Tube bending machine is a special mechanical equipment used to bend tubes (such as steel tubes, copper tubes, aluminum tubes, etc.). It applies external force to make the tubes plastically deform according to the predetermined angle and shape to meet the processing needs of different industries.
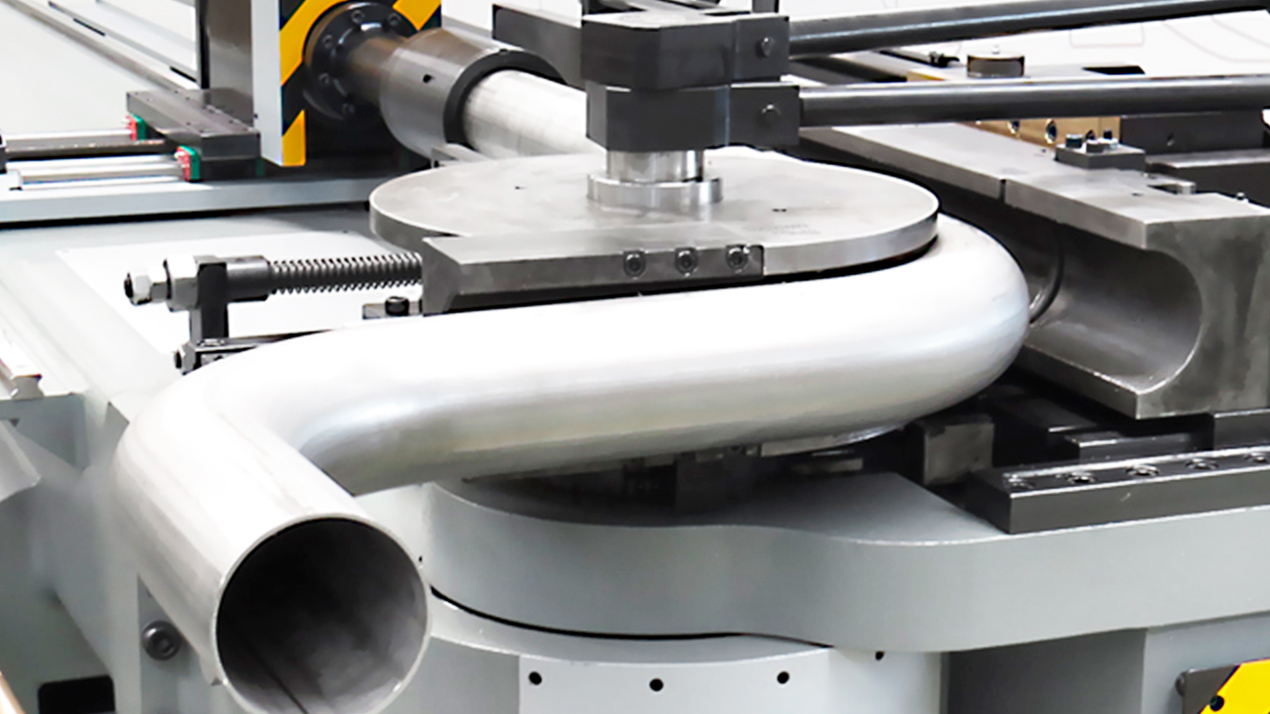
Table of Contents
1.Definition of tube bending machine:
Industrial equipment that bends pipes through mechanical force, hydraulic pressure or CNC systems.Bends straight pipes into specific angles (such as 90°, 180°) or complex curves to meet the shape requirements of pipeline installation, parts manufacturing and other scenarios.
2.Working principle of tube bending machine
The working principle of the tube bending machine is based on the “plastic deformation” characteristics of the tube. The main processes are: fix the tube, put the tube into the mold, and fix it with a clamping device (such as a clamp, chuck) to prevent displacement during bending.
Apply bending force: Use a robotic arm, hydraulic cylinder or servo motor to drive the bending mold to apply continuous pressure to the tube so that it bends around the mold contour.
Accurately control the angle: Stop applying force after the bending angle reaches the preset value in real time through a sensor, encoder or CNC system. Forming and demolding: After the bending is completed, release the pressure and take out the formed tube.
3.Classification of tube bending machines
According to the different driving modes and automation levels, tube bending machines are mainly divided into the following categories:
3.1 Hydraulic Tube Bending Machine
Driving mode: The hydraulic system is used as the power source, and the bending die is pushed by the hydraulic cylinder.
Structure: It consists of an oil tank, a hydraulic pump station, a bending device, a control system, etc.
Features: It has strong power and is suitable for bending large-diameter and thick-walled pipes.
The operation is relatively simple and the price is low. It is suitable for scenes with low precision requirements (such as building pipelines).
The domestic market share is high, but the hydraulic system may have the risk of oil leakage and the maintenance cost is high.
3.2 CNC tube bending machine
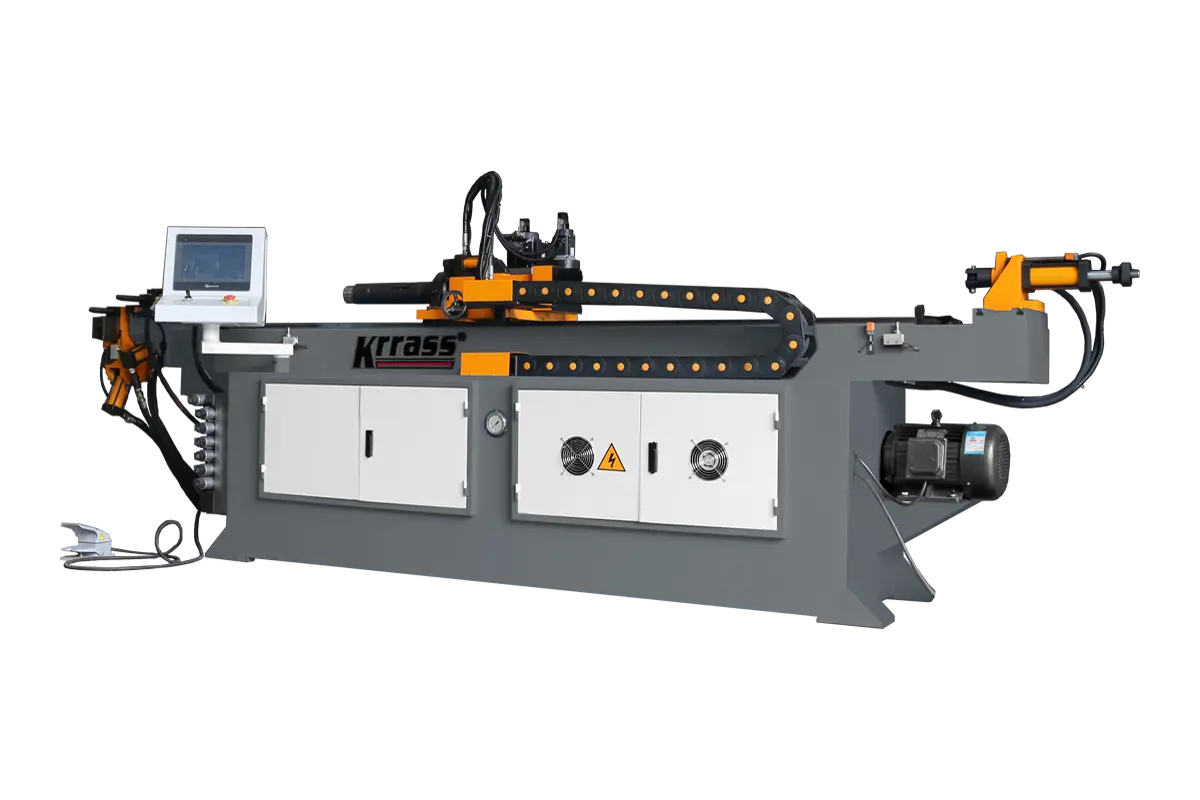
Drive mode: Servo motor or stepper motor is used to control the bending action through computer program (CNC system).
High precision: The bending angle and curvature radius can be accurately controlled, and the error is usually within ±0.5°.
Automation: Bending is automatically completed after inputting parameters, and complex trajectories (such as multi-segment bending and spatial curves) are supported.
High efficiency: Suitable for mass production, reducing manual intervention, and commonly used in aerospace, automobile manufacturing and other fields.
3.3 Fully automatic tube bending machine
Integrated design: It integrates mechanical, electrical and hydraulic systems, and is equipped with PLC (Programmable Logic Controller) and touch screen.
Function: It can automatically complete the whole process of “feeding – positioning – bending – cutting”, and some models support pipe surface treatment (such as deburring).
Application scenario: Large-scale production scenarios (such as furniture pipes, bathroom accessories), with efficiency increased by more than 50% compared with manual or semi-automatic equipment.
3.4 Manual tube bending machine
Driving mode: Manual operation handle or lever to apply bending force.
Features: Simple structure, low cost, but only suitable for small diameter pipes (such as below φ10mm), bending accuracy depends on operating experience, often used in small repairs or DIY scenarios
4.Operation and safety precautions
Before operation: Check whether the equipment is well grounded and whether the hydraulic system oil level is normal.
Confirm that the mold matches the pipe specifications (such as pipe diameter and wall thickness) to avoid mold wear or pipe deformation.
During operation: prohibit the human body from entering the rotation range of the bending mold to prevent pinching.
The hydraulic system pressure must not exceed the rated value (such as 14MPa) to avoid equipment overload damage.
After operation: cut off the power supply, clean the mold and equipment, and lubricate the mechanical parts regularly to extend the service life.
5.How to choose tube bending machine?
5.1 Clarify core needs: starting from the processing scenario
(1) Tube specifications and materials
Pipe diameter and wall thickness:Small diameter (such as φ10-φ50mm): manual tube bending machine or small hydraulic tube bending machine (low cost and easy operation) can be selected.
Large diameter (such as φ50-φ200mm): hydraulic or CNC tube bending machine (sufficient power and controllable precision) is required.
Ultra-thick wall pipe (such as wall thickness > 5mm): servo motor driven CNC machine is preferred to avoid bending deformation caused by insufficient pressure in the hydraulic system.
Material hardness:
Material Type | Recommended model | Reason |
Aluminum tube, copper tube | Manual / hydraulic pipe bending machine | The material is relatively soft and can be formed with ordinary equipment. |
Stainless steel tube, carbon steel tube | CNC tube bending machine (servo drive) | It has high hardness and requires precise control of bending force. |
Alloy steel tube | High precision CNC tube bending machine (with heating function) | It requires auxiliary heating to prevent cracking during bending. |
(2) Bending accuracy requirements
Low precision (±2° or more): hydraulic tube bending machine or semi-automatic model, suitable for building pipes, furniture frames, etc.
Medium precision (±1°-±2°): CNC tube bending machine (basic model), suitable for automobile exhaust pipes and general mechanical pipelines.
High precision (within ±0.5°): servo CNC tube bending machine or fully automatic model, used in aerospace, medical equipment and other fields.
5.2Comparison of key parameters: Determining device performance
(1) Core technical parameters
Maximum bending radius: must be ≥1.5 times the diameter of the pipe (e.g. φ50mm pipe, bending radius ≥75mm) to avoid wrinkling or breaking of the pipe.
Bending angle range: conventional equipment supports 0°-180°. Complex scenarios (such as U-shaped and S-shaped) need to confirm whether they support multi-segment bending and spatial angle adjustment.
Repeat positioning accuracy: CNC models need to be ≥±0.1°, hydraulic models ≥±1°, and manual models do not have rigid requirements.
Feeding length accuracy: Fully automatic models need to pay attention to the accuracy of the feeding system (e.g. ±0.5mm), which affects the consistency of multi-segment bending.
(2)Drive and control mode
Hydraulic drive: suitable for large diameter and low precision scenarios, with low price (50,000-200,000), but high maintenance cost (hydraulic oil needs to be replaced regularly).
Servo motor drive: high precision, fast response, suitable for CNC models (200,000-1 million), suitable for high-precision mass production.
CNC system: brand system (such as Siemens, Fanuc) is preferred, supporting CAD drawing import and program storage (can save more than 100 sets of process parameters).
5.3 Additional functions and configurations
- Mold compatibility: confirm the mold types supported by the equipment (such as single-bend molds, multi-bend molds), and whether it supports fast mold change (change time <10 minutes, improve production efficiency).
Customization requirements: If special bending shapes (such as elliptical arcs, spiral bends) are required, it is necessary to communicate with the manufacturer in advance about the mold customization plan. - Auxiliary functions: anti-wrinkle molds and mandrels: When bending thin-walled pipes (wall thickness <2mm), anti-wrinkle molds or mandrels are required to prevent the inner side of the pipe from denting.
- Deburring device: Fully automatic models can be equipped with a tube cutting and deburring function to reduce subsequent processes (such as manual grinding).
Data traceability: High-end CNC models support production data recording (such as bending times, parameter logs) to meet quality control needs.
6.Tube bending machine brand selection?
Unison, Italy: Five-axis CNC tube bending machine with leading technology, suitable for the aerospace field.
EMHART, USA: High-precision servo tube bending machine, mainly targeting the automotive and medical device markets.
KRRASS: Hydraulic and CNC tube bending machines are cost-effective, with a domestic market share of over 30%. Focus on large hydraulic tube bending machines, suitable for engineering machinery. CNC tube bending machines have an accuracy of ±0.1° and support small and medium batch customization.
Cost budget: balancing performance and price
Machine type | Price range(USD) | Applicable scenarios |
Manual pipe bending machine | 5,000 – 20,000 | Home DIY, small batch repairs |
Hydraulic pipe bending machine | 50,000 – 200,000 | Construction, furniture, general mechanical processing |
CNC pipe bending machine | 200,000 – 600,000 | Automobiles, ships, medical equipment |
Fully automatic pipe bending machine | 300,000 – 1,000,000 | Massive production, production line integration |
High-end five-axis CNC pipe bending machine | 1,000,000 and above | Aerospace, military and other high-precision fields |