When it comes to modern metal fabrication, the panel bender machine has revolutionized the industry by offering precision, efficiency, and versatility. As manufacturers seek to improve their production lines, understanding the different features, prices, and performance of various panel bender machines becomes crucial. In this article, we will delve into the key aspects that differentiate these machines, helping you make an informed decision for your business.
What Is A Panel Bender Machine
A panel bender machine is a sophisticated tool used in metal fabrication that automates the bending of sheet metal. Unlike traditional methods that relied on manual labor, panel benders streamline the process by offering automated features for precise and efficient bending operations. These machines are designed to handle various types of sheet metal, allowing manufacturers to produce complex shapes with high accuracy and repeatability.
Sheet metal panel bender machines are smart manufacturing tools, invented by Guido Salvagnini in 1977, designed for flexible and automatic production of sheet metal panels starting from punched blanks without retooling or operator intervention.
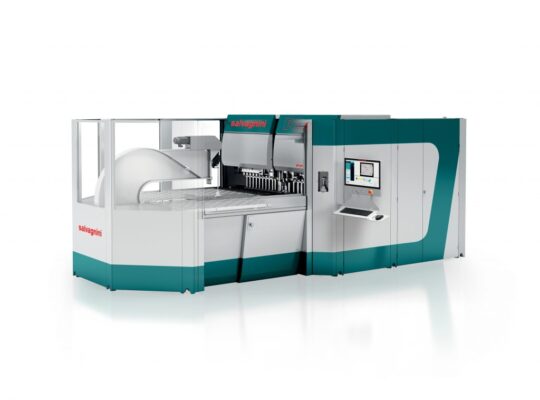
Evolution of Metal Bending: From Manual to Automated Panel Benders
The panel bender is a machine with functions similar to the press brake but is more automatic and has more advanced features. In the past, metal bending relied on manual machines. However, with continuous technological progress, sheet metal forming has entered the era of automation.
Types of Metal Bending Machines: Manual, Semi-Automatic, and Fully Automatic Bending Centers
- Manual Bending Machines: These offer simplicity and affordability but require skilled operators and are inefficient for large-scale production.
- Semi-Automatic Bending Centers: These machines blend manual and automated features, reducing the need for constant manual intervention and enhancing efficiency.
- Fully Automatic Bending Centers: Equipped with automatic tool changing and measuring systems, these machines significantly improve metal bending efficiency.
The Panel Bender: A Modern Solution
The panel bender, while similar to the traditional press brake, stands out due to its labor-saving and high-speed capabilities.
Blade Functionality: The panel bender’s blade can form flanges horizontally while the blank holder keeps the material stable. Standard bending blades can produce various radii without leaving marks, resulting in more aesthetically pleasing and clean workpieces compared to those from a press brake.
Automation and Versatility: This machine can perform fully automatic bending processes, including tool loading and unloading, feeding, measuring, bending, and outputting. It features a short bending stroke, fast feeding speed, and produces highly accurate workpieces.
(1) Advantages Over Traditional Press Brakes
Compared with the bending workpieces produced by a press brake, those from a panel bender are more aesthetically pleasing and clean. The panel bender also offers significant labor-saving and high-speed advantages, making it a superior choice for modern metal bending applications.
(2) Special Capabilities and Applications
The panel bender can use special tools for complex bending tasks, such as crimping and offset bending. However, not all workpieces are suitable for the panel bender. It is generally better for producing box-type workpieces, as it can bend the sides of an entire box at once.
(3) Integration with Robotics
Today, combining a press brake and a panel bender with a robot can achieve full automation. However, their functions are not as comprehensive as those of a robot bending center. Understanding the differences between a press brake and a panel bender is crucial for choosing the right machine for your needs. The panel bender’s highly automated features and versatility make it an essential tool in the modern sheet metal industry.
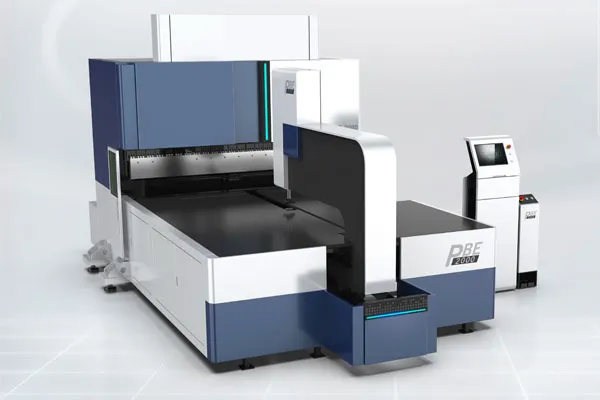
Working Mechanism of Panel Bender Machine
The panel bender revolutionizes sheet metal bending with its automated and precise operational capabilities, distinct from traditional press brakes. Here’s a detailed exploration of how the panel bender functions:
Automated and Controlled Operation
In contrast to the manual control required by press brakes, the panel bender automates much of the bending process. Operators load the sheet metal into the machine, and sophisticated software manages the positioning, bending angles, and tool adjustments.
Bending Methodology
Rather than pressing the metal into lower dies, the panel bender uses a pair of blades to securely clamp the sheet metal and bend it up and down. This method ensures that the material is bent precisely to form the desired profiles and shapes, maintaining surface integrity without marks or deformations.
Precision in Flanging and Tool Adjustment
After the workpiece is positioned, the panel bender swiftly adjusts to the optimal tool length for bending. Clamping beam tools secure the material in place, with the lower tool moving upward to create positive bends and the upper tool moving downward for negative bends. This precise control over tool movements allows for accurate forming of flanges and intricate geometries.
Clamping and Forming Process
Clamping claws descend to firmly hold the sheet metal during the bending process. The extension of the sheet metal beyond the clamping claw determines the height of the flange produced by the machine, ensuring consistency and quality in the formed components.
Versatility and Applications
Panel benders excel in handling a wide range of workpieces, including box-type structures, flat panels, and large-scale components. They are particularly effective in forming complex angles, radii, and curls by adjusting the movement of the bending tools. This versatility makes them indispensable in industries requiring high precision and efficiency in metal fabrication.
Advantages of Modern Panel Benders
1. Increased Productivity
Panel bending machines streamline the bending process, significantly boosting productivity while ensuring high-quality bends and material integrity. With CNC control, manual labor is drastically reduced, leading to higher efficiency and operational ease. For instance, advanced CNC panel benders can achieve a maximum bending speed of 0.5 seconds per bend, automating even complex shapes with consistent precision.
2. Precision and Accuracy
These machines deliver precise results, bending metal sheets into intricate shapes with remarkable accuracy. With CNC controls and precise tooling, they achieve tolerances as tight as ±0.1mm, crucial for industries like aerospace and medical equipment manufacturing. This precision minimizes material waste and ensures strong output integrity and consistent quality.
3. Versatility in Bending Operations
Panel bending machines offer unparalleled versatility, capable of handling various bending operations—from simple to highly complex shapes—across a wide spectrum of materials and thicknesses. They integrate seamlessly with other machinery and are available in different sizes with customizable settings to fit specific production needs.
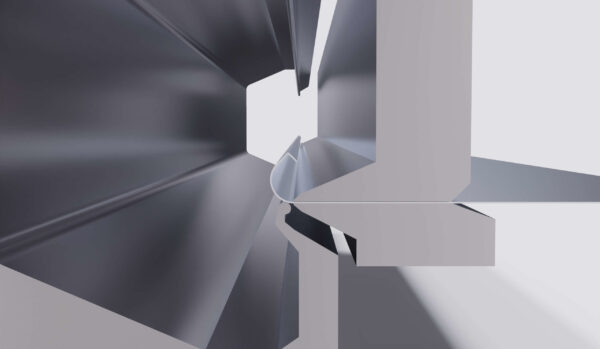
4. Reduced Setup Times
Setup times are significantly reduced with CNC panel bending machines due to quick tooling changes, automation, and user-friendly controls. Setup adjustments can be completed in minutes, allowing for swift transitions between different bending requirements and maximizing operational uptime.
5. Cost Savings
These machines contribute to cost reduction in several ways:
- Labor costs: With simplified operation and fewer operators needed per machine, labor costs are minimized. Training requirements are also reduced.
- Material waste: Precision bending reduces material wastage, saving costs on raw materials.
- Rework: Enhanced precision and efficiency lead to fewer errors and less rework, saving both time and resources.
6. Flexibility in Material Handling
Panel benders handle a wide range of materials—including aluminum, stainless steel, and various alloys—across different thicknesses with minimal adjustment. This flexibility optimizes production processes and ensures consistent quality across diverse material requirements.
7. Enhanced Safety Features
Modern panel bending machines prioritize safety with features such as automated shut-offs, light curtains, interlocks, and emergency stop buttons. These features protect operators and materials, fostering a safer work environment and reducing the risk of accidents.
8. Improved Workflow Integration
These machines seamlessly integrate into modern workflow systems and existing production lines. Compatibility with CAD/CAM software enables efficient design-to-production workflows, enhancing operational efficiency and facilitating seamless integration with other manufacturing processes.
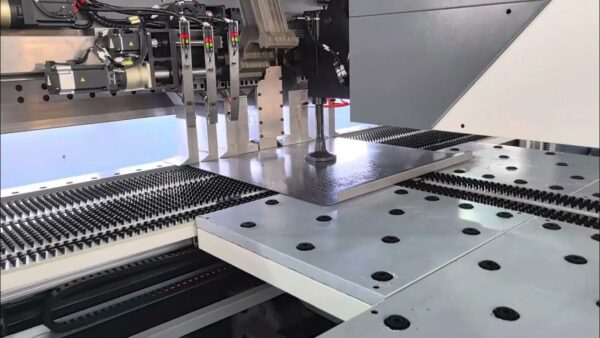
Panel Bender Machine Vs. Press Brake: How to Choose
Choosing between a panel bender machine and a press brake depends on several factors, primarily related to the specific requirements of your manufacturing operations. Here are key considerations to help you decide:
Panel Bender Machine
Machine Structure:
The panel bender comprises essential components: a robust steel body for stability and durability, a worktable that securely positions and fixes plates during bending, and a precision bending mechanism that accurately shapes plates through meticulous mechanical engineering. A sophisticated control system oversees equipment operations and parameter adjustments, enhancing user-friendliness and efficiency with intuitive interfaces and intelligent control logic. Together, these elements ensure high-performance bending capabilities for a variety of materials and thicknesses in industrial settings.
Complexity of Bends:
Panel bender machines can handle complex bends with high precision. For example, advanced models like the KRRASS BEC line can achieve bending speeds of up to 0.5 seconds per bend, suitable for automating intricate shapes and multiple bending operations in different planes.
Precision and Accuracy:
Panel benders offer precise bending capabilities with tolerances as tight as ±0.1mm. This level of accuracy is critical in industries such as aerospace and medical equipment manufacturing, where exacting standards are required to minimize material waste and ensure product quality.
Automation and Efficiency:
Automated panel bender machines significantly reduce manual labor and setup times. They can operate continuously with minimal downtime, contributing to higher productivity. Studies show that automation in panel bending can increase throughput by up to 50% compared to manual operations.
Material Handling:
Panel bender machines are versatile in handling a wide range of materials and thicknesses. They can accommodate materials from thin aluminum sheets to thicker stainless steel, often with quick changeover times between different material types and thicknesses.
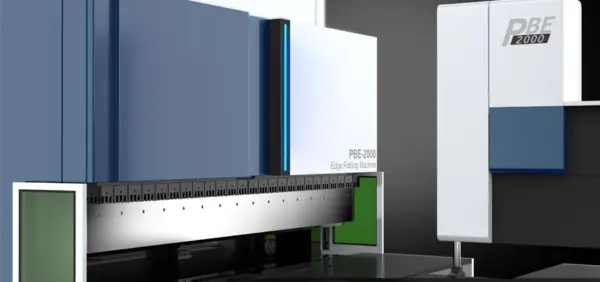
Press Brake
Machine Structure:
A press brake typically features a conventional C-type or gantry structure, consisting primarily of a machine body, worktable, bending mechanism, and backgauge device. It excels in performing angle bending operations on metal sheets with versatility and precision.
On the other hand, a panel bender is specialized for handling large panels, characterized by a larger and more intricate structure. It includes a spacious worktable, a high-precision bending mechanism, and often an automated feeding system. These components collectively enable the precise shaping of large panels, accommodating various complex bending requirements efficiently and effectively
Versatility in Bending:
Press brakes are versatile machines capable of bending various materials and thicknesses. They are commonly used in industries such as automotive and construction, where flexibility in bending operations is crucial for producing a wide range of components.
Flexibility in Applications:
Beyond bending, press brakes can perform additional operations such as shearing and punching. This versatility makes them suitable for various metal forming tasks within a single machine setup, reducing the need for multiple specialized machines.
Skill Requirements:
Operating a press brake requires basic training in machine setup and programming. Compared to panel bender machines, press brakes have a shallower learning curve, making them easier to integrate into production workflows with minimal specialized skills required.
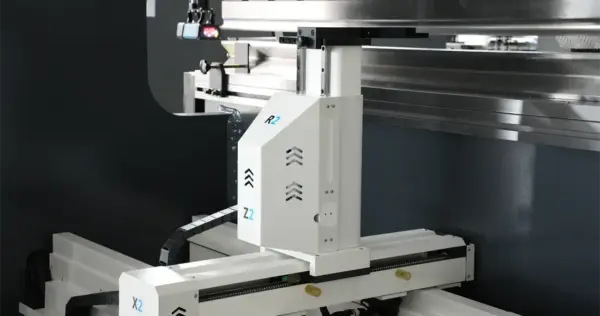
Limitation
Press Brake Machine
Operating a press brake involves significant manpower and auxiliary equipment, making it complex and labor-intensive. Specialized training is essential for operators to master correct procedures and safety protocols. Additionally, auxiliary tools like clamps and molds are crucial, adding to the operational complexity and requiring careful management of labor costs and production efficiency.
For intricate products such as electrical cabinets, press brake efficiency diminishes due to the need for frequent adjustments in bending angles and sizes. These adjustments lengthen production cycles and reduce overall efficiency. Moreover, the complexity of operations increases the risk of errors, further delaying production timelines, escalating costs, and leading to material wastage. These challenges underscore the importance of streamlined processes and skilled personnel in managing production costs and optimizing resource utilization.
Panel Bender Machine
Panel benders excel with thinner metal sheets but may struggle with thicker materials like high-strength steel, often requiring the versatility of a press brake. They are ideal for smaller components due to potential size limitations in bending length and width. In contrast, press brakes handle larger or uniquely shaped components effectively, accommodating their complexity and size requirements. Choosing between the two depends on material thickness, component size, and the intricacy of shapes needed in metal fabrication processes.
What Are Panel Bender Prices
Here are profiles of some world-famous panel bender manufacturers, along with their popular models and general price ranges:
1. Salvagnini
Company Profile: Salvagnini is an Italian manufacturer known for pioneering flexible manufacturing systems and innovative panel bending technology. Founded in 1963, Salvagnini has a global presence and is recognized for its high-quality sheet metal processing solutions.
Pros:
- Innovative Technology: Known for introducing flexible automation systems in sheet metal processing.
- High Precision: Offers precise bending solutions with advanced software integration.
- Versatility: Capable of handling a wide range of materials and complex bending tasks.
Cons:
- High Cost: Salvagnini machines are generally high-priced due to their advanced features and automation.
- Complexity: Requires specialized training and support due to the complexity of automation and software integration.
Popular Models:
- Salvagnini P2lean: Compact and efficient panel bender suitable for small to medium-sized components.
- Salvagnini P4Xe: Advanced model with automatic tool changing and robotic handling capabilities.
Price Range:
- Prices typically range from $80,000 to $300,000 or more, depending on the model and configuration.
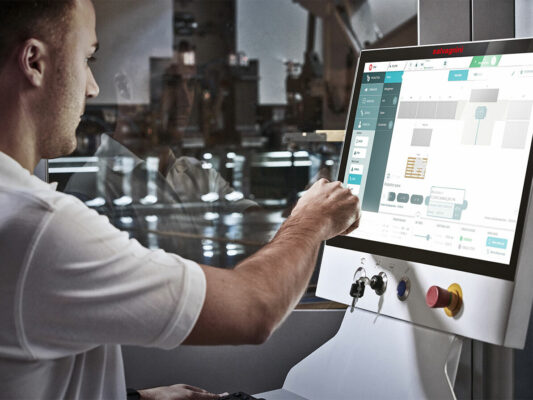
2. TRUMPF
Company Profile: TRUMPF, based in Germany, is a leading manufacturer of machine tools and laser technology for industrial applications. Founded in 1923, TRUMPF has a strong reputation for precision engineering and innovation in sheet metal processing.
Pros:
- Reliability: Known for robust and durable machine construction.
- Advanced Automation: Offers high levels of automation with intuitive control interfaces.
- Global Presence: Provides extensive customer support and service worldwide.
Cons:
- Initial Investment: Higher initial costs compared to some competitors.
- Technical Complexity: Requires skilled operators and maintenance personnel.
Popular Models:
- TRUMPF TruBend Series: Includes models like TruBend 7036 and TruBend 5085, known for their versatility and precision.
Price Range:
- Prices start from $60,000 for entry-level models and can exceed $300,000 for fully automated versions.
3. AMADA
AMADA, headquartered in Japan, is a global leader in sheet metal fabrication machinery and solutions. Founded in 1946, AMADA is known for its comprehensive range of equipment and cutting-edge technology.
Pros:
- Versatility: Offers a wide range of models suitable for various applications and industries.
- Efficiency: High-speed and accurate bending capabilities.
- Innovation: Continual advancements in machine technology and software integration.
Cons:
- Cost: Initial investment can be significant, especially for advanced models.
- Maintenance: Requires regular maintenance and support due to high operational demands.
Popular Models:
- AMADA HFE Series: Includes models like HFE 1003 and HFE 2204, known for their speed and precision.
Price Range:
- Prices typically start around $50,000 for basic models and can exceed $200,000 for high-capacity and automated versions.
4. LVD
Company Profile: LVD, headquartered in Belgium, specializes in sheet metal working technology and offers a wide range of machinery for bending, punching, and laser cutting. Founded in 1952, LVD is known for its reliable and durable equipment.
Pros:
- Robust Construction: Machines are built for durability and long-term reliability.
- Flexibility: Offers customized solutions and modular designs.
- Global Support: Extensive network for service and support worldwide.
Cons:
- Complexity: Requires skilled operators for optimal performance.
- Customization: Fully customized solutions may come at a higher cost.
Popular Models:
- LVD PPEB Series: Includes models like PPEB 80/20 and PPEB 320/40, known for their versatility and precision.
Price Range:
- Prices generally start from $40,000 and can exceed $150,000 for specialized configurations and high-capacity models.
Basic Rules to Find A Ideal Paner Bender
1. Identifying Your Specific Requirements and Budget
When choosing a panel bender machine, it's crucial to define your specific requirements upfront. This includes identifying the types of materials such as aluminum or stainless steel, along with their varying thicknesses, that you'll be bending. Additionally, determine the range of component sizes, from maximum to minimum dimensions, that the machine needs to accommodate.
2. Matching Features and Performance to Your Production Goals
Start by assessing the machine's bending length, width, and accuracy to ensure they align with your component size and precision requirements. Determine the level of automation needed based on your production volume and the complexity of bending tasks you handle. Consider the machine's software capabilities, including CAD/CAM integration, ease of programming, and simulation functionalities, which can streamline workflow and enhance productivity.
3. Tips for Evaluating and Testing Machines Before Purchase
Demonstrations and Trials: Request demonstrations and trials from manufacturers or distributors to see the machine in action.
Sample Bending: Test the machine with samples of your actual production materials to evaluate bending quality and performance.
Operational Ease: Assess the machine’s user interface, control panel layout, and ergonomic features for ease of operation and setup.
4. Importance of After-Sales Support and Training
nquire about their technical support capabilities, including the availability of spare parts and the responsiveness of service teams to ensure minimal downtime during maintenance or repairs. Evaluate the training programs provided by the manufacturer for operators and maintenance personnel to ensure they are robust and tailored to maximize machine efficiency and longevity.
For instance, KRRASS emphasizes robust technical support capabilities, ensuring prompt availability of spare parts and responsive service teams to minimize downtime.
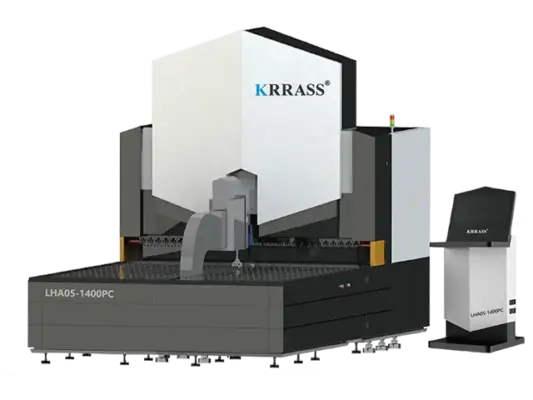