Hydraulic sheet metal bending machines, commonly used in sheet metal fabrication, are essential for achieving precise bends. However, like any complex machinery, they can encounter various issues during operation. This guide provides an in-depth analysis of common faults in CNC bending machines, including potential causes and troubleshooting methods.
1. Excessive Noise from the Hydraulic sheet metal Bending Machine Oil Pump
One frequent issue is the oil pump noise in CNC press brakes, often due to oil leakage or low oil levels, which leads to oil pump suction issues. If the oil viscosity is too high at low temperatures, it increases oil absorption resistance, impacting the efficiency of the CNC hydraulic system. Furthermore, clogged oil suction filters or damage during installation can cause significant noise, leading to long-term damage if not addressed. It's essential to regularly inspect the hydraulic oil pump and ensure proper installation to prevent such issues.
2. No Pressure Build-up in the CNC Hydraulic System
When a bending machine’s hydraulic system fails to build up adequate pressure, it might result from oil pump steering errors, oil pump damage, or even a malfunctioning pressure gauge. Ensure that the pressure control valve isn’t blocked and that the compensation amplifier is functioning correctly. These components play critical roles in maintaining proper pressure in the CNC press brake hydraulic system.
3. Slow Pressure Build-up in Bending Machine with REXROTH Hydraulic System
In some cases, REXROTH hydraulic systems used in bending machines may experience slow pressure build-up due to blocked pressure valve ports or malfunctioning cartridge valves. This problem may be further complicated by electrical issues, such as solenoid valve failures, which can delay the pressure build-up process in the bending machine hydraulic system.
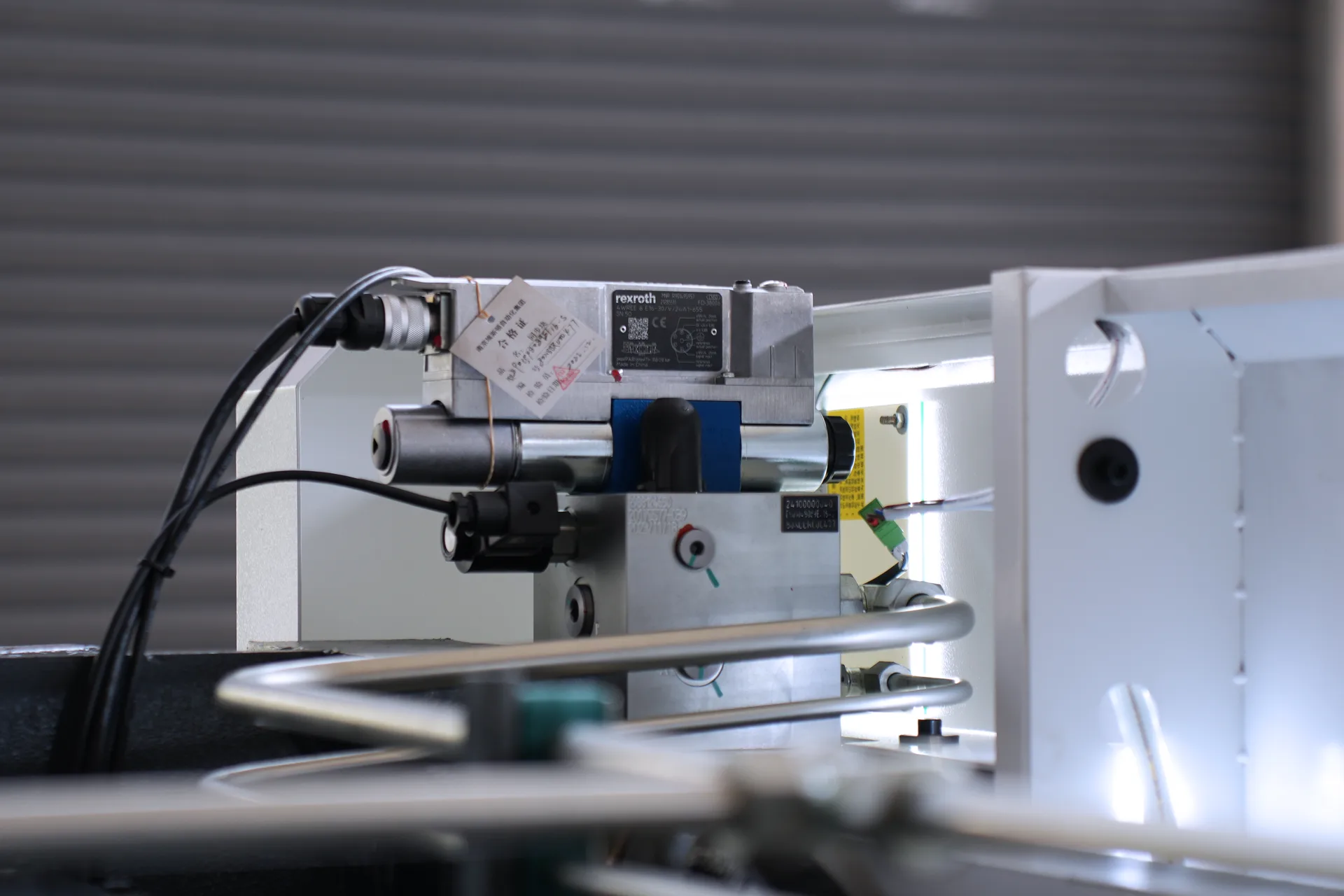
4. Impact Sounds During Hydraulic sheet metal Press Brake Operation
Impact sounds can occur during bending machine operation, often caused by loose rails or improper installation of the grating ruler. This mechanical issue can result in misalignment and poor bending accuracy. Addressing such mechanical issues promptly can improve the machine's overall performance, particularly in terms of bending precision.
5. Slider Fails to Perform Quick Action
The failure of the CNC press brake slider to perform quick actions could be linked to a fast-down valve malfunction or lack of electrical signals to the electromagnetic proportional directional valve. Mechanical issues such as a tight guide plate or cylinder can also prevent the slider from functioning properly. Regular maintenance and inspections ensure the smooth operation of the bending machine’s slider.
6. Prolonged Pause at the Slider Speed Conversion Point
When the bending machine experiences a long pause at the speed conversion point, it may be due to air entering the oil tank’s upper chamber, which delays pressure build-up. An incomplete closure of the filling valve or a low flow rate through the self-suction pipe can also contribute to this issue. Ensuring proper closure and pressure regulation is crucial for efficient machine performance.
7. No Slider Slowdown in Bending Machine
A common issue in bending machines is the slider failing to slow down, typically caused by electromagnetic proportional reversing valve malfunctions, or system pressure that cannot be built. Regular checks on the filling valve and associated pressure components help maintain the machine’s operational integrity.
8. Slider Vibration, Swinging, or Noise During Operation
Vibration and noise during the slider’s movement in bending machines often point to air bubbles in the hydraulic oil, excessive friction between slider rails, or uneven gaps in the guide plate. These mechanical faults can disrupt the smooth operation of the CNC hydraulic press brake. Regular lubrication and inspection of the hydraulic system can minimize such issues.
9. Synchronization Errors During Slider Slowdown
Synchronization errors when the CNC press brake slider slows down are typically caused by faults in the CNC system parameters or proportional directional valves. These errors can lead to inaccurate bending angles and affect overall machine efficiency. Regularly fine-tuning the system’s parameters ensures smooth operation.
10. Oscillation and Jitter at the Lower Dead Center
When the CNC press brake’s slider oscillates or jitters at the lower dead center, it’s often a sign of issues with the grating ruler or the pressure parameters of the CNC system. Oscillation can lead to inaccurate bending angles and should be addressed immediately to avoid further complications in metal sheet bending operations.
11. Slow or No Return of the Slider
The slow return or complete failure of the bending machine slider to return to its original position could be due to a damaged electromagnetic proportional reversing valve or low return pressure. Such issues can affect the overall production speed and precision of the machine, especially during repetitive bending tasks.
12. Vibrations During Slider Return
If the bending machine experiences vibrations during the slider’s return, the issue is often linked to improper pressure settings or faults in the system parameters. Adjusting the pressure and ensuring proper calibration of the proportional valve helps mitigate these vibrations, ensuring smooth machine operation.
13. Slider Sliding at the Top Dead Center
A sliding slider at the top dead center of the bending machine can indicate issues with the back pressure valve, hydraulic oil levels, or the stability of the sealing ring. Addressing these components can help prevent unwanted sliding, which can impact the accuracy and safety of sheet metal bending operations.
14. Large Bending Angle Errors
Large errors in the bending angles produced by Hydraulic sheet metal bending machines can result from a compensation cylinder not fully restoring to zero, loose quick clamping, or issues with the grating ruler. Variations in the material, such as thickness or stress, can also cause inconsistencies in metal bending angles.
15. Significant Bending Errors in CNC Press Brakes
If a CNC press brake produces significant bending errors, it could be due to the deformation of the upper and lower dies, problems with the worktable, or insufficient compensation for deflection. Ensuring proper die alignment and inspecting the machine's components can help achieve more precise sheet metal bending results.
16. Hydraulic Line Leakage in CNC press brakes
Leaks in the CNC hydraulic system are typically due to improper tubing installation, vibration, or external impact. Ensuring that all hydraulic lines are correctly installed and secured with clamps is vital to preventing leaks that could affect the machine’s performance.
17. Important Considerations for Hydraulic System Installation and Maintenance
During the installation and maintenance of the CNC hydraulic system, it’s crucial to avoid tampering with any sealed valves. After servicing the system, always replace the hydraulic oil and clean the oil tank to ensure the system functions optimally.
18. Common Rear Stopper Faults in Hydraulic sheet metal press brakes
Issues with the rear stopper in Hydraulic sheet metal bending machines, such as failure to move or drive alarms, often arise from mechanical problems or faulty encoder cables. Checking the X and R axes for instability and ensuring the proper alignment of the servo motor can help prevent these faults.
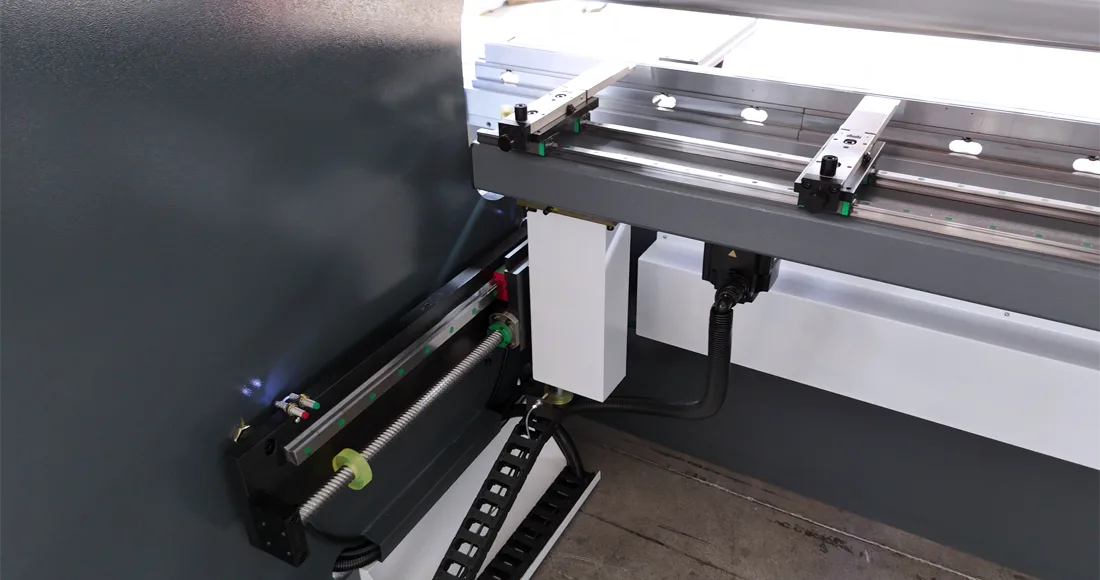
Siempre podemos confiar en la calidad de esta máquina de doblado
Buena calidad, buen servicio, todo perfecto