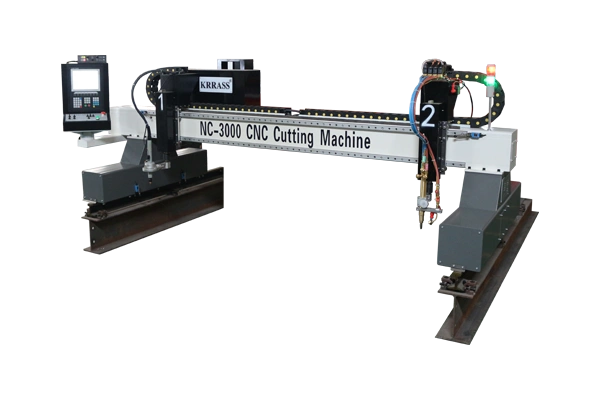
Oxy Plasma and Flame Carbon Steel Cutting Machine
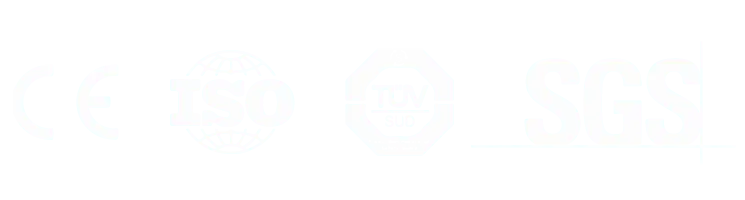
Oxy Plasma Carbon Steel Cutting Machine
We designed the plasma-oxygen carbon steel cutting machine using modern construction and mechanics solutions. They ensured the best efficiency and an attractive, innovative look. Modified bridge construction makes it more rigid and resistant to high temperatures. It is essential, especially during even 300 mm thick materials cutting. The unique combination of safety systems used in plasma-oxygen carbon steel cutting machines ensures the highest comfort and the best level of safety for machine operators and the people around them.
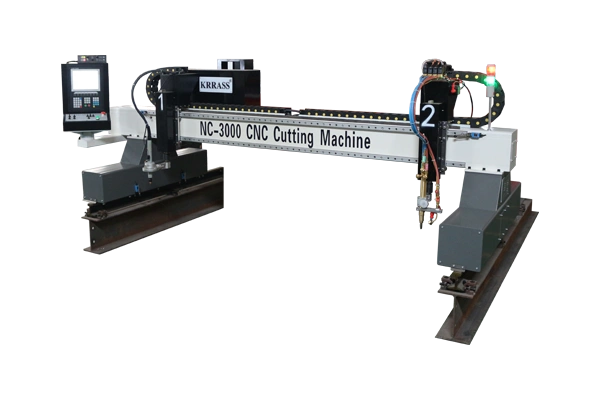
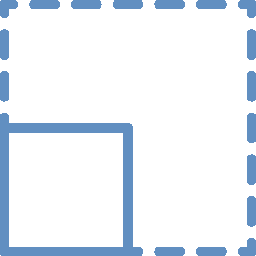
Top performances allow to accurately and cost-efficiently cut pieces in high volumes.
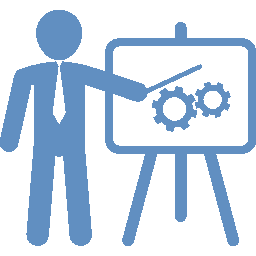
The cutting table is also structurally independent from the machine, which is ideal for loading heavy plates since accidental shocks will not affect the performance.

A unique safety system, with an assigned perimeter and an emergency stop, stops the machine instantly in the event of a collision to protect the safety of your operators.
Standard Equipment
- Hypertherm Power Source
- Automatic Torch Height Control (Sensor THC)
- CAD/CAM Software
- Hypertherm Auto Gas control unit
- Bridge driven with Servo Motors on both sides X Axis
- Precise helical rack, pinion and linear dual guiding
- CNC controled outputs/inputs for vacum table & filtering unit
- Positioning accuracy +- 0,1 mm
- Positioning speed 40 m/min
- Torch collision sensor
- Independent bridge and cutting table design
Optional Features
- Hypertherm Edge Connect /TC CNC Unit
- Other Hypertherm power source options
- Auto Gas Console options
- Lantek CAD/CAM software, automatic nesting
- Hypertherm Pronest CAD/CAM software
- Filter Unit
- Consumables starter kit
- 5-Axis cutting head
- Double bridge
- Pipe cutting
- Oxy cutting head • Tanaka Oxy Torch • Messer Oxy Torch
- Multi Plasma heads
- True Hole
Technicial Specifications Of Carbon Steel Cutting Machine
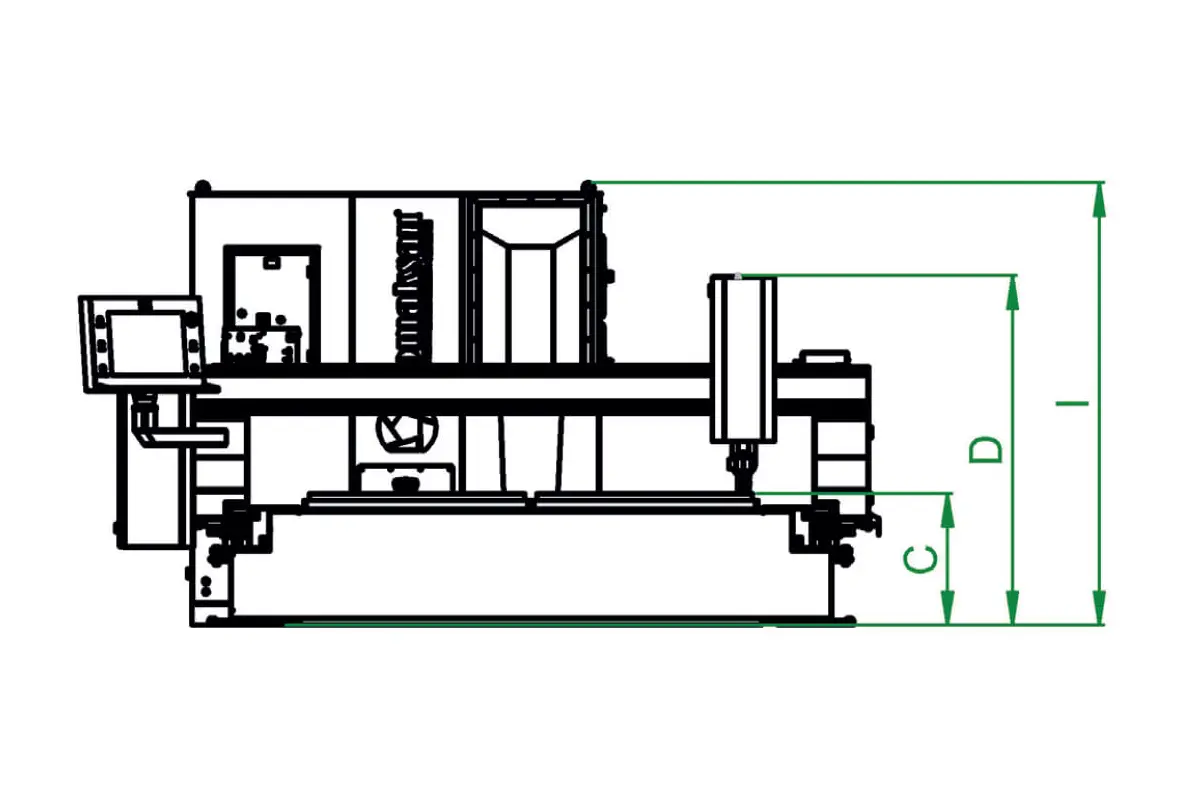
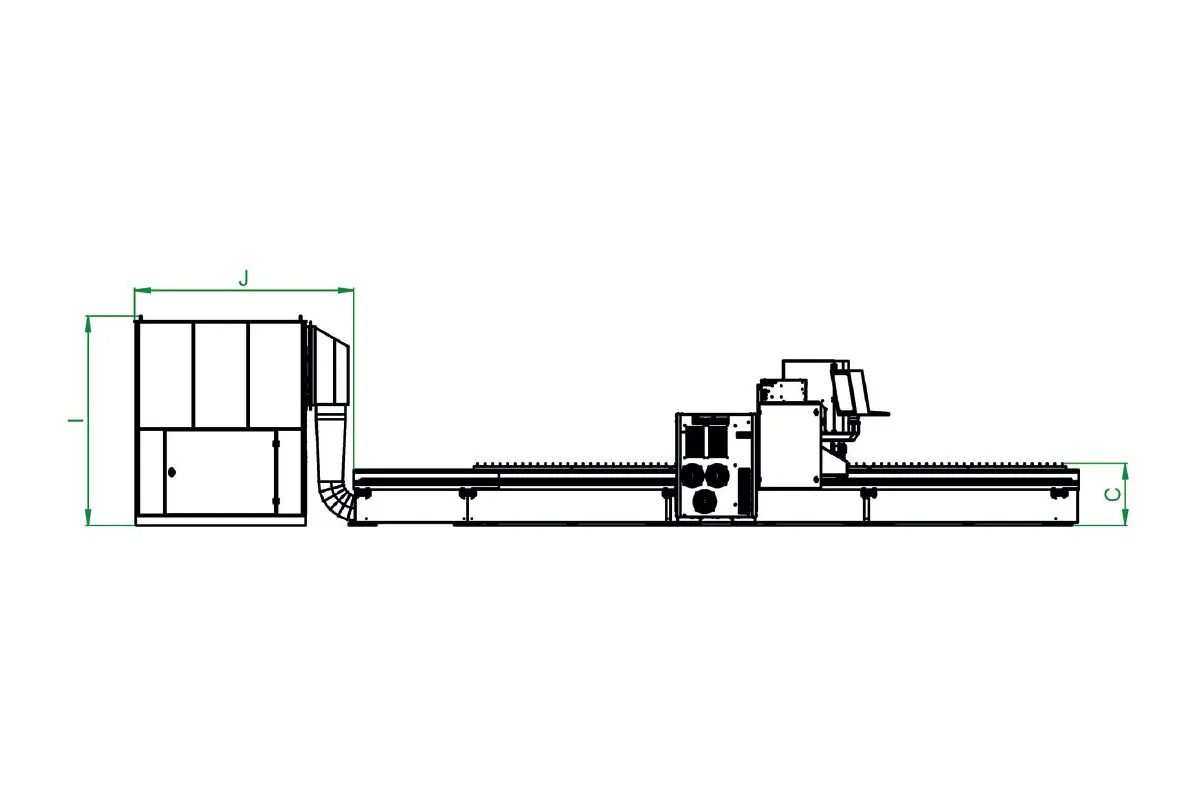
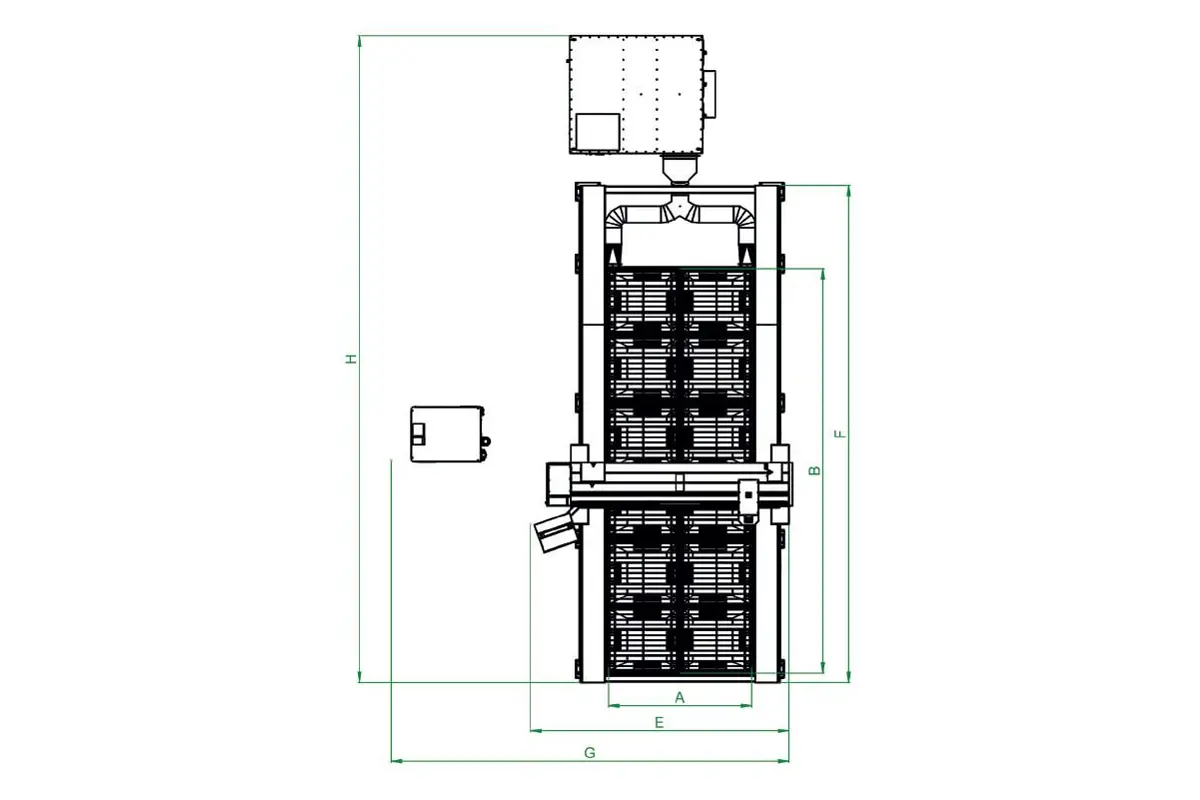
Technical Parameters Of Carbon Steel Cutting Machine
P-Series Plasma Cutting | Cutting Width | Cutting Length | Table Height | Height | Width | Length | Width (Including Power Unit) | Length (Including Filter) | Filter Height | Filter Length | |
A | B | C | D | E | F | G | H | I | J | ||
mm | mm | mm | mm | mm | mm | mm | mm | mm | mm | ||
A1500 | 3000 | 1500 | 3100 | 650 | 2000 | 2320 | 4500 | 5500 | 6500 | 2200 | 2000 |
4000 | 1500 | 4100 | 650 | 2000 | 2320 | 5500 | 6000 | 7500 | 2200 | 2000 | |
6000 | 1500 | 6100 | 650 | 2000 | 2320 | 7500 | 6000 | 10000 | 2200 | 2500 | |
A2000 | 6000 | 2000 | 6100 | 650 | 2000 | 2820 | 7500 | 6500 | 10000 | 2200 | 2500 |
Introduction to Configuration
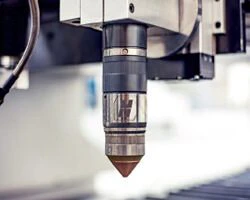
HYPERTHERM CUTTING HEAD
High productivity, low operating cost, high cutting speed, long life and exceptional cutting quality. Offers wide range cutting from very thin sheet thickness to very thick sheet thickness.
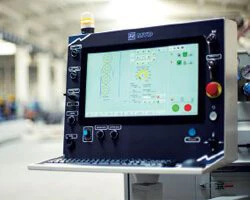
CNC CONTROL UNIT ESA / HYPERTHERM
Thanks to its easy operation, plasma processes can be efficiently and easily managed.
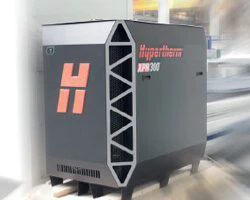
HYPERTHERM POWER SOURCE
Efficiency, fast cutting, fast processing cycle provides high reliability with easy replacement of consumables. Advantages: Superior cutting quality, minimum operating cost and maximum productivity.
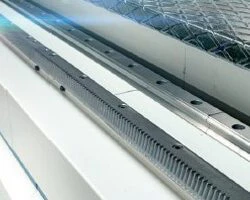
RACK PINION AND LINEAR GUIDING
High precision cutting achieved with dual guiding system Rack Pinion and Linear Guides for this carbon steel cutting machine.
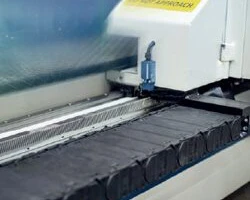
CABLE TRAY CARRIERS
Cable channels in accordance with CE standards, silent operation, durability, With its anti-friction and non-breaking properties usage life is much longer.
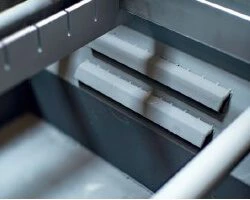
PARTIAL PNEUMATIC SUCTION SYSTEM
With the PLC software, pneumaticly controlled hatches which are only at the cutting area are opened. With this way more powerful suction with less energy consumption can be achieved.
EDGE® Connect, Hypertherm’s newest Computer Numeric Control (CNC) plat- form, delivers unmatched reliability, powerful embedded capabilities, and a high level of customizability. Based on our proprietary, industry-leading Pho- enix® CNC platform, the system offers new, advanced software features – inc- luding ProNest® CNC automatic nesting delivering SureCutTM technology – along with enhanced hardware. For easy set up, changes, and upgrades, EDGE Connect CNCs can be configu- red in the field with software specific to the plasma cutting machine application. The easy-to-use system combines advanced cutting performance with an intuitive graphical interface, and supports plasma, oxyfuel, and waterjet applications.
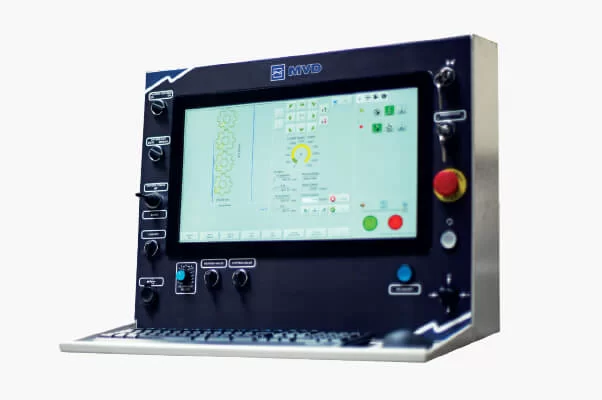
- With Patented CutPro® Wizard, even new operators can be cutting production parts in less than five minutes
- On-screen Software Operator’s Console (Soft OpCon) allows easy setup and operation of cutting station and manual motion
- Integrated communications with plasma and torch height control systems deliver automated and expert control using installed factory or custom cut charts
- Custom cut charts can be created and controlled in the part program or made available to the CutPro Wizard
- EDGE Connect runs on the Windows® 10 Enterprise operating system
CAD / CAM Softwares for Carbon Steel Cutting Machine
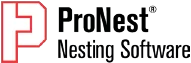
ProNest® LT (formerly known as TurboNest®) is a powerful CAD/CAM part nesting software designed for light industrial, mechanized cutting in production environments. It provides a single software solution for all your conventional carbon steel cutting machines and oxyfuel cutting machines.
- Part design and development
- Integrated 2D CAD program to create and edit CAD files
- Variable Shape Parts library to develop common parts from templates
- CAD/CAM import and conversion
- Import CAD files (industry-standard file formats)
- Import PDF
- Raster to vector converts static images to CAD
- Automatic CAD file correction and error notification
- Automatic spline/ellipse smoothing and reduction
- Separate multiple parts from a single CAD file
- Automatic mapping of CAD layers to processes (cut, mark, etc.)
- Fast, easy job setup
- SureCut™ technology and built-in process enterprise
- Interactive manual nesting
- Detailed reporting
- Simplified costing
- Choice of output
- Post-processor with NC output
- DXF output
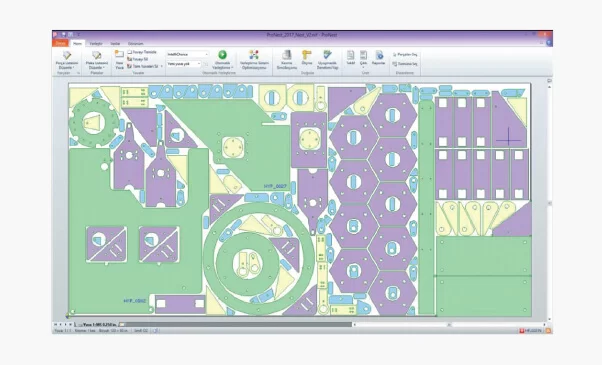

- Offers perfect nesting efficiency for automatic or manual part nesting
- Copy, move, reverse, turn alignment manual, semi-automatic, functions geometrical working
- Advanced nesting algorithm optimizes the use of a material, minimizing scrap.
- Can work with standard sheets stocked in the warehouse and/or with scraps obtained from previous processes.
- Automatic cutting path determination
- Time/Cost analyses
- Simulation before actual cutting
- Smart Part importer / Exporter from CAD system, DXF, DWG, IGES, Step etc file formats
- Part Drawing module, call parts, automatic or manual nesting, machining, CNC codes generates, Sheet metal stock searching etc
- Various input/output methods, film burning, specialized piercing, fast laser, micro-joints, head direction management, edge binding
- Complicated functions and program
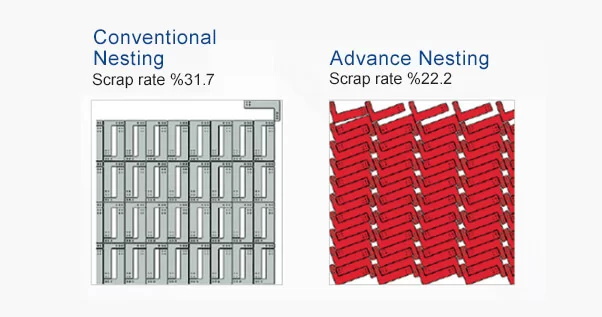
Head Options of Carbon Steel Cutting Machine
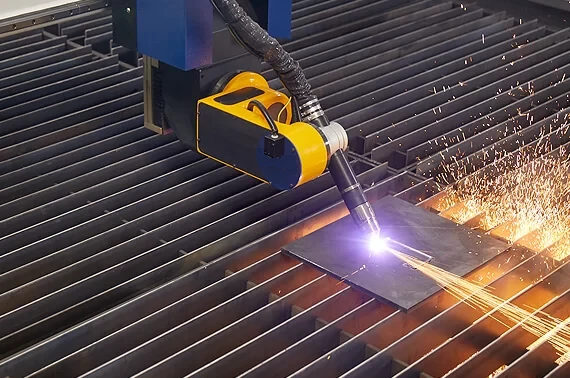
Beveling Head (5-Axis)
KRRASS 5-Axis beveling head is designed for 3D and angle cutting. Up to 45° all the angles are calculated automaticly and created so the operator can input the desired angles as needed. Also the straight vertical cuts can be done, reduced maintenance due to height detection sensor.
- Offers bolt hole quality
- Automatic angle adjustment
- Time saving – short setting time
- Excellent cutting and contouring
- Low production costs
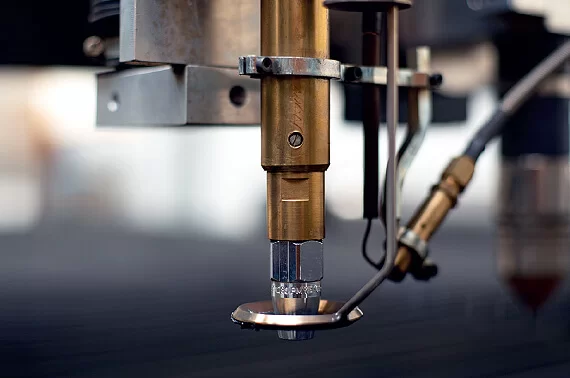
Oxy Cutting
KRRASS CNC Controlled carbon steel cutting machines also provide oxygen cutting capability. With our oxygen head equipped machines up to 200 mm cut can be done and this limit can be increased with special design options.
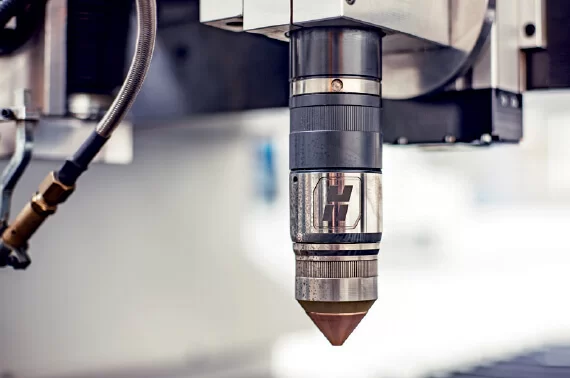
Plasma Cutting
The carbon steel cutting machine uses Hypertherm’s patented technologies for quality, more power, more precision and more consistent cutting.
- Decreases cost per cut
- Power Pierce: Repels molten metal during piercing allowing strong production piercing
- Long Life: Gas intake and flow rate is adjusted under contol.
- High Definition: Aligns and focuses the arc, superior quality and consistent cutting
- High Definition: Delivers increased arc density and cut speeds while maintaining arc stability and smoother cut edges.
- Increases number of cuts per hour
Dust Collector Filter System
During carbon steel cutting machine cutting operations filter is needed for extraction of smoke, dust and emissions. Creates a more better working environment for everybody, specially for plasma operators. Shipped in one piece by means of its specially defined dimensions, this way all accessories and pre-set and ready to startup. Particles carried by the dirty air entering through the side walls of filter cabin are held by means of a crashing plate. In this section, speed of the air is decreased and desired filtering rates are obtained. In addition, sparks that may touch the filter and big and corrosive particles are directed to the collecting bucket underneath the bunker. Thus, life of the filters is increased. Other dusts and smokes that constitute the polluted air are held by BIA-approved filter materials tested according to DIN EN 60335-2-69 appendix AAand selected according to the application. Dusts held are automatically cleaned thanks to jet pulse cleaning system. Cleaned air is absorbed from the cabin by means of a fan and released to the environment desired.
- Compact easy shipping
- Easy maintenance, fast cartridge change
- Quite <70 db (A)
Reviewed by 9 users
Портальный станок для газовой резки с ЧПУ NC-3000 очень хорош. Резка очень хорошо
ماكينة قطع بالبلازما بنظام التحكم الرقمي CNC ذات جودة
ممتازة TNC-1325 وخدمة العملاء من الدرجة الأولى.
The plasma cutter is a reliable and versatile machine that will exceed my expectations
The excellent customer service experience has added immense value to this purchase of this plasma cutter machine and the technical support team has been accommodating whenever I had questions or needed assistance with operating the plasma cutter.
Oxy Plasma Carbon Steel Cutting Machine
After a long time check and thinking ,finally , i booked one Oxy Plasma Steel Cutting Machine from KRRASS .
With the help from them on line by WA , I managed to install this machine . And works really in good condition .
As the old saying goes you get what you pay for , i am very happy about this machine .