In the ever-evolving world of metal fabrication, the advent of automatic panel bending machines has marked a significant leap forward in technology and efficiency. These sophisticated machines offer unparalleled precision, speed, and versatility, making them an indispensable asset for modern manufacturing facilities. By automating the bending process, they not only reduce the need for manual labor but also minimize errors and enhance productivity. This guide delves into the key features and benefits of automatic panel bending machines, providing valuable insights for businesses looking to stay ahead in the competitive landscape of metal fabrication.
Introduction
Automatic Panel Bending Machines in Metal Fabrication
The evolution of metal fabrication has seen numerous advancements over the years, but few have been as transformative as the introduction of automatic panel bending machines. From the early days of manual bending to the advent of hydraulic and CNC machines, the industry has continually sought ways to improve precision, efficiency, and productivity. Automatic panel bending machines represent the pinnacle of these efforts, integrating cutting-edge technology to deliver unparalleled performance. These machines have revolutionized the metal fabrication landscape, offering manufacturers the ability to produce complex, high-quality components with unprecedented speed and accuracy.
Importance of Understanding Features and Benefits
Understanding the features and benefits of automatic panel bending machines is crucial for modern manufacturing. As the demand for intricate and precise metal parts grows, manufacturers must leverage the capabilities of these advanced machines to stay competitive. By exploring their key features and benefits, businesses can make informed decisions about incorporating automatic panel bending machines into their operations, ultimately enhancing their production capabilities and maintaining a competitive edge in the market.
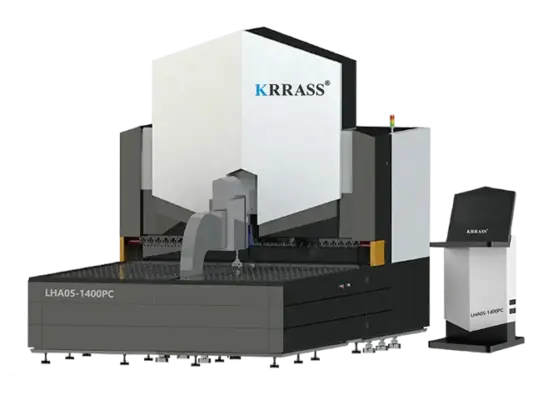
What is an Automatic Panel Bending Machine?
Definition and Basic Functionality
An automatic panel bending machine is a highly advanced piece of equipment designed to automate the process of bending sheet metal into specific shapes and forms. These machines utilize sophisticated technology, including computer numerical control (CNC), to precisely control the bending operations.
The basic functionality involves feeding a sheet of metal into the machine, which then uses a series of programmed movements and forces to bend the metal at predetermined angles and curves. This process is controlled by software that allows for high precision and repeatability, making it ideal for producing complex and consistent metal parts.
Comparison with Traditional Bending Methods
Traditional bending methods, such as manual bending and press braking, have long been the backbone of metal fabrication. These methods often involve the use of simple tools or mechanical presses where an operator must position the metal sheet and manually guide the bending process. While effective for simple tasks, these traditional methods come with several limitations that can impact productivity, cost, and quality.
Precision and Accuracy:
Manual bending methods are inherently prone to human error. Inconsistencies in pressure application and alignment can lead to variations in the final product. Studies show that manual bending can result in an error margin of up to 1-2 mm, which is significant in high-precision industries like aerospace and automotive manufacturing. In contrast, automatic panel bending machines utilize CNC technology, which ensures precision within micrometers. The use of advanced sensors and control systems allows these machines to consistently produce high-quality bends, significantly reducing the rate of defective parts.
Speed and Efficiency:
Traditional bending is labor-intensive and time-consuming, with each bend requiring manual setup and adjustment. This inefficiency can lead to extended production times, especially for large batches. According to industry reports, manual bending can be up to 50% slower compared to automated processes. Automatic panel bending machines, on the other hand, streamline the entire process by automating the setup and execution of bends. This automation can reduce cycle times by up to 70%, drastically improving throughput and allowing manufacturers to meet tight deadlines.
Complexity of Shapes:
Manual bending is often limited in its ability to produce complex and intricate shapes due to the skill and effort required to execute precise bends. Automatic panel bending machines excel in this area, capable of handling a wide range of shapes and sizes with ease. Their programmable nature allows for the creation of complex geometries that would be challenging or impossible to achieve manually. This capability is particularly valuable in industries requiring intricate designs and tight tolerances.
Labor Costs:
Traditional bending methods rely heavily on skilled labor, which can be both costly and difficult to source. Skilled operators are essential to ensure quality and precision, but their availability can be limited. The U.S. Bureau of Labor Statistics reports that the median wage for metal fabricators is approximately $40,000 annually, and this cost can add up quickly in large-scale operations. Automatic panel bending machines reduce the dependence on skilled labor, as the automation handles the precision and execution of the bends. This shift can lead to labor cost savings of up to 30%, making the investment in automation financially beneficial in the long run.
Safety:
Manual bending involves direct interaction with heavy machinery, posing significant safety risks to operators. Common injuries include cuts, bruises, and more severe incidents such as crushed fingers or hands. The Occupational Safety and Health Administration (OSHA) notes that manual metal forming tasks are among the higher risk activities in manufacturing. Automatic panel bending machines enhance safety by minimizing human intervention in the bending process. Advanced safety features such as light curtains, emergency stop buttons, and enclosed workspaces help protect operators from potential hazards, creating a safer working environment.
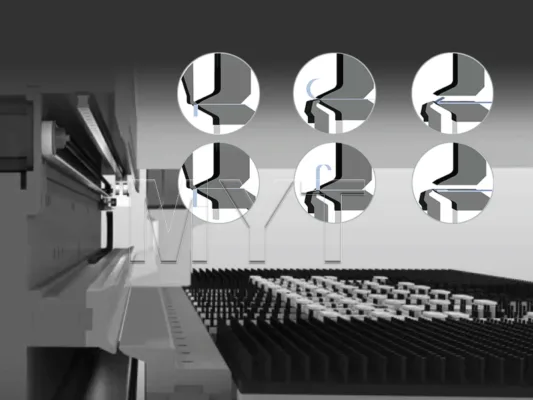
Main Components of Automatic Panel Bender
Upper and Lower Blades: These components move vertically to exert force on the sheet metal, initiating the bending process with accuracy and consistency.
Automatic Blankholder: Ensures the secure clamping of the workpiece during bending, maintaining precise positioning and stability throughout the cycle.
Counterblade: Collaborates with the upper and lower blades to firmly grip and bend the sheet metal, ensuring uniform and accurate bending results.
Manipulator: Automates the handling, gripping, and rotation of the sheet metal throughout the bending cycle, minimizing the need for manual intervention and enhancing operational efficiency.
Control System: Utilizes advanced CNC or proprietary control systems to orchestrate the movements of blades and the blankholder, ensuring meticulous control over bending angles and maintaining repeatability.
Automatic Tool Changer: Facilitates swift tool changes to accommodate varying bending angles and part sizes seamlessly, optimizing production flexibility without the need for manual re-tooling.
Human-Machine Interface (HMI): Provides operators with an intuitive interface to monitor and control the bending process, equipped with user-friendly software for enhanced operational oversight.

Types of Automatic Panel Benders
Servo-Electric Panel Bending Machines
Servo-electric panel bending machines utilize electric servo motors to drive the bending process, offering high precision, energy efficiency, and quieter operation compared to hydraulic counterparts. These machines provide precise control over bending angles and speeds, facilitate rapid tool changes, and offer programmable settings. They are particularly suited for bending thin to medium-thickness materials, making them ideal for industries like electronics, aerospace, and automotive where precision and repeatability are crucial. Their capabilities support applications that demand high accuracy in sheet metal fabrication processes.
Hydraulic Panel Bending Machines
Hydraulic panel bending machines utilize hydraulic systems to exert force for bending metal sheets, renowned for their robustness, power, and capability to handle thicker materials. These machines offer high bending force capabilities, making them suitable for bending thick and heavy materials. They often incorporate programmable controls, multiple bending axes, and are adept at handling complex shapes. Commonly employed in heavy industries like shipbuilding, construction, and metal fabrication, they excel in applications requiring substantial bending force and capacity.
Hybrid Panel Bending Machines
Hybrid panel bending machines merge servo-electric and hydraulic technologies to enhance performance and flexibility. These machines leverage servo-electric drives for precise bending and hydraulic systems for high-force operations, achieving a balance between accuracy, power, and versatility. They are well-suited for diverse applications across industries that demand flexible material handling and bending capabilities, accommodating varying production needs efficiently.
CNC-Controlled Panel Bending Machines
CNC-controlled panel bending machines employ computer numerical control (CNC) technology to automate bending processes, providing precise control over bending angles, sequences, and tool movements. These machines, available in servo-electric, hydraulic, or hybrid configurations based on manufacturer and application needs, are highly programmable. They excel at managing intricate bending operations with minimal manual intervention. Widely adopted across industries including automotive, HVAC, furniture manufacturing, and electronics, they are instrumental in producing accurate, customized sheet metal components efficiently.
Fully Automatic Panel Bending Cells
Fully automatic panel bending cells seamlessly integrate panel bending machines with advanced automation features such as robotic loading/unloading, automated material handling systems, and in-line quality control mechanisms. These systems are meticulously designed for uninterrupted, unmanned operation, effectively maximizing productivity while minimizing labor costs. They typically incorporate integrated CAD/CAM software to streamline workflow management and optimize production processes. Ideal for high-volume manufacturing environments, these solutions ensure efficiency, consistency, and operational continuity, catering to industries where stringent quality standards and rapid production turnaround times are critical.
Adaptive Panel Bending Machines
Adaptive panel bending machines integrate advanced technologies like adaptive bending systems, laser measurement, and AI-driven algorithms to optimize bending processes in real-time. These machines dynamically adjust bending parameters based on material properties, sheet conditions, and production requirements, enhancing flexibility, productivity, and accuracy. They are particularly suitable for industries needing rapid setup, the handling of complex geometries, and adaptive manufacturing processes, ensuring efficient and precise sheet metal fabrication.
Key Features of Automatic Panel Bending Machines
Precision and Accuracy
Automatic panel bending machines are equipped with advanced control systems and sensors that ensure exceptional precision and accuracy in every bend. These systems use real-time feedback to adjust the bending process, correcting any deviations instantly. For instance, laser-based measuring devices and high-resolution encoders can detect and correct positioning errors within micrometers, resulting in consistently high-quality bends. This precision is crucial for industries that require tight tolerances, such as aerospace, automotive, and electronics manufacturing.
Speed and Efficiency
High-speed operations are a hallmark of automatic panel bending machines. By automating the setup and execution of bends, these machines can significantly reduce cycle times compared to manual methods. Like Krrass automatic bending machines can operate up to 70% faster than traditional press brakes, allowing manufacturers to increase their production throughput. This efficiency is achieved through rapid tool changes, optimized bending sequences, and simultaneous operations, all controlled by sophisticated software that maximizes productivity.
Versatility
One of the standout features of automatic panel bending machines is their ability to handle a wide variety of materials and complex shapes. These machines are designed to work with different types of metals, including steel, aluminum, and copper, as well as varying thicknesses. The programmable nature of these machines allows for the creation of intricate geometries and multi-step bending processes that would be difficult or impossible to achieve manually. This versatility enables manufacturers to produce a diverse range of products with high precision.
Automation and Integration
Automatic panel bending machines are designed for seamless integration with CAD/CAM systems and Industry 4.0 technologies. This integration allows for direct data transfer from design software to the bending machine, reducing the need for manual programming and minimizing the risk of errors. Industry 4.0 capabilities, such as IoT connectivity and smart manufacturing solutions, enable real-time monitoring, predictive maintenance, and data-driven decision-making. These features enhance overall operational efficiency and allow manufacturers to adapt quickly to changing production demands.
Safety Features
Enhanced safety mechanisms are a critical feature of automatic panel bending machines, designed to protect operators and equipment. These machines are equipped with advanced safety features such as light curtains, safety interlocks, and emergency stop buttons. Light curtains create an invisible barrier around the machine's working area, stopping operations if the barrier is breached, thus preventing accidental injuries. Safety interlocks ensure that the machine cannot operate unless all safety conditions are met. Additionally, enclosed workspaces and automated handling systems further reduce the risk of operator injury by minimizing direct contact with moving parts.
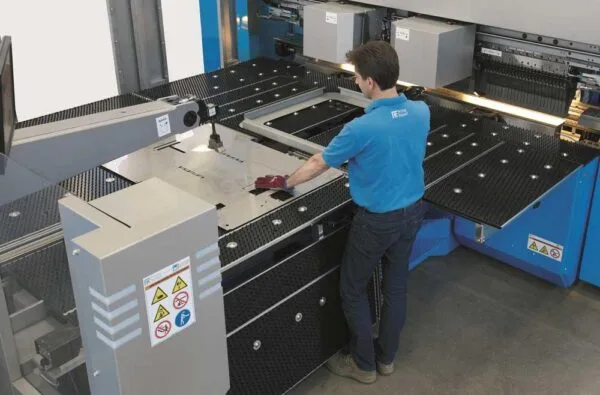
Benefits of Using Automatic Panel Bending Machines
Increased Productivity
Automatic panel bending machines significantly enhance productivity by automating the bending process. With the ability to perform high-speed operations and reduce cycle times, these machines can produce more parts in a shorter amount of time compared to manual methods. Studies have shown that automatic bending machines can increase production throughput by up to 70%, allowing manufacturers to meet high-demand schedules and improve overall efficiency.
Cost Savings
The automation of bending processes reduces the need for manual labor, which in turn lowers labor costs. Skilled operators, while essential, can be expensive and difficult to find. By minimizing the reliance on human intervention, automatic panel bending machines can cut labor costs by up to 30%. Additionally, the precision and accuracy of these machines reduce material waste, further contributing to cost savings. The initial investment in an automatic bending machine often pays off quickly due to these operational efficiencies.
Improved Quality
Consistency and precision are critical in metal fabrication, and automatic panel bending machines excel in these areas. Advanced control systems and sensors ensure that each bend is executed with high accuracy, minimizing errors and variations. This level of precision leads to higher-quality products, reducing the need for rework and ensuring that parts meet strict industry standards. The ability to produce complex shapes with consistent quality is particularly valuable in sectors such as aerospace and automotive manufacturing.
Flexibility
Automatic panel bending machines offer unparalleled flexibility, capable of handling various materials and complex shapes. Whether working with steel, aluminum, or copper, these machines can be programmed to perform a wide range of bending operations. This versatility allows manufacturers to adapt to different production needs and quickly switch between projects. The programmable nature of these machines enables the creation of intricate geometries and multi-step bending processes, expanding the possibilities for product design and customization.
Enhanced Workplace Safety
Safety is a paramount concern in manufacturing, and automatic panel bending machines significantly improve workplace safety. By automating the bending process, these machines minimize direct human interaction with the machinery, reducing the risk of injuries. Advanced safety features such as light curtains, safety interlocks, and emergency stop buttons are standard in these machines. These mechanisms ensure that operations cease if safety barriers are breached, protecting operators from potential hazards. Additionally, enclosed workspaces and automated handling systems further enhance safety by keeping operators away from moving parts.
In summary, the benefits of using automatic panel bending machines are manifold. They increase productivity, provide significant cost savings, improve product quality, offer flexibility in production, and enhance workplace safety. These advantages make automatic panel bending machines an essential asset for manufacturers aiming to optimize their operations and maintain a competitive edge in the industry.
Applications of Automatic Panel Bending Machines
Automotive: The automotive industry relies heavily on precise and efficient metal bending for components such as body panels, frames, brackets, and structural parts. Automatic panel bending machines ensure consistency and accuracy, which are critical for the safety and performance of vehicles.
Aerospace: In the aerospace sector, the need for high precision and complex shapes is paramount. Automatic panel bending machines are used to produce parts like fuselage panels, wing components, and support structures, meeting the stringent standards of this industry.
Electronics: The electronics industry requires intricate metal enclosures, chassis, and heat sinks. Automatic panel bending machines provide the precision needed to fabricate these detailed components, ensuring they meet the exact specifications required for proper functioning and assembly.
HVAC: Heating, ventilation, and air conditioning systems involve numerous sheet metal components, such as ducts, vents, and enclosures. Automatic panel bending machines streamline the production of these parts, improving efficiency and reducing production times.
Furniture: The production of metal furniture and fixtures, including office desks, cabinets, and shelving units, benefits from the versatility and precision of automatic panel bending machines, enabling the creation of both standard and custom designs.

How to Choose the Right Automatic Panel Bending Machine
Factors to Consider
Choosing the right automatic panel bending machine involves a comprehensive evaluation of several critical factors tailored to your specific production requirements:
Production Volume: Assess your anticipated production volume to determine the machine's capacity and speed capabilities. For high-volume production, prioritize machines that offer fast cycle times and continuous operation without compromising on quality.
Material Types and Thickness: Consider the types of materials you will primarily work with, such as steel, aluminum, or copper, along with their respective thicknesses. Ensure that the machine is equipped to handle these materials effectively and can accommodate variations in thickness as needed.
Budget Constraints: Establish a clear budget that aligns with your financial resources and expected return on investment (ROI). While automatic panel bending machines vary in price based on features and capabilities, it’s crucial to balance cost with long-term productivity gains and operational efficiency.
Precision and Accuracy Requirements: Evaluate the precision and accuracy levels required for your parts. Industries like aerospace and electronics demand tight tolerances, necessitating machines with advanced control systems, high-resolution sensors, and precise tooling capabilities.
Versatility and Flexibility: Assess the machine’s versatility in handling a wide range of shapes and bending operations. Look for features such as multiple bending axes, programmable settings, and tool-changing capabilities that enhance flexibility and adaptability to diverse production needs.
Space and Installation Considerations: Evaluate the physical space available in your facility for installing the machine. Consider the machine’s footprint, operational requirements (such as power supply and ventilation), and any additional space needed for maintenance and operator access.
Tips for Evaluating and Selecting the Best Machine
Research and Comparison: Conduct thorough research on different brands and models of automatic panel bending machines. Compare specifications, features, and customer reviews to gain insights into their performance, reliability, and suitability for your specific applications.
Consultation with Experts: Seek advice from industry experts, consultants, or equipment suppliers who can provide valuable recommendations based on their experience and knowledge of the market. They can help identify machines that best meet your technical requirements and budget constraints.
Request Demonstrations and Trials: Whenever possible, request demonstrations or trials of the machines you are considering. Hands-on testing with your materials and designs allows you to assess performance, accuracy, and ease of operation firsthand.
Evaluate After-Sales Support: Assess the manufacturer’s reputation for after-sales support, including availability of maintenance services, spare parts, and technical assistance. A reliable support network ensures minimal downtime and prompt resolution of any operational issues.
Training and Integration: Inquire about training programs offered by the manufacturer to ensure your operators are proficient in using the machine effectively. Consider compatibility with your existing CAD/CAM systems or Industry 4.0 technologies for seamless integration into your workflow.
Long-Term Considerations: Anticipate future growth and evolving market demands when selecting a machine. Choose a supplier known for innovation and product development, ensuring that your investment remains viable and adaptable to future manufacturing trends.
Automatic Panel Bending Machine Price
Entry-level Machines: Basic models with limited automation and lower capacity may start from approximately $50,000 to $100,000 USD, suitable for smaller-scale operations or specific applications.
Mid-range Machines: These machines, offering moderate automation and capacity, typically range from $100,000 to $300,000 USD. They are suitable for medium-sized enterprises looking to balance cost and performance.
High-end Machines: Advanced models with extensive automation, high precision, and large capacity can range from $300,000 USD to over $1 million USD. These machines are ideal for large-scale production facilities and industries requiring top-tier performance and reliability.
Introduction to World Renowned Manufactures
1. Trumpf
Popular Model: TruBend Series
Description: The Trumpf TruBend series offers a range of automatic panel bending machines known for their precision, efficiency, and integration capabilities.
Features: These machines feature CNC control, automatic tool changers, high-speed bending, advanced tooling options, and compatibility with CAD/CAM systems. They are designed for versatility and high-volume production.
Price Range: Approximately $200,000 to $800,000 USD, depending on configuration and model.
2. Amada
Popular Model: HG Series
Description: The Amada HG series is renowned for its reliability, precision bending, and user-friendly operation.
Features: These machines include CNC control, multi-axis backgauges, high-speed bending capabilities, adaptive bending systems, and a wide range of tooling options. They are suitable for various sheet metal applications.
Price Range: Typically priced between $150,000 to $600,000 USD, depending on specifications.
3. Salvagnini
Popular Model: P4 Series
Description: The Salvagnini P4 series represents advanced panel bending technology with a focus on flexibility and efficiency.
Features: These machines feature flexible tooling systems, automatic tool changeovers, integrated bending and shearing capabilities, modular designs, and Industry 4.0 readiness. They are known for their high productivity and precision.
Price Range: Generally ranges from $250,000 to $800,000 USD, depending on customization and automation levels.
4. Prima Power
Popular Model: eP Series
Description: The Prima Power eP series offers servo-electric panel bending technology with advanced features for complex bending tasks.
Features: These machines include servo-electric bending technology, automatic tool changing systems, adaptive bending algorithms, digital manufacturing integration, and user-friendly interfaces. They are designed for high precision and efficiency.
Price Range: Typically priced between $150,000 to $500,000 USD, depending on model and specifications.
5. Durma
Popular Model: AD-S Series
Description: The Durma AD-S series includes a range of automatic panel bending machines known for their robust construction and cost-effectiveness.
Features: These machines feature CNC control, rapid tool change capabilities, precision bending tools, and sturdy construction suitable for heavy-duty applications. They offer reliability and efficiency in sheet metal bending.
Price Range: Generally ranges from $100,000 to $300,000 USD, depending on model and customization options.
6. LVD Group
Popular Model: ToolCell Series
Description: The LVD ToolCell series combines automatic panel bending with advanced bending technologies for high-performance applications.
Features: These machines feature advanced control technology, automatic tool changing, adaptive bending systems for complex geometries, and integration capabilities with digital manufacturing solutions. They are designed for precision and versatility.
Price Range: Typically priced between $120,000 to $400,000 USD, depending on the model and features.
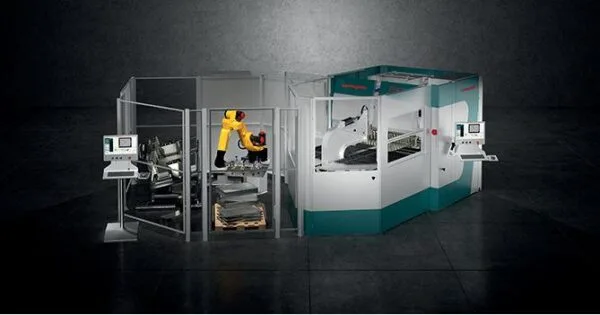
Innovations in Automatic Panel Bending Machines: What to Expect in 2024
In 2024, automatic panel bending machines will advance significantly through the integration of AI, machine learning, robotics, and IoT technologies. AI and machine learning algorithms will enable predictive maintenance and real-time optimization of bending processes based on material properties and production conditions, enhancing operational efficiency.
Robotics will further automate material handling, tool changing, and part manipulation, reducing cycle times and ensuring consistency in operations. IoT connectivity will facilitate seamless data exchange between machines, enabling remote monitoring, diagnostics, and predictive analytics for improved production planning and machine performance optimization. These innovations will collectively transform the capabilities and efficiency of automatic panel bending machines in manufacturing environments.
In Krrass Machinery, Find Your Bender Solution
At Krrass, we leverage over 20 years of expertise in manufacturing top-quality bending machines. Whether you require a versatile CNC or hydraulic press brake, or seek the efficiency of a highly automated panel bender, our dedicated team is poised to assist. We understand the nuances of each machine type and can guide you towards the ideal solution that aligns with your production needs.
In addition to bending solutions, we offer comprehensive services including laser cutting, shearing, and more. Contact us today to explore how our advanced machinery can elevate your manufacturing capabilities and drive your business growth forward.
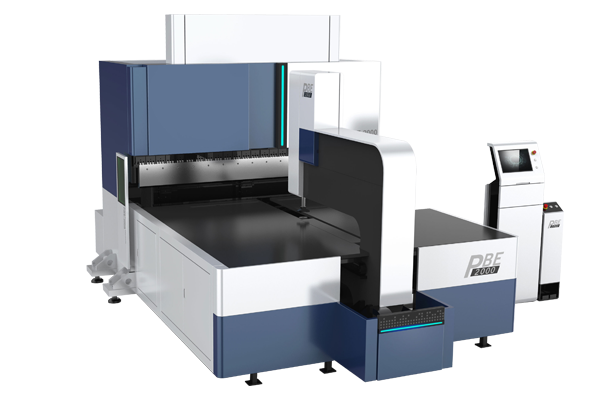