In the realm of modern manufacturing, precision, efficiency, and versatility are paramount. Enter laser cutting machines, the unsung heroes of metal fabrication. In this article, we delve into the world of laser cutting machine for metal. From understanding the intricacies of their operation to exploring their diverse applications, we aim to shed light on why these machines have become indispensable in the manufacturing landscape. Whether you're a seasoned industry professional or an aspiring entrepreneur, join us on a journey through the cutting-edge realm of laser technology, where precision meets possibility.
Laser Cutting Technology
Laser cutting is a machining process that uses a high-energy laser beam to cut through any material. Laser stands for Light Amplification by Stimulated Emission of Radiation. It is one of the most popular types of industrial cutting processes. Lately, laser cutters have also become prevalent in small workshops, hobbyists, businesses, and schools. Laser cutting works on cutting every material regardless of its physical properties.
Laser beams work in two ways- continuous and pulses. Continuous laser cutting uses a light beam for a long period without intermittent breaks. The pulsed mode uses high-energy laser beams for a short time. The compression of pulses allows for high energy density of the beam.
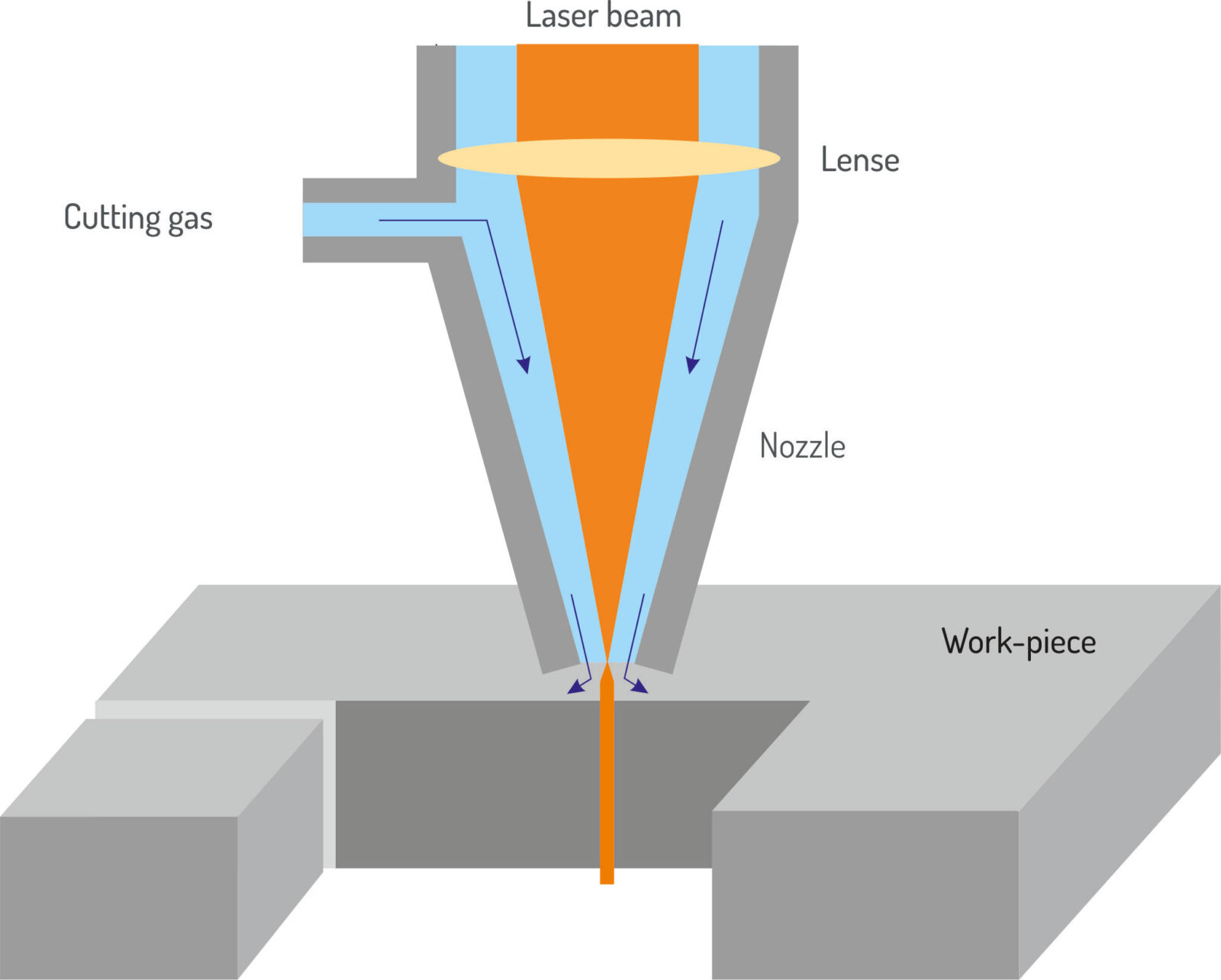
Benefits of Laser Cutting
Unlike mechanical cutting processes that rely on blades and drills, laser cutting uses a focused laser beam to precisely cut through and shape workpieces. Using a laser cutting machine for metal, the workpiece or the laser moves based on instructions derived from a digital design file to cut the workpiece according to the design specifications. Laser cutting has become a popular cutting method in manufacturing for numerous industries and applications.
Some of the benefits of choosing laser cutting over more traditional options include:
- Easy automation. Laser cutting processes fit well into automated production lines.
- Complexity. Laser cutters can create highly intricate geometries quickly.
- Accuracy. Lasers cut sharp, precise edges and create extremely accurate profiles.
- Finish. Laser-cut edges often don’t require any additional finishing operations.
- Versatility. Laser cutting works with a broad range of metals and non-metals, wood, and thermoplastics.
Process of Laser Cutting Machine For Metal
- Design Preparation: The process begins with the creation or transfer of a digital design file into a format compatible with the laser cutting machine's software. This design typically contains the specifications for the desired cuts, including dimensions, shapes, and any intricate patterns.
- Material Selection: Once the design is ready, the appropriate type and thickness of metal are selected for cutting. Laser cutting is compatible with a wide range of metals, including steel, aluminum, copper, and titanium, among others.
- Machine Setup: The selected metal sheet is securely placed onto the cutting bed of the laser machine. The machine's parameters, such as laser power, cutting speed, and focal length, are configured according to the material type and thickness, as specified in the design.
- Laser Beam Generation: The laser cutting process relies on the generation of a highly focused and intense beam of light. This beam is produced within the laser resonator, where energy is converted into light amplification through stimulated emission of radiation (LASER).
- Beam Delivery: The generated laser beam is then directed through a series of mirrors and lenses within the machine's optical path. These components ensure that the beam maintains its focus and accuracy as it travels towards the material surface.
- Material Interaction: As the focused laser beam makes contact with the metal surface, it generates intense heat, causing localized melting, vaporization, or thermal fracturing of the material. The energy from the laser beam is absorbed by the metal, leading to rapid temperature increases and subsequent material removal.
- Cutting Process: Depending on the design specifications, the laser beam follows the predetermined cutting path, guided by the machine's motion control system. The focused energy of the beam melts through the metal along the designated cutting line, creating clean, precise edges with minimal heat-affected zones.
- Gas Assist and/or Coolant: In some cases, a gas assist system is employed to help expel molten metal and debris from the cutting area, preventing buildup and ensuring smooth cutting operations. Additionally, coolant systems may be utilized to regulate the temperature of the workpiece and minimize thermal distortion.
- Quality Control and Inspection: Once the cutting process is complete, the finished parts are inspected for dimensional accuracy, edge quality, and any signs of defects or imperfections. Quality control measures help ensure that the fabricated components meet the required specifications and standards.
- Post-Processing (Optional): Depending on the application and desired surface finish, the cut parts may undergo additional post-processing treatments, such as deburring, surface cleaning, or surface treatment, to achieve the desired final appearance and functionality.
Types of Laser Cutting Process
CO2 Laser Cutting
In CO2 laser cuttings, the laser amplification occurs through a CO2 gas discharge. CO2 lasers are one of the earliest and most popular types of lasers. The gas discharge isn’t entirely Co2. It contains CO2, Nitrogen, Hydrogen, Xenon, and Helium.
C02 laser cutting comes with two options: using Oxygen or Nitrogen gas. Oxygen gas is preferred for laser cutting thicker materials. Nitrogen gas is preferred for laser-cutting thin sheets. Using oxygen C02 laser cutting creates an oxide layer on the cut surface. Pre-treatment processes such as blasting are done on the workpiece to avoid this.
Fiber Laser Cutting
Fiber laser cutting uses optical fiber for light amplification instead of conventional gas discharge. Light emitted through laser diodes passes through the optical fiber. The resultant light beam is sufficiently strong to melt away stainless steel up to 1 cm in thickness.
A strong airflow system often accompanies the light beam. The airflow pushes away the molten material for a clean cut. The fiber optics of these lasers utilize several elements like Ytterbium, Neodymium, Erbium, and Dysprosium.
Nd:YAG Laser Cutting
Nd:YAG stands for Neodymium-doped Yttrium Aluminum Garnet (Nd:Y3Al5O12). Nd:YAG crystals are used in lasers for amplified beam instead of gas discharge or fiber. These lasers are capable of both continuous and pulsed laser beam.
Excimer Laser cutting
Excimer stands for Excited Dimer. Excimer laser cutting uses an ultraviolet laser beam. Excimer laser cutting is used in small-scale precision cutting processes. Some common examples are eye surgery, microelectronics, and semiconductor cutting.
How Thick Can Laser Cut For Metal
Laser Cutting Thickness Limit
While metal laser cutters may be highly precise tools and can cut through thick steel, their capabilities have some limitations. Users will find that the thickness of the steel that a laser cutter can cut through will depend on the power of the laser itself, as well as the type of steel being used.
The reason for this is that thicker steel requires more laser power, which can result in slower cutting speeds and increased heat generation, affecting the quality of the cut and requiring the use of specialised cutting techniques or cooling systems to prevent the steel from warping or melting. Some types of steel, such as stainless steel, are more reflective than others, which can cause the laser beam to bounce off the steel surface, making stainless steel sheets with greater thickness more challenging to cut through.
Cutting Thickness Limit Based on Power
When fabricating different types of steel, the laser’s power must be strong enough to create an intense heat that melts or vaporises the cut material. The higher the wattage of the laser, the more powerful the beam it produces, which translates into thicker materials that can be cut by lasers. Depending on the type of material being cut, the laser’s wattage will vary.
For example, a low-wattage laser may not be able to cut stainless steel sheet thickness. A standard reference for wattage and the maximum thickness of stainless steel sheets and other metals includes:
Type of Laser Cutting Machine | Maximum Thickness of Carbon Steel | Maximum Thickness of Stainless Steel | Maximum Thickness of Aluminium Plate | Maximum Thickness of Copper Plate |
500W | 6mm | 3mm | 2mm | 2mm |
1000W | 10mm | 5mm | 3mm | 3mm |
2000W | 16mm | 8mm | 5mm | 5mm |
3000W | 20mm | 10mm | 8mm | 8mm |
Laser Cutting Machine For Metal Price: Guide For 2024
Laser cutting equipment can provide your business with a quick and effective way to cut, etch, and engrave items. Cutting and Engraving projects with laser machines are more precise and cleaner than most other cutting techniques, and requires less deburring or finishing after the cuts. Though this is dependent upon the materials you cut, laser cutting is famous for making accurate and precise cuts. Prices and costs of laser cutting machines fluctuate greatly depending on the design, type, and ability of laser. If you plan to cut metal, tough woods, or other dense materials, you’ll need a higher watt laser than in case you wished to cut thinner materials, like cloth. On the other hand, the more complex the laser’s wattage, the higher the cost. It’s your choice to balance price and practicality.
- Assessing your commanding computer’s hardware and software will help your cutting machine function quicker, although the upgrade could be expensive.
- Entry-level laser cutting components usually contain very weak lasers, suitable only for light engraving or cutting. Employing an underpowered laser to cut a thick or hard material can ruin the surface, requiring expensive material replacement.
- Most providers of laser cutting machines sell versions in a variety of sizes. Cutting larger objects will need an expensive larger machine. Buying a high watt laser cutting machine can be cost-effective for prolific cutters. If you do not know what you plan to cut out, or you wish to cut a wide variety of materials, a top watt laser is best. This type of laser is sufficiently strong to cut and engrave almost anything, providing you the flexibility you need.
Is Worth Investing High-power Laser Machine
However, high wattage laser cutting machines are usually a lot more expensive than entry-level units. You can pay anywhere from $4,000 to $15,000 for some laser cutter models. Working with our staff at Krrass Laser, we can help you find a price point that caters to exactly what you need. Prices differ widely for each model of Thunder Laser cutting machines. Things you should take into consideration when estimating the cost of a particular model are wattage, work-surface size, the type of laser, and some other additional features you need — generally, the bigger the wattage and work-surface, the higher the cost.
Call us to discuss what additional add-ons your laser machine model ought to have, and get an itemized price estimate. Addons can cost around $2,000 to $5,000, though it varies depending upon the attachments.
CO2 and Fiber Lasers: Price Differences
- CO2 Lasers:
- Price Range: CO2 laser cutting machines typically have a lower initial purchase cost compared to fiber lasers. Entry-level CO2 laser machines can start from around $20,000 to $30,000 for smaller cutting capacities and basic features.
- Operating Costs: While CO2 lasers may have a lower upfront cost, they tend to have higher operating costs due to their higher energy consumption and the need for gas replenishment. CO2 lasers require a supply of carbon dioxide gas, which can add to the ongoing expenses.
- Maintenance: Maintenance costs for CO2 lasers can vary depending on the specific model and usage, but they generally require regular maintenance to ensure optimal performance and lifespan.
- Fiber Lasers:
- Price Range: Fiber laser cutting machines typically have a higher initial purchase cost compared to CO2 lasers. Entry-level fiber laser machines can start from around $50,000 to $100,000 for smaller cutting capacities and basic features.
- Operating Costs: Fiber lasers are known for their energy efficiency, consuming significantly less power compared to CO2 lasers. Additionally, fiber lasers do not require laser gas, resulting in lower ongoing operating costs over time.
- Maintenance: Fiber lasers generally have lower maintenance requirements compared to CO2 lasers, as they have fewer moving parts and do not require gas replenishment. However, routine maintenance is still necessary to ensure consistent performance and longevity.
Things To Consider When Choosing Laser Cutting Machine For Metal
Whether you're cutting metal sheets, pipes, or stainless steel and aluminum rods, there is a laser metal cutter made for the task. There are four key factors to consider when choosing a laser fiber metal cutter: Working area, laser power supply, laser speed, warranty and service offerings:
- Working Area: Also known as bed-size, this is the size of the actual table used for cutting metal. Choose a working area that is large enough to fit the size of the metal you are working with but not so big that it is outsized for your space or needs. Make the most of the cutting surface by choosing an open-faced table model.
- Laser Power Supply: The higher the laser's power supply wattage, the more power the laser will have to cut through metal. More powerful fiber laser metal cutters come with higher price tags, so look for one that meets but does not exceed your needs so that you're not paying for more power than you'll actually use.
- Laser Speed: Laser speed is important to your productivity when cutting metal, but the laser's speed and power supply must be matched so that one does not outpace the other, which could damage the metal you are cutting.
- Warranty and Service: Protect your investment by choosing a reputable company that provides training on its machines and backs up its products with a substantial warranty and expert-level technical support.
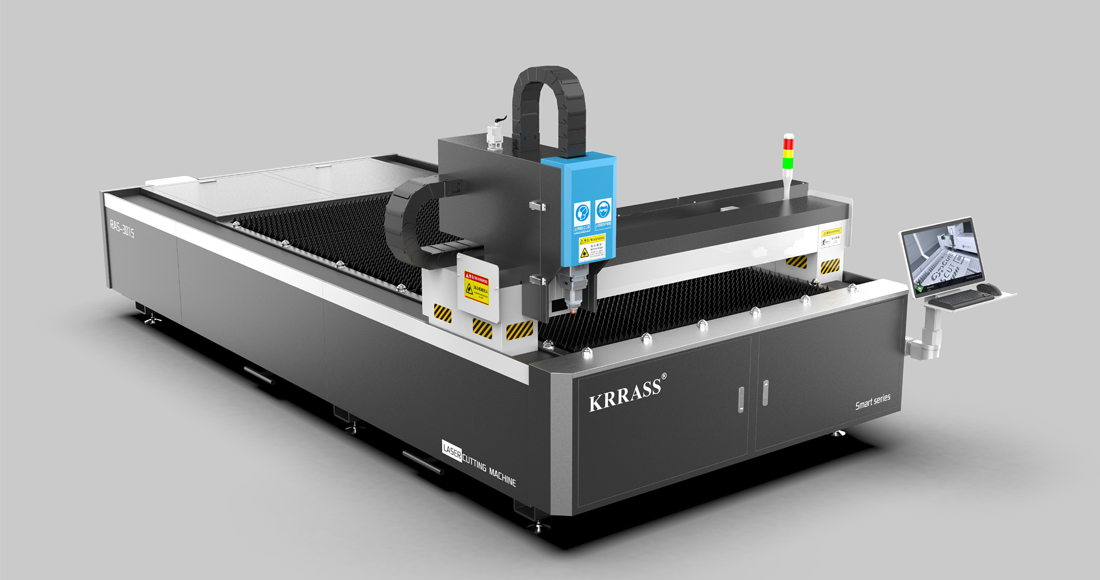