Laser Cutting Machine Wood is a highly efficient wood processing equipment for precise cutting and engraving, which is widely used in furniture, building decoration, handicrafts and other industries. Choosing an ideal wood laser cutting machine can improve productivity, reduce production costs and realize precision processing. However, there are many types of wood laser cutting machines on the market, how to choose the right equipment for their needs has become a key issue. This article will introduce how to choose the ideal wood laser cutting machine to help you find the most suitable equipment for you.
What Is Laser Cutting Machine Wood?
Laser cutting machine is a device that utilizes a focused beam of light to cut or engrave materials. A laser cutter consists of a focused beam of light from an optical laser. When it comes into contact with materials and workpieces, the high power laser light emitted by the laser engraver causes the substance to rapidly heat up and melt.
When purchasing a wood laser cutter, evaluating the following factors ensures you select a machine tailored to your specific woodworking needs:
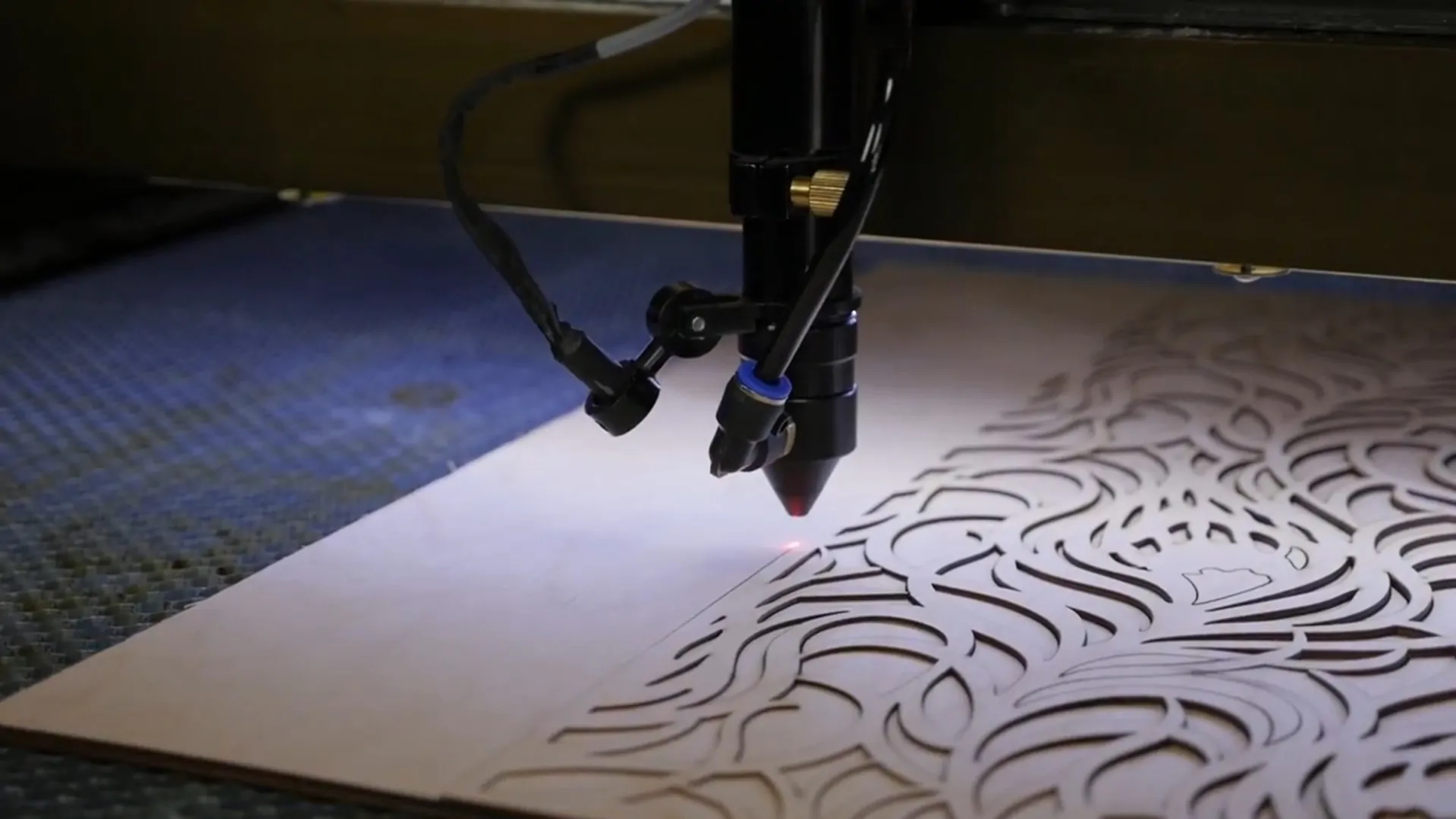
Advantages of Cutting Wood with a Laser Cutting Machine
Cleanness and low noise level. Due to the non-contact processing, there are no chips and dust. Laser production is quite clean, and for proper operation, it is enough to use an air exhausted system that comes with any Wattsan laser machine;
High precision and cutting fine contours and detailed items. First, it saves material to some extent. The exposure area of the laser beam is 0.3-0.5 mm therefore the beam does not “eat up” extra material as, for example, a milling machine does (you can read about it in the article about CNC routers). Secondly, you can obtain the result that is unattainable or difficult to achieve with other types of machining;
Speed of operation. The Wattsan wood laser cutting machines achieves operating speeds of up to 500 mm/s and idle or engraving speeds of up to 700 mm/s;
No time wasted on attaching the workpiece because the cutting is non-contact;
For the same reason, there is no chipping or notches at the edges of the product which can occur with traditional wood-cutting methods;
In addition to laser cutting, you can also perform engraving and ablation of wood on a wood laser machine. This significantly expands the possibilities for your production and allows you to get creative with the process;
The CNC brings down to a minimum the possibility of errors during operation because all manipulations are performed by the programmed controller;
For the same reason, the laser ensures high quality, precision, and repeatability of products;
Processing of a number of other materials: different types of plastics, rubber, ceramic, fabric, fur, and leather, foam, cardboard and paper, stone, composites. When combining materials and methods of processing, your possibilities are only limited by your imagination.
What Are the Factors to Consider When Buying a Laser Cutting Machine Wood?
Laser Power
The machine’s power rating influences its ability to cut various thicknesses of wood. A higher wattage allows for faster cutting and the ability to handle denser or thicker wood materials.
Cutting Area Size
Choose a laser cutter with a bed size that fits the dimensions of the wood pieces or sheets you typically work with. A larger cutting area provides flexibility for bigger projects, while a smaller bed may suit compact, detailed work.
Laser Tube Type
CO2 laser tubes are ideal for cutting wood due to their versatility and cost-effectiveness, while fiber lasers are primarily for metals. Opt for a CO2 laser cutter for woodworking applications.
Cutting Speed and Accuracy
Speed and precision are essential for achieving clean, detailed cuts. Look for a machine that balances high cutting speed with the accuracy needed for fine woodworking projects.
Software Compatibility
Ensure the machine is compatible with the design software you prefer (e.g., AutoCAD, Adobe Illustrator). Smooth integration ensures your designs are executed with precision.
Cooling System
A robust cooling system prevents the laser tube from overheating, prolonging the life of the machine and maintaining cutting quality. Look for models with built-in water or air cooling systems.
Price and Budget
Laser cutters come in a range of prices. Focus on machines that offer the right combination of features within your budget. Avoid overspending on features you may not use often.
Manufacturer Reputation and Support
Choose a machine from a reputable brand known for quality and reliability. Consider customer support availability, warranty options, and access to replacement parts.
By assessing these factors, you can choose a wood laser cutter that matches your production needs, ensuring optimal performance for your woodworking projects.
CO2 Laser Cutting Machine Wood
CO2 laser cutting is an advanced wood processing technology that precisely cuts wood with a high-energy laser beam. In the wood processing industry, CO2 laser cutting technology has unique advantages.
High Precision
CO2 laser cutting technology is renowned for its exceptional precision, capable of achieving cuts at the millimeter level or even finer. This allows for intricate detailing and precise execution in wood processing projects. The ability to cut with such high accuracy ensures that each piece maintains the desired design without the need for additional refinement, making CO2 laser cutting ideal for both decorative work and complex industrial applications.
High Efficiency
One of the standout advantages of CO2 laser cutting for wood is its speed and efficiency. The laser operates at high speeds, enabling faster cutting times compared to traditional mechanical methods. This increase in efficiency not only reduces production time but also lowers costs, making it a highly effective solution for businesses aiming to boost productivity. Whether for large-scale manufacturing or smaller projects, the high-speed capabilities of CO2 laser cutting can significantly improve overall output.
Non-Contact Processing
CO2 laser cutting is a non-contact technology, meaning the laser beam never physically touches the wood surface. This eliminates the risk of damaging the wood’s texture, leaving the original grain and appearance intact. The absence of physical contact also minimizes wear and tear on the equipment, extending its lifespan and reducing the need for maintenance. This makes laser cutting ideal for projects where maintaining the integrity of the wood surface is a priority.
Enhanced Flexibility
Flexibility is another key advantage of CO2 laser cutting. With the help of advanced automation and design software, it is possible to cut a wide range of complex shapes with precision and ease. This makes it highly versatile, allowing manufacturers to create custom designs, intricate patterns, and detailed engravings. As a result, CO2 laser cutting has found a strong foothold in the custom wood processing industry, where unique and intricate designs are in high demand.
Environmentally Friendly and Energy Efficient
CO2 laser cutting is not only efficient but also environmentally conscious. Unlike traditional cutting methods that may produce waste materials, harmful gases, or water pollution, laser cutting produces minimal waste and requires no additional treatments. Moreover, laser cutting machines are generally energy-efficient, consuming less power compared to older mechanical processing technologies. This makes it an eco-friendly and sustainable choice for manufacturers looking to reduce their environmental impact.
Consistently High Quality
The precision of CO2 laser cutting leads to a consistently high level of quality in the finished products. Each cut is executed with uniform accuracy, ensuring that every piece meets the same high standards. This level of consistency is essential for maintaining product quality across multiple production runs. The reliability and repeatability of CO2 laser cutting not only improve the competitiveness of the products but also increase market recognition for their superior craftsmanship.
CO2 Laser Cutting Thickness (only for reference)
Materials type | 40W | 60W | 80W | 100W | 120W | 150W | 200W |
Wood | 3mm | 7mm | 10mm | 12mm | 13mm | 15mm | 18mm |
Plywood | 2mm | 6mm | 10mm | 12mm | 13mm | 15mm | 18mm |
Leather | 1mm | 3mm | 4mm | 5mm | 6mm | 7mm | 10mm |
Acrylic | 2mm | 10mm | 13mm | 15mm | 17mm | 16mm | 20mm |
PVC | 1mm | 3mm | 4mm | 5mm | 6mm | 7mm | 8mm |
Plastic (easy to melt) | 1mm | 2mm | 3mm | 4mm | 5mm | 6mm | 8mm |
Rubber | 2mm | 3mm | 4mm | 5mm | 6mm | 7mm | 10mm |
Crystal/Jade/Stone/Marble/Medal | Only for engraving | ||||||
Clothing(fabric,wool) | 2mm | 3mm | 4mm | 5mm | 6mm | 8mm | 10mm |
Bamboo Works | 1mm | 3mm | 4mm | 5mm | 6mm | 7mm | 10mm |
What Thickness Can a Wood Laser Cutter Handle?
A properly adjusted laser cutting machine with a 100 W laser tube cuts 10 mm thick wood although it can handle thicknesses up to 20 mm. However, please note that in this case, the operating speed will be 2 mm/s, and there will be soot at the edges.
Solid wood thicker than 5 mm is rarely cut out with a laser – there is noticeable soot on the material that requires additional post-treatment. If your main task is to cut out thick wooden materials without fouling, we recommend to use CNC router machines.
Tips for Cutting Cutting Machine Wood
To achieve optimal results when working with wood laser cutting machines, follow these best practices for material selection, equipment use, and post-treatment:
Material Quality
Start by selecting high-quality wood with a uniform color and structure, avoiding knots and imperfections. This ensures consistent cutting quality and helps achieve smooth, predictable results. The more homogenous the wood, the better the final outcome will be, minimizing inconsistencies in machining.
Edge Cleanliness with Air Compressor
To prevent fouling and achieve clean, light-colored edges, it’s essential to use an air compressor during cutting. Supplying 1-2 atm of air pressure to the cutting area, as recommended by Wattsan engineers, helps blow away debris and soot, leading to cleaner cuts and a polished finish.
Laser Power Usage
For optimal performance and extended machine life, it's advised to run the laser emitter at no more than 75% of its maximum power. While running at full power might not dramatically impact the cutting results, operating at a lower power level helps prolong the life of the laser tube without compromising quality.
Operator Expertise
The operator's skill level significantly influences both cutting quality and speed. A qualified operator can efficiently manage 5-6 machines simultaneously, maintaining high standards without sacrificing output or precision. Proper knowledge of the equipment ensures efficient operation and consistent results.
Post-Treatment Considerations
Though post-treatment such as sanding and painting is often required for wood projects, working on a high-quality machine like those from Wattsan can reduce the need for additional edge treatment. With the correct settings, the machine produces light, clean edges without excess fouling. However, if fouling does occur, a light sanding or the use of a stiff brush may suffice, especially if tolerances have been adjusted to account for material removal.
Maintenance and Alignment
The quality of your cuts depends heavily on the alignment and maintenance of the machine. Regular cleaning of the optics is crucial to maintaining high cutting quality. Even the best settings and techniques cannot compensate for poorly aligned or low-quality machines, which will inevitably result in substandard work.
By ensuring careful selection of materials, proper machine settings, and maintaining equipment, you can achieve superior cutting results with minimal post-processing required.
Laser Cutting Machine for Wood: Essential Tips for Accurate and Smooth Cuts
Laser cutting machines are increasingly popular for woodworking due to their precision and efficiency. However, achieving the best results requires understanding and optimizing several key factors. Here are essential tips for ensuring accurate and smooth cuts with your laser cutting machine for wood:
Choose the Right Laser Power Selecting the appropriate laser power is crucial for achieving clean cuts. The power output of your machine should match the thickness and type of wood you are working with. For thinner woods or detailed cuts, a lower power setting may suffice, while thicker or denser woods may require higher power. Adjusting the power settings ensures that you get the cleanest and most precise cuts without damaging the wood.
Optimize Cutting Speed The cutting speed plays a significant role in the quality of your cuts. Too fast, and the laser may not penetrate the wood completely; too slow, and you risk burning or charring the edges. Find the right balance by experimenting with different speeds and observing the results. Most laser cutting machines offer adjustable speed settings, so you can fine-tune them to match your specific project requirements.
Use High-Quality Materials The quality of the wood you use can greatly impact the outcome of your laser cutting. Ensure that your wood is free of defects, such as knots or warping, which can affect the cutting process. Additionally, using high-quality, well-sanded wood will result in smoother edges and a better finish.
Maintain Proper Focus and Alignment Accurate focusing of the laser beam is essential for clean cuts. Ensure that the laser is properly aligned and focused on the wood surface to achieve the best results. Many machines come with autofocus features or manual adjustment options to help with this. Regularly check and calibrate the focus to maintain cutting precision.
Utilize Proper Ventilation Laser cutting generates smoke and fumes, especially when cutting wood. Adequate ventilation or an exhaust system helps to remove these byproducts and prevents them from interfering with the cutting process. This not only improves the quality of your cuts but also protects the machine and the surrounding workspace from potential damage.
Experiment with Settings Different types of wood and project requirements may need specific adjustments in laser settings. Experiment with various power levels, speeds, and focus settings on test pieces before starting your main project. This practice will help you determine the optimal settings for different wood types and thicknesses, leading to better results.
Regular Maintenance and Cleaning Keeping your laser cutting machine in good condition is essential for consistent performance. Regularly clean the lens, mirrors, and other components to prevent dust and residue buildup, which can affect the laser’s efficiency. Follow the manufacturer’s maintenance guidelines to ensure the longevity and reliability of your machine.
Leverage Software Features Many modern laser cutting machines come with advanced software that offers features such as design integration, job management, and real-time monitoring. Utilize these features to enhance your workflow, ensure precision, and streamline the cutting process. Software capabilities can also assist in optimizing cut paths and reducing waste.
By following these tips, you can maximize the performance of your laser cutting machine and achieve precise, smooth cuts in your woodworking projects.
Conclusion
Incorporating a laser cutting machine into your woodworking operations can significantly enhance precision, efficiency, and flexibility. With the ability to achieve high accuracy, handle various wood types, and deliver smooth, clean cuts, these machines are a valuable asset for both professional craftsmen and hobbyists. By selecting the right laser power, optimizing cutting speed, and maintaining proper equipment care, you can ensure the highest quality results for your wood projects. The advanced technology of laser cutting not only improves production speed but also reduces waste and supports creative customization. As you explore the capabilities of laser cutting machine wood, these essential tips will help you harness their full potential, ultimately leading to superior craftsmanship and greater satisfaction in your woodworking endeavors.