Maintaining your CNC metal brake is crucial for ensuring its longevity and efficiency. Regular maintenance not only extends the life of the machine but also enhances its performance, leading to more precise and consistent results. Whether you're a seasoned professional or new to CNC metal brakes, following a comprehensive maintenance routine can save you time and money in the long run. In this guide, we will explore essential tips and best practices to keep your CNC metal brake in top condition.
What is A CNC Sheet Metal Brake Machine
A CNC sheet metal brake machine is an advanced piece of equipment used in metalworking to bend and shape sheet metal with high precision and consistency. CNC stands for Computer Numerical Control, indicating that the machine's movements and operations are controlled by computer software, which enhances accuracy and repeatability.
Applications of CNC Sheet Metal Brake Machines:
Automotive Industry: Manufacturing car body parts, brackets, and other components.
Aerospace Industry: Producing aircraft panels, frames, and structural parts.
Construction: Fabricating metal parts for buildings, bridges, and infrastructure.
Electronics: Creating enclosures, chassis, and other components for electronic devices.
Furniture Manufacturing: Producing metal frames, brackets, and decorative elements.
HVAC: Making ductwork, fittings, and other heating, ventilation, and air conditioning components.
Key Features of a CNC Sheet Metal Brake Machine:
Computer Numerical Control (CNC): The machine uses computer software to control the bending process, allowing for precise and complex bends with minimal manual intervention. Operators input the specifications, and the machine executes the bends according to the programmed instructions.
Hydraulic or Electric Actuation: CNC sheet metal brakes can be powered by hydraulic systems, electric motors, or a combination of both. Hydraulic systems provide powerful and smooth bending operations, while electric systems offer energy efficiency and precision.
Programmable Bending Sequences: Users can program a series of bends and angles into the machine, enabling it to perform complex bending sequences automatically. This feature is especially useful for producing multiple parts with identical specifications.
High Precision and Accuracy: The CNC control system ensures that each bend is performed with high precision, reducing the likelihood of errors and material waste. This is crucial for applications that require tight tolerances and consistent quality.
Versatility: CNC sheet metal brakes can handle a wide range of materials, including steel, aluminum, copper, and other metals. They can also accommodate various thicknesses and sizes of sheet metal, making them versatile tools for different manufacturing needs.
Safety Features: Modern CNC sheet metal brakes are equipped with safety features such as light curtains, safety interlocks, and emergency stop buttons to protect operators from potential hazards during operation.
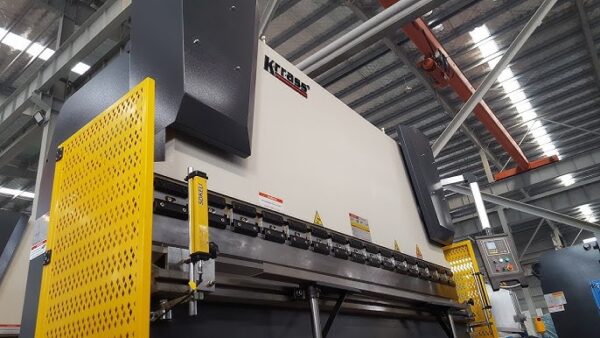
Introduction to CNC Metal Brake Maintenance
Proper maintenance of your CNC metal brake is essential for ensuring its longevity and optimal performance. A well-maintained machine not only produces more accurate and consistent results but also minimizes downtime and reduces the likelihood of costly repairs. By adhering to a regular maintenance schedule, you can significantly extend the lifespan of your CNC metal brake and ensure it operates at peak efficiency.
Importance of Maintenance
Preventive Care: Routine checks and servicing can identify potential issues before they become major problems, preventing unexpected breakdowns and costly repairs.
Safety: Ensuring all components are in good working condition minimizes the risk of accidents, protecting both the operator and the machine.
Consistency: Regular maintenance helps maintain the precision and accuracy of the brake, which is vital for producing high-quality parts.
Benefits of Regular Upkeep
The benefits of regularly maintaining your CNC metal brake include:
Extended Lifespan: A well-maintained machine lasts longer, providing a better return on investment.
Cost Savings: Preventive maintenance reduces the need for expensive repairs and part replacements, saving money in the long run.
Improved Performance: Regular upkeep ensures that the machine operates smoothly and efficiently, leading to better productivity and quality of work.
Reduced Downtime: Keeping the machine in good condition minimizes unexpected breakdowns and the associated production delays.
How to Maintain A CNC Metal Brake Machine
Before Buying
Maintaining your press brake should start well before the machine even arrives at your shop. It's crucial that operators, shop staff, and managers all embrace a maintenance mindset for every piece of equipment and the entire work environment. Without this proactive approach, your new press brake could quickly develop expensive issues right from the beginning.
Are your machinery operators adhering to the scheduled maintenance routines for your existing machines? Do they keep both the machines and the shop area clean? It's common for operators and shop workers to leave parts, tools, and debris around the machines. It's essential for your team to develop the habit of maintaining cleanliness in all machines and work areas. Neglecting this can lead to safety and productivity problems, as well as potential damage to your machines due to accumulated dirt and debris.
When You Buy
Ensuring Proper Training and Staffing
When purchasing new equipment, especially a CNC press brake, it’s vital to ensure you have staff who are either already trained or willing to be trained to operate the machines. Complex equipment like CNC machines and lasers require skilled personnel who can operate them correctly without resorting to shortcuts or making mistakes that could damage parts, the machines themselves, or, more importantly, harm people. It's important to allocate enough budget for staff training or to hire new operators who will run and maintain the machines properly.
Leveraging Machine Features for Easier Maintenance
Many machines come with features designed to make processes easier and safer. An example is a tooling system for a press brake that quickly and accurately seats tooling, saving time and preventing damage from improperly seated tools. Explore available options that can simplify maintenance and reduce potential issues. These features not only enhance efficiency but also contribute to the longevity and safety of your equipment.
Importance of Maintaining and Storing Manuals
It's essential to have a backup of your press brake manual. If it comes in printed form, ask the seller or manufacturer for a digital copy. If unavailable, take the time to photocopy the manual or scan it into a PDF. Conversely, if the manual is digital, print a copy and store it in the electrical panel for easy access by operators and service technicians. Store any digital copies, such as those on thumb drives or CD-ROMs, in a safe location away from the machine. A manual is as crucial to your press brake as the tooling itself. Operators often misplace them, and replacements can be costly. Additionally, valuable billable time can be lost while technicians wait for the manual to be found or a replacement to be obtained.
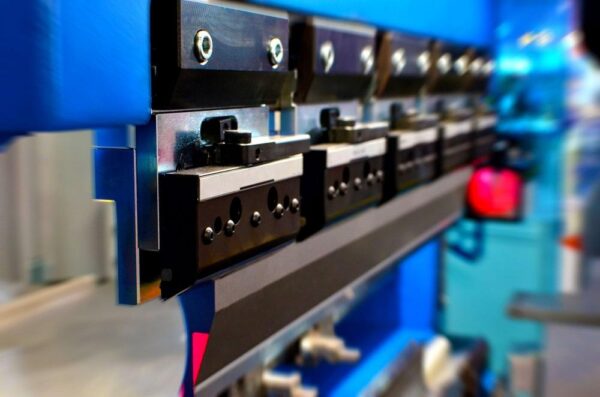
When Install A CNC Metal Brake
Proper preparation before the installation of your press brake is crucial to ensure smooth operation and prevent potential damage. Waiting until the machine is powered up for the first time to start maintenance practices is often too late and can lead to serious issues. Many press brake buyers make the mistake of attempting to experiment with their machines before they are fully installed by trained professionals, which can result in various problems and even significant damage.
Before the installation crew arrives, there are essential tasks that should be completed:
Positioning: Ensure the press brake is placed exactly where you want it in your workshop.
Anchoring Preparation: Prepare the area for anchoring the press brake securely to the floor.
Leveling: Verify that the press brake is ready to be leveled accurately.
Power Preparation: Ensure there is power available for the press brake, but do not connect it until instructed.
Oil Check: Confirm that the press brake has sufficient oil to operate effectively.
After completing these preparations, it's crucial to refrain from further handling or experimentation and await the arrival of the installers. Proper installation and calibration by trained professionals are essential. If not executed correctly, the press brake may never achieve optimal performance.
Daily Maintenance Routine for Your Press Brake
At the Start of Each Workday
Every morning, before your operator begins work, it's crucial to maintain a clean environment around the press brake to ensure safe and efficient operation. Removing hazards and dirt that can potentially interfere with the machine's functions is essential. Your operator should carefully wipe down the tooling and other surfaces of the press brake using a dry cloth to eliminate visible dirt, dust, or any foreign objects. These contaminants pose a threat to both the press brake and its tooling, underscoring the importance of maintaining a consistently clean environment.
Additionally, your operator should prioritize cleaning the safety lasers with a dedicated, non-abrasive cloth. Over time, dirt build-up and scratches on the lens can scatter the laser light, compromising its ability to accurately target the receiver. By maintaining cleanliness and ensuring the lasers remain in optimal condition, you enhance the safety and precision of your press brake operations. Regular attention to these details helps mitigate potential issues and prolongs the lifespan of your equipment.
Preparing for a Job
The quality of your press brake's performance heavily relies on the quality and condition of its tooling. Using high-quality, well-maintained tooling is crucial for achieving accurate and precise parts. If the press brake is equipped with old or worn-out tooling, it not only compromises part accuracy but also diminishes the overall machine performance.
As your operator loads tooling for a job, ensuring correct seating is paramount. The upper tool should be seated under a small amount of tonnage to ensure it fully engages into the tooling holder. Periodically verifying correct tooling alignment is also essential to prevent operational issues. When troubleshooting a press brake, one of the initial steps should be verifying and adjusting tooling alignment to maintain optimal performance.
Maintenance of Tooling and Surrounding Areas
During bending operations, metal can shed mill scale and other debris, while grease and oil may attract dust and dirt. Over time, these contaminants can accumulate around and under the tooling, potentially affecting accuracy. When changing tooling, your operator should meticulously clean the working surfaces of the tooling, the upper punch where it seats, and underneath the bottom die. Ensuring these areas are free from grit and dust prevents inaccuracies that can arise if even minor build-ups alter the height or positioning of the tooling. In fact, a bend's accuracy can be disrupted by up to two degrees if the press brake tooling height shifts by as little as two thousandths of an inch due to dust and debris accumulation.
By adhering to these practices, your operators can uphold the precision and efficiency of your press brake operations, minimizing errors and maximizing the lifespan of your equipment. Regular maintenance and careful preparation contribute significantly to achieving consistent high-quality results in metal bending processes.
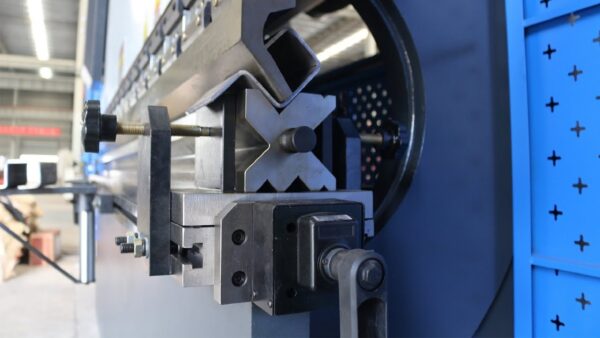
During Press Brake Operations
Monitoring Tooling and Listening for Signs
It's crucial for the press brake operator to regularly inspect and clean the tooling's exposed surfaces during operation. This visual inspection helps to detect any build-up or wear that could affect the bending process. Additionally, operators should listen attentively for unusual noises while the press brake is in use. Any unusual sounds or vibrations should prompt immediate investigation, as they may indicate loose components or other mechanical issues that need attention.
Bending Practices for Optimal Results
Always bend parts in the center of the press brake, regardless of whether it's a small part or the machine features a Y1/Y2 setup. This practice ensures that bending forces are evenly distributed, minimizing the need for adjustments and reducing strain on the brake over time.
Monitoring Anchor Bolts and Machine Stability
Press brakes are dynamic machines that undergo continuous movement and flexing during operation. Operators should regularly check anchor bolts to ensure the machine remains stable and level. A stable machine foundation is critical to maintaining accurate bends and preventing potential damage caused by machine movement.
By integrating these practices into daily operations, operators can enhance the reliability and longevity of the press brake while optimizing production efficiency and part quality. Regular monitoring and proactive maintenance contribute to a safer and more productive work environment for press brake operations.
After Job Completion
After completing the day's tasks, it's important to follow proper procedures to ensure the longevity and performance of your press brake:
Ram Positioning: Hydraulic systems can lose pressure when the ram is held up. Therefore, a standard practice is to lower the ram to the bottom position at the end of its use. Your operator should lower the beam with the punch fully down into the die. To protect the tooling, consider removing them and supporting the ram's weight on blocks of wood or other suitable materials. Always park the ram before performing any maintenance on hydraulic or mechanical systems.
Surface Cleaning: Once again, using a dry cloth, the operator should meticulously wipe down the tooling, back gauges, guides, and other surfaces. This routine maintenance helps remove dirt, dust, and debris accumulated during the day's operations, ensuring that the machine remains in optimal condition for the next workday.
By incorporating these practices into your daily routine, you can uphold the efficiency, accuracy, and longevity of your press brake equipment. Regular maintenance and proper cleaning not only preserve the machine's performance but also contribute to a safer and more productive work environment.
Implementing Weekly Press Brake Maintenance
Establishing Routine Maintenance
To ensure the longevity and optimal performance of your press brake, establish a weekly maintenance routine based on the manufacturer's recommendations. Post a prominently displayed list of these tasks in your shop near the machine, and require all operators and shop workers to adhere to it. Managers should regularly check compliance to maintain machine integrity and safety. Consider scheduling a dedicated time at the end of each workweek for comprehensive cleaning and inspection of all machines in your shop.
Safety Precautions and Inspection
During maintenance activities, operators should thoroughly inspect the machine for any loose parts while cleaning. Always ensure the power to the machine is turned off, locked out, and disconnected to prevent accidents and damage during maintenance.
Lubrication and Cleaning
Follow the maintenance schedule specified in your press brake manual for lubricating various parts weekly. Heavy components like the ram guiding system should be greased, while more delicate mechanisms such as back gauge spindles should be oiled to avoid picking up mill scale. Clean the surfaces as you lubricate, removing excess grease and oil. Apply rust protectant to susceptible surfaces to prevent corrosion.
Touch Screen Care
The touch screen controls on your press brake are sensitive and essential for operation. Regularly clean the touch screen with a microfiber cloth to remove natural oils and contaminants from operator's hands, as well as residue from tooling and parts. This practice helps prevent operational errors and ensures the touch screen remains responsive and functional.
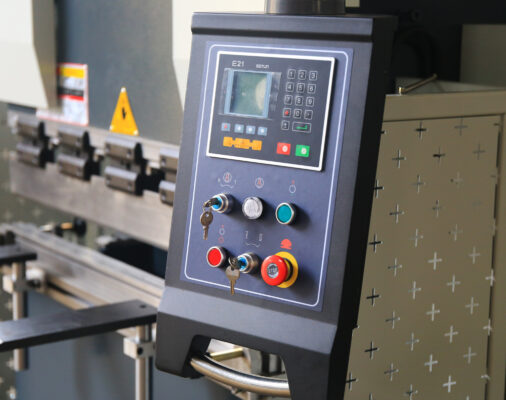
Monthly Maintenance Guidelines for Your Press Brake
Greasing and Hydraulic Maintenance
Refer to your press brake manual to identify and grease monthly-moving parts as specified. Check hydraulic oil levels regularly, using the recommended oil type for top-ups to maintain optimal performance.
Hydraulic System and Electrical Cabinet Care
Regularly clean the hydraulic pump motor and all hydraulic circuit components to prevent dust accumulation. Check for leaks and ensure all hydraulic connections are secure when the machine is powered off. Monthly, inspect and clean the air filter in the hydraulic tank for proper ventilation. Clean filters on electrical cabinet vents and cooling fan to prevent overheating of critical components. Keep the electrical cabinet door closed when not in use for safety and cleanliness.
Bolt and Connection Inspection
Monthly, inspect and tighten all bolts and connections to prevent issues arising from vibrations during operation. Ensuring all components are securely fastened contributes to the smooth and reliable performance of your press brake.
By diligently following these monthly maintenance routines, you can prolong the lifespan of your press brake, minimize downtime, and maintain high operational efficiency in your workshop. Regular care and inspection help mitigate potential issues, ensuring consistent productivity and safety.
Annual Maintenance Procedures for Your Press Brake
Hydraulic System Maintenance
Change hydraulic oil and oil filters annually, or after approximately 2000 hours of operation. Properly drain and dispose of the old oil, clean the tank thoroughly, and install a new oil filter. If switching to a different type or brand of oil, ensure the entire hydraulic system is cleaned to prevent compatibility issues.
Electrical System Inspection
Annually inspect all electrical connections and switches. Some checks may require operation under power, necessitating strict adherence to safety protocols. For other electrical maintenance tasks, ensure the main power is switched off and locked out to prevent accidents.
Professional Service and Maintenance Contracts
Arrange for a specialized service technician to conduct annual preventative maintenance on your press brake. They can identify and address potential issues in the electrical and hydraulic circuits that may not be apparent to operators. Consider opting for annual maintenance contracts offered by press brake dealers or service centers, which can provide cost savings and ensure regular upkeep of your equipment.
By adhering to these annual maintenance practices, you can enhance the reliability, safety, and longevity of your press brake. Regular professional servicing and systematic checks minimize downtime, optimize performance, and contribute to a productive workshop environment.
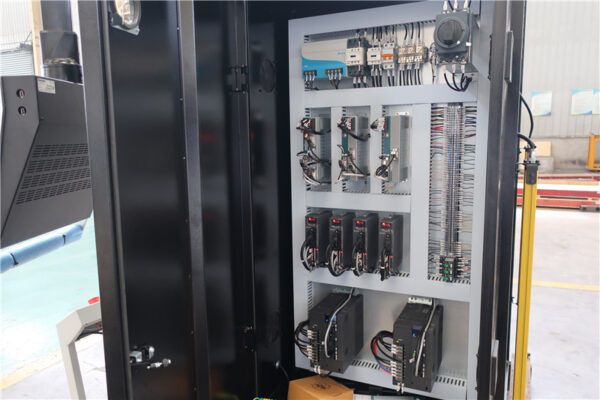
Press Brake Troubleshooting Guide: When It Won’t Go Up
Encountering issues with a press brake not moving the ram upward can be complex, requiring a methodical approach to diagnose and resolve the problem effectively. Here’s a comprehensive continuation of troubleshooting steps:
Electrical System Check
Ensure all electrical components are operational. Verify the emergency stop button is released and the main power switch is on, as these safety features can inadvertently prevent the machine from powering up. Inspect for blown fuses or tripped circuit breakers that may interrupt the power supply to the press brake.
Hydraulic System Inspection
Check the hydraulic oil reservoir to ensure it is adequately filled. Inspect all hydraulic hoses and connections for leaks, cracks, or loose fittings that could affect hydraulic pressure. Listen for abnormal noises or vibrations from the hydraulic pump, indicating potential mechanical issues. Test the hydraulic pressure using a pressure gauge to verify it meets manufacturer specifications, and adjust if necessary as per the press brake manual.
Mechanical Component Evaluation
Check for obstructions or misalignments in the ram guiding system that may impede smooth movement. Inspect all bolts and fasteners to ensure they are securely tightened. Verify that the back gauge and tooling are correctly installed and calibrated.
Control System Troubleshooting
Review the control panel for error messages, alarms, or indicators of malfunction. Ensure all safety interlocks are engaged correctly. Test the press brake with a known working program to determine if the issue lies with the program or the control system itself.
Hydraulic Pressure Adjustment
Consult the press brake manual for instructions on adjusting hydraulic pressure settings. Make small, incremental adjustments to hydraulic pressure and observe the ram's movement after each adjustment to gauge effectiveness.
Professional Service Consultation
Contact a qualified service technician or the press brake manufacturer's technical support for further assistance if troubleshooting steps do not resolve the issue. Provide detailed information about the issue, including symptoms observed and steps taken during troubleshooting, to aid in diagnosis.
By following these systematic troubleshooting steps, you can identify and address the root cause of a press brake's failure to move the ram upward. Regular maintenance and proactive troubleshooting contribute to reliable operation and prolonged equipment lifespan in your workshop.
Conclusion
In conclusion, maintaining your CNC metal brake is essential for ensuring its longevity and efficiency. By following a regular maintenance schedule, keeping the machine clean, and addressing any issues promptly, you can prevent costly downtime and extend the life of your equipment. It’s also crucial to train your operators properly and ensure they understand the importance of maintenance tasks.
Investing in a quality machine, like those from Krrass, can also make a significant difference. Krrass press brakes are known for their durability, precision, and ease of maintenance. By choosing a reliable CNC metal brake from Krrass, you can benefit from advanced features and robust construction that contribute to the overall efficiency and productivity of your shop.
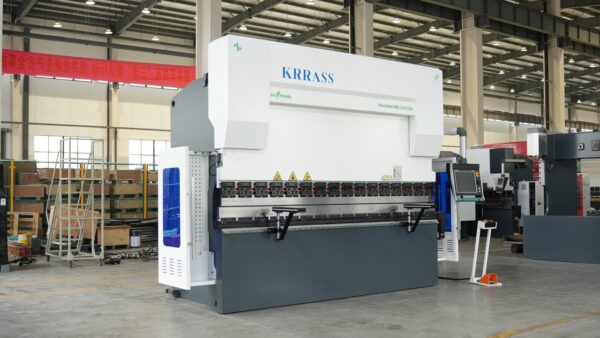