Addressing Hardness and Other Material Property Variations
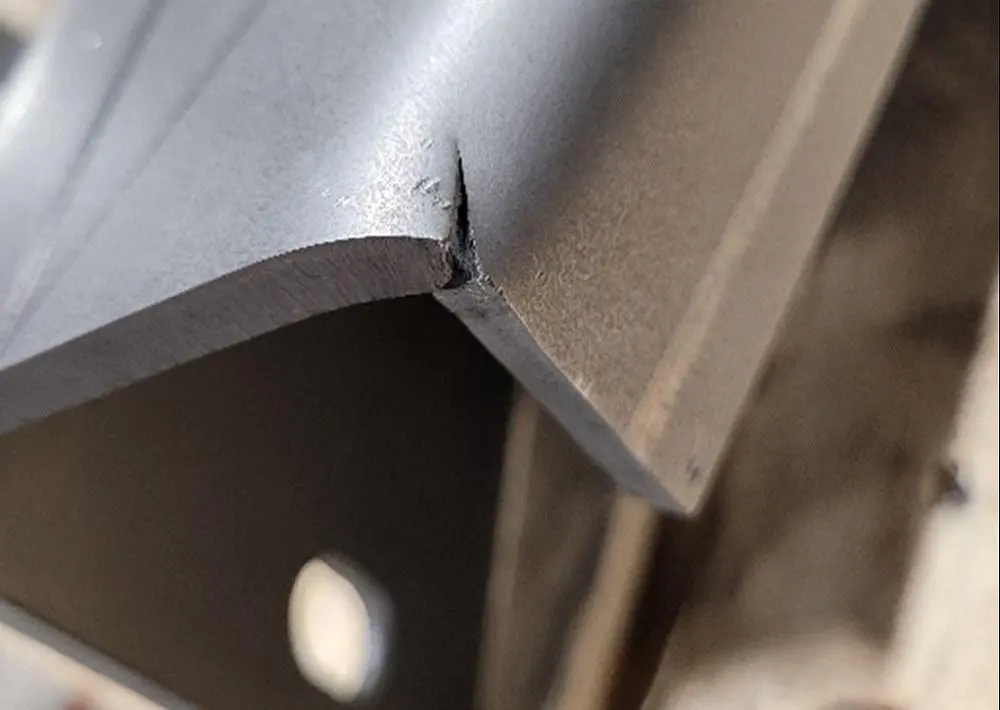
Question: We have encountered cracking at the edges of several different 0.25-inch-thick A36 parts after bending (see Figure 1). We have previously bent these same parts without any problems, but recently cracks have started to appear. The external bend angles range from 75 to 90 degrees, and the specified inside bend radius is 0.25 inches. We are using a 2-inch V die and a punch with a 0.236-inch radius.
We have noticed that cracking occurs regardless of whether we bend with or against the material grain, although it seems to be more pronounced when bending with the grain. However, this alone does not seem to explain the cracking issue, as we have had other batches of parts that did not crack, irrespective of grain orientation. We are currently investigating whether all the cracked parts came from the same sheets. We are also verifying the grain directions by checking the laser nests.
One possibility is that the cracked parts were mistakenly cut from the wrong material, such as C-1010. However, we would expect the lower hardness of C-1010 to make it less prone to cracking compared to A36. Furthermore, since both are mild steels, neither should crack when bent over a 2-inch die.
We were hoping you could provide some insight into the causes of cracking like this. How does hardness affect bendability? What other factors could have changed and led to cracking in this manner? Considering that all the cracks originated on the edge of the part, could changes in the laser cutting conditions have affected the edge hardness and caused this issue?
Answer: The hardness of steel can significantly impact its ability to bend without fracturing. Steel with a high hardness rating, such as hardened or tempered material, will be more brittle and less ductile than softer steel. Consequently, it becomes more challenging to bend without the risk of cracking or breaking. Additionally, when sheet metal or plate is laser- or plasma-cut, the heat-affected zone (HAZ) near the cut becomes hardened (see Figure 2). The extent of this zone can vary depending on the thickness and type of metal (see Figure 3).
Indeed, hardening of the edge can affect the material's formability and machinability, as the hardened region tends to be more brittle and less ductile compared to the rest of the material. Consequently, edge cracking becomes a distinct possibility, particularly if the laser power and cutting speed were not optimized to minimize the HAZ. To achieve a softer edge, additional processing or heat treatment may be necessary to restore the desired material properties.
During the bending process, the outer grains of the steel experience tension, while the inner grains experience compression. Harder steels are less able to deform under these stresses, which can lead to fractures along the outer grains. In contrast, softer steels are more malleable and can deform better under stress, allowing for bending without breaking.
The thickness of the sheet also plays a role in its bendability. Thicker steel requires more force to bend, increasing the likelihood of cracking or breaking, especially if it is already hardened or tempered.
When working with steel, it is important to consider its hardness and thickness to determine its ability to bend without fracturing. Softer and more malleable metals are generally easier to work with, while harder metals require more careful handling to avoid damage.
Regarding Hardness
The hardness range for A36 steel is not explicitly defined by standards organizations. However, it is generally known to have a Brinell hardness range (a measure of a material's resistance to indentation) between 119 and 159. The hardness of A36 steel can vary depending on factors such as the specific heat treatment used, material thickness, and any welding or heating processes employed during fabrication.
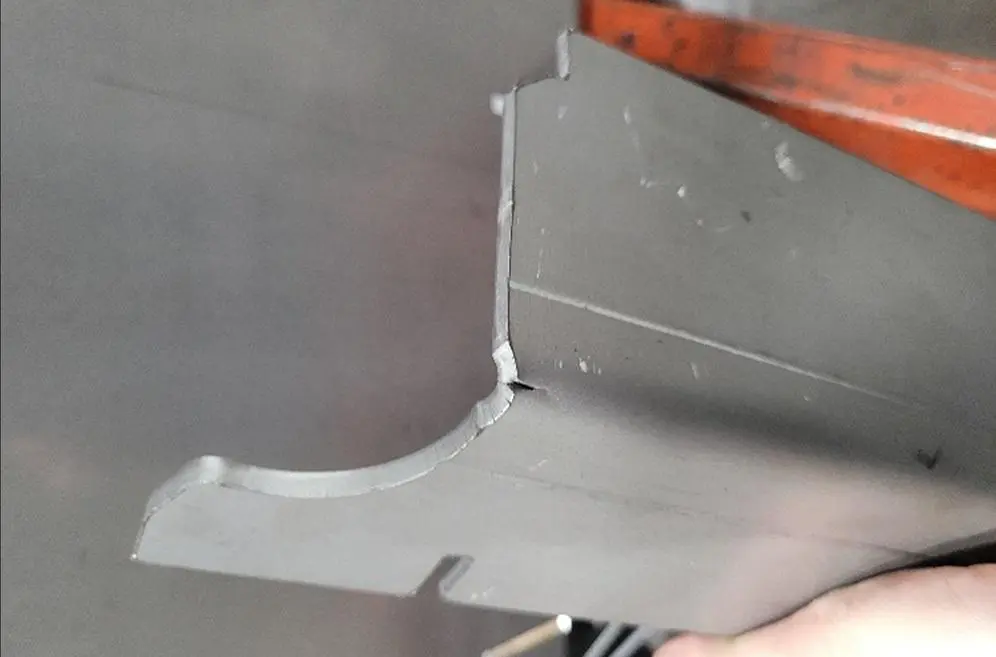
If you require a specific hardness tolerance rating for your A36 steel application, it is advisable to work with your supplier to determine the appropriate heat treatment and quality control measures needed to achieve the desired hardness and avoid or minimize cracking.
The Effect of HAZ on Forming
During laser cutting of A36 steel, the heat generated by the laser can lead to localized heating and cooling, potentially resulting in a hardened edge. However, the extent of hardening depends on several factors, including laser power, cutting speed, and material thickness.
Insufficient control of laser power and cutting speed can cause the material to melt and rapidly solidify, resulting in a hardened edge. This process is known as laser quenching. The extent of hardening is also influenced by material thickness. Thinner materials cool more rapidly, leading to a higher degree of hardening at the edge.
However, if the laser cutting process is well-controlled, it is possible to minimize the extent of hardening. For instance, using lower laser power and slower cutting speed, depending on the laser system employed, can reduce the HAZ and produce less hardening.
An extensive HAZ can also affect the material's mechanical properties. If the HAZ is too large, the material properties in that region can be compromised, making it more susceptible to cracking or other defects during subsequent forming. Localized stresses can cause the material to crack along the edge, particularly for materials with high hardness, such as hardened or tempered steel, which tend to be more brittle and less ductile than softer steel. Even though you are bending mild steel, the cracking you are experiencing may result from increased or inconsistent hardness.
Inconsistencies in material properties can also occur, as it is an inherent issue in any given metal. The material itself becomes the weak point in the entire forming process, causing problems beyond your control. Based on the description provided, your initial analysis seems correct—hardness is likely the primary factor causing difficulties.
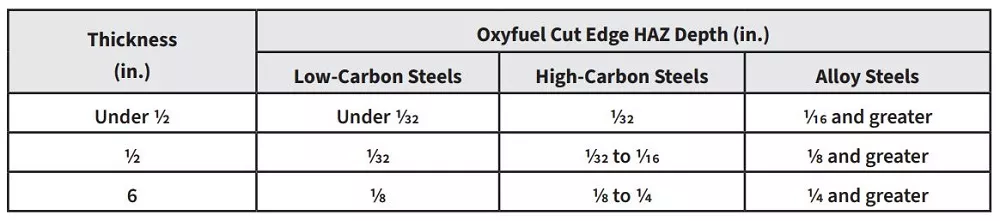
Learn more about our products, please visit and subscribe to our Youtube channel