Hydraulic Press Brake is a machine used for bending sheet metal and metal plate, most commonly sheet metal. It forms predetermined bends by clamping the workpiece between a matching top tool and bottom die.
Warning!
When using the machine, basic safety precautions should always be followed to reduce the risk of fire, electric shock and personal injury.
Read all instructions before attempting to operate this machine and keep these instructions.
- Operator must know about the construction and feature of the machine. If more than one person operates the machine, a director must take charge of the producing!
- Prohibited the hands enter between the upper punch and lower dies!
- Keep the machine and around ground clean and the lines isolating!
- Keep the worktable area clear, avoid something enter between the toolings making accident!
- Inspect all parts of the machine usually; make sure there is no hidden danger!
- The max working pressure is 23 MPa: it has been adjusted before outing the factory, the user can adjust it according to the actual situation.
- Opening the electric cabinet by not authorized service personnel is prohibited! Please make sure the Power switch is on the OFF position before opening the door of electric cabinet!
Safety notes!
1. DANGREOUS:
Error operation may cause die or serious injure.
2.NOTE:
Fault operation may cause mid-grade harm, flesh wound or damage.
There are emergency stop buttons on the handle control station. When there happens error operation or other accidents, push the emergency stop button, the machine will power off.
Safety device checking list
Please check the safety related device according to the below checking list before starting the machine:

Catalogue
- Technical parameters
- Overall picture
- Functions and Range of Work
- Hoisting and Installation of Machine
- Working theory
- Control axes
- Hydraulic parts
- Safeguard
- NC system parameters
- Startup
- Maintenance
Introduction!
We suggest all users and operators to read this operation manual carefully before using this machine.
This manual is designed for specialized and qualified personnel. It comes completes with diagrams and all the documentation necessary to lift, move and place the machine and instructions for the safe use and maintenance of this machine. All information contain in here are accurate at the time of print. However, our company reserves the rights to modify and improve specifications without prior notice.
This machine should be properly installed as instructed; regular inspection and faithful maintenance service should be carried out so that good performance can be maintained.
Any incorrect and irresponsible usages may cause irreparable damage to the machine and nullify the safety protection for the operator.
We do not assume any responsibility for improper services or modifications or connections made by unauthorized personnel.
We suggest that all users to read and understand this manual before using this machine.
2.Overall picture
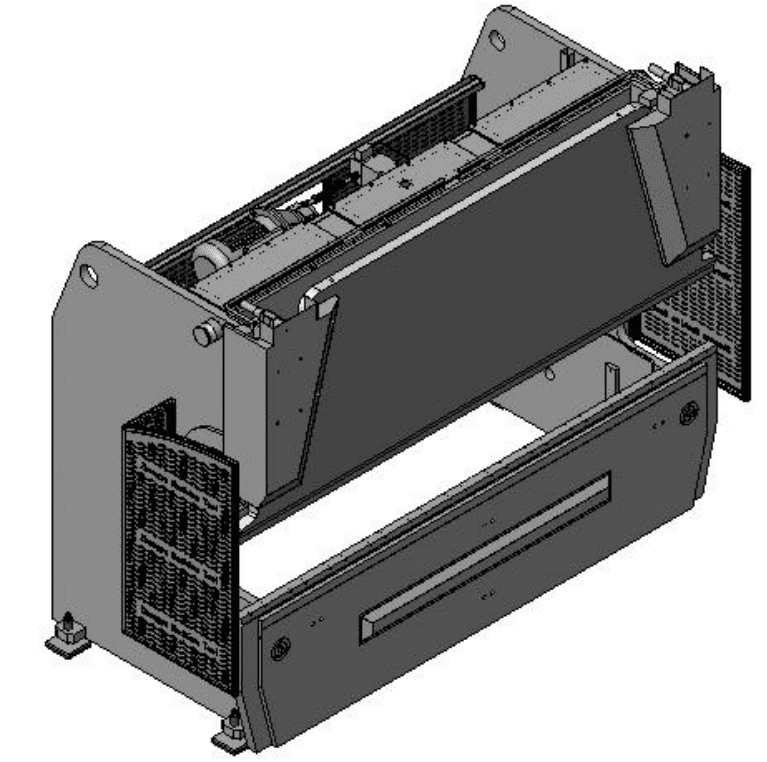
3.Functions and Range of Work
The electro hydraulic servo numeric-control press brake is high-efficiency and high-precision in bending sheet metal. The opening size of V-gutter on lower dies, usually larger than eight times of the sheet thickness, should be regulated for sheets in different thickness. Using different kinds of upper and lower dies can bend all kinds of work pieces. And see the Sheet of Bending Brake (on the body of machine) for desired bending force or calculate out the bending force using bending formula. One slider travel makes a sheet bending and the complicated shape work piece may be achieved through bending many times.
The Hydraulic Press Brake machine is structured in steel plate fabrication with sufficient strength and rigidity. The hydraulic drive prevents the machine from serious overload operation accidents caused by the change of sheet thickness or bad choice of lower die cavity. Additionally, this machine is also featured by the steadiness of work, convenience of operation, and reliable safety. The connecting section to the upper die is provided with compensation device, which compensates the deflection of worktable and slider in bending and guarantees the high work precision.
It is equipped with hydraulic electric control, freely adjustable slider travels and inching operating criterion convenient for module trial and adjustment.
This machine is advanced in technology and reliable in performance, and among the ideal shaping apparatuses. It is widely used in plane, automobile, shipbuilding, and machine with high production efficiency.
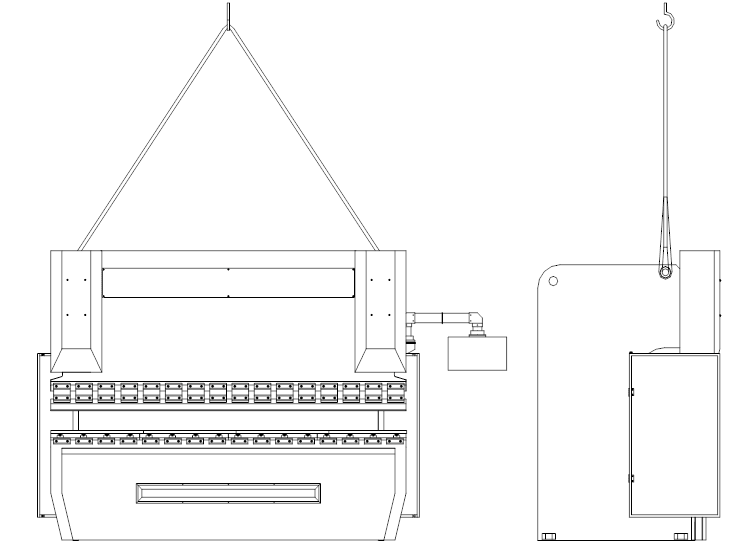
4.Hoisting and Installation of Machine
4.1 Hoisting of Machine
Given a high center of gravity, this bending brake is heavy in the front and light in the rear. So attention must be paid to the center of gravity in order to avoid the turnover of machine. Silk ropes should be used at small included angle to assure the consistency of machine.
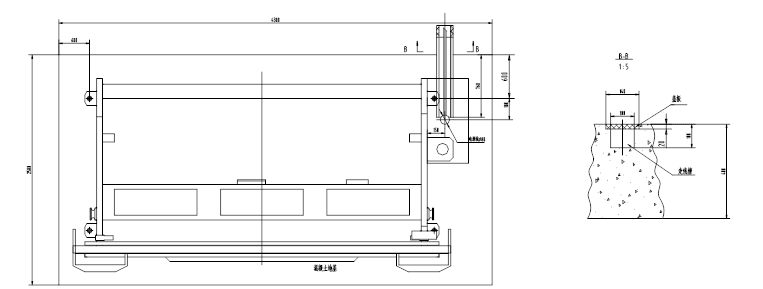
4.3 Clear up
Before running the Hydraulic Press Brake, must get rid off the rust protection oil on the following moving parts.
---the surface of piston pole
---surface of slider raster guide rail
---the surface of guide rail, axis, supporting on the bake gauge
---the surface of slider guide rail
---the surface of worktable and mould set
Note: Permit to use gasoline and coal oil to clean, prohibit using dissolvent wash.
4.4 Level
Note: Place the Hydraulic Press Brake on the horizontal underlay. To do the precision adjustment after all parts of machine are connect well including electrical parts. The process is: set the slider block on the upper dead spot, set a gradienter (precision is ±0.05mm/m) on the two sides of slider blocks, adjust the vertical level. The horizontal level adjustment set a gradienter (precision is ±0.05mm/m) in the middle of worktable, and in all this process, the bottom screw must be connected well.
Note: The level must be check and adjust again after using for 30-50 hours.
4.5 The connections of electric
After main switch (power phases: R, S, T, PE) coupling, check the hydraulic pump orientation through short testing start. If the orientation is wrong, cut the power right away, and exchange the two phase-lines (see the hydraulic pump moving arrowhead).
The cable entrance set on the bottom of electric box.
Note: (1) Confirm the voltages are matching.
(2) Make sure to let the expert of electric or expert according the manual to instruct person to do the electric connection of machine.
5.Working theory
The Hydraulic Press Brake is gathering with numerical technology, servo and hydraulic, upper crossbeam through the movement of control valve to carry out moving up and down periodically, the measure of movement read by the rasters at two sides of the machine.
DNC control the hatches of two valves in left and right oil cylinders. If need, the flux in oil cylinder can be reassigned by servo, make the upper crossbeam to move straight on vertical orientation, and the measure of movement is decided by new measured pulse number. (Fig. 3)
6.Control axes
6.1 The definition of axes
Through DNC to control axes
Left oil cylinder of slider block: Y1
Right oil cylinder of slider block: Y2
Lower crowing table: V
The back gauge moving front and bake: X
Note: The position of slider block can be programmed by equation of absolute value and size of angle.
Manual adjusting Z1, Z2, R1, R2
6.2 The position and character of each axis

Note: (1) According to the DNC manual operation to do the programs of axes
(2) The left and right in the table means we face the front of machine.
Warning: (1) The operator should pay attention to the position of back gauge, if it through the area of mould, the machine will be damaged.
(2) When adjusting the Z axis manual only allow to do it from the back of machine.
(3) Must be careful when adjusting back gauge to avoid hit the lower die.
The back gauge is supported by straight-line guide and ball bearing lead screw, it composes by a beam from one side of machine to another side, and the guide of back gauge equipped on the two sides of machine body, behind has free moving working space, X to moves the part by the DNC control, the back gauge is driving by servo motor.
7.Hydraulic parts
7.1 Hydraulic pressure oil box
The hydraulic pressure oil box welded inside of the machine body, the inhaler equipped on it, and the motor, oil pump, high pressure valve, control valve and electron system are equipped outside, the filtrating core and valve pedestal are equipped on the peak, discharging oil screw equipped on the bottom of oil box.
7.2 Electric motor
3-phase four-grade motor
7.3 Oil pump
High pressure gear pump and main motor connected by flexibility joining shaft.
7.4 The inhaler
The grade of filtration is 10μm, and max pressure is 400bar, when the filter was jammed or change the oil, the filter must be instead.
7.5 Synchro servo valve
The servo valve is equipped on the top of oil cylinder; its flux is controlled by DNC numerical control system and servo amplifier, then control the slider block speed in the whole travel range, the position and manner it can control as follows:
Moving quickly
Bending speed
Lower dead spot
Return travel
Upper dead spot
7.6 Fill in valve
It’s on the top of oil cylinder, when the slider moving quickly, the oil in the oil box through the fill in valve flow in the oil cylinder, it’s closed when bending.
7.7 Pressure valve
The pressure valve is on the servo valve, back pressure when adjustable return travels.
8.Safeguard
The over travel protection controlled by DNC, the DNC check the time and pressure oil way of over travel when start. This is also called oil pressure leaking checking.
9.NC system parameters
9.1
Note: 1st, before the manufacturer orders all machine tool parameter has all established, these parameters can guarantee the operation security.
2nd, the machine tool parameter change, only then to carry on after obtained the manufacturer notice
3rd, when the 2nd request cannot obtain observes, can cause the machine tool parameter change, creates the equipment accident.
9.2 The selection of lower die
F: The requiring bending force (KN/m) of per meter when the material tensile strength is 400 N/mm.
If the material tensile strength is 800N/mm, the requiring bending force (KN/m) of per meter doubles.
S: Plate thickness (mm)
B: Minimum bending width (mm)
V: The width of lower die opening (mm)
R: The bending half diameter (mm)
V width of V lower die must determinates according to the material thickness S and the general formula is:
S<3mm V=(6~8) ×S
S>3mm V=(8~12) ×S
At the same time, min bending width and bending angle are changed, only this, can determinate the limit of lower die overall dimension scientificly.
Learn more about our products, please visit and subscribe to our Youtube channel