Before using the Press Brake, please check the overall condition of the machine. Check if there are any residues in the die area and on the worktable. Check if the upper and lower dies have any defects or cracks. If the die has cracks, it will affect the bending quality of the workpiece.
Test the accuracy of the stopper and the position of the stopper fingers. In addition, test whether all buttons, switches, indicator lights and foot pedal control devices are sensitive. These can be regarded as routine inspection items for each use of the Press Brake. Moreover, some important components require special maintenance.
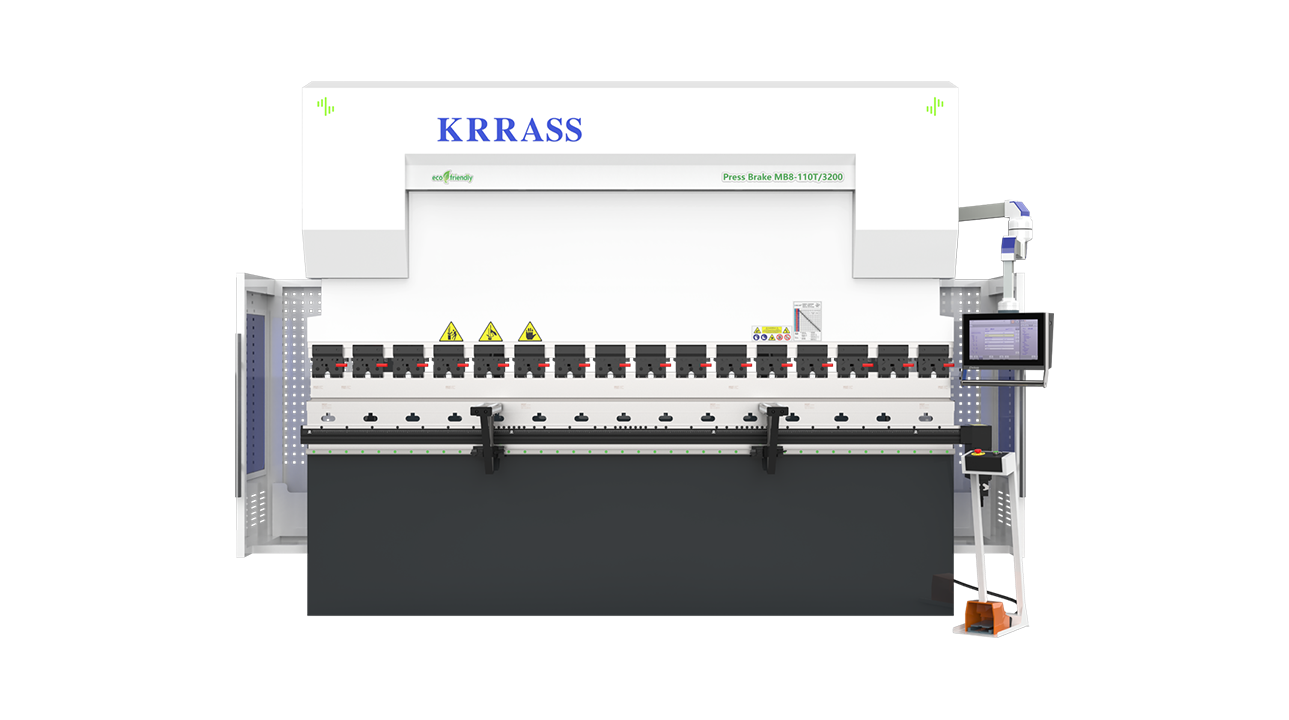
Table of Contents
1.Press Brake Hydraulic Pipeline
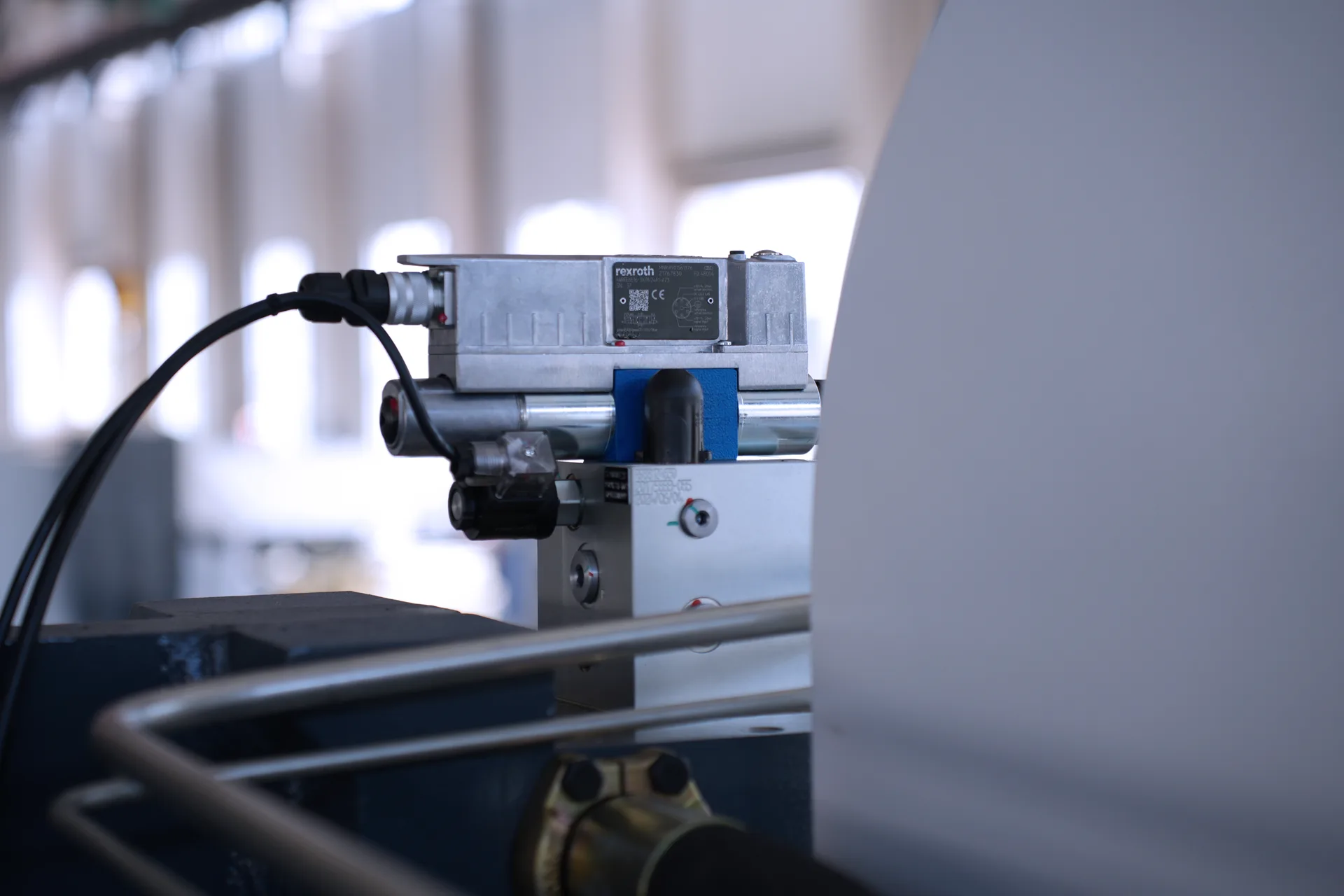
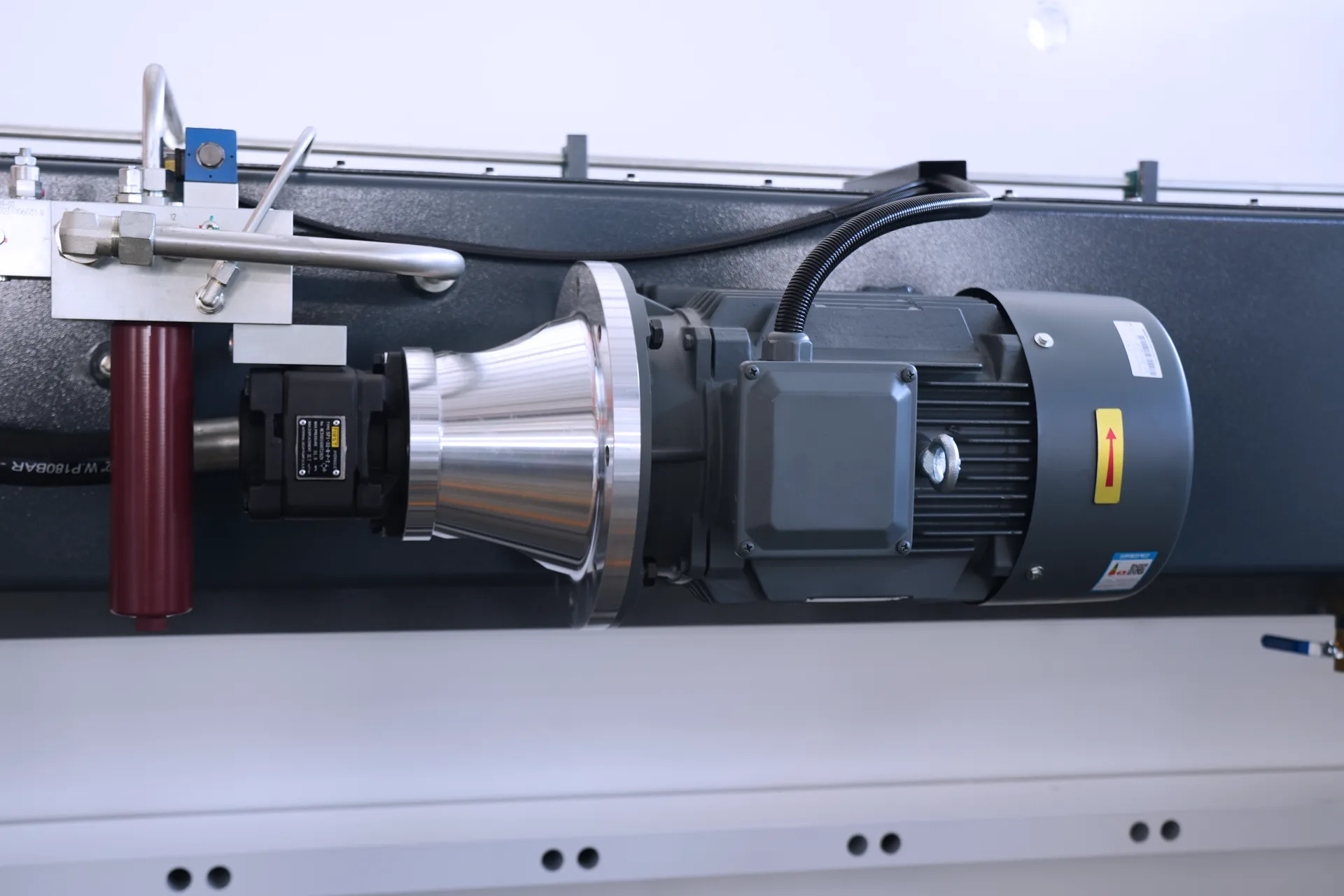
Part of the maintenance for the Press Brake involves checking for any leaks in the hydraulic system and ensuring that the hydraulic oil level is within the recommended range. The hydraulic oil serves as the energy source for the hydraulic system. Keeping the oil and hydraulic circuits clean is extremely important. The hydraulic circuits include the oil tank, valve group, piping, motor, oil pump, etc. When cleaning valves, oil tank covers, and related accessories, it is not recommended to use cleaners.
In addition, it is necessary to visually check the oil level in the oil tank every day to ensure it is within the safe range. Otherwise, it will affect the operation of the hydraulic pump and cause insufficient power to drive the piston. Ensure that the oil tank is well sealed and ventilated.
However, the oil tank cannot be completely sealed. A respirator should be used to prevent the oil tank from creating a vacuum. The purpose of sealing is to prevent particles from entering the oil tank and contaminating the oil. Contaminated oil will clog valves and damage the hydraulic pump, thereby affecting the operation of the hydraulic system.
2.Mechanical Components of Press Brake
Mechanical components must be inspected regularly to ensure the stability of all parts. All bolts, nuts and screws must be tightened regularly and the connection between the piston and the plunger must be checked. Check for cracks in the connection parts of the base and the condition of the rear stop and stop fingers. If necessary, recalibration is required.
3.Press Brake lubrication system
The lubrication of the Press Brake components is an important factor in extending the machine’s service life. Some components of modern Press Brakes may undergo sliding, rolling or friction. Lubrication can reduce friction and damage to the components.
Components that require regular lubrication and cleaning include ball screws, guides, rear clamps, gears, etc. These components should be lubricated at least once a week, and some may even need to be lubricated every day. Other components, such as the guides of the moving crossbeam, need to be lubricated once a year.
However, it is important not to over-lubricate, otherwise it will lead to insufficient friction or component contamination. Before applying lubricating oil or grease, ensure that all components are clean and use the lubricating products recommended by the manufacturer.
4.Press Brake electrical equipment
The maintenance of electrical equipment is of paramount importance for extending the service life of the Press Brake. At least once a year, the entire electrical system, including all electrical connections and switches, should be inspected.
Before inspecting the machine, the main power switch must be turned off. Other inspections can be carried out after the power is connected. When assembling electrical components, keep the components clean and safe.
Check the connection status of the junction boxes and wiring boards on the monitor and relay. Check whether all wires are loose, whether the insulation layer is damaged, and whether the wires are clean and orderly. If the wires are loose, tighten them and clean them with a clean cloth or compressed air.
Inspect the air filters of the electrical cabinet and frequency converter box of the Press Brake, and clean them with compressed air. Check all cables, printed circuit boards and switches. If there is any damage or malfunction, repair or replace them. Check the limit switches and voltage.
Keep the cooling fans and heat exchanger filters clean and in normal operation. Check whether the distribution panel outside the electrical box is closed, and whether the switches, lights and other functions are working properly.
5.Press Brake tool system
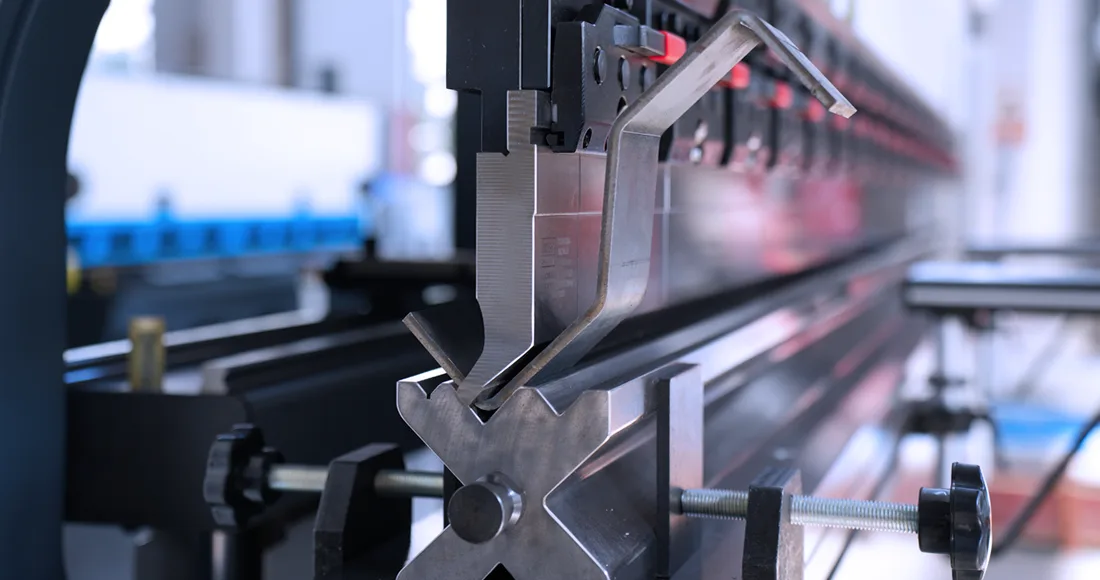
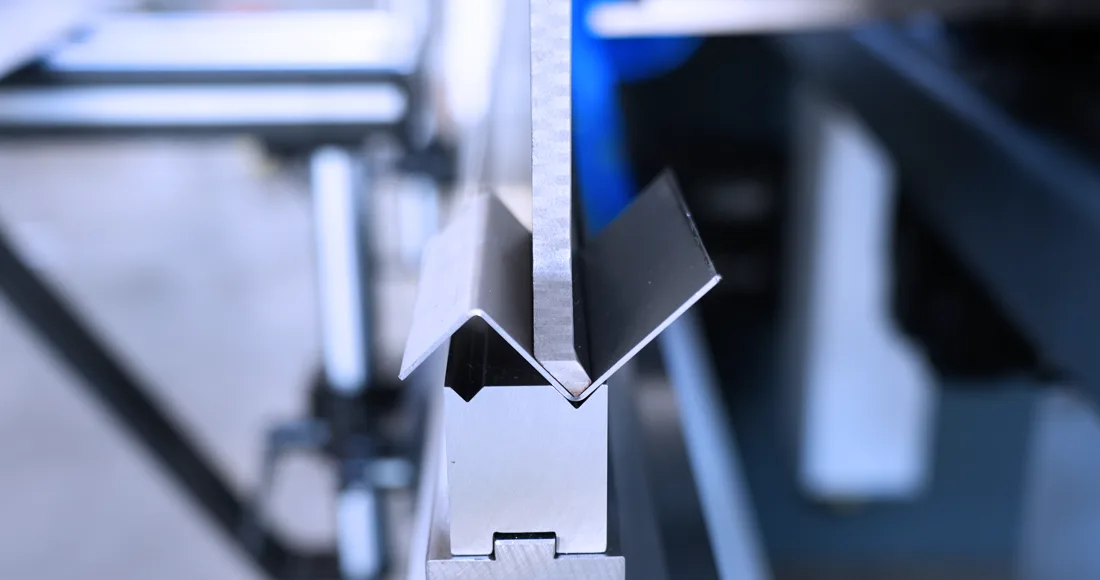
A Press Brake is a machine used for bending various metal sheets. Dust and dirt are the enemies of the entire machine, especially the molds. Keeping the Press Brake clean and tidy is of utmost importance. The punches and molds of the machine will come into direct contact with the sheets, so the material of the molds is particularly crucial. The material of the workpiece also needs to be considered, as materials with chips can wear down the molds.
After use, the punches and molds need to be maintained regularly to prevent rust and corrosion. After each use, wipe the punches and molds with a clean, lint-free towel and alcohol. Press Brake tools should not only be cleaned when replaced, but also cleaned between each use, even if they remain in the machine. Keep the tools clean, free of scale, and visually inspect the tools before each use. This is done to remove fingerprints, as the pH value of the hands can corrode the mold surface.
Then, put on gloves and apply anti-corrosion lubricant to the punches and molds. Finally, put them in the tool box and place at least one bag of silica gel inside. If the punches or molds are damaged, they need to be replaced.
If the Press Brake is equipped with a hydraulic tool clamping system for clamping the punches and molds, the oil level should also be checked regularly.
6.Press Brake BackGauge
Regular maintenance of the backgauge and positioning system is crucial for achieving precise bending results.
Calibration of the backstop
Regularly calibrate the backstop and positioning system to obtain accurate results. Check whether these components are aligned, worn, or damaged, and make necessary adjustments and replacements as needed.
Lubrication of the backstop
Keep the backstop and positioning system well-lubricated to achieve smooth and precise movement.
7.Press Brake Safety and Protection Maintenance
Ensuring the normal operation of all safety systems is crucial for the safe operation of the Press Brake.
Check the safety systems
Check the safety systems every day, including the protective devices and emergency stop buttons, to ensure their normal operation. Confirm that the positions of all protective devices are correct and firmly installed.
Clean the light curtains
Use a lint-free cloth to clean the transmitter and receiver of the light curtain, and check if the wiring connections are loose.
8.Why is it necessary to maintain a Press Brake?
The maintenance of Press Brake helps to extend its service life and reduce costs. The maintenance of Press Brake is mainly divided into several parts, including the hydraulic system, mechanical components, lubrication, electrical equipment and tools.
The importance and benefits of regular maintenance: The service life of Press Brake depends on both product quality and the daily usage by users. Regular maintenance can extend the service life of the machine, prevent failures, reduce the rate of workpiece damage, prevent debris from entering the system, improve machine accuracy and ensure the safety of employees.
The advantages of regular maintenance: Improve machine performance, ensure bending accuracy: Regular maintenance keeps Press Brake calibrated, ensures precise bending, and reduces material waste by minimizing errors in metal forming, ensuring stable performance, preventing parts from being scrapped and reworked, and improving overall production efficiency.
Cost savings through regular maintenance: Active care reduces maintenance: Routine inspections and preventive measures can solve wear problems early, avoiding costly failures and emergency repairs.
Extending machine lifespan: Appropriate maintenance can maximize the service life of the hydraulic system, tools and other components, thereby postponing the need for replacement.
Regular maintenance increases energy efficiency: Good maintenance of Press Brake can improve operating efficiency, reduce energy consumption and operating costs.
Regular maintenance enhances the safety of Press Brake usage: Reduce high-pressure risks: Press Brake operates under high pressure; regular maintenance of Press Brake ensures the normal operation of the hydraulic system, safety functions and electrical components, thereby reducing the risks to operators.
Preventing workplace accidents: Faulty or negligent machines increase the likelihood of accidents. Maintenance can ensure that safety devices, sensors and emergency stop devices are in optimal condition.
Regular maintenance can increase productivity: Minimize downtime: Preventive maintenance can reduce unexpected machine failures, which can disrupt production plans and cause costly delays.
Improve operating efficiency: Well-maintained Press Brake provides stable performance, enabling enterprises to continuously achieve production goals.
9.Brake Maintenance Schedule:
Maintenance schedule | Assignment |
everyday | 1. Check the hydraulic oil level and check for leakage 2. Check whether the connection of electrical components is loose or damaged 3. Check for defects and cracks in the mold and check alignment 4. Clean machine parts, especially hydraulic system 5. Check the condition and alignment of the punch and die |
weekly | 1. Clean the machine and remove accumulated dust or debris 2. Clean and replace the filter when necessary 3. Lubricate all moving parts as recommended by the manufacturer 4. Make a detailed assessment of the overall condition of the machine 5. Check and adjust the alignment of the back stop and plunger |
monthly | 1. Check for signs of wear on the seals and cylinders of the hydraulic system 2. Check for leakage and ensure that the hydraulic pressure and flow are normal 3. Check that the electrical components are not loose or overheated 4. Ensure correct grounding to avoid electrical hazards 5. Check for wear, misalignment or damage to the frame, plunger, bed and rear stop system 6. Thoroughly check the overall condition of the machine 7. Check the condition of the punch and die, clean and lubricate the tool |
semi-annual | 1. Replace the hydraulic oil and filter according to the manufacturers advice 2. Thoroughly check the hydraulic system 3. Review and update the control system software (if any updates are available) 4. Conduct a thorough inspection of all electrical components and connections 5. Perform deep maintenance tasks, such as calibrating machines and performing calibration 6. Check and maintain the guide rail, rear stop, shaft and ball screw 7. Ensure that all tools are in good condition and properly aligned 8. Replace any worn or damaged punches and dies in time |
year | 1. Thoroughly check the overall condition of the machine 2. Test the accuracy of the stop material and the position of the stop finger 3. Carry out a comprehensive inspection and maintenance of the hydraulic system 4. Perform a detailed inspection of all electrical components and connections 5. Thorough inspection and maintenance of all mechanical parts 6. Conduct a comprehensive inspection and maintenance of all tools |