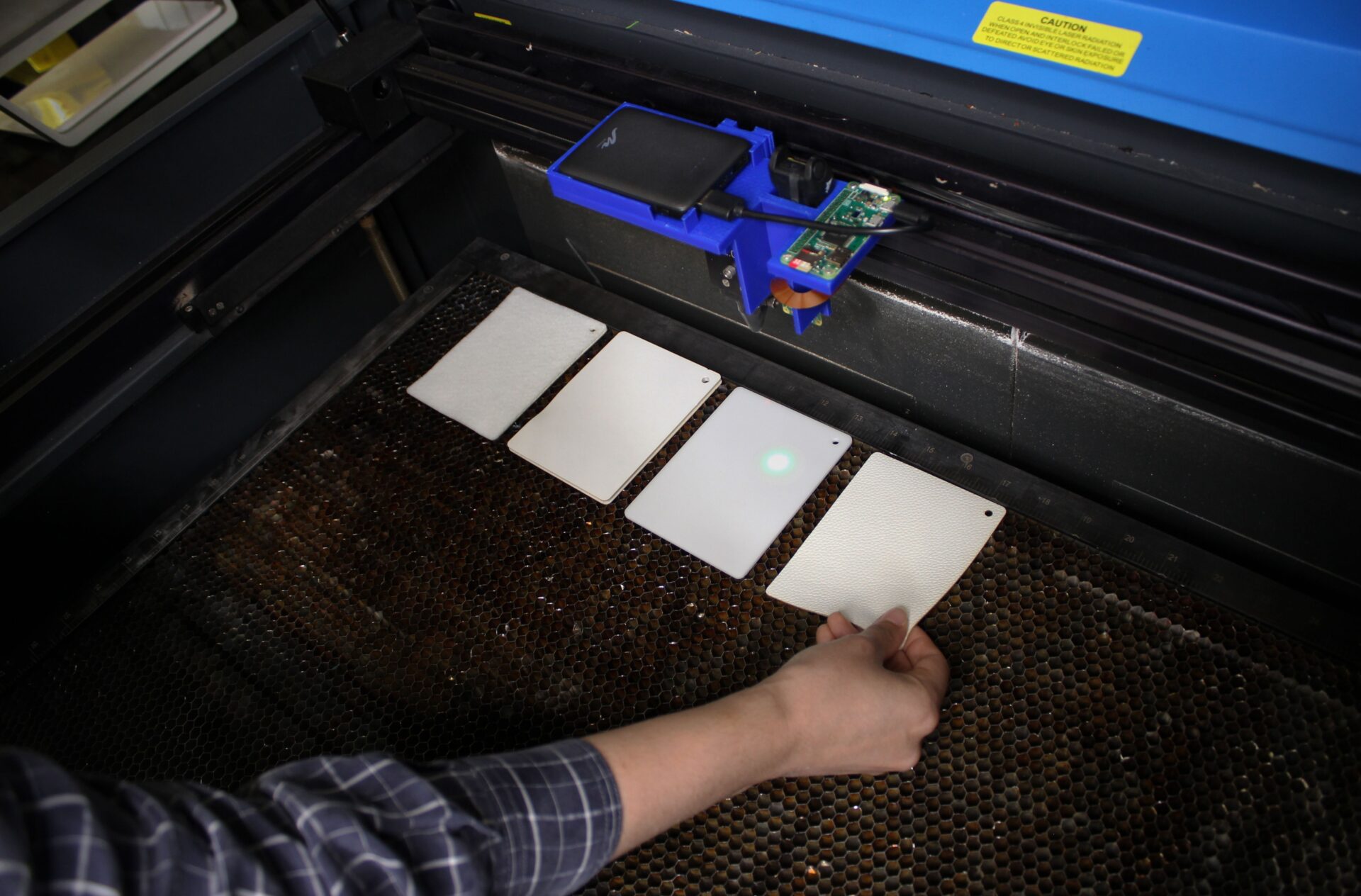
Ways That May Damage Your Sheet Metal Laser Cutting Machine
1. Not testing a sample of your material
Failing to do a test on a sample of material before starting a cut is a big cause of laser cutters being ruined. As we’ve already touched on, you can’t assume that every sheet of material will be exactly the same as the last, and if you’re cutting organic materials such as wood, or leather with your laser cutter, there may be different amounts of resin or oil in the material.
Aside from knowing whether the material will create the best finish, you need to know if the material might start to smoke or burn easily. You’ll only know that this is the case once you’ve done a test, so be sure to factor in testing your materials before getting started.
2. Neglecting Proper Machine Maintenance
Just as you wouldn’t purchase an expensive sports car and expect it to run flawlessly forever without maintenance, the same principle applies to your laser cutter. After the initial excitement of your first cuts with a new machine, it's crucial to focus on understanding and implementing its maintenance requirements.
Different types of laser cutters and brands have varied maintenance needs, but generally, there are tasks that must be performed daily, weekly, monthly, every six months, or at other intervals. Once you determine the schedule for these tasks, make sure to mark them in your calendar and adhere strictly to the routine. Regular maintenance is essential for ensuring your laser cutter's longevity and consistent performance.
If your laser cutter isn’t in daily use, you might be able to extend the intervals between some maintenance tasks (such as after a certain number of operating hours). In this case, keeping detailed records is vital to ensure you don’t miss any critical maintenance activities and to keep the machine running smoothly.
It's also important to maintain not just the laser cutter itself but its peripherals, including gas assists, air dryers, and regulated power supplies. Each of these components has its own maintenance requirements. Failing to properly care for these peripherals can lead to malfunctions or downtime, impacting the operation of your laser cutter.
3. Preparing Your Machine for Extended Periods of Inactivity
When your workshop is closed for an extended period, such as during the Christmas break, it’s important to properly prepare your laser cutter for inactivity. If your workspace maintains a constant temperature, you may only need to turn off the machine. However, if your workshop lacks heating and outside temperatures are expected to drop significantly, additional precautions are necessary.
Always follow the manufacturer’s recommendations for shutting down the machine for longer periods. Ensure that your premises are securely closed—an open window can significantly lower the room temperature. Once you return and resume operations, perform the necessary checks and maintenance before starting any new jobs to ensure the laser cutter is in optimal condition.
To ensure the safety of yourself and your team, adhere to the following guidelines:
- Never modify, adapt, or disable any safety features installed by the manufacturer.
- Always use the laser cutter with covers in place and ensure that all locking mechanisms are functioning properly.
- Avoid looking directly into the laser beam.
- Wear the appropriate Personal Protective Equipment (PPE) at all times when operating the laser cutter.
- Only cut materials that are approved by the manufacturer and avoid cutting unsuitable or hazardous materials.
- Never leave the laser cutter operating unattended.
- Keep a properly maintained fire extinguisher nearby and ensure it is readily accessible.
- Wait for materials to cool before removing them from the cutting bed.
- Regularly clean the machine and remove debris and dust after each job.
- Ensure the laser cutter is always used with a functioning exhaust system.
- Do not operate the laser cutter if the exhaust or air filtration systems are not working correctly.
Conclusion
With advancements in technology and ongoing innovation, the future of laser cutting accuracy promises even greater possibilities. Imagine the potential when combining these precise tools with artificial intelligence or machine learning!
In conclusion, laser-cutting accuracy is crucial for modern manufacturing across industries such as aerospace, automotive, and electronics. It enables businesses to produce high-precision components, enhance efficiency, and minimize material waste.
Don’t settle for anything less than perfection. Choose KRRASS Machinery today and experience the pinnacle of accuracy with our cutting-edge sheet metal laser cutting machines. Your business deserves nothing but the best!
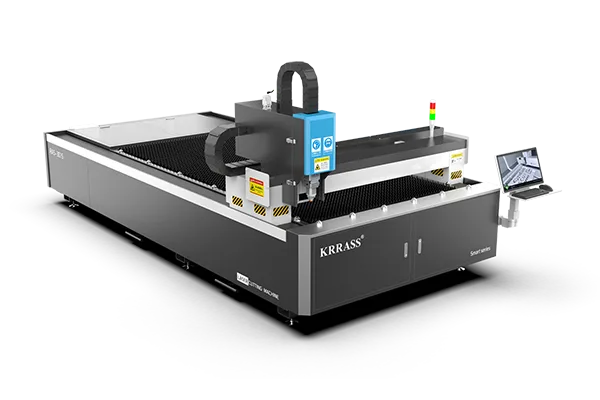
Reviewed by 1 user
Appreciate this article, help lots before i made a decide to purchase the laser machine