Welcome to the 2024 Latest Panel Bender Price Guide, your comprehensive resource for navigating the current landscape of panel bender prices. Panel benders play a crucial role in modern manufacturing, offering precision bending capabilities essential for various industries. As businesses strive for efficiency and cost-effectiveness, understanding the factors influencing panel bender prices is paramount. This guide explores the pricing dynamics across different brands, models, and specifications, helping you make informed decisions for your manufacturing needs.
What Is Panel Bender
Panel benders are sophisticated machines used primarily in the manufacturing and fabrication industries to accurately bend metal sheets or panels. They are essential for shaping various components used in sectors such as automotive, aerospace, electronics, furniture, and architectural industries. Unlike traditional press brakes, which typically bend metal at specified angles using a punch and die setup, panel benders employ a different approach known as folding.
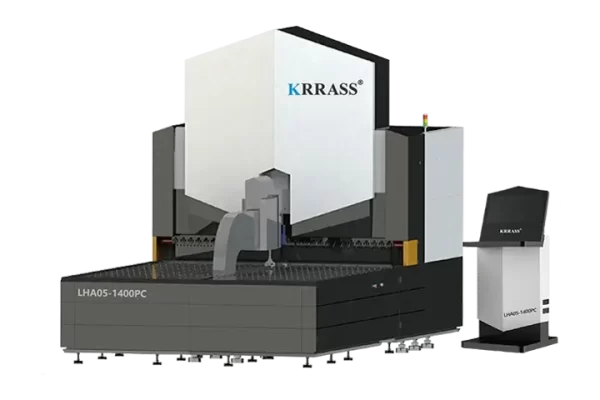
Unveiling the Mechanics of Panel Bender Machines
Delving into the realm of metal fabrication, the panel bender machine stands out as a cornerstone for efficient and precise metal forming. This engineering marvel not only simplifies the bending process but also guarantees unparalleled accuracy and repeatability. Fundamental to its functionality is its capability to shape metal sheets into precise angles and forms, catering to a diverse range of industrial applications.
Panel benders are advanced machines crucial to the precision bending of metal sheets or panels in various manufacturing industries. Unlike traditional press brakes, which rely on punch and die setups, panel benders utilize a folding mechanism to achieve bends along straight lines. This approach offers several distinct advantages in terms of efficiency, precision, and versatility.
At its core, the frame of the panel bender machine provides essential support and stability. Crafted from robust materials, it withstands the demands of bending operations while maintaining utmost precision. Crucial to the bending process, the bending blade varies in design based on machine models and specific bending requirements. The material and structure of the blade are critical in achieving precise and sharp bends.
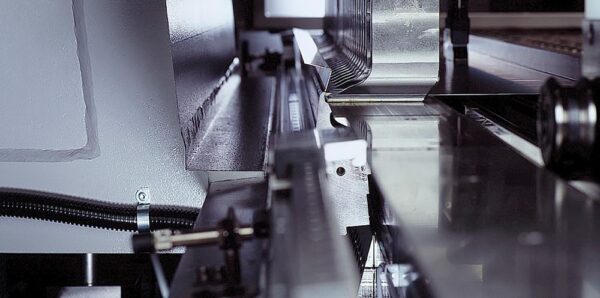
The control system acts as the machine's central intelligence. Modern panel benders integrate sophisticated software that facilitates precise control over the bending process. Operators can input parameters such as bend angle and sheet thickness, ensuring each bend is executed with meticulous accuracy. Additionally, the control system allows for program storage and retrieval, optimizing efficiency and consistency across production runs.
An indispensable component is the clamping system, which securely holds the metal sheet in place during bending. This prevents slippage and ensures precise alignment throughout the operation. Clamping systems vary in design, with some machines employing pneumatic or hydraulic mechanisms for enhanced strength and reliability.
Key Features and Functionality of Panel Benders
Folding Mechanism and Precision
Panel benders employ a folding beam that moves vertically to bend metal sheets accurately. This mechanism ensures high precision, typically with tolerances as tight as ±0.1 mm. In comparison, traditional press brakes may achieve ±0.5 mm tolerances, highlighting the superior accuracy of panel benders in intricate bending tasks.
Automation and CNC Control
Modern panel benders integrate Computer Numerical Control (CNC) systems, allowing for automated operation and precise control over bending parameters. Operators can program the CNC to execute complex bending sequences and adjust parameters such as bend angle, back gauge position, and tooling setups automatically. This level of automation significantly reduces setup times and increases productivity compared to manual setups on traditional equipment.
Efficiency and Throughput
The automation and programmability of panel benders enhance production efficiency by minimizing downtime between setups. They can perform multiple bends in a single setup, reducing cycle times and increasing throughput. Studies indicate that panel benders can achieve up to 50% higher productivity compared to traditional press brakes due to reduced setup and handling times.
Complex Bending Capabilities
Panel benders excel in bending complex shapes and geometries, such as flanges, hemming, and overlapping bends. Unlike traditional methods that may require multiple setups or secondary operations, panel benders streamline these processes into a single operation. This capability not only saves time but also improves product consistency and reduces material waste.
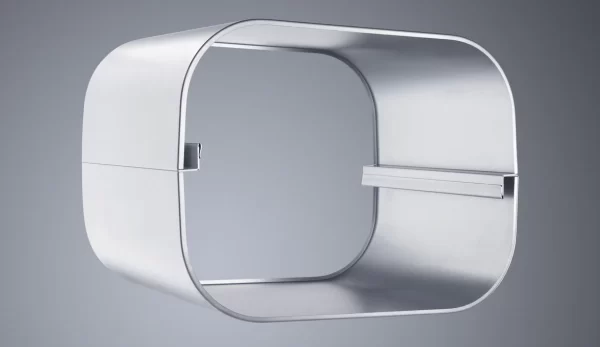
Economic Considerations
While initial investment costs for panel benders may be higher than traditional press brakes, their long-term economic benefits are significant. Factors such as reduced labor costs, lower scrap rates due to precise bending, and higher production throughput contribute to a favorable return on investment (ROI) over the machine's lifecycle. Studies suggest that businesses can achieve payback periods as short as 1-3 years depending on production volume and efficiency gains.
Advantages of Owning a Panel Bending Machine
Easy to Operate: Panel bending machines by KRRASS are designed for user-friendliness, accommodating various loading systems or operators with minimal training. Even manually loaded machines require only placing the panel and retrieving the finished product. Each KRRASS panel bender model includes part verification to ensure precision, independent of the loading method. Bending quality remains consistently high, unaffected by operator skill.
No Extra Tools: KRRASS panel benders achieve nearly every bend angle and radius using a single tool geometry, eliminating the need for additional tools and simplifying production setups.
Increased Productivity: Equipped with a tool changer and fast changeover times, KRRASS panel benders allow for smaller batch sizes and optimized production based on real-time demand. This reduces storage requirements and enhances overall productivity.
Precision Bending: KRRASS boasts industry-leading precision with a manipulator that offers positioning accuracy of +/- 0.0008” and rotation accuracy of +/- 0.001°. Their AC-servo motors ensure reliability, repeatability, and precise bending. The bending tools maintain contact with the outside edge throughout the movement, preventing flange twisting and ensuring straightness against the flat tool surface.
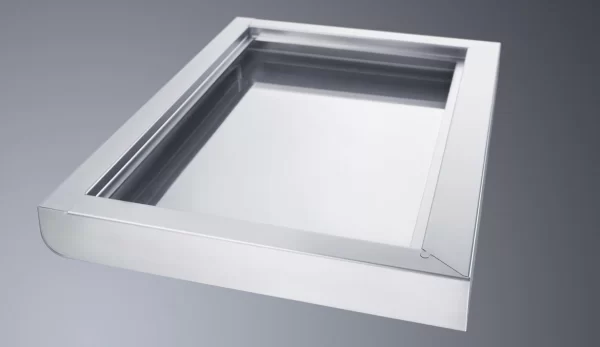
Why Does Panel Bender Also Calle "Soft Panel Bender"
Material Handling: Panel benders are known for their gentle handling of materials, which is crucial when working with delicate or thin sheets of metal. They use a folding method that minimizes stress on the material, hence the term "soft" as opposed to more forceful bending methods.
Reduced Marking: Compared to other bending techniques that may leave marks or require additional finishing, panel benders often produce clean bends without surface imperfections. This gentler bending process can be seen as "soft" on the material's surface.
Precision: Panel benders are capable of high precision in bending operations. The term "soft" may also refer to the precise control these machines offer over the bending process, ensuring accurate results without over-stressing the material.
In summary, "soft panel bender" highlights the machine's capability to handle materials gently, with precision and minimal impact, making it suitable for applications where preserving the material's integrity is crucial.
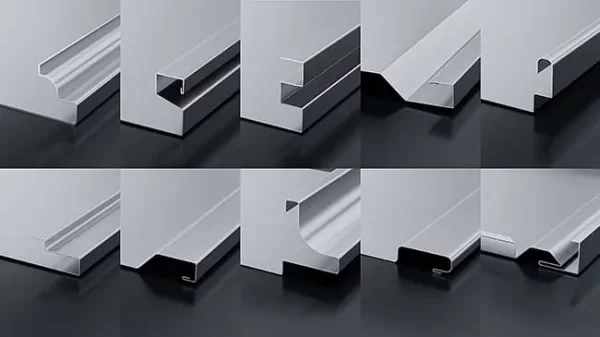
What Are Types of Panel Bender
Manual Panel Benders
Pros: Manual panel benders offer simplicity and affordability, making them ideal for small workshops or new businesses in metal fabrication. Operators have direct control over the bending process, allowing for adjustments based on their skill and experience.
Cons: They rely on manual labor, which can lead to inconsistencies in production and limit speed and output volume. Achieving precision in bends requires a higher level of operator skill.
Suitable Projects: Best suited for custom or low-volume projects where the craftsmanship of the operator can enhance the quality of bespoke items.
Semi-Automatic Panel Benders
Pros: Semi-automatic models provide a balance between manual and fully automatic machines, offering higher precision and productivity than manual benders. They require less manual effort and deliver more consistent results.
Cons: While improving efficiency and consistency, they still require operator intervention for certain tasks, which can limit output compared to fully automatic models.
Suitable Projects: Ideal for medium-sized production runs or workshops handling diverse projects, offering a good mix of speed, flexibility, and cost-effectiveness.
Fully Automatic Panel Benders
Pros: Fully automatic panel benders represent the peak of technology and efficiency in metal fabrication. They deliver the highest precision, speed, and consistency with minimal human intervention, suitable for handling large volumes of work.
Cons: Higher initial investment costs and complexity in operation and maintenance. They may offer less flexibility for unique, one-off projects compared to manual or semi-automatic machines.
Suitable Projects: Best suited for high-volume production environments such as automotive, appliance manufacturing, and construction, where precision, speed, and repeatability are crucial.
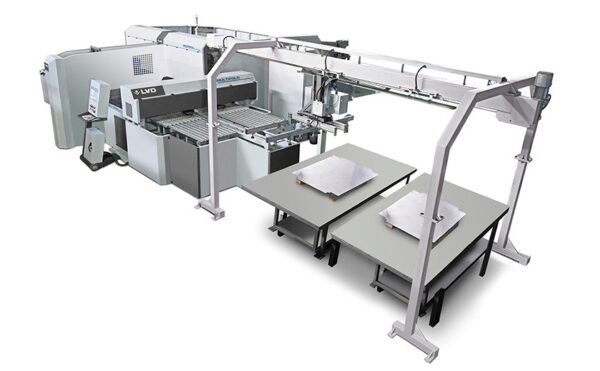
Basic Undertstanding of Paner Bender Price
What Factors Affect Panel Bender Price
1. Machine Type and Complexity
Manual Panel Benders: These are the least expensive type of panel benders. They rely on manual operation without automated controls or motorized adjustments. The simplicity in design and operation keeps costs lower, making them accessible for smaller workshops or businesses.
Semi-Automatic Panel Benders: Semi-automatic models incorporate some level of automation, such as motorized bending and back gauge adjustments. This automation increases precision and reduces manual effort compared to manual benders. As a result, semi-automatic panel benders are priced higher than manual ones but lower than fully automatic models.
Fully Automatic Panel Benders: These are the most expensive due to their advanced automation features. They typically include CNC controls for precise bending angles, automatic tool changers for rapid setup, and integrated software systems for programming complex bends. Fully automatic panel benders require minimal operator intervention and are capable of high-speed, high-volume production, making them ideal for large-scale manufacturing environments.
2. Size and Capacity
- Larger panel benders designed to handle thicker and wider materials require stronger structural components and higher power capabilities. This increased size and capacity result in higher manufacturing costs and consequently a higher selling price. These machines are suited for heavy-duty applications where robustness and capacity are critical.
3. Features and Technology
CNC Controls: Machines equipped with CNC (Computer Numerical Control) systems offer precise control over bending operations. The integration of CNC technology allows for complex bending sequences and ensures consistent accuracy, which adds to the machine's cost.
Precision Bending Capabilities: Advanced bending features such as programmable bending sequences, multi-axis back gauges, and adaptive bending technologies contribute to higher precision and flexibility. These capabilities enhance the machine's performance but also increase its price.
Automatic Tool Changers: Automated tool changers facilitate quick changeovers between different bending tools, reducing setup times and increasing operational efficiency. This feature is typically found in semi-automatic and fully automatic models, adding to their cost.
Integrated Software Systems: Modern panel benders often come with integrated software for CAD/CAM programming, simulation of bending processes, and optimization of material usage. These software systems enhance productivity and reduce material waste, but they also contribute to the overall cost of the machine.
4. Brand and Reputation
- Well-established brands with a reputation for quality, reliability, and excellent customer support tend to command higher prices for their panel benders. Customers are willing to pay a premium for machines from brands known for their durability, service network, and customer satisfaction.
5. Material Handling and Feeding Systems
- Additional features such as automated material handling systems, automatic feeding mechanisms, and part removal systems increase the efficiency of panel benders. These systems reduce downtime between operations, enhance workflow continuity, and improve overall productivity. However, they also raise the upfront cost of the machine.
6. Customization and Options
- Panel benders can be customized to meet specific production requirements, such as special tooling configurations or unique bending profiles. Customization options allow manufacturers to tailor the machine's capabilities to the exact needs of their production processes. However, customization adds engineering and manufacturing complexity, resulting in a higher price tag.
7. Market Demand and Supply
- Like any other product, panel bender prices are influenced by market demand and supply dynamics. High demand for panel benders, especially during periods of economic growth or industry expansion, can lead to higher prices. Conversely, oversupply or reduced demand may lead to price competition among manufacturers.
8. Country of Manufacture
- Manufacturing costs vary significantly by region due to differences in labor costs, material costs, regulatory requirements, and overhead expenses. Machines produced in regions with higher manufacturing costs (e.g., North America, Western Europe) may have higher prices compared to those manufactured in regions with lower costs (e.g., Asia). Additionally, factors like import tariffs and shipping costs can affect the final price of panel benders imported from different countries.
What Are Panel Bender Prices
Panel bender prices can vary widely based on the type of machine and its specific features. Here's a general overview of the price ranges you might expect for different types of panel benders:
Prices Based on Types
Manual Panel Benders:
Prices for manual panel benders typically range from approximately $5,000 to $20,000 USD, depending on the size, capacity, and basic features. These machines are simpler in design and operation, aimed at smaller workshops or businesses with lower production volumes.
Semi-Automatic Panel Benders
Semi-automatic panel benders offer increased automation and precision compared to manual models. Prices for semi-automatic benders generally range from around $20,000 to $80,000 USD. The cost varies based on the level of automation, bending capacity, and additional features like CNC controls and automatic tool changers.
Fully Automatic Panel Benders
Fully automatic panel benders are the most advanced type, designed for high-volume production and minimal operator intervention. Prices for fully automatic machines can start from $80,000 USD and go up to several hundred thousand dollars, depending on the size, complexity, precision capabilities (such as multi-axis CNC controls), and additional features like integrated software systems and advanced material handling.
Custom and High-End Models
Customized panel benders or high-end models equipped with specialized features, large bending capacities, and advanced automation can exceed $500,000 USD, particularly in industries requiring extreme precision and productivity, such as aerospace or automotive manufacturing.
Prices Based on Countries
North America and Western Europe
- Manual Panel Benders: Prices typically range from $8,000 to $25,000 USD.
- Semi-Automatic Panel Benders: Prices range from $30,000 to $100,000 USD.
- Fully Automatic Panel Benders: Prices start from $100,000 USD and can exceed $500,000 USD for high-end models.
- Custom and High-End Models: Prices can exceed $500,000 USD depending on customization and advanced features.
Machines manufactured in North America and Western Europe generally command higher prices due to higher labor costs, strict manufacturing standards, and advanced technological features often integrated into these machines.
Eastern Europe and Asia
- Manual Panel Benders: Prices typically range from $5,000 to $20,000 USD.
- Semi-Automatic Panel Benders: Prices range from $20,000 to $80,000 USD.
- Fully Automatic Panel Benders: Prices start from $80,000 USD and can go up to $300,000 USD or more for advanced models.
- Custom and High-End Models: Prices can vary widely based on customization but generally remain competitive compared to North America and Western Europe.
Machines manufactured in Eastern Europe and Asia often offer competitive pricing due to lower labor costs and favorable manufacturing conditions. However, pricing can still vary significantly based on the brand reputation, technological features, and customization options.
Other Regions (Latin America, Africa, etc.)
- Manual Panel Benders: Prices can range widely depending on local manufacturing capabilities and market demand, generally similar to or slightly lower than Asian prices.
- Semi-Automatic and Fully Automatic Panel Benders: Prices may vary but are generally reflective of regional economic factors and manufacturing capabilities.
Prices in other regions outside of the main manufacturing hubs (North America, Western Europe, Eastern Europe, and Asia) can vary greatly depending on local economic conditions, import tariffs, and availability of advanced manufacturing technologies.
Global Market Dynamics
Market Demand and Supply: Prices can also fluctuate based on global market dynamics, including changes in raw material costs, currency exchange rates, and global economic conditions affecting manufacturing costs and pricing strategies of panel bender manufacturers.
Top Panel Bender Manufacturers Along with Famous Models
Salvagnini
- Famous Model: Salvagnini P4Xe
- Description: The Salvagnini P4Xe is known for its advanced technology, high precision, and flexibility in handling complex bending tasks. It integrates cutting-edge software for precise control and automation, making it ideal for demanding industrial applications.
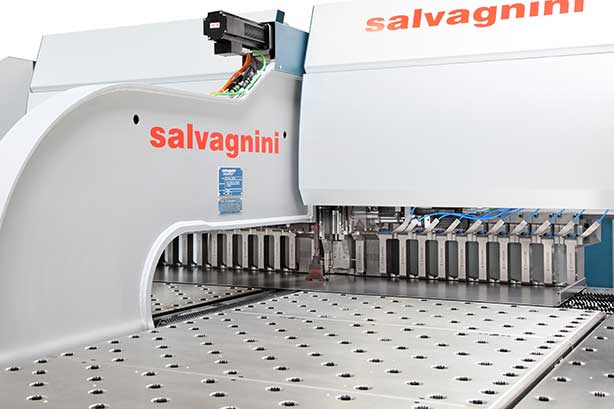
Schroeder
- Famous Model: Schroeder MAK V
- Description: The Schroeder MAK V series offers robust construction and versatile capabilities in bending various sheet metal thicknesses. It is renowned for its reliability, precision bending, and user-friendly features.
CIDAN Machinery
- Famous Model: CIDAN K25
- Description: CIDAN's K25 series is celebrated for its reliability, ease of use, and efficiency in handling diverse bending requirements. It is designed to provide consistent and precise bending results across different industrial sectors.
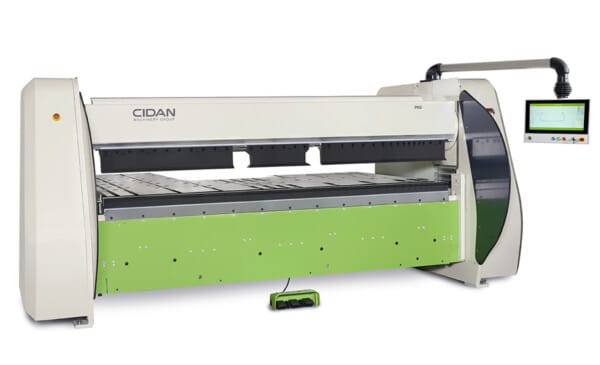
Gasparini
- Famous Model: Gasparini X-Press
- Description: The Gasparini X-Press series is known for its speed, accuracy, and advanced features like automatic tool changing systems. It is favored for high-volume production environments requiring rapid and precise sheet metal bending.
Haco
- Famous Model: Haco HSLX
- Description: The Haco HSLX series combines durability with advanced bending technology, offering precise bending results and adaptability to varying production demands. It is recognized for its reliability and high-performance capabilities.
RAS Systems
- Famous Model: RAS XXL Center
- Description: RAS's XXL Center series stands out for its large format bending capabilities, precision, and flexibility in handling oversized sheet metal parts. It is designed for high accuracy and efficiency in large-scale production.
Boschert
- Famous Model: Boschert Powerbend Series
- Description: The Boschert Powerbend series is recognized for its robust design, high-speed bending, and advanced control systems. It ensures consistent and accurate bending results, meeting the demands of modern sheet metal fabrication.
Krrass
- Famous Model: Krrass PBE Series
- Description: Krrass's PBE series offers a balance of affordability, reliability, and advanced bending features. It is suitable for both small-scale and large-scale sheet metal bending operations, providing efficient and precise bending solutions.
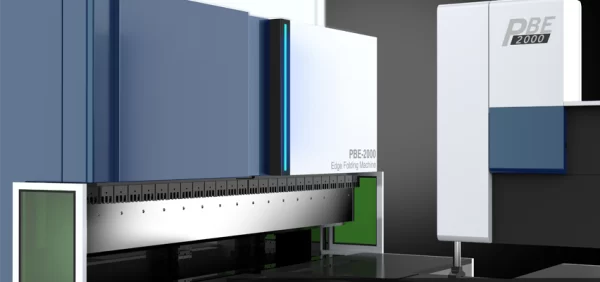
Why Panel Bender Price Is More Expensive
Panel benders represent a significant advancement in sheet metal bending technology, offering distinct advantages over traditional press brakes that justify their higher price points in the market. These machines excel in automation, precision, and efficiency, which are crucial for modern manufacturing demands.
Automation and Precision
Panel benders are equipped with sophisticated CNC systems and automated features such as robotic handling and tool changers. This automation minimizes manual intervention, ensuring consistent and precise bending operations. The ability to adjust bending parameters automatically based on material thickness and other variables enhances overall accuracy, reducing the risk of defects and material waste.
Production Efficiency
Unlike press brakes, which require multiple handling steps for complex bends, panel benders can execute multiple bends in a single setup. This capability significantly speeds up the production process, making them ideal for high-volume manufacturing environments where efficiency is paramount.
Versatility and Capability
Panel benders are designed to handle a wide range of sheet metal thicknesses and complex bending geometries. They can produce intricate bends that may be challenging or impossible for traditional press brakes, making them suitable for diverse applications across industries like aerospace, automotive, and architectural fabrication.
Advanced Features
These machines often feature advanced capabilities such as automatic angle correction, intelligent bending sequences, and integration with CAD/CAM software. Such features not only enhance operational efficiency but also contribute to higher accuracy and consistency in the finished products.
Reduced Labor Costs
The high level of automation in panel benders reduces dependency on skilled labor for operation. Operators can oversee multiple machines or focus on other tasks, leading to long-term savings in labor costs for manufacturers.
Conclusion
In conclusion, the 2024 Latest Panel Bender Price Guide offers a comprehensive market overview and specific price references, aiding both consumers and industry professionals in making informed decisions when selecting and comparing equipment. Whether for startup ventures or established manufacturers, understanding market trends and product advantages will be crucial to making successful purchases.
Reviewed by 2 users
I brought this panel bender machine and asking for the technical support,very helpfully, thank you the team
Panel Bender
We got the Panel Bender Macmine from KRRASS, and after the training and learning of the commissioning personnel, it is very stable.