For industrial manufacturing processes like sheet metal fabrication, machinists have a variety of cutting equipment to choose from. In addition to standard CNC machines equipped with sharp metal cutting tools, other options include laser cutters, water jet cutters, and plasma cutters. Each of these industrial tools has its unique advantages and is suitable for specific applications. While all are commonly used in sheet metal fabrication, the methods of laser, water jet, and plasma cutting are best suited for different situations based on material type, sheet thickness, and the required tolerance or edge quality. This article will provide a clear comparison of plasma cutting vs laser cutting vs waterjet, exploring the fundamentals of each technique, their pros and cons, and the ideal applications for each method.

What is Laser Cutting?
Laser cutting is a machining process that employs a high-power laser to cut through materials by vaporization. Depending on the material and application, the laser can be a CO2, fiber, or diode laser, with fiber lasers often used for sheet metal cutting.
In laser cutting machines, some systems move the material (workpiece) while keeping the optics stationary, others maintain a fixed workpiece and move the optics, and some utilize hybrid systems. Compared to plasma cutters, laser cutting machines are typically more expensive.
Advantages of Laser Cutting
- Fast Cutting Speeds: Particularly effective for thin workpieces like sheet metal.
- High Precision: Offers a high level of accuracy and precision.
- Versatile: Compatible with a wide range of materials.
- Minimal Kerf Widths: Achieves kerf widths as small as 0.4 mm, providing excellent detail.
- Superior Surface Quality: Produces clean, smooth edges.
- Cost-Effective Operation: Lower operational costs compared to similar processes.
Limitations of Laser Cutting
- Reflective Metals: Not ideal for shiny metals as the laser beam can be reflected.
- Reduced Speed for Thick Materials: Cutting speeds decrease significantly with thicker workpieces.
- Complex Setup: Can be complicated to set up the optics properly.
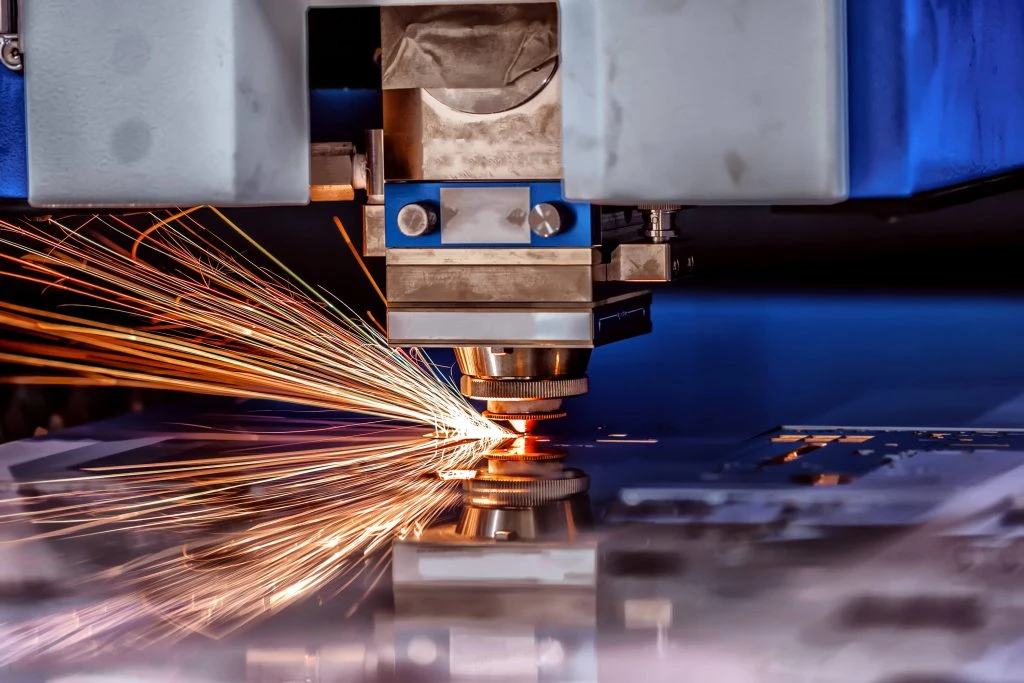
What is waterjet cutting?
Water jet cutting (waterjet cutting) is a machining technique that uses a CNC water jet cutter to cut through various materials. This machine uses a high-pressure pump to force out a high-pressure jet of water — typically in the range of 30,000–90,000 psi — that can cut through the material.
For hard materials like sheet metal, the water is mixed with an abrasive substance such as garnet or aluminum oxide, increasing its cutting power.
Because water jet cutters generate minimal heat — in fact, the water also acts as a coolant — they are ideal for metals with a low melting point that might otherwise deform when cut with a metal cutting tool or laser.
Advantages of water jet cutting
- Does not create a heat-affected zone, reducing warping and allowing for features like sharp corners and internal radii
- Compatible with range of materials
- Can produce intricate and complex cuts
- Very high level of accuracy and precision
- Higher cutting edge quality than comparable processes
- Low kerf widths around 0.6 mm
Limitations of water jet cutting
- Slower than comparable processes
- Higher operational cost than comparable processes
- Noisy process (not relevant to customer)
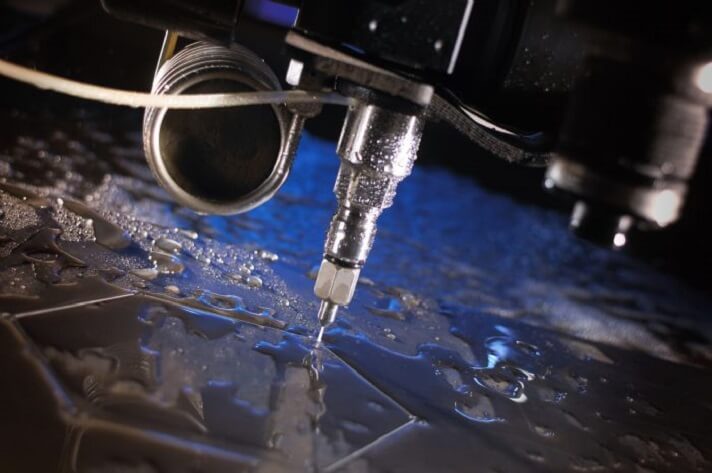
What is Plasma Cutting?
Plasma cutting is a machining process used to cut materials like sheet metal using an accelerated jet of hot plasma. Unlike methods that employ sharp tools, lasers, or water jets, plasma cutting is specifically designed for cutting electrically conductive materials such as steel, stainless steel, aluminum, brass, and copper.
During the plasma cutting process, the cutter completes an electric circuit by generating a channel of electrically ionized gas (plasma) through the workpiece. The cutter’s power is not limited by the thickness of the material being cut.
CNC-controlled plasma cutters are generally more affordable than laser or water jet machines, and they also have relatively low operating costs.
Advantages of Plasma Cutting
- Versatile Thickness Cutting: Capable of cutting through very thick workpieces without sacrificing cut quality.
- Fast Cutting Speeds: Efficient for both thick and thin metals.
- Cost-Effective: Low machine and operating costs make it an economical choice.
Limitations of Plasma Cutting
- Material Limitation: Only suitable for electrically conductive materials.
- Precision: Less accurate and precise than other comparable processes.
- Edge Quality: Produces poorer edge quality with kerf widths around 3.8 mm.
- Fume Emission: Generates fumes during the cutting process.
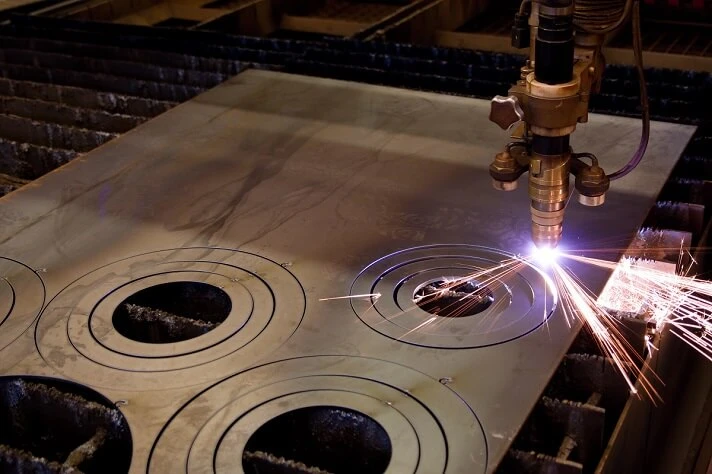
Quick Comparison: Plasma Cutting vs Laser Cutting vs Waterjet
Laser cutting | Water jet cutting | Plasma cutting | |
Cutting precision | High | Very high | Moderate |
Kerf width | 0.4 mm | 0.6 mm | 3.8 mm |
Material range | Wide | Wide | Narrow |
Cutting speed (thin) | Very fast | Moderate | Fast |
Cutting speed (thick) | Moderate | Slow | Fast |
Operating cost | Low | High | Low |
Machine cost | High | High | Low |
The table above shows the respective strengths and weaknesses of laser cutting, water jet cutting, and plasma cutting.
In summary, laser cutting is the best process available for the fast and precise cutting of thin-gauge sheet metal, water jet cutting is best for for ultra high-precision cutting when speed is not a priority, and plasma cutting is best for cutting thick workpieces made from conductive metals and alloys.
Ideal Applications
Laser Cutting
Laser cutting is most beneficial in scenarios that require high precision and intricate details, such as in the electronics and aerospace industries. It is particularly suited for processing thin materials like metal sheets and plastics where speed and precision are essential. This method is also ideal for rapid prototyping due to its fast setup and cutting speeds, making it a popular choice for short production runs.
In the electronics industry, laser cutting is used for creating small components for devices and circuit boards. The aerospace industry benefits from laser cutting by fabricating lightweight parts with complex geometries. In the automotive sector, laser cutting is employed for producing intricate patterns and designs in both interior and exterior components.
Plasma Cutting
Plasma cutting is most beneficial for cutting thick plates of electrically conductive metals like steel and aluminum. It offers a cost-effective solution for applications that do not require the highest precision, making it ideal for heavy industries. Its portability and ability to handle various environmental conditions make it suitable for outdoor and on-site fabrication tasks.
In the construction industry, plasma cutting is used for cutting large steel beams and plates for building structures. The shipbuilding industry utilizes plasma cutting to fabricate parts for ships and marine vessels. Metal fabrication shops rely on plasma cutting for general-purpose cutting of various metal shapes and sizes.
Waterjet Cutting
Waterjet cutting is most beneficial for materials sensitive to heat, such as composites, plastics, and certain metals. It is capable of cutting very thick materials with precision, making it suitable for complex shapes. Industries that prioritize minimal environmental impact find waterjet cutting advantageous, as it produces no hazardous fumes and requires no secondary finishing.
In the architecture and art sectors, waterjet cutting is used for creating detailed architectural elements and artistic pieces from stone, glass, and metal. The aerospace industry benefits from waterjet cutting for processing composite materials and metals for structural components. In the mining and quarrying industries, waterjet cutting is employed for cutting and shaping stone and ceramics for various industrial applications.
Environmental and Safety Considerations
Laser Cutting
Laser cutting is generally environmentally friendly, as it produces minimal waste and requires no consumables like abrasives or gases that could lead to pollution. However, laser cutting can generate fumes and gases, especially when cutting materials like plastics and certain metals, which may require proper ventilation and filtration systems to ensure a safe working environment.
From a safety perspective, laser cutting requires protective measures to shield operators from the intense light and potential reflections. Operators must wear safety glasses, and machines should be enclosed or fitted with protective screens to prevent accidental exposure to the laser beam.
Plasma Cutting
Plasma cutting can produce significant amounts of fumes and gases, especially when cutting thicker metals, which can have environmental and health impacts. Proper ventilation and filtration systems are necessary to manage these emissions and ensure a safe working environment.
Safety considerations for plasma cutting include protecting operators from the intense light and heat generated during the process. Operators should wear appropriate protective gear, including face shields, gloves, and aprons, to prevent burns and exposure to UV radiation. Additionally, the high noise levels generated by plasma cutting may require hearing protection.
Waterjet Cutting
Waterjet cutting is one of the most environmentally friendly cutting methods, as it produces no hazardous fumes or gases and generates minimal waste. The water and abrasive materials used in the process can often be recycled, further reducing environmental impact. However, proper disposal of used abrasive materials is necessary to prevent environmental contamination.
From a safety standpoint, waterjet cutting poses minimal risk as there is no heat involved, reducing the chance of burns or thermal damage. Operators should still wear protective gear to guard against high-pressure water and abrasive spray. Ensuring that the equipment is well-maintained and operated within safety guidelines is essential to prevent accidents.
Plasma Cutting vs Laser Cutting vs Waterjet: Comparison Guide
Having looked at the definitions, advantages, and disadvantages of each cutting method, it is now time to examine how they compare against each other.
Cost
Regarding purchasing cost, a plasma cutting is the most cost effective while the laserjet is the most expensive. For operating cost, when you take into consideration the materials used for each machine, plasma will again score the lowest price with waterjet being the most expensive.
Process | Initial Cost | Operating Cost | Maintenance cost |
---|---|---|---|
Laser Cutting | High | High | Low |
Plasma Cutting | Low | Low | Low |
Waterjet Cutting | High | Very high | High |
Initial cost
For a machine with similar capabilities, laser cutters are the most expensive, followed by waterjet cutters and plasma cutters.
However, keep in mind that the initial price of the machine may vary depending on the manufacturer and the services (extended warranty) you are bundling with your machines.
A high-end industrial CNC plasma cutter can cost around $50,000 – $100,000.
Followed by Industrial level CNC water jet cutters with a price range of around $100,000 – $300,000.
The industrial CNC laser cutters are the most costly among the three, with a price range of above $350,000. But there are hobby lasers that cost less than $500 that can cut thin nonmetallic materials.
Operating cost
Plasma cutters offer the most economical operation with an average operational cost of around $15 per hour.
With an operating cost of about $20 per hour, laser cutters are slightly more expensive to run compared to plasma cutters.
Cost of waterjet cutting, when compared to laser cutting and plasma cutting, is the highest among the three at around $30 per hour, which can further increase, depending upon the type of abrasive used.
Although plasma cutters might seem like the clear winners, the average operational cost for a particular job is directly affected by the cycle time.
When cutting thin materials, laser cutters provide an exceptionally quick cycle time, reducing their overall operational cost, making them ideal for thin workpieces.
However, the exact operational cost varies from one machine to another and depends on various factors such as power, cutting speed, cycle time, etc.
Maintenance cost
Waterjet cutters have the highest maintenance cost due to the wear and tear caused by vibrations and the finite life of some parts like nozzles.
Plasma and laser cutters require comparatively less maintenance with occasional greasing of the moving parts (like axes) depending on the usage of the machine.
However, CO2 laser cutters require weekly cleaning of the mirrors and occasionally changing some parts in about 2000 to 3000 hours of usage (about 4 years).
Speed of Operation
The production rate of these metal cutting machines is determined by their cutting speeds. Waterjet is the slowest (especially on thick materials) followed by laserjet. Plasma jet is the fastest.
Cutting edge quality
The precision of a cutting machine is normally determined by comparing the actual measurements of the resulting part compared to the programmed part size. Due to less heat distortion, waterjet cutting is the most accurate, followed by laser and finally plasma. However, it is worth noting that on thick materials laserjet can cause distortion.
Precision plasma, laser and water cutting is the key to accurate and high-quality manufacturing. Swanton Welding offers reliable metal cutting services that will help you meet all your deadlines and budgetary goals whilst upholding production quality standards. No matter which type of metal cutting is right for your project Swanton Welding can carry it out for you today.
Precision Comparison
Plasma cutters are the least precise, with a typical part size tolerance of about +/-0.005 inches (1.3 mm), followed by laser cutter with part size tolerance of about +/-0.004 inches (1 mm).
The precision of plasma cutting can be improved by performing it under water which reduces warping of the metal.
It also reduces the heat-affected zone (HAZ) and improves the surface finish of the cut.
On the other hand, waterjet cutters offer the highest precision, with a typical part size tolerance of about 0.020 inches (0.5 mm).
Learning Curve for Operation
Operating any of these machines requires good knowledge of CNC softwares and machining parameters.
There are comparatively fewer variables in plasma cutting and waterjet cutting, making them easy to learn.
Whereas laser cutting consists of various variables such as type of laser, focal point, laser power, cutting speed, frequency, raster and vector designs, etc.
All these variables increase the complexity of the process, and therefore the learning curve for laser cutting is comparatively steep.
Noise Levels Comparison
Waterjet cutters are the loudest among them all due to the use of powerful pumps and the constant interaction of workpiece and pressurized water jet.
Plasma and laser cutters are comparatively silent, but they require a ventilation system that generates considerable noise.
However, laser cutters generally operate in an enclosure, which allows them to use a low-powered ventilation system, thereby generating the least noise.
Frequently Asked Questions (FAQ)
Is waterjet cutting cheaper than laser cutting?
No, waterjet cutting is generally more expensive than laser cutting. While the initial cost of a waterjet cutter can sometimes be lower than that of a laser cutter, the ongoing costs are higher due to the use of costly abrasive materials, slower cutting speeds, and frequent maintenance requirements. In contrast, laser cutting is faster and does not require expensive cutting materials, making it a more cost-effective option overall.
Can we use a waterjet cutter for engraving?
Yes, a waterjet cutter can be used for engraving by controlling the water jet's pressure to engrave the material. However, laser cutters are typically recommended for engraving because they offer faster speeds and higher-quality outputs across a variety of materials.
What materials should not be cut using a laser cutter?
Laser cutting is not suitable for certain plastics, such as HDPE, polycarbonate, ABS, and plastics containing PVC. When these materials are exposed to laser processing, they can release toxic gases harmful to humans and damaging to the laser cutter.
Conclusion
Laser cutters are recommended for their versatility, as they can be used for cutting, engraving, and marking a wide range of materials. Plasma cutters are optimal for making smooth cuts in medium to thick metal workpieces at comparatively faster cutting speeds. Waterjet cutters are primarily used in situations where high cut quality is prioritized over cycle time. If you need further guidance on choosing the right cutting equipment for your needs, consider consulting with experts at Krrass, who can provide tailored advice and support.
Reviewed by 1 user
Recently, we have been considering the purchase of a plasma or laser machine. Through this article, we have better understood our current needs, and we look forward to receiving the laser machine