When considering the capabilities of a 3000W fiber laser, one of the most critical questions is: how thick can 3000W fiber laser cut? The answer to this question depends on various factors, including the type of material, the quality of the laser beam, and the specific cutting conditions. Normally, 3000W fiber laser cutting machine the maximum thickness of carbon steel is 20mm; The maximum thickness of stainless steel is 10mm; The maximum thickness of aluminum plate is 8mm; The maximum thickness of copper plate is 8mm. In this article, we will delve into these aspects to provide a comprehensive understanding of the cutting thickness capabilities of a 3000W fiber laser.
Understanding Cutting Capability of Fiber Lasers
Evolution of Metal Fabrication: From Plasma to Fiber Laser Cutting
In the early stages of automated metal fabrication, business owners typically opted for either a primary CNC plasma table or a waterjet cutting machine for rough cutting thick metal, alongside a fine CNC plasma cutter for precise cutting of thin metal. However, with increasing emphasis on manufacturing safety and environmental protection, YAG and CO2 Laser Cutting Machines emerged in the market, elevating metal cutting quality to new standards. Additionally, lasers offered advantages in terms of eco-friendliness and safety compared to plasma and waterjet methods, as they required no consumables.
Despite their benefits, both YAG and carbon dioxide lasers had limitations, including high investment costs, restricted cutting thickness, and sometimes slower speeds compared to plasma cutting. However, a breakthrough occurred with the introduction of the fiber laser metal cutting system. This innovation revolutionized the industry, offering unparalleled levels of precision, quality, speed, and versatility.
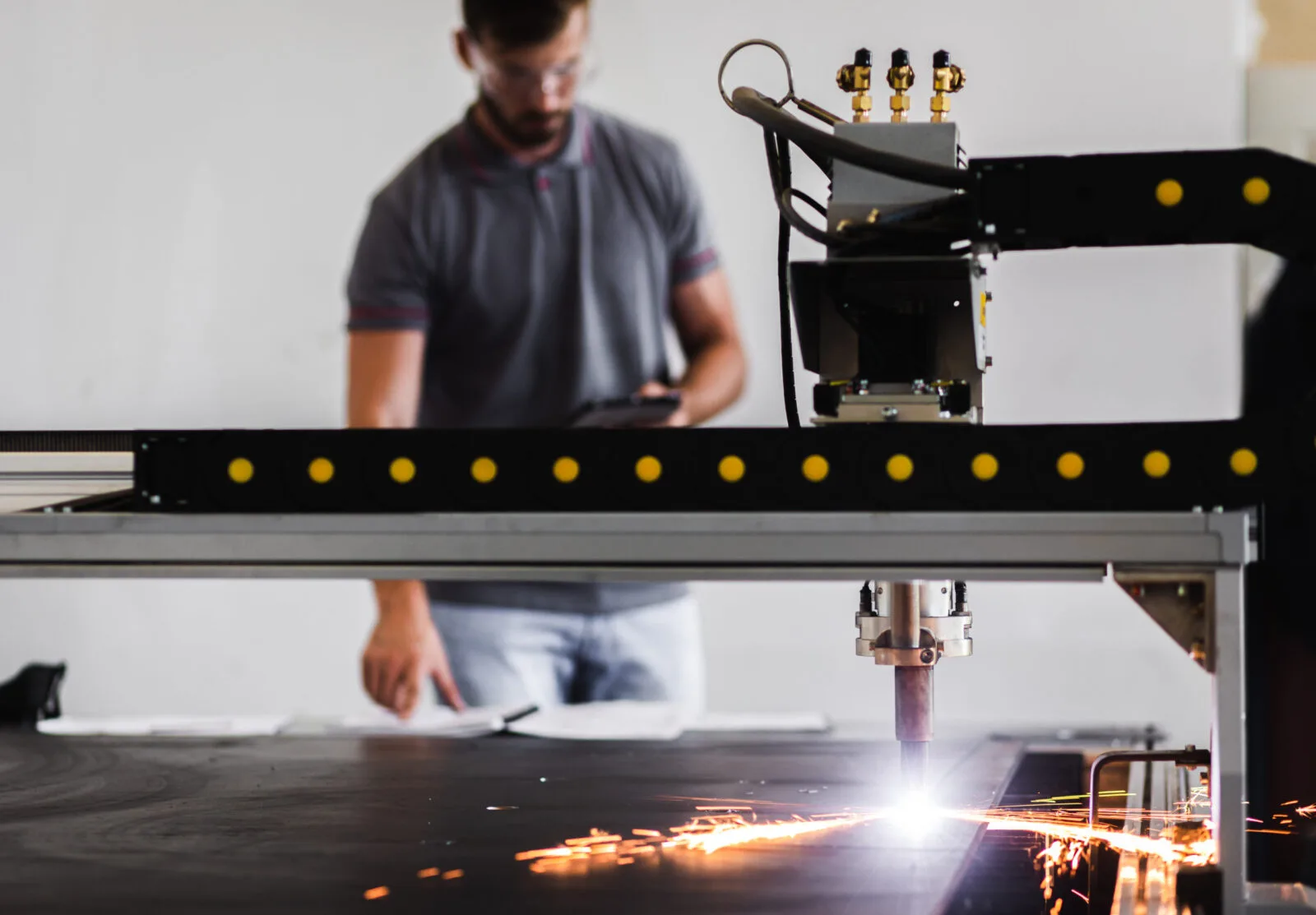
Cutting Advantages of Fiber Laser Cutter
The fiber laser cutter represents a cutting-edge solution for high-precision metal fabrication, utilizing a CNC controller to guide the laser head in accordance with the designated layout file. This technology is highly versatile, catering to the needs of both small businesses and large-scale industrial manufacturing operations.
Capable of cutting a wide range of materials, from 1mm stainless steel to over 100mm carbon steel, fiber lasers excel even with highly reflective metals like brass, copper, aluminum, gold, and silver. This versatility is enhanced by the option to use various working gases such as air, nitrogen, and oxygen, ensuring optimal cutting performance across different materials and thicknesses.
Whether dealing with sheet metal, tubes, or specialized profiles, fiber laser machines deliver precise and clean cuts, allowing for the creation of smooth contours and intricate shapes with ease. This makes them indispensable tools in modern metal fabrication processes, where efficiency, accuracy, and quality are paramount.
What Factors Affect Cutting Thickness of Fiber Lasers
Laser Power
For continuous wave output lasers, both the magnitude of laser power and the quality of the model significantly influence cutting outcomes. Laser power directly determines the thickness of the steel plate that can be cut, with higher power enabling cutting of thicker materials. Additionally, power level impacts workpiece size accuracy, cutting width, and surface roughness.
While it's common to set maximum power for increased cutting speeds or thicker materials, it's not always the optimal choice. Laser beam pattern, representing energy distribution across the cross-section, plays a crucial role. Increasing laser power can alter the laser mode, with the highest power density and cut quality often occurring below maximum power.
Insufficient laser power may result in inadequate material heating, especially near the lower edge, leading to incomplete slag removal due to insufficient airflow pressure. Conversely, excessive laser power can lead to excessive heat input, causing a larger melting range than the airflow can handle, resulting in residual molten metal on the sheet and excessive combustion.
It's crucial to carefully consider laser power according to specific cutting conditions to achieve optimal results. Finding the right balance ensures efficient material processing and high-quality cuts while avoiding issues such as incomplete slag removal or excessive combustion.
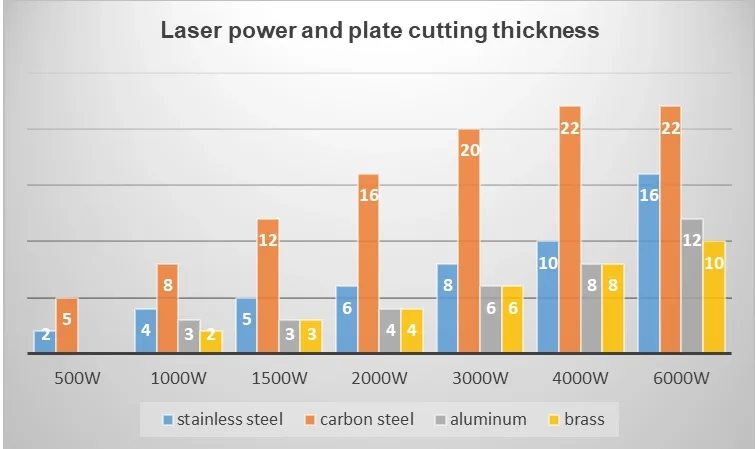
Cutting Speed
Cutting speed plays a pivotal role in determining cutting quality, with its impact heavily influenced by material density and thickness. Generally, when other parameters remain constant, cutting speed exhibits an inverse relationship with material density and thickness. Optimal cutting speed results in a smooth cut surface without any dross formation on the lower part.
If the cutting speed is too fast, the material may not be fully cut through, leading to sparks, slag formation on the lower part, and potential lens damage due to excessive heat buildup. Conversely, excessively slow cutting speed can cause over-melting of the material, widening of the slit, and even workpiece overheating.
Therefore, striking the right balance in cutting speed is crucial. It ensures efficient material processing while maintaining high-quality cuts, minimizing issues such as incomplete cuts, slag formation, or material overheating. Adjusting cutting speed according to material characteristics and desired cutting outcomes is essential for achieving optimal results in laser cutting operations.
- Laser Cutting Thickness & Speed Chart
Metal Type | Maximum Cutting Thickness (mm) | Recommended Cutting Speed (mm/s) |
Mild Steel | 20 | 600-900 |
Stainless Steel | 10 | 300-600 |
Aluminum | 8 | 1000-1500 |
Copper | 3 | 600-900 |
Brass | 4 | 600-900 |
Titanium | 4 | 400-600 |
Nickel | 3 | 400-600 |
Zinc | 3 | 400-600 |
Beam Mode & Quality
The quality of the laser beam affects its focusability and intensity. A high-quality beam can maintain its focus over longer distances, enabling efficient cutting of thicker materials.
And different beam modes (such as Gaussian or TEMoo) can affect how the laser energy is distributed and absorbed by the material. Some modes are more suitable for cutting thicker materials due to their ability to deliver higher power densities.
Assist Gas
Material cutting requires the use of an assist gas, which is usually launched coaxially with the laser beam to protect the lens from contamination and to blow away slag at the bottom of the cutting zone. When the auxiliary gas can generate enough pressure, the cutting is completed and the slag is transparent. Both the pressure and type of gas affect the roughness of the cut section and the generation of slag.
Material Type
The composition and properties of the material being cut influence the cutting process. Materials with higher thermal conductivity or reflective properties may require higher laser power or specialized techniques to achieve desired cutting thicknesses.
The output power of fiber laser cutting machines typically ranges from 500W to 1000W for standard models, while higher power versions exceed 2000W. Machines with power below 1000W are ideal for cutting carbon steel up to 14mm thick and stainless steel up to 6mm thick. Within these thickness ranges, cutting quality is excellent, and cutting speeds are fast, ensuring efficient operation and cost-effectiveness.
However, when cutting materials exceed the recommended thickness, cutting speed decreases, leading to lower cutting quality. Thicker materials may become difficult or impossible to cut. Conversely, for materials thinner than the recommended thickness, such as 1mm stainless steel, cutting quality remains exceptional, often eliminating the need for additional post-processing.
Maintaining material within the recommended thickness range ensures optimal cutting efficiency and cost-effectiveness, maximizing the benefits of laser cutting technology.
How Thick Can 3000W Fiber Laser Cut
When you choose 3000w laser power to cut the board, it is recommended to cut the stainless steel plate with a maximum cutting thickness of 8mm and a cutting speed of 1.2 m/min. The maximum thickness of the cutting carbon steel plate is 20mm, and the cutting speed will be 0.55-0.65 m/min. The maximum thickness of the cutting aluminumalloy plate can be cut 6mm with 3000w, and the cutting speed is 2m/min. When cutting copper plates, the maximum plate thickness for stable cutting is also 6mm, and the cutting speed is 1.3 m/min.
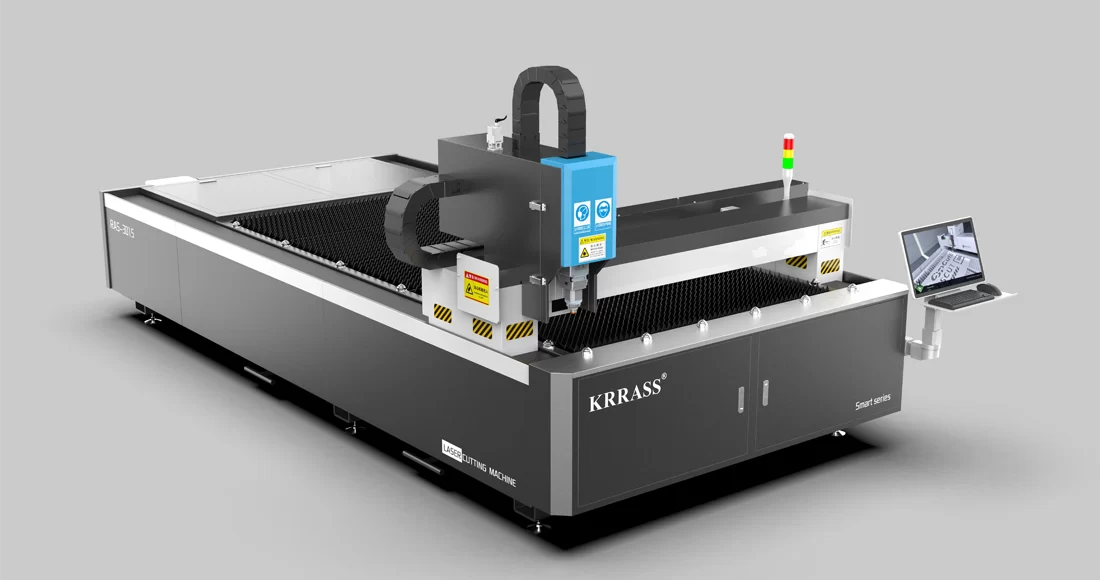
For more about 3000W fiber laser cutting machine parameters infomation, you can cilck here to find.
Pros of 3KW Laser Wattage
- Precision – A 3000W/3kW laser is capable of delivering high levels of precision and accuracy, making it a good fit for applications that require fine details or intricate designs.
- Versatility – A 3000W/3kW laser can be used on many materials, from mild steel to aluminum to copper. This machine is versatile for businesses that work with different materials and can be used in multiple ways.
Cons of 3KW Laser Wattage
- Slower Laser Cutting Speed – A 3000W/3kW laser machine may have a slower cutting speed than higher-wattage lasers. This can result in longer processing times and may not be ideal for businesses that need to work with high volumes of material.
- Limited Thickness Capacity – A 3000W/3kW laser may not be able to cut through thicker materials as quickly or efficiently as higher-wattage lasers. This factor may limit the types of projects that a business can take on.
Relationship Between Cutting Thickness and Speed
Impact of Thickness on Cutting Speed
The relationship between a laser cutting machine’s cutting speed and material thickness is tightly interconnected. Thicker metals demand more energy, time, and cutting resources to achieve the desired results. Slower cutting speeds provide the laser cutter with additional power and more penetration time, essential for cutting through thick materials effectively.
Balancing Cutting Quality and Efficiency
Achieving the perfect balance between efficiency and value requires careful adjustment of cutting speed and material thickness. For thicker materials, slower cutting speeds are necessary to ensure clean cuts and sufficient penetration. However, slower speeds increase production costs and time, impacting service delivery. Conversely, faster cutting speeds can lead to distortions or errors, compromising cut quality.
Required Cutting Parameters for Various Metals and Thicknesses
Different materials and thicknesses require specific cutting parameters, including power, assist gas setup, speed, and material properties. Adhering to a cutting guideline is crucial to achieve optimal results for various metals and their corresponding thicknesses. This ensures that the laser cutter operates under the ideal conditions, balancing efficiency, cost, and cutting quality.
- Laser Cutting Thickness & Speed Chart
Metal Type | Maximum Cutting Thickness (mm) | Recommended Cutting Speed (mm/s) |
Mild Steel | 20 | 600-900 |
Stainless Steel | 10 | 300-600 |
Aluminum | 8 | 1000-1500 |
Copper | 3 | 600-900 |
Brass | 4 | 600-900 |
Titanium | 4 | 400-600 |
Nickel | 3 | 400-600 |
Zinc | 3 | 400-600 |
By fine-tuning these parameters and maintaining a balance between speed and thickness, manufacturers can optimize their laser cutting processes to deliver high-quality results efficiently.
How to Balance Power, Speed, and Material Thickness in Laser Cutting
1. Understand Material Properties
- Thickness: Thicker materials require more power and slower speeds to ensure a clean cut.
- Type: Different metals have varying thermal properties and melting points, affecting how they respond to laser cutting.
2. Adjust Power Settings
- Higher Power for Thicker Materials: Increase the laser power to cut through thicker materials efficiently.
- Lower Power for Thinner Materials: Use lower power settings for thinner materials to avoid burning or excessive melting.
3. Optimize Cutting Speed
- Slower Speed for Thicker Materials: Reduce the cutting speed for thicker materials to allow the laser enough time to penetrate and cut cleanly.
- Faster Speed for Thinner Materials: Increase the speed for thinner materials to maintain efficiency without sacrificing quality.
4. Fine-Tune Assist Gas Parameters
- Type of Gas: Choose the appropriate assist gas (e.g., oxygen, nitrogen, air) based on the material being cut. Each gas affects the cutting process differently.
- Gas Pressure: Adjust the gas pressure to optimize the cutting edge quality and remove molten material effectively.
5. Monitor Cutting Quality
- Visual Inspection: Regularly inspect the cut quality. Look for signs of excessive slag, burn marks, or incomplete cuts.
- Adjust Parameters: If the quality is not satisfactory, tweak the power, speed, and gas settings accordingly.
6. Use Cutting Guidelines
- Manufacturer Recommendations: Follow guidelines provided by the laser cutter manufacturer for different materials and thicknesses.
- Empirical Data: Use data from previous cuts to inform parameter settings for similar materials and thicknesses.
7. Conduct Test Cuts
- Small Test Pieces: Perform test cuts on small pieces of the material to fine-tune settings before cutting larger sections.
- Iterative Adjustments: Make incremental adjustments to parameters and evaluate the results until the desired quality is achieved.
Example: Balancing Parameters for 10mm Carbon Steel
- Set Power: Use a high power setting (e.g., 1500W) to ensure adequate penetration.
- Adjust Speed: Set a slower speed (e.g., 0.5 m/min) to allow the laser to cut through the thickness effectively.
- Assist Gas: Use oxygen at an appropriate pressure to enhance the cutting process and achieve a clean edge.
- Monitor and Adjust: Inspect the cut and make adjustments to power, speed, or gas pressure if necessary to improve quality.
By understanding and balancing these factors, you can optimize the laser cutting process to achieve high-quality cuts efficiently across a range of materials and thicknesses.
Tips For Choosing Optimal Power Level For Laser Cutting
There are some considerations for you to select the right laser cutting power.
Material Considerations
- Acrylic:
- An 80-100W CO2 laser cutter is ideal for cutting acrylic.
- CO2 lasers offer better performance than fiber lasers for non-metal cutting.
- This power range ensures smooth, elegant edges for acrylic.
- Wood:
- MDF and plywood are common wood types for laser cutting.
- Use a CO2 laser with a lower power level compared to cutting acrylic.
- High energy levels can damage the wood's edge, resulting in unsatisfactory cuts.
- Metal:
- Different metals require different power levels for cutting.
- Professional laser cutting of metals like carbon steel, mild steel, and stainless steel typically requires over 100W laser power.
- For thick metal cutting, consider high-power fiber laser machines like 1000W or 4000W models for precise and efficient cuts.
Thickness Considerations
- Thicker materials require higher power levels to achieve the desired cutting depth.
- The thickness of the material influences the required power level.
- Balancing power, speed, and material thickness is essential for optimal results in laser cutting.
Summary of Recommendations
- Acrylic Cutting:
- Power Range: 80-100W CO2 laser cutter.
- Ensures smooth and elegant cut edges.
- Wood Cutting (MDF/Plywood):
- Lower power CO2 laser compared to acrylic cutting.
- Prevents damage to wood edges.
- Metal Cutting:
- Over 100W laser power for professional metal cutting.
- Consider high-power fiber lasers (e.g., 1000W or 4000W) for thick metal cutting.
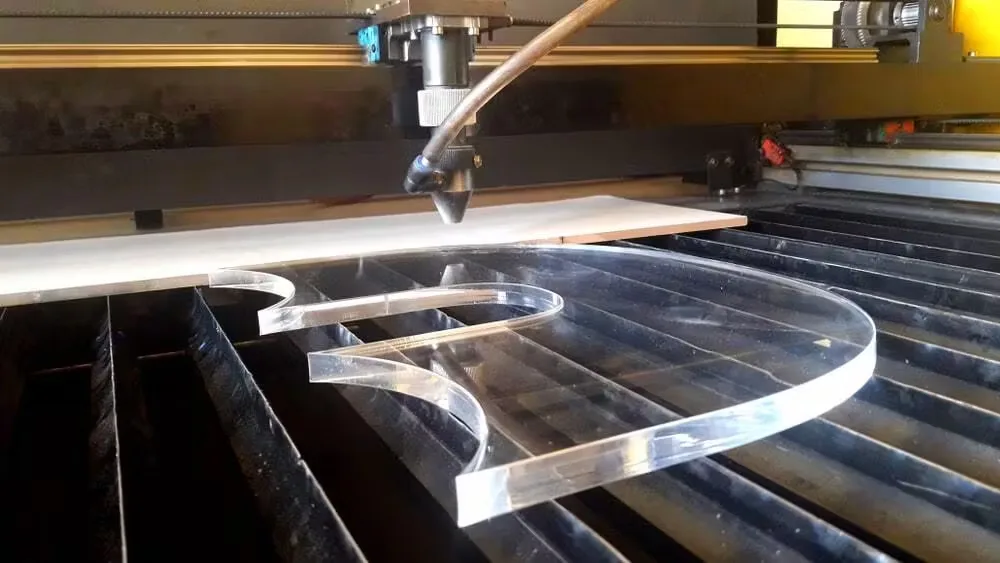
Thickness Guidelines
- Thicker materials require higher power levels to achieve desired cutting depth.
- Consider material thickness when selecting laser cutting power for optimal results.
- Balance power, speed, and material thickness for efficient and effective laser cutting.
By understanding these factors and considering the specific requirements of your materials, you can select the right laser cutting power to achieve high-quality results in your cutting applications.
Max. Cutting Thickness Reference List
Material Type | Laser Power (W) | Maximum Cutting Thickness (mm) |
Non-Metal | ||
Acrylic | 80-100 | Up to 20 |
Wood (MDF/Plywood) | 40-80 | Up to 12 |
Metal | ||
Carbon Steel | 100-300 | Up to 10 |
Stainless Steel | 100-300 | Up to 8 |
Aluminum | 100-300 | Up to 6 |
Carbon Steel | 500-1000 | Up to 20 |
Stainless Steel | 500-1000 | Up to 15 |
Aluminum | 500-1000 | Up to 12 |
Carbon Steel | 1000-4000 | Up to 30 |
Stainless Steel | 1000-4000 | Up to 25 |
Aluminum | 1000-4000 | Up to 20 |
This table provides an estimate of the maximum cutting thickness achievable with different laser powers for each material type. Actual cutting capabilities may vary depending on the specific machine, material properties, and other factors.
Conclusion
In conclusion, the cutting capabilities of a 3000W fiber laser are influenced by various factors such as material type, laser beam quality, and cutting conditions. While it can effectively cut through a range of materials with impressive precision and speed, there are limitations to consider. Understanding fiber lasers capabilities allows manufacturers and operators to optimize their laser cutting processes for efficient and precise results. As technology continues to advance, we can expect further enhancements in fiber laser cutting capabilities, opening up new possibilities for diverse industrial applications.