In the world of metal fabrication, hydraulic shearing machines play a crucial role in cutting and shaping materials with precision and efficiency. Whether you're a small workshop or a large manufacturing facility, understanding the price dynamics of these machines can significantly impact your investment decisions. This ultimate guide will explore the various factors that influence hydraulic shearing machine price, from types and features to market trends and cost-benefit analyses. By the end of this article, you'll be equipped with the knowledge needed to make an informed purchase, ensuring you get the best value for your investment.
What Is A Hydraulic Shearing Machine
Before we get to the prices, let us first understand what a Hydraulic Shearing Machine is and its uses. A Hydraulic Shearing Machine is an industrial tool used for cutting metal bars and sheets that you otherwise would find difficult to cut. It includes a combination of rotating blades and disks that allow for the above-mentioned action.
Hydraulic shearing machines, while sharing a similar core mechanism, can be categorized based on the shape of their blades—either linear or circular. Shearing is one method of shaping metal and other materials, alongside other techniques such as bending, cutting, spinning, and rolling.
These machines are essential tools in fabrication, with widespread applications across various industries. Krrass, a well-known manufacturer, has built a strong clientele from diverse sectors that rely on these machines for their operations. Primarily, hydraulic shearing machines are used in manufacturing to produce a range of products.
They are particularly valuable in heavy-duty industries, contributing to the production of components for ships, airplanes, and railways. Additionally, they find use in other sectors, such as the culinary, electrical, and decorative industries, showcasing their versatility and importance in modern manufacturing.
What's the Working Principle of Hydraulic Shearing Machine
A hydraulic shearing machine uses a hydraulic system to drive a moving blade, cutting metal sheets into the desired shape with powerful hydraulic pressure. The operation begins with the operator placing the metal sheet on the shearing table and adjusting the back gauge to ensure correct material positioning. Once the hydraulic system is activated, the hydraulic pump generates pressure, delivering hydraulic fluid to the cylinders, which drive the blade carrier downward. The moving blade approaches the fixed blade in a scissor-like motion, completing the shearing process.
After the cut is complete, the hydraulic cylinders retract, and the blade carrier returns to its initial position, ready for the next operation. Operators can adjust the cutting angle, blade clearance, and stroke length to accommodate different materials and thicknesses, ensuring high-precision cutting. Hydraulic shearing machines are widely used in metal fabrication, heavy industry, and light industry due to their precision, versatility, and efficiency. They are instrumental in producing components for vehicles, ships, airplanes, and electrical appliances.
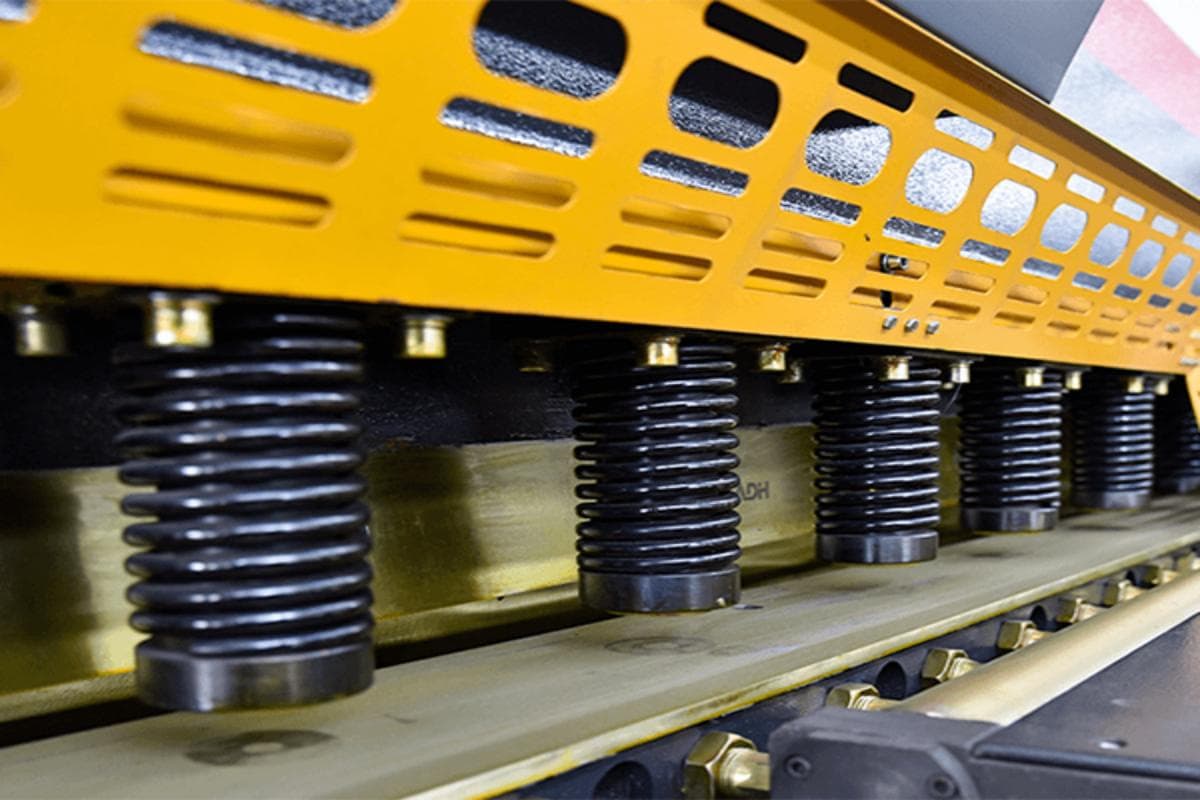
What's the Parts of Hydraulic Shearing Machine
The Rack
The entire body of the machine is built to be sturdy, durable, and reliable.
The tool holder
It has the shearing tool (upper blade) attached to it. With the force from the hydraulic system, it realizes the shearing process, cutting the materials in desired sizes.
Gap adjustment tool
This tool allows you to adjust the gap between the upper and lower blades to ensure that the best shearing force is utilized. It helps get high-quality work while ensuring the longevity of the shearing blade.
Back gauge mechanism
It is fixed to the tool holder and has other features attached to it like adjusting mechanisms (micromotion, back gauge motor), digital display, a mechanism for lifting tailgate, guide rod, and more.
Safety guard and pressing tool
The safety guard is located in the front wall of the machine from where the desired material is inserted. It is a protective fence that prevents any personal injury of the operator.
The pressing tool (presser foot) is used to press down the material to prevent it from striking while the shearing process is going on.
Frontal loading area
This is the area where you can insert the material within the machine for the shearing process to begin. It is structured in a way that is efficient and convenient for the workers to load and unload the materials.
The electrical unit
This unit is responsible for feeding instruction into the system, controlling the power, initiates the oil pump, and the hydraulic system.
The hydraulic system
Mainly consisting of the hydraulic system, oil pump, cylinder, line, pressure cylinder, and the likes. It is responsible for building up the force that allows the shear to cut the materials.
To see a Hydraulic Shearing Machine in action, you can watch Accurl’s demo videos of the machines. This will help you get a good understanding of the working mechanism of the tool along with management tips.
Hydraulic Shearing Machine Uses
The shearing machine offers exceptional support for industrial production with its high-precision and high-speed cutting capabilities. These specialized tools are integral to industries such as machinery manufacturing, aerospace, and automobile production.
In the aerospace sector, for example, shearing machines are used to cut high-strength steel plates, essential for manufacturing aircraft components. Similarly, in the automotive industry, these machines efficiently cut both steel and aluminum plates to produce parts like car bodies and doors.
Beyond industrial applications, shearing machines are also employed in various other fields, including household appliances, electronics, and building decoration. In the household appliance industry, they cut stainless steel plates for products like refrigerators and air conditioners. Meanwhile, in the electronics industry, shearing machines are used to cut aluminum plates for computer and mobile phone casings.
What Are Types of Sheaing Machine
Depending on the drive mode, common types of shearing machines mainly include manual sheet metal shearing machines, mechanical shearing machines, hydraulic shearing machines, and pneumatic shearing machines.
1. Manual Sheet Metal Shearing Machine
Manual sheet metal shears are equipment that can perform cutting of plates by manually moving the blade up and down. These shears are powered by hand, easy to operate and suitable for cutting small plates, but their cutting accuracy is low and cannot meet the requirements of large plates.
2. Mechanical Shearing Machines
The mechanical shearing machine operates using a power device consisting of a motor, flywheel, worm shaft, and clutch. It has faster cutting speeds and more strokes per minute compared to the hydraulic shearing machine.
The flywheel of the mechanical shearing machine stores energy, allowing a motor with lower horsepower to be used. Based on the operation mode, mechanical shearing machines can be further divided into up-moving and down-moving types.
3. Hydraulic Shearing Machines
The hydraulic shearing machine is powered by a hydraulic cylinder and motor. The motor drives the hydraulic cylinder, applying hydraulic oil pressure to the piston, providing power to the upper blade's piston.
The hydraulic shearing machine has a longer stroke and can handle different load capacities. Materials cut using a hydraulic shearing machine have a smooth surface with minimal markings. These machines are known for their large shearing force, stable operation, and good controllability.
The hydraulic shearing machine can be categorized into two types: the swing beam shearing machine and the guillotine shearing machine.
The swing beam shearing machine performs the shearing movement by swinging the tool rest, resulting in high speed, high shearing accuracy, and high efficiency.
The guillotine shearing machine can be powered either by hydraulic or mechanical means. It consists of a working table, upper and lower blades, a hydraulic piston, a clamping tool, and a blank holder.
This machine can cut plates of varying thicknesses and lengths due to their ability. The movable blade of the guillotine shearing machine can be straight or angled to reduce the cutting force.
Equipped with CNC system, the guillotine shearing machine can handle large cutting thicknesses and lengths with fast cutting speed, making it ideal for mass production. However, the cut edges produced are rough and unattractive.
Comparison of Mechanical and Hydraulic Shearing Machines
Feature | Mechanical Shearing | Hydraulic Shearing |
Transmission | Mechanical (crank linkage, gear) | Hydraulic (hydraulic cylinders) |
Cutting Speed | Faster in full-cycle mode | Slower, but can operate continuously |
Capacity | Limited to thinner materials (up to 1/4" plate) | Can cut thicker materials (3/8" to 1" plate) |
Precision | Lower accuracy and adjustability | Higher accuracy and precise adjustments |
Noise | Loud during operation, but quieter overall | Constant noise from hydraulic system |
Maintenance | Simpler mechanisms, easier to maintain | More complex, but designed for easy operation and maintenance |
Safety | Can be stopped mid-cycle, but more hazards | Automatic reverse, light curtains, overload protection |
Cooling | Not required | Hydraulics run hot and require cooling |
Environmental Impact | No hydraulic waste (oil, filters) | Produces hydraulic waste |
Shock Resistance | More shock resistant due to robust construction | Less shock resistant due to hydraulic cylinders |
Pneumatic shearing machines utilize a pneumatic system to control the blade's up-and-down movement for cutting metal plates. These machines are known for their high shearing speed and accuracy, as the blade's movement can be precisely adjusted through air pressure. They are particularly well-suited for cutting specialized plates with high hardness and strength.
Due to their rapid cutting speed and precision, pneumatic shearing machines are ideal for applications requiring high-speed and high-precision cutting. There are two main types of shearing machines used for cutting plates: linear and circular.
Linear shearing machines are powered by hydraulic systems and are capable of handling thicker metal plates. On the other hand, circular plate shearing machines are motor-powered and designed to cut circular metal plates. Each type of shearing machine has its advantages and is tailored for different cutting needs.
Users can choose the most suitable shearing machine based on their requirements and the material properties. For example, manual shearing machines are perfect for cutting small plates, while larger plates may necessitate the use of a guillotine or pneumatic shearing machine.
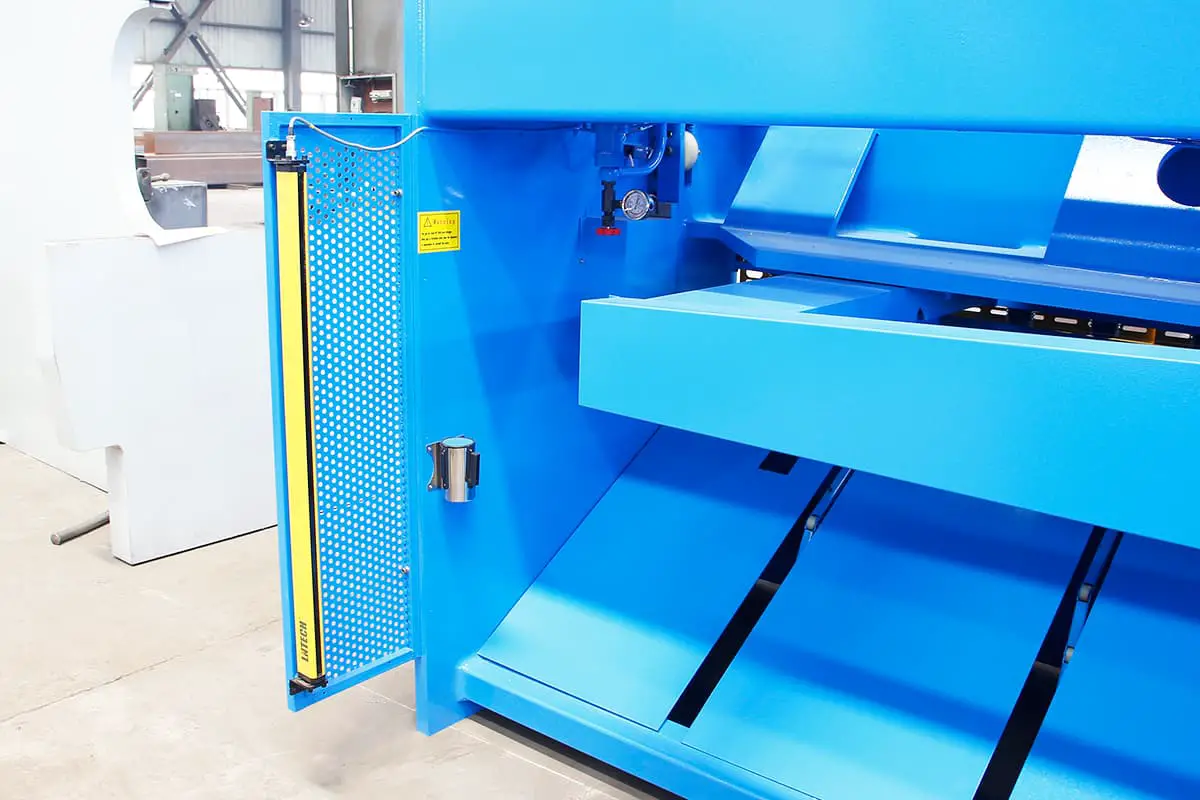
What's the Price of Hydraulic Shearing Machine
The price of a hydraulic shearing machine varies widely, typically ranging from $5,000 to $80,000 depending on its size, capacity, brand, and features. Used machines generally cost less than new ones, with prices influenced by factors such as condition and age. Here's a general overview of the price range you can expect:
Price Range
- Small to Medium-Sized Machines:
- Typically used in small workshops or for light industrial applications.
- Price range: $5,000 to $30,000.
- Large Industrial Machines:
- Suitable for heavy-duty applications and large-scale production.
- Price range: $30,000 to $100,000 or more.
- High-Precision CNC Hydraulic Shearing Machines:
- Equipped with advanced controls and automation features for precision cutting.
- Price range: $50,000 to $200,000 or more, depending on the sophistication and capabilities.
Swing Beam vs Guillotine Shears: Which Is More Expensive
When comparing swing beam shears and guillotine shears, the cost difference is influenced by various factors, including the machine's design, capacity, and features. Here's a breakdown of each type and their relative costs:
Swing Beam Shears
Description:
- Swing beam shears use a pivoting beam to cut materials, where the blade swings down in an arc to perform the cut.
- They are generally suitable for cutting medium to large sheets and are known for their reliability and simplicity.
Price Range:
- Typically priced between $15,000 and $60,000 depending on the size, capacity, and features.
- Generally, they are less expensive than high-end guillotine shears.
Advantages:
- Often less complex and easier to maintain.
- Suitable for a wide range of applications and materials.
- Generally more affordable for medium-sized operations.
Guillotine Shears
Description:
- Guillotine shears use a straight, vertical blade that moves downwards in a linear motion to cut materials.
- They are known for their precision and are often used in high-precision and heavy-duty applications.
Price Range:
- Typically priced between $30,000 and $100,000 or more, depending on size, capacity, and advanced features.
- High-end models with advanced CNC controls and automation can exceed these ranges.
Advantages:
- Known for providing high precision and clean cuts, especially for large or thick sheets.
- Often equipped with advanced features and automation options, leading to higher costs.
- Suitable for large-scale and high-volume production environments.
Cost Comparison
Guillotine Shears are generally more expensive than Swing Beam Shears. This is due to several factors:
- Precision and Features: Guillotine shears often come with advanced features, CNC controls, and automation, which increase their cost.
- Heavy-Duty Construction: Guillotine shears are built to handle thicker and harder materials, which can add to their price.
- Market Position: Guillotine shears are often positioned as high-end machines for demanding applications, which reflects in their higher price tag.
Swing Beam Shears, while generally less expensive, provide a good balance of cost and functionality for many industrial applications, especially in medium-sized operations.
If you are looking for a more cost-effective option and your needs are aligned with medium to large sheet cutting, a swing beam shear might be the better choice. For high-precision cutting, larger volumes, and advanced features, a guillotine shear, though more expensive, may offer greater value.
What Factors Affect Hydraulic Shearing Machine Price
Several factors influence the price of a hydraulic shearing machine. Understanding these factors can help you make a more informed decision when purchasing or budgeting for this equipment:
Machine Size and Capacity
Size: Larger machines with greater cutting capacities and larger beds typically cost more. Machines designed to handle bigger or thicker materials require more robust construction.
Capacity: The ability to cut materials of varying thicknesses and widths affects the price. Higher capacity machines, capable of cutting thicker or larger sheets, are generally more expensive.
Brand and Manufacturer
Reputation: Well-established brands with a strong reputation for quality and reliability often command higher prices. These brands may also offer better after-sales support and warranty.
Manufacturing Standards: Higher-quality materials and construction standards from reputable manufacturers can lead to a higher price.
Technology and Features
Control Systems: Machines with advanced CNC controls, automation, and digital displays generally cost more. These features offer increased precision and efficiency.
Additional Features: Options such as programmable backgauges, auto-lubrication systems, and advanced safety features can also impact the price.
Material Type and Thickness
Specialized Cutting: Machines designed to cut specialized or harder materials (e.g., high-strength alloys) may be priced higher due to the need for more durable components.
Cutting Thickness: Higher thickness capabilities often mean more robust and expensive machines.
Manufacturing Complexity
Design and Build Quality: More complex designs and higher build quality (e.g., robust frames, precision-engineered components) can increase the cost.
Customization: Custom-built or modified machines tailored to specific applications or requirements often come with a higher price tag.
Automation and Efficiency
Automation Levels: Fully automated shearing machines with advanced feeding systems, blade positioning, and cutting controls are typically more expensive than manual or semi-automated models.
Energy Efficiency: Machines designed to be energy-efficient or to minimize operational costs may also come with a higher initial price.
Market Conditions
Supply Chain: Fluctuations in the cost of raw materials and components can affect the overall price of the machine.
Demand: High demand for shearing machines can drive up prices, while lower demand might result in discounts or better deals.
After-Sales Support and Warranty
Service and Maintenance: Machines that come with comprehensive after-sales support, training, and extended warranties may have a higher price but offer greater long-term value.
Parts Availability: Availability of spare parts and ease of maintenance can also influence the overall cost of ownership.
Understanding these factors can help you evaluate your needs and budget effectively, ensuring you select a hydraulic shearing machine that offers the best value for your specific applications.
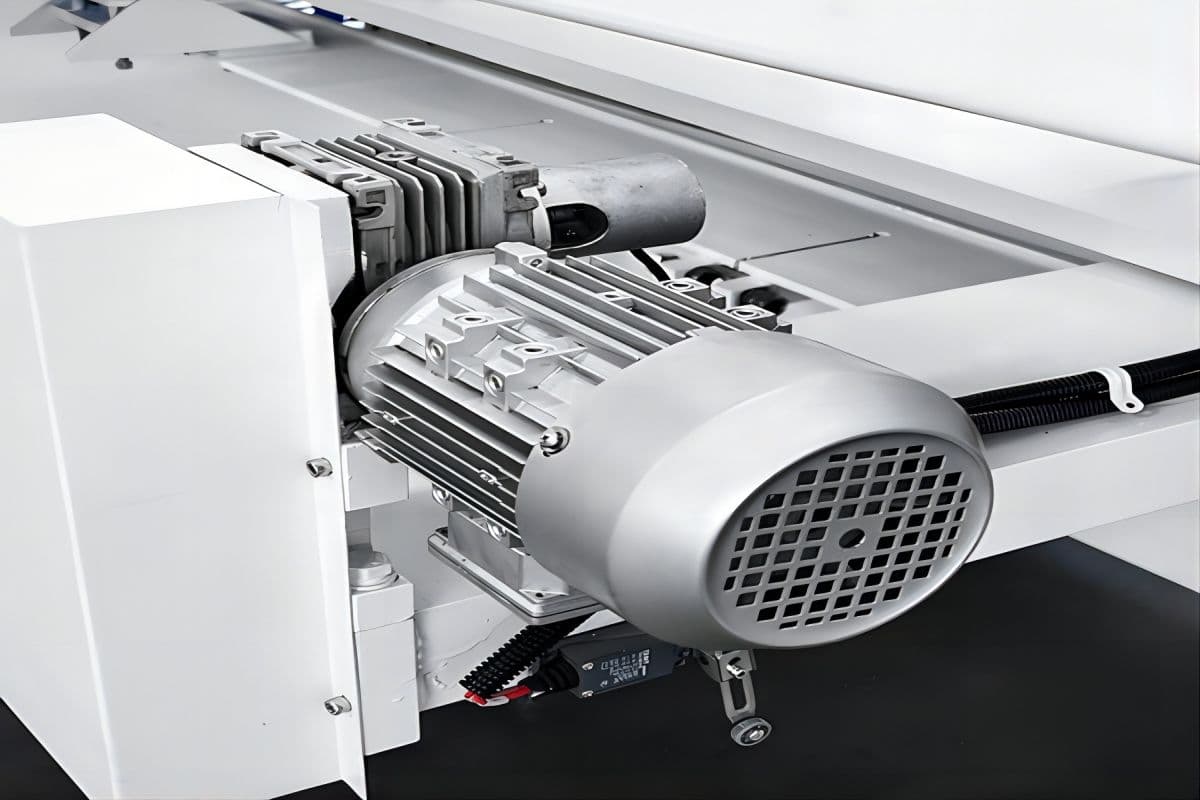
Used Hydraulic Shearing Machine Price
The price of a used hydraulic shearing machine varies significantly based on several key factors, including the machine's age, condition, brand, size, and features. Here’s a detailed guide to help you navigate the market and understand the price variations.
1. Price Ranges for Used Hydraulic Shearing Machines
- Small to Medium-Sized Used Machines:
- Price Range: $5,000 to $20,000
- Description: These machines are typically used in smaller workshops or for lighter industrial applications. They are ideal for cutting thinner sheets and are more budget-friendly. Prices within this range will depend on the machine’s specific capacity, condition, and brand.
- Large Industrial Used Machines:
- Price Range: $20,000 to $50,000
- Description: Designed for heavy-duty tasks and large-scale production environments, these machines offer greater cutting capacities and durability. They are suitable for thicker and larger materials, making them more expensive. The cost within this range will vary based on factors like cutting length, thickness capacity, and the machine's overall condition.
- High-End Models with Advanced Features:
- Price Range: $30,000 to $80,000 or more
- Description: These machines come equipped with advanced technology such as CNC controls, automation features, and high-precision cutting capabilities. They are often used in high-volume or specialized manufacturing environments. The higher price reflects the advanced features and the machine’s ability to perform complex tasks with greater efficiency and accuracy.
2. Factors Influencing the Price
- Age and Condition:
- Age: Newer models generally command higher prices. Machines that are well-maintained and relatively new may offer better value, as they are less likely to require significant repairs or upgrades.
- Condition: The physical and operational condition of the machine plays a crucial role in determining its price. Machines with minimal wear, proper maintenance, and functioning components will be priced higher.
- Brand and Model:
- Brand: Reputable brands such as Accurl, Amada, or Trumpf often have higher resale values due to their reliability and durability. Well-known brands are perceived to have better build quality and performance.
- Model: Certain models that are popular or known for their advanced capabilities may be priced higher. Specific features and innovations associated with a particular model can also influence its price.
- Size and Capacity:
- Size: Larger machines with extensive cutting capabilities are typically more expensive. The size of the machine affects its ability to handle larger sheets and thicker materials.
- Capacity: The cutting capacity, including the maximum material thickness and width the machine can handle, affects the price. Higher capacities generally mean a higher price.
- Features and Technology:
- Controls and Automation: Machines with advanced CNC controls, programmable features, and automation systems are priced higher. These features enhance precision, efficiency, and ease of operation.
- Special Features: Additional features such as advanced blade positioning systems, auto-lubrication, and safety enhancements contribute to higher prices.
- Market Conditions:
- Supply and Demand: The availability of used machines and market demand can impact pricing. A high demand or limited supply may drive prices up, while a surplus or lower demand might offer more competitive pricing.
- Economic Factors: Economic conditions, such as fluctuations in material costs and overall market trends, can influence equipment prices.
3. Where to Find Used Hydraulic Shearing Machines
- Industrial Equipment Dealers: Specialized dealers often have a range of used machines and can provide detailed specifications and condition reports. They may also offer warranties or service packages.
- Online Marketplaces: Websites like eBay, MachineryTrader, and Machinio list used hydraulic shearing machines from various sellers, allowing you to compare prices and features easily.
- Auctions: Equipment auctions, both physical and online, can be a good source for finding used machines at competitive prices. Auctions often feature machines from various sellers and can offer deals.
- Direct from Previous Owners: Buying directly from businesses that are upgrading or closing can sometimes yield better deals. This route may also provide insights into the machine’s history and usage.
4. Tips for Purchasing a Used Hydraulic Shearing Machine
- Inspect the Machine: Always perform a thorough inspection of the machine’s physical condition, operational functionality, and any signs of wear or damage. Verify that all components are in working order.
- Request Documentation: Obtain maintenance records, service history, and any available documentation. This helps assess the machine’s reliability and potential need for future repairs.
- Compare Prices: Research similar used machines to gauge fair pricing. This helps ensure you are getting a competitive deal and not overpaying.
- Consider Additional Costs: Factor in potential costs for refurbishment, repairs, or upgrades. Budget for any additional expenses that may arise to bring the machine up to your operational standards.
Conclusion
When selecting a shearing machine manufacturer, it is crucial to consider factors such as common hydraulic shearing machine prices, functionalities, warranty, and other details thoroughly.
KRRASS is a renowned manufacturer of sheet metal processing machines with over 20 years of experience. They offer a range of high-quality and reliable equipment, including hydraulic press brakes and plate shearing machines. The performance and durability of KRRASS machines are well-regarded, with competitive pricing for hydraulic press brakes and other products.
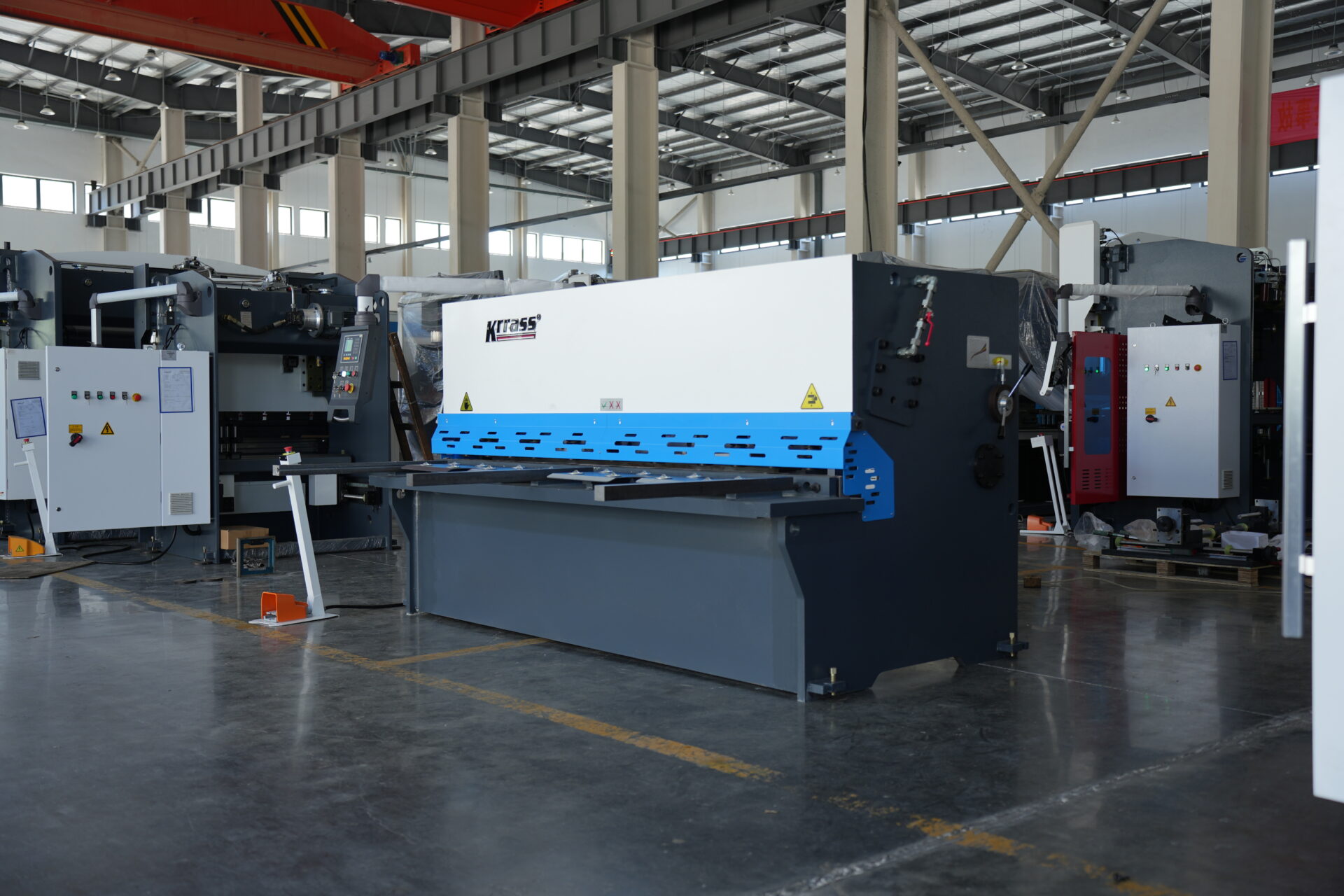
Reviewed by 3 users
Great shearing machine and always work well
i have been working with KRRASS for 7 year, their quality Always reliable
hydraulic shearing machine
The best cutting machine in China, reasonable design, durable, blade material is H13, very good, we cut stainless steel, very sharp.