Mastering press brake operation is crucial for beginners in the sheet metal fabrication industry. Whether you're new to the field or looking to refine your skills, understanding the best practices for press brake operation can significantly improve your efficiency and ensure high-quality results. This guide is designed to provide beginners with practical tips and techniques for safe and effective press brake operation, covering everything from initial setup to advanced bending strategies. By following these best practices, you can enhance your operational proficiency and produce precise, reliable bends every time.
Introduction
Mastering the operation of a press brake is crucial for anyone involved in metal fabrication. This skill ensures precision, efficiency, and safety in bending metal sheets, which is a fundamental process in manufacturing a wide range of products. Skilled operation of a press brake can lead to higher quality outputs, reduced waste, and increased productivity. Moreover, understanding the nuances of different press brake types, such as hydraulic and CNC, can significantly enhance a fabricator's ability to choose the right equipment for specific tasks, optimizing the production process.
Understanding Press Brakes
A press brake is a machine used in metalworking to bend and shape sheet metal and plate materials. It operates by clamping the material between a matching punch and die, then applying force to bend the material into the desired shape. Press brakes are essential in manufacturing and fabrication industries, producing components for various applications such as automotive parts, appliances, and construction materials.
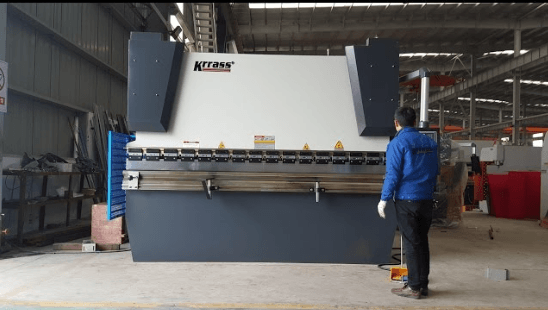
Components and Function of Press Brake
Frame and Ram: The frame serves as the robust structural foundation of the press brake, supporting the ram's movement. Together, they provide stability and rigidity crucial for maintaining bending accuracy, especially when handling heavy or thick materials.
Bed and Back Gauge: The bed acts as the stationary base where the material rests during bending, ensuring uniform support to prevent material deformation. Meanwhile, the back gauge functions as a precision positioning device, allowing operators to accurately position and hold the material for consistent bends throughout the production process.
Control Unit and Tooling: Powered by advanced CNC systems, the control unit enables precise programming of bending sequences and real-time monitoring of operations. This capability not only enhances operational efficiency but also facilitates complex bending tasks with high repeatability. Tooling, comprising punches and dies, shapes the material according to specified designs, demanding meticulous selection and maintenance to uphold bending precision and product quality.
Hydraulic System and Safety Features: In hydraulic press brakes, the hydraulic system generates the force required to operate the ram effectively, facilitating smooth and controlled bending operations. Safety features such as guards, light curtains, and emergency stop buttons ensure operator safety by mitigating potential hazards during machine operation. These features are indispensable for creating a secure work environment and safeguarding both personnel and equipment.
Foot Pedal: Operating the foot pedal initiates and halts the ram's movement, granting operators hands-free control over the bending process. This functionality enhances operational flexibility and safety by allowing operators to maintain a safe distance while managing bending tasks effectively.
What Are the Types of Press Brakes
Hydraulic Press Brakes
- Operation: Hydraulic press brakes use hydraulic fluid to generate the force needed to bend metal sheets.
- Advantages & Applications: They offer high bending accuracy, excellent control over speed and force, and are suitable for heavy-duty applications such as automotive, aerospace, and heavy machinery manufacturing.
Mechanical Press Brakes:
- Operation: Mechanical press brakes utilize a mechanical flywheel and clutch system to exert force on the material.
- Advantages & Applications: Known for faster cycle times and cost-effectiveness in high-volume production environments. They are commonly used in industries requiring speed and repetitive bending tasks.
Pneumatic Press Brakes:
- Operation: Pneumatic press brakes operate using compressed air to power the bending process.
- Advantages & Applications: They offer quick setup times, energy efficiency, and are suitable for lighter gauge materials. Pneumatic press brakes find application in industries requiring rapid production of smaller parts, such as electronics and appliance manufacturing.
CNC Press Brakes:
- Operation: CNC press brakes are equipped with Computer Numerical Control (CNC) systems for precise control over the bending process.
- Advantages & Applications: Automation allows for complex bends, high repeatability, and reduced setup times. They are ideal for industries demanding high precision and flexibility in bending operations, including custom fabrication and aerospace.
Electromagnetic Press Brakes:
- Operation: Electromagnetic press brakes use electromagnetic force to apply pressure to the material.
- Advantages & Applications: Offering precise control over force and speed, they are suitable for sensitive materials. Electromagnetic press brakes are used in industries requiring precise bending without material deformation, such as electronics and medical device manufacturing.
Key Terminology in Press Brake Operation
Understanding key terminology is crucial for mastering press brake operation and effectively communicating within the sheet metal fabrication industry.
Bend Allowance: The amount of material length required to form a bend. It accounts for material stretch and compression during bending.
Bend Radius: The inside radius of the bend. It determines how tightly the material can be bent without fracturing.
Bend Angle: The angle formed between the two legs of the bent material.
Springback: The tendency of metal to return to its original shape after being bent. It must be compensated for in bending calculations.
Tonnage: The force exerted by the press brake ram onto the material during bending. It is measured in tons and correlates with the material thickness and type.
Die Opening: The gap between the punch and die when the press brake ram is fully open. It determines the maximum thickness of material that can be bent.
Punch: The upper tooling component that applies force to the material, causing it to bend against the lower tooling component (die).
Die: The lower tooling component that supports the material during bending and determines the final shape of the bend.
Back Gauge: A positioning system that moves the material accurately along the bed of the press brake, ensuring precise bending locations.
Crowning: The slight curve in the bed or ram of the press brake to compensate for deflection during bending, ensuring uniform bend angles across the length of the material.
CNC (Computer Numerical Control): A control system that automates the press brake's operation, allowing for precise control over bending parameters and sequences.
Programmable Controller: A device used to input and store bending programs, including bend angles, depths, and sequences, for consistent and repeatable operations.
Tooling Setup: The process of selecting and installing punches and dies of appropriate sizes and shapes to achieve desired bend configurations and angles.
Press Brake Cycle: The sequence of operations that the press brake performs to bend a piece of material, including lowering the ram, forming the bend, and returning to its starting position.
Potential Harzards of Press Brake Operation
Crushing and Pinching Hazards:
- Risk: The powerful force exerted by the press brake's ram and tools can crush or pinch fingers, hands, or other body parts if caught between the tooling and material.
- Prevention: Use safety guards, light curtains, and two-hand controls to prevent access to the danger zone during operation. Operators should never reach into the machine while it is in operation or within the area where tooling moves.
Material Handling Risks:
- Risk: Improper handling of metal sheets or plates can lead to injuries such as cuts, strains, or falls.
- Prevention: Train operators in safe lifting techniques and provide appropriate lifting equipment. Ensure materials are securely positioned and clamped before initiating bending operations.
Noise and Vibration Exposure:
- Risk: Press brakes can generate high levels of noise and vibration during operation, potentially causing hearing damage and long-term health issues.
- Prevention: Implement soundproofing measures in the workplace, provide hearing protection for operators, and conduct regular noise level assessments. Maintain equipment to reduce vibration and ensure stable operation.
Ejection of Workpieces:
- Risk: During bending, workpieces may unexpectedly eject from the press brake, posing impact hazards to nearby personnel.
- Prevention: Securely clamp workpieces and use appropriate tooling to prevent movement during bending. Maintain a safe distance from the machine during operation and wear appropriate personal protective equipment (PPE).
Electrical and Hydraulic Hazards:
- Risk: Malfunctions or failures in electrical or hydraulic systems can result in electrical shocks, fluid leaks, or other hazards.
- Prevention: Regularly inspect and maintain electrical connections, hydraulic hoses, and fluid levels. Ensure operators are trained in emergency shutdown procedures and use lockout/tagout protocols when servicing equipment.
Tooling and Equipment Maintenance:
- Risk: Improper maintenance of punch and die tooling, or neglecting machine upkeep, can lead to tool breakage, equipment malfunction, and safety hazards.
- Prevention: Establish a routine maintenance schedule for inspecting and lubricating tooling and machine components. Follow manufacturer guidelines for replacement intervals and ensure only qualified personnel perform repairs and adjustments.
Press Brake Operation Safety Precautions
Personal Protective Equipment (PPE):
- Always wear appropriate PPE, including safety glasses, hearing protection, gloves, and steel-toed shoes.
- Ensure clothing is fitted and free of loose ends that could get caught in moving parts.
Machine Safety Features:
- Familiarize yourself with the press brake’s safety features, including emergency stop buttons, safety guards, and light curtains.
- Ensure all safety features are functional before starting any operation.
Operational Safety Guidelines:
- Never bypass or override safety mechanisms.
- Do not operate the press brake if you are fatigued or under the influence of medications or substances that may impair judgment or reflexes.
Material Handling:
- Inspect materials for defects, such as oil, rust, or warping, which can affect bending quality.
- Use proper lifting techniques and equipment to handle heavy or awkwardly shaped materials safely.
Setup and Calibration:
- Follow manufacturer guidelines for machine setup and calibration.
- Ensure the back gauge and tooling are correctly adjusted before initiating any bending operations.
Tooling Safety:
- Use the correct punches and dies for the job, ensuring they are securely mounted and in good condition.
- Avoid placing hands near tooling or between moving parts during operation.
Bending Operation:
- Stand clear of the ram and back gauge during bending cycles.
- Avoid distractions and maintain focus on the task at hand.
Emergency Procedures:
- Know the location of emergency exits, first aid kits, and fire extinguishers.
- Establish and communicate emergency procedures with all operators and personnel in the vicinity.
Regular Maintenance:
- Schedule routine maintenance and inspections of the press brake to ensure it operates safely and efficiently.
- Keep all machine components clean and lubricated according to manufacturer recommendations.
Training and Supervision:
- Provide comprehensive training to operators on safe press brake operation, including emergency protocols.
- Supervise new operators until they demonstrate proficiency in operating the press brake safely.
Initial Setup and Calibration of a Press Brake
Installation and Setup:
- Placement: Ensure the press brake is installed on a level and stable foundation to prevent vibrations that can affect precision.
- Power and Connections: Connect the press brake to power and ensure all electrical and hydraulic connections are secure and operational.
- Tooling Installation: Install the appropriate punch and die tooling based on the bending requirements of the job.
Safety Check:
- Verify that all safety guards and devices are properly installed and functional.
- Conduct a thorough inspection to ensure there are no loose parts or potential hazards.
Backgauge Setup:
- Adjust the backgauge to the correct position according to the dimensions specified in the bending program or manual setup.
- Ensure the backgauge fingers are aligned properly to accurately position the material for bending.
Die Alignment and Crowning:
- Align the die with the punch to ensure uniform bending across the length of the material.
- Check and adjust the crowning system if available to compensate for any deflection in the press brake bed, ensuring consistent bend angles.
Tooling Clearance and Safety Distance:
- Set the appropriate tooling clearance (gap between punch and die) based on the material thickness and type.
- Establish the safety distance to prevent collisions between the punch, die, and backgauge during operation.
Calibration and Testing:
- Perform calibration procedures according to the manufacturer's specifications or using calibration tools to verify the accuracy of bend angles and positions.
- Conduct test bends on scrap material to validate setup adjustments and ensure the press brake performs as expected.
Documentation and Training:
- Document the setup parameters and calibration results for future reference and quality control.
- Train operators on proper setup procedures, safety protocols, and troubleshooting techniques to maintain efficient and safe operation.
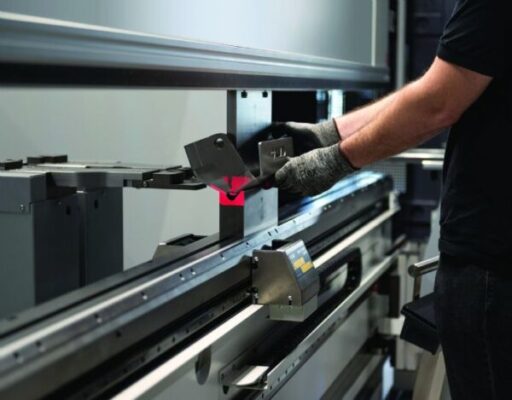
Troubleshooting and Problem-Solving for Press Brakes
Identify the Problem:
- Symptoms: Observe and document the specific issue such as inaccurate bends, strange noises, or hydraulic problems.
- Gather Information: Review machine settings, recent operations, and any error messages on the control panel.
Check Basic Settings and Conditions:
- Tooling: Verify the correct punch and die are installed and aligned properly.
- Material: Ensure the material thickness and type are suitable for the selected tooling and bending parameters.
- Backgauge: Confirm the backgauge settings and material positioning are accurate.
Inspect Mechanical Components:
- Hydraulic System: Check hydraulic fluid levels and inspect for leaks or pressure issues.
- Electrical System: Examine connections, fuses, and circuit breakers for any signs of damage or loose connections.
- Mechanical Parts: Inspect for worn-out components, loose bolts, or misalignment in the ram, bed, or frame.
Review Programming and Controls:
- CNC Controls: Verify program parameters, sequences, and tool offsets are correctly entered and active.
- Safety Features: Ensure all safety devices are functioning correctly and not triggering unintended stops or errors.
Perform Test Bends and Diagnostics:
- Trial Runs: Conduct test bends on scrap material to replicate the issue and identify potential causes.
- Diagnostic Tools: Utilize machine diagnostics or measurement tools to assess bend angles, force levels, and other critical parameters.
Consult Manuals and Resources:
- Manufacturer’s Manual: Refer to the press brake’s operation and troubleshooting manuals for guidance on specific issues and solutions.
- Technical Support: Contact manufacturer support or experienced technicians for assistance with complex or persistent problems.
Implement Solutions and Preventive Measures:
- Adjustments: Make necessary adjustments to tooling, settings, or mechanical components based on findings from troubleshooting.
- Maintenance: Schedule regular maintenance checks and preventive measures to prevent future issues and ensure optimal performance.
Document and Learn:
- Record Keeping: Document troubleshooting steps, solutions implemented, and outcomes for future reference.
- Training: Provide additional training to operators on troubleshooting techniques and preventive maintenance practices.
Maintenance and Long-Term Care
Regular Inspections:
- Daily Checks: Inspect the press brake for leaks, unusual noises, and visual signs of wear before starting operations.
- Weekly Inspections: Check hydraulic fluid levels, lubricate moving parts, and inspect electrical connections for tightness and wear.
Lubrication:
- Schedule: Follow manufacturer recommendations for lubricating mechanical components such as bearings, guides, and ball screws.
- Types of Lubricants: Use appropriate lubricants to prevent friction and wear, ensuring smooth operation and extending component life.
Cleaning:
- Debris Removal: Regularly clean the machine, removing metal chips, dust, and debris from the tooling area, backgauge, and surrounding surfaces.
- Hydraulic System: Keep hydraulic filters clean and replace them as per the maintenance schedule to maintain optimal fluid quality and system performance.
Alignment and Calibration:
- Die and Punch Alignment: Periodically check and adjust the alignment of dies and punches to ensure accurate bending results.
- Crowning Adjustment: If applicable, calibrate the crowning system to compensate for any bed deflection and ensure uniform bending across the length of the material.
Electrical and Control Systems:
- Inspection: Inspect electrical components, including switches, relays, and control panels, for signs of wear, corrosion, or damage.
- Software Updates: Keep CNC and control software up to date with the latest versions to access new features and ensure compatibility with programming tools.
Safety Checks:
- Guard Inspection: Regularly inspect safety guards and devices to ensure they are in place and functioning correctly to protect operators from hazards.
- Emergency Stop Testing: Test emergency stop buttons and safety circuits periodically to verify they immediately halt machine operations when activated.
Training and Documentation:
- Operator Training: Provide ongoing training to operators on proper machine operation, maintenance procedures, and safety protocols.
- Maintenance Records: Maintain detailed records of maintenance activities, including inspections, repairs, and parts replacements, to track machine history and identify recurring issues.
Professional Service and Support:
- Scheduled Maintenance: Schedule routine maintenance by qualified technicians to perform comprehensive checks, adjustments, and preventive measures.
- Emergency Repairs: Promptly address any malfunction or significant issue by contacting manufacturer support or certified service providers for expert assistance.
By implementing a proactive maintenance strategy and adhering to manufacturer guidelines, press brake operators can enhance equipment performance, minimize downtime, and ensure safe and efficient operation over the long term. Regular care and attention to detail contribute to maximizing the investment in press brake machinery and maintaining high-quality production standards.
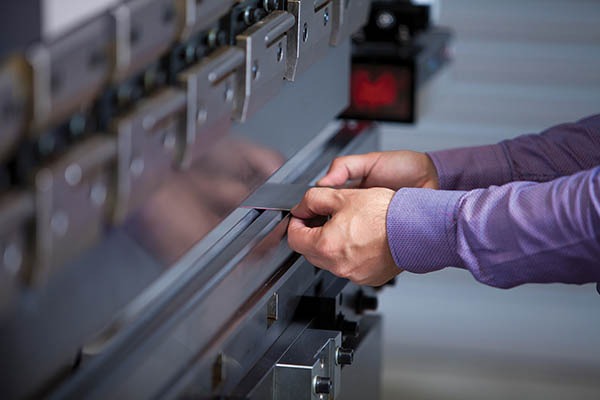
Top 10 Press Brake Operation Mistakes to Avoid
Avoiding common mistakes in press brake operation is crucial for maintaining efficiency, safety, and quality in metal bending processes. Here are the top 10 press brake operation mistakes to avoid:
Incorrect Tool Selection: Using improper punch and die sizes or types for the material thickness and bending requirements can lead to inaccurate bends and tool damage.
Poor Material Handling: Incorrect positioning or clamping of the material can cause misalignment during bending, resulting in flawed parts and increased scrap.
Neglecting Tool Maintenance: Failing to regularly inspect and maintain punch and die tooling can lead to premature wear, affecting bend quality and increasing production costs.
Incorrect Bending Sequence: Improper sequencing of bends, especially in complex parts, can result in collisions between the tooling and material, causing damage to both.
Ignoring Machine Setup Procedures: Skipping or improperly following setup procedures, including backgauge settings and tooling clearance adjustments, can lead to inconsistent bends and safety hazards.
Overloading the Press Brake: Exceeding the machine's tonnage capacity or attempting to bend materials beyond recommended thicknesses can damage the press brake components and compromise safety.
Not Using Safety Equipment: Failing to use safety guards, light curtains, or personal protective equipment (PPE) increases the risk of accidents, injuries, and machine damage.
Inadequate Programming Skills: Incorrectly programming the CNC controls or manual settings can result in incorrect bend angles, wasted material, and extended setup times.
Lack of Operator Training: Insufficient training in press brake operation techniques, including safety protocols and troubleshooting procedures, can lead to operational errors and reduced productivity.
Ignoring Machine Feedback and Alerts: Disregarding error messages, alarms, or unusual machine behavior without proper investigation can lead to serious mechanical issues and unplanned downtime.
By addressing these common mistakes through proper training, adherence to procedures, and regular maintenance, operators can enhance productivity, maintain equipment longevity, and ensure safe operation of press brakes in metal fabrication environments.
Step-by-Step Guide to Mastering Press Brake Operation
Understand Press Brake Basics:
- Learn the components of a press brake: frame, ram, bed, punch, die, backgauge, and control system.
- Familiarize yourself with different types of press brakes: hydraulic, mechanical, pneumatic, and CNC.
Safety First:
- Prioritize safety protocols and equipment, including guards, light curtains, and personal protective gear.
- Understand emergency stop procedures and machine-specific safety features.
Material Preparation:
- Select the appropriate material type and thickness for your project.
- Ensure materials are clean, flat, and properly positioned on the bed for accurate bending.
Tooling Selection and Installation:
- Choose the correct punch and die sizes and types based on material thickness and bending requirements.
- Install and align tooling properly to avoid defects and premature wear.
Machine Setup:
- Follow manufacturer guidelines for machine setup, including backgauge settings, tooling clearance, and crowning adjustment if applicable.
- Perform a trial run with scrap material to verify setup accuracy.
Programming and Control:
- Understand the programming interface: CNC controls for automated bending sequences or manual settings for simpler operations.
- Input bend angles, tool offsets, and other parameters accurately to achieve desired results.
Operational Techniques:
- Master bending techniques such as air bending, bottoming, and coining based on material properties and part requirements.
- Practice proper tool handling and machine operation to maintain consistent quality and productivity.
Quality Assurance:
- Use measurement tools like protractors and calipers to verify bend angles and dimensions.
- Implement quality checks throughout the bending process to detect and correct defects early.
Troubleshooting Skills:
- Develop the ability to identify and resolve common operational issues, such as tooling wear, material slippage, or programming errors.
- Utilize machine diagnostics and consult manuals or technical support for complex problems.
Continuous Learning and Improvement:
- Stay updated with advancements in press brake technology, techniques, and safety standards.
- Seek feedback from experienced operators, attend training sessions, and participate in professional development opportunities.
Summary of Mastering Press Brake Operation and KRRASS's Expertise
Mastering press brake operation is crucial for achieving precision, efficiency, and safety in metal fabrication. Understanding press brake components, safety protocols, material preparation, tooling selection, and machine setup ensures consistent quality and productivity. By honing operational techniques, programming skills, and troubleshooting abilities, operators optimize manufacturing capabilities.
Businesses seeking to enhance their press brake operations can leverage KRRASS's advanced solutions. Explore KRRASS's comprehensive range of press brakes, equipped with state-of-the-art technology and backed by robust support services. By choosing KRRASS, you can maximize equipment performance and achieve superior results in metalworking applications.