A hydraulic ironworker machine is a metal processing tool used in the steel fabrication industry that can shear, cut, and punch holes. It is the most commonly used type of ironworker machine and is used in industries such as metallurgy, bridges, communications, electric power, and military. Today, I will give you a comprehensive and detailed introduction to the hydraulic ironworker machine from multiple angles, so that buyers can better grasp and operate the machine. Hope it helps you.
Table of Contents
What is Hydraulic Ironworker Machine
A hydraulic ironworker machine is a versatile piece of industrial equipment used for cutting, punching, notching, and bending various types of metal. It’s commonly found in metalworking shops, fabrication shops, and manufacturing plants. The machine operates using hydraulic power to generate the force needed for various metalworking tasks.
Multiple Functions
Cutting:
It can cut through flat bars, angle iron, round and square rods, and even structural steel sections with ease. This makes it useful for creating parts with precise dimensions in metal fabrication.
Notching:
The machines can notch metal sheets and plates at precise angles, making it easier to fit pieces together during fabrication. This function is particularly useful for creating joints in metal structures.
Bending:
Some hydraulic ironworker machines come with bending attachments or accessories that allow them to bend metal bars, tubes, and plates into various shapes. This adds to the machine’s versatility and makes it capable of handling a wide range of metalworking tasks.
Shearing:
In addition to cutting flat bars and plates, hydraulic ironworkers can also shear metal sections such as angle iron and channel beams. This makes it useful for quickly and accurately cutting metal stock to size.
Multiple Stations
Punching station
All metal punching operations of the ironworker machine are processed using hydraulic power, thus allowing the machine to punch very efficiently and silently. Punching is silent, powerful, and efficient. The device can either be used to hit thick metal or thin materials layered together. The waste materials come off together and in layers. The punching table consists of two parts: the first is the punching flange, and the second is the holder. There are different holders for different materials. The holder is a device that prevents the fabric from coming back with the punch after cutting.
Flat bars shearing station
The metal shear station of the ironworker machine has been equipped with simple and sturdy fixing mechanisms. Depending on the machine’s cutting capacity, You can adjust it for any steel thickness. The shearing capacity can go up to 17.71 inches in the flat bar or the cutting of corner profiles. The shearing blades, built for mass production, can be used on both sides (the upper blade has two cutting edges, and the lower blade has four cutting edges); this ensures a clean cut with minimal warping, from the total capacity to a thickness of only 1/8 inch.
Bars cutting station
Standard machines are equipped with blades for cutting U-sections. The edges are held by efficient jaws, ensuring the equipment can be arranged easily at the device without any additional adjustment. Thanks to other equipment, cutting I-section profiles, T-sections, and round and square metal bars is possible.
Notching station of ironworker machine
High Adaptability: With QBH, QCS, and other optical fiber interfaces, it can be adapted to various mainstream laser devices.
Excellent Design: Optimized optical configuration and smooth and efficient airflow design significantly improve cutting quality and efficiency.
Angle shearing station
This station enables the cutting of large angles with a capacity ranging from 17 3/4 inches to 35 1/2 inches.
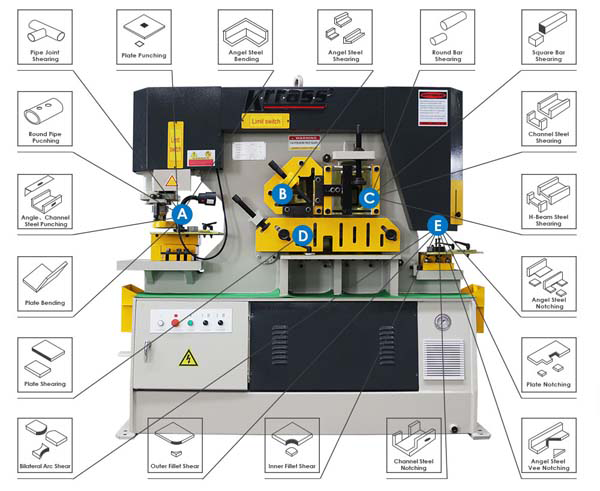
Features
The main features of a hydraulic ironworker machine can be the following:
- Accurate & Solid steel frame
- Adjustable stroke controls with indicators on both cylinders
- Hydraulic system with overload protection
- Easy to maintain
- Can stop when emergency by using switch
- Large flat cutting table with a ruler guide
- 2 independent hydraulic cylinders
How Does an Ironworker Work?
A typical ironworker is comprised of a fixed frame, motor, safety shields, the metal working pieces as well as a control panel/foot pedal. Most machines are electronically and/or hydraulically controlled, and some typical working principles include:
- The sliding plate with a cutting edge to shear metal materials against a fixed edge.
- The movable punch to produce customizable holes in a variety of metal materials.
- The ram or sliding arm to force metal products around a fixed point or into a die.
The single operator can complete most actions using a foot pedal or button, with many actions often repeated in quick succession for a steady production flow.
Due to the high forces required to bend and cut metal, hydraulic transmissions are common on ironworker machines.
General Capabilities of an Ironworker Machine
An ironworker machine can come in many different sizes, with the specifications of each one varying accordingly. For example, the weight of an ironworker machine can vary from 1,500kg to over 12,000kg, with the corresponding cutting force ranging from 600kN to 2500kN respectively.
Ironworkers can cut plates from 16mm thick up to 40mm thick, punch through metal up to 35mm thick and cut channel up to 300mm.
Depending on the size of the actual machine, you can feed different lengths of the metal products into an ironworker – it is possible to shear flat plates up to 750mm in length. This makes these machines incredibly versatile and a useful addition to any metal workshop.
Types of Ironworker Machine
There are two main types of ironworkers: Mechanical Ironworker machine and hydraulic ironworker machine.
Mechanical ironworkers are powered by mechanical means, typically using a flywheel and clutch system. They are often operated manually or with the help of foot pedals. These machines are reliable and efficient for smaller-scale metalworking operations.
Hydraulic ironworkers use hydraulic power to perform cutting, punching, notching, and bending operations. They offer higher precision, greater power, and increased versatility compared to mechanical ironworkers.
Hydraulic ironworkers are popular in medium to large metal fabrication shops and manufacturing plants.
The most widely used Ironworker machine is the ydraulic Ironworker Machine. Because it is suitable for processing small workpieces and can work multiple stations at a time.
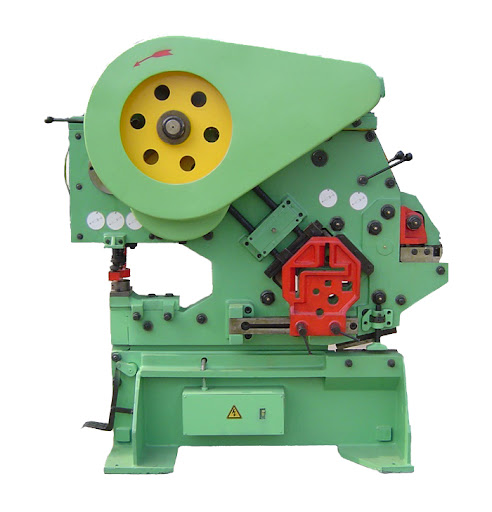
Here’s a comparison between mechanical and hydraulic ironworker machines:
Power Source: Mechanical ironworkers are powered by mechanical means, typically using a flywheel and clutch system. They may require manual operation or foot pedals to activate the cutting, punching, and bending mechanisms. Hydraulic ironworkers use hydraulic power to generate the force needed for cutting, punching, notching, and bending operations. They typically offer greater control over the application of force, allowing for precise and efficient metalworking.
Speed: Mechanical ironworkers often have a fixed speed determined by the rotation of the flywheel. While they can be efficient for smaller-scale operations, their speed may be limited compared to hydraulic ironworkers. Hydraulic ironworkers often offer variable speed settings, allowing operators to adjust the speed according to the specific task and material being processed. This can result in faster overall production rates compared to mechanical ironworkers.
Maintenance: Mechanical ironworkers tend to have simpler mechanisms and require less maintenance compared to hydraulic counterparts. They may have fewer moving parts, reducing the likelihood of mechanical failures.
Cost: Mechanical ironworkers are generally less expensive upfront compared to hydraulic models. They can be a cost-effective option for smaller shops or hobbyists with lower production volumes.
Force: Mechanical ironworkers may have limitations in terms of the force they can exert compared to hydraulic models. This could affect their ability to handle thicker or harder materials efficiently.
Versatility: Hydraulic ironworkers are highly versatile and capable of performing a wide range of metalworking tasks, including cutting, punching, notching, and bending. They can handle various materials and thicknesses with ease.
Control: Hydraulic ironworkers offer precise control over the application of force, allowing for accurate and repeatable metalworking operations. This level of control is especially beneficial for tasks requiring tight tolerances or complex shapes.
Mechanical vs Hydraulic Ironworker Machine: How to Choose
Mechanical ironworkers are simpler, more cost-effective, and easier to maintain, but they may have limitations in terms of speed, force, and versatility. Hydraulic ironworkers, on the other hand, offer greater power, speed, versatility, and control, making them well-suited for heavy-duty industrial applications and tasks requiring precision and efficiency. The choice between mechanical and hydraulic ironworkers ultimately depends on factors such as budget, production requirements, and the specific needs of the metalworking operation.
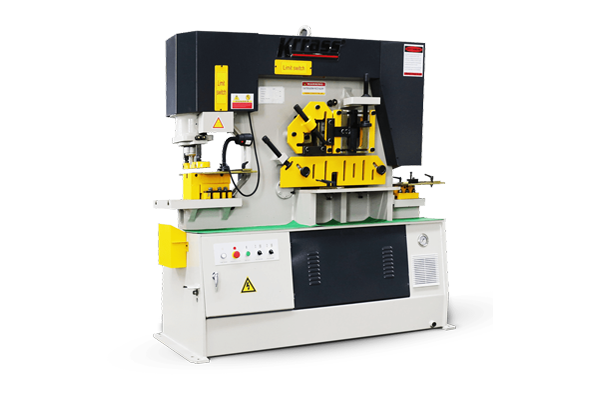
Advantages and Disadvantages of Hydraulic Ironworker Machine
Hydraulic ironworker machines offer several advantages and disadvantages compared to other types of ironworker machines, such as mechanical models. Here are some of the key advantages and disadvantages of hydraulic ironworker machines:
Advantages:
Versatility: Hydraulic ironworkers are highly versatile machines capable of performing multiple metalworking operations, including cutting, punching, notching, and bending. This versatility makes them suitable for a wide range of metal fabrication tasks and materials.
Powerful: Hydraulic ironworkers utilize hydraulic power to generate significant force, allowing them to cut through thick or tough materials with ease. They can handle heavy-duty metalworking applications that may be challenging for other types of ironworker machines.
Precise Control: Hydraulic systems offer precise control over the application of force, allowing for accurate and repeatable metalworking operations. This level of control is essential for achieving tight tolerances and producing high-quality metal parts.
Variable Speed: Many hydraulic ironworkers feature variable speed settings, allowing operators to adjust the speed according to the specific task and material being processed. This flexibility improves efficiency and productivity, particularly for complex or varied metalworking projects.
Ease of Use: Hydraulic ironworkers are relatively easy to operate, with intuitive controls and user-friendly interfaces. They require minimal physical effort from the operator, reducing fatigue and increasing productivity during prolonged use.
Safety: Hydraulic ironworkers often come equipped with safety features such as guards, emergency stop buttons, and overload protection systems to ensure operator safety during operation. These safety features help prevent accidents and injuries in the workplace.
Disadvantages:
Initial Cost: Hydraulic ironworker machines tend to be more expensive upfront compared to mechanical models. The initial investment cost may be prohibitive for smaller workshops or businesses with limited budgets.
Maintenance: Hydraulic systems are more complex than mechanical systems and may require more frequent maintenance to ensure optimal performance. Regular maintenance tasks such as hydraulic fluid checks, filter replacements, and seal inspections are essential to prevent downtime and costly repairs.
Space Requirements: Hydraulic ironworkers are typically larger and heavier than mechanical models, requiring more floor space in the workshop or industrial facility. If space is limited, this could be a significant drawback.
Hydraulic Fluid Concerns: Hydraulic systems rely on hydraulic fluid to function properly. Issues such as leaks, contamination, or fluid degradation can affect the performance and reliability of the machine. Regular monitoring and maintenance of the hydraulic fluid system are necessary to prevent problems.
Energy Consumption: Hydraulic ironworker machines require electrical power to operate the hydraulic pump, which can result in higher energy consumption compared to mechanical models. However, advances in hydraulic system design have led to improved energy efficiency in modern machines.
Applications of Hydraulic Ironworker Machine
Metal Fabrication: Hydraulic ironworkers are widely used in metal fabrication shops to cut, punch, notch, and bend metal sheets, plates, bars, and sections. They are essential for creating precise and complex metal parts and components used in structures, machinery, equipment, and products.
Construction: In the construction industry, hydraulic ironworker machines are utilized for fabricating structural steel components such as beams, columns, and brackets. They can efficiently cut, punch, and notch steel materials to the required specifications for building construction, infrastructure projects, and architectural applications.
Manufacturing: Hydraulic ironworkers play a crucial role in manufacturing operations for producing various metal products and components. They are used in the production of automotive parts, machinery components, industrial equipment, appliances, and consumer goods, among others.
Steel Service Centers: Hydraulic ironworker machines are commonly found in steel service centers and metal processing facilities. They help process large volumes of steel and metal stock by cutting, punching, notching, and bending them into the desired shapes and sizes according to customer requirements.
Metalworking Workshops: Hydraulic ironworkers are essential tools in metalworking workshops of all sizes, from small-scale job shops to large-scale manufacturing facilities. They enable metalworkers to perform a wide range of metalworking tasks efficiently and accurately, improving productivity and reducing production time.
Shipbuilding and Marine Industries: Hydraulic ironworker machines are used in shipbuilding yards and marine industries for fabricating metal components used in ship construction, offshore structures, and marine equipment. They are instrumental in processing steel plates, profiles, and sections for various maritime applications.
Agricultural Machinery: Hydraulic ironworkers are utilized in the agricultural sector for fabricating metal components used in farming machinery and equipment. They can cut, punch, and bend metal materials to manufacture parts for tractors, harvesters, irrigation systems, and agricultural implements.
Repair and Maintenance: Hydraulic ironworker machines are indispensable tools for repair and maintenance tasks in various industries. They are used to replace damaged or worn-out metal parts, fabricate custom components, and perform metalworking repairs on machinery, equipment, vehicles, and infrastructure.
Hydraulic ironworker machines find extensive applications in metalworking industries where cutting, punching, notching, and bending of metal materials are required. Their versatility, efficiency, and precision make them indispensable tools for a wide range of metal fabrication and manufacturing processes.
How to Use a Hydraulic Ironworker Machine
- Check the power supply, the voltage is stable, there is no lack of phase, and the leakage protector and air switch are intact.
- Wiring, open the wiring cabinet of the combined punching and shearing machine, connect the wires, and close the cabinet door.
- Step on the foot switch after powering on, and the machine has no action. Replace the power cords and check whether the emergency stop switch is turned on at the same time.
- Connect the foot pedal switch.
- When working, pay attention to turn off the power every time the mold is changed at work
- Turn off the switch after finishing the work, turn off the main power switch, skim off the power cord, and clean up debris.
Precautions When Using Hydraulic Ironworker Machine
- Before driving, check whether the transmission parts of the punching and shearing machine and the connecting screws and pins of each part are loose. Whether the electrical grounding is intact.
- Lubricate all parts before work, and start the trial run for two to three minutes, and then put into work without any problems.
- Overload is not allowed, and punching and shearing of quenched steel is strictly prohibited.
- Wear gloves and labor protection equipment when working. Sandals and slippers are strictly prohibited.
- When punching and cutting, always add oil to the punches to prevent the upper and lower punches from skewing.
- Pay attention to the safety of your fingers when feeding the material, especially when the sheet material is not pressed by the presser foot at the end, punching and shearing are prohibited.
- It is strictly forbidden to disassemble and proofread the cutting edge and punching die when driving. Don’t hit punches, shears and other parts with force.
- Strictly control the specification range of the sheet material, and it is strictly forbidden to punch and cut when it exceeds it.
- The workplace shall not accumulate other objects and a large amount of flushing materials, and must stop during adjustment and cleaning.
- After the work is completed, shut down and cut off the power in time to clean up the site.
Maintenance
Regular Inspection: Perform visual inspections of the machine regularly to check for any signs of wear, damage, or leaks. Inspect hydraulic hoses, fittings, seals, and cylinders for any signs of leakage or deterioration.
Hydraulic Fluid Checks: Check the hydraulic fluid level regularly and top up if necessary. Inspect the hydraulic fluid for signs of contamination, such as dirt, debris, or water. Replace the hydraulic fluid and filters according to the manufacturer’s recommendations.
Lubrication: Ensure that all moving parts, including bearings, joints, and guides, are properly lubricated according to the manufacturer’s specifications. Use the recommended lubricants and grease points to prevent friction, wear, and corrosion.
Cleanliness: Keep the machine clean and free from dirt, dust, and debris. Regularly clean the work area, surfaces, and components to prevent contamination of hydraulic fluid and maintain optimal performance.
Safety Checks: Inspect safety features such as guards, emergency stop buttons, and overload protection systems regularly to ensure they are functioning correctly. Replace or repair any damaged or malfunctioning safety components immediately.
Alignment and Adjustment: Check the alignment and adjustment of cutting blades, punching dies, and bending attachments regularly to ensure accurate and precise operation. Make any necessary adjustments or replacements to maintain quality and consistency in metalworking tasks.
Electrical Components: Inspect electrical connections, switches, and controls regularly to ensure they are secure and functioning correctly. Check for any signs of damage or wear and replace or repair as needed.
Training and Operator Awareness: Provide training to operators on the proper operation, maintenance, and safety procedures for the hydraulic ironworker machine. Encourage operators to report any issues or abnormalities promptly to prevent further damage or safety hazards.
Scheduled Maintenance: Follow the manufacturer’s recommended maintenance schedule for the hydraulic ironworker machine. Schedule routine inspections, lubrication, and servicing to prevent unexpected breakdowns and downtime.
Professional Service: If significant repairs or servicing are required, consult a qualified technician or service provider familiar with hydraulic systems and ironworker machines. Avoid attempting complex repairs or adjustments without the necessary expertise and equipment.
By performing regular maintenance and following proper care procedures, you can ensure that your hydraulic ironworker machine operates efficiently, safely, and reliably for years to come.
Technical Parameters of Q35Y Series Hydraulic Ironworker Machine
Technical Specification | Q35Y-12 | Q35Y-16 | Q35Y-20 | Q35Y-25 | Q35Y-30 | Q35Y-40 | Q35Y-50 | |||
---|---|---|---|---|---|---|---|---|---|---|
Punching Pressure(T) | 35T | 60T | 90T | 120T | 160T | 200T | 250T | |||
Depth of throat(mm) | 115 | 300 | 355 | 400 | 600 | 600s | 600 | |||
Standard Die | Punching | Dia.X Max.Thickness | mm | 25X12 | 25X16 | 30X20 | 35X25 | 38X26 | 40X35 | 40X40 |
Dia.X Thickness | mm | 25X12 | 25X16 | 30X20 | 35X25 | 38X26 | 40X35 | 40X40 | ||
Max.Diameter | mm | 12 | 25 | 30 | 35 | 38 | 40 | 40 | ||
Travel | mm | 35 | 80 | 80 | 80 | 80 | 80 | 80 | ||
Working Travel | mm | X18 | X20 | X25 | X25 | X30 | X35 | X40 | ||
Throat Depth | mm | 115 | 300 | 355 | 400 | 600 | 600 | 600 | ||
Steel Bar | Round | mm | 35 | 45 | 50 | 60 | 65 | 70 | 80 | |
Square | mm | 30X30 | 40X40 | 50X50 | 50X50 | 55X55 | 60X60 | 65X65 | ||
Steel Angle | Angle Size | mm | 86X86X8 | 125X125X12 | 140X140X12 | 160X1160X14 | 180X180X16 | 200X200X18 | 200X200X20 | |
Cutting Angle | ° | 50X50X5 | 50X50X5 | 50X50X5 | 60X60X6 | 60X60X6 | 100X100X10 | 120X120X10 | ||
Angle Section | mm | 5.5 | 5.5 | 6.5 | 9 | 11.5 | 12 | 12 | ||
Slotting | Thickness | mm | 100 | 126 | 160 | 210 | 280 | 300 | 320 | |
Width | mm | 30 | 53 | 60 | 75 | 86 | 89 | 92 | ||
Depth | mm | |||||||||
Optional Die | U-I Shaped Profile | mm | 100X100X8 | 125X125X12 | 140X140X12 | 160X160X14 | 180X180X16 | 160X160X14 | 180X180X16 | |
T-shaped Profile | mm | 40X40X6 | 60X60X8 | 70X70X10 | 80X80X10 | 80X80X10 | 80X80X10 | 80X80X10 | ||
I-Beam | mm | 40X60X4 | 126X74X5 | 160X86X6 | 200X102X9 | 280X124X10.5 | 300X126X11 | 320X130X10 | ||
V-Bending | Length | mm | 600 | 600 | 600 | 600 | 600 | 600 | 600 | |
V-Bending | Thickness | mm | 4 | 10 | 15 | 20 | 26 | 33 | 40 | |
Voltage | Kn | 350 | 600 | 900 | 1200 | 1600 | 2000 | 2500 | ||
Motor Power | kw | 4 | 5.5 | 7.5 | 11 | 15 | 18.5 | 18.5 | ||
Weight | Kg | 1600 | 1800 | 2400 | 4200 | 6800 | 7600 | 13500 | ||
Outline Dimension (LXWXH) | mm | 950X950X1800 | 1640X730X1770 | 1860X800X1990 | 2355X960X2090 | 2680X1040X2300 | 2970X1240X2350 | 3000X1440X2450 |
Conclusion
Hydraulic ironworker machines are valued for their efficiency, versatility, and ability to perform multiple metalworking tasks in a single machine, making them essential equipment in many metal fabrication and manufacturing operations. If you’re looking for a hydraulic ironworker machine with international standards, then contact KRRASS. KRRASS is the best company that supplies Q35Y series hydraulic ironworker machines all around the globe so no order is too small or too large to complete!
Reviewed by 1 user
Good machine
Very good iron workers, we have been buying for 2 years, we will buy again soon.