The most important thing when choosing a press brake is the bending accuracy, because product accuracy will affect the market and customer orders, so everyone must pay attention when choosing.
Table of Contents
1.Material factors
- 304L: Ultra-low carbon 304 steel. Reducing the carbon content can improve corrosion resistance, especially the sensitivity to intergranular corrosion after welding. Under the condition of meeting the mechanical strength requirements, it can be used to manufacture welded parts with large cross-sections.
- 304H: Increasing the carbon content to 0.10% increases the strength of 304 steel and makes austenite more stable. It is more suitable for use in low temperature environments and non-magnetic parts than 304 steel.
- 304LN: Adding nitrogen to 304L combines the advantages of 304L and 304N. It has the characteristics of ultra-low carbon and the strengthening effect of nitrogen.
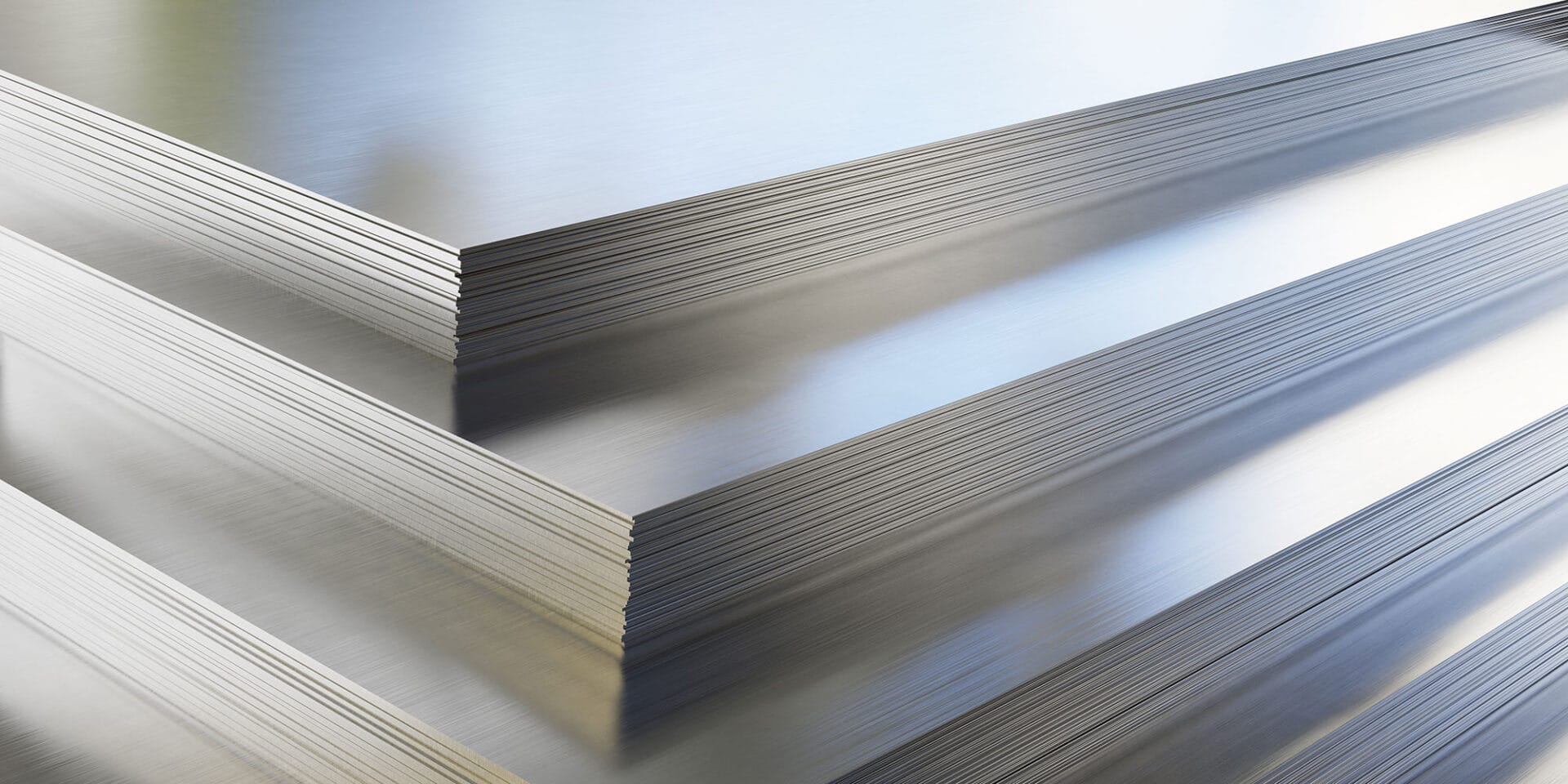
- The physical properties of the bending material, such as hardness, toughness, and elastic modulus, will affect the accuracy of Press Brake processing. Materials with high hardness are difficult to bend, while materials with low toughness are easy to break. In addition, the surface state of the material will also affect the accuracy of Press Brake processing. Uneven surface or the presence of substances such as oxides will cause unbalanced Press Brake processing, thus affecting the processing effect.
- The bending accuracy will also be affected by the thickness of the plate. Too thick plates will cause angle and size errors during the bending process; at the same time, some suppliers lack strict control over the quality of the plates when leaving the factory, and the thickness of the same plate is inconsistent. The consistency of plate thickness is crucial for uniform bending. Changes will cause one side of the material to bend more than the other side, resulting in uneven final products.
- The mechanical properties of the material and the uneven distribution of components will cause different shapes and sizes of the workpieces bent from the same sheet material due to different stress and rebound values, which will cause certain dimensional deviations.
- The uneven thickness of the material will result in different sizes and shapes of the workpieces even if the same bending die is used for bending. The thicker the material, the greater the resistance during bending and the smaller the springback; the thinner the material, the greater the springback, and the inaccurate shape and size, which affects the accuracy of the workpiece and is prone to warping and twisting.
2.Press Brake Mold Factors
- Material: 42CrMo is a high-strength alloy tempered steel with high strength and good toughness. It can work below 500 degrees.
- Hardness: After tempering, the typical hardness is 25~35HRC (Rockwell hardness), depending on the tempering temperature. If the tempering temperature is increased, the hardness will decrease and the toughness will increase; if the tempering temperature is reduced, the hardness can be increased to 38~42HRC, but the toughness will decrease.
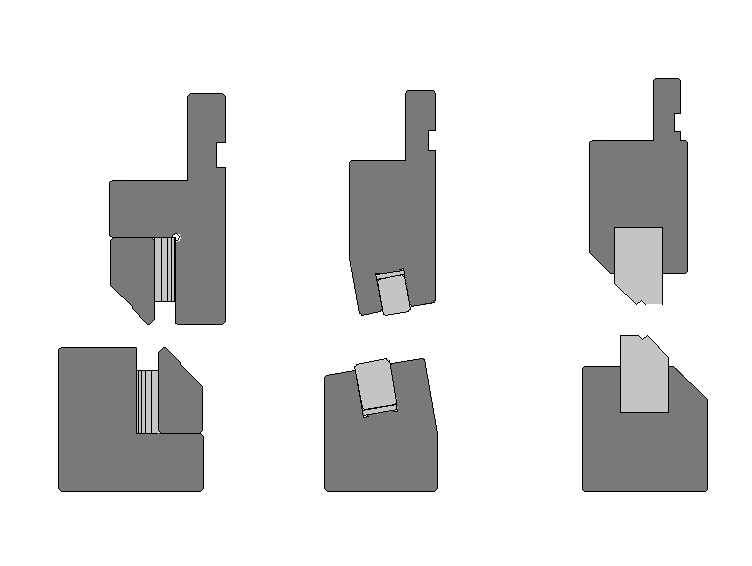
- The shape of the mold has a direct impact on the bending angle. For example, the V-shaped mold has different opening sizes and depths of the V-shaped groove, and the bending angle will be different. If the V-shaped groove opening is large, when bending the same sheet, the bending force on the sheet in the mold is relatively dispersed. To achieve the same bending angle, greater pressure is required, and the accuracy of the bending angle may be relatively low. On the contrary, the V-shaped groove opening is small, the bending force is concentrated, it is easier for the sheet to reach the set bending angle, and the accuracy can be better controlled. For example, when making small metal parts, a V-shaped mold with a smaller opening and higher accuracy is required.
- The material of the mold also affects the bending angle. The mold hardness and wear resistance of different materials are different. For example, carbide molds have high hardness and strong wear resistance. During long-term bending operations, the deformation of the mold itself is minimal. This makes it possible to apply pressure to the sheet stably during the bending process to ensure the consistency and accuracy of the bending angle. If the mold is made of ordinary steel, the mold is prone to wear as the number of uses increases, especially at the bending angle. After wear, the shape of the mold changes, and the bending angle will deviate from the design value. In the mass production of automotive parts, due to the extremely high precision requirements for the bending angle, carbide molds are preferred to ensure product quality.
- The gap of the mold is also a key factor. The size of the gap between the upper and lower molds determines the degree of deformation of the sheet during bending. If the gap is too large, the sheet will have a larger space for movement during the bending process, and the bending force will have an unstable effect on it, making it difficult to control the bending angle, and the angle may be too large or irregular. If the gap is too small, the friction force on the sheet increases, and it is easy to scratch the surface, and excessive pressure may cause the sheet to deform excessively, and the accurate bending angle cannot be obtained. Taking the thin plate of the electrical housing as an example, the appropriate mold gap can make the angle after bending accurately meet the design requirements and ensure the assembly accuracy of the housing.
- The design structure of the mold will affect the bending angle. Some complex molds have adjustable parts or special positioning devices. For example, a mold with a fine-tuning structure can adjust the position or angle of the mold in a small range according to the actual situation during the bending process, so as to correct the bending angle in time. This kind of mold is often used in the production of high-precision aviation parts and can meet strict angle tolerance requirements. Simple-structured molds may lack these adjustment functions. When encountering slight changes in the thickness of the sheet or other interference factors, the bending angle is prone to deviation.
- The surface roughness of the mold is also related to the bending angle. The mold surface is smooth, the friction between the sheet and the mold surface is uniform when bending, the bending process is smoother, and it can better deform according to the shape of the mold, thereby ensuring the accuracy of the bending angle. If the mold surface is rough and the friction is uneven, the sheet may be partially stuck or slide abnormally when bending, resulting in deviations in the bending angle. When making metal parts for precision instruments, the surface roughness of the mold is extremely high. Through fine grinding, the mold surface is smooth to obtain a precise bending angle.
- The wear of the mold is directly reflected in the bending angle. As the number of times the mold is used increases, the working surface of the mold will gradually wear out. Especially at the bending edges, the wear is more obvious. The shape and size of the worn mold change, and the bending angle of the mold that can accurately bend a specific angle will deviate. For example, when producing a large number of metal doors and windows for construction, if the mold is not maintained and replaced in time after long-term use, the angle of the bent door and window frame will not meet the installation requirements.
- The debugging of the mold has a great influence on the bending angle. Before the new mold is put into use, it needs to be finely debugged. The debugging process includes adjusting the pressure, stroke, positioning and other parameters of the mold. If the debugging is not in place, such as inaccurate pressure setting, excessive pressure may cause the sheet to bend excessively, and the angle exceeds the design value; if the pressure is too small, the sheet cannot reach the predetermined bending angle. Only after repeated debugging and finding the most suitable parameter combination can the accuracy of the bending angle be guaranteed. For example, when producing metal frames for large mechanical equipment, mold debugging is particularly important. Once the debugging is not good, the assembly of the entire frame will have problems.
- The heat treatment process of the mold will affect its performance, and then affect the bending angle. The mold that has been well heat treated has a uniform internal structure and suitable hardness and toughness. Such a mold can withstand greater pressure during the bending process without deformation, ensuring the stability of the bending angle. For example, the comprehensive mechanical properties of the mold after quenching and tempering are improved, and when bending high-strength alloy steel, it can be stably bent to the specified angle. However, molds that are improperly heat treated may have uneven hardness or insufficient toughness, which is easy to be damaged during bending, and the bending angle cannot be guaranteed to be accurate.
- The dimensional accuracy of the mold determines the initial setting of the bending angle. If there is an error in the size of the mold itself, the bending angle will inevitably be affected. For example, if the bending radius of the mold is inaccurate, the bending deformation path of the plate during bending will change, and ultimately the bending angle will not match the design angle. When making high-precision electronic component housings, the mold dimensional accuracy is extremely high. Any slight dimensional error may cause a deviation in the bending angle, affecting the assembly and performance of the component.
- The clamping method of the mold is also related to the bending angle. If the clamping is not firm, the mold may shift or shake during the bending process, making the force on the plate unstable during bending, and the bending angle is difficult to control. The correct clamping method can ensure the stability of the mold during the working process, so that the sheet can be bent in the expected direction and angle. For example, when using large bending equipment, the mold is firmly fixed on the workbench by a suitable clamp to prevent the mold from loosening during high-pressure bending and ensure the accuracy of the bending angle.
- The lubrication condition of the mold will also indirectly affect the bending angle. Good lubrication can reduce the friction between the sheet and the mold, so that the sheet can deform more smoothly during the bending process. When the lubrication is insufficient, the friction increases, the deformation of the sheet is hindered, and the bending angle may deviate. In some processes that have high requirements for surface quality and bending angle accuracy, special lubricants are used to ensure the smooth progress of the bending process and the accuracy of the angle. For example, when producing metal parts for high-end kitchenware, proper lubrication can make the surface of the bent parts smooth and the angle accurate.
- The maintenance of the mold is related to the long-term stability of the bending angle. Regular cleaning, inspection and maintenance of the mold can timely detect and deal with problems such as mold wear and deformation, and ensure that the mold is always in good working condition. If the mold maintenance is neglected, the performance of the mold will gradually decline and the deviation of the bending angle will become larger and larger. For example, in the automobile manufacturing industry, there are strict systems and processes for mold maintenance. Through regular maintenance, it is ensured that the mold can bend parts that meet the precision requirements during the long production process.
3.Press Brake Mechanical Factors
- Mold wear and installation accuracy: The long-term use of Press Brake molds will cause the V-groove to become larger or irregular due to wear, affecting the fit between the plate and the mold, resulting in uneven force on the workpiece and deformation. In addition, the wear of the R angle of the mold will also change the force situation at the bending point, affecting the bending effect. The installation accuracy of the mold is also very important, and even a slight deviation may cause an error in the bending angle.
- Degradation of equipment accuracy: The mechanical parts of the Press Brake, such as the slider, guide rail, and workbench, will experience wear and looseness after long-term use, causing changes in the straightness and verticality of the mechanical parts, affecting the uniform force during bending, and causing deformation of the workpiece. The reduction in the accuracy of the control system will also cause the actual bending parameters to be inconsistent with the set parameters, resulting in deformation of the workpiece.
- Mechanical structure design: The mechanical structure design of the Press Brake directly affects its accuracy. For example, the straightness of the clamping opening of the slider, the verticality and inclination of the frame, etc. all need to be precisely controlled. In addition, the connection between the cylinder and the slider, the strength and accuracy of the frame and the slider will affect the bending accuracy.
- Measures to improve the bending accuracy include:
- Regularly check and maintain mechanical parts: Ensure that the straightness and verticality of components such as sliders, guide rails, and workbenches are kept within a reasonable range.
- Use advanced CNC system: The intelligent CNC system can control the stroke and speed of the slider according to the pre-entered program instructions to achieve precise control of the bending angle. The real-time monitoring function can feedback the bending angle data through the sensor, and correct it immediately once the deviation is found.
- Choose a suitable mold: Choose a suitable mold according to the material, thickness and shape of the workpiece, and ensure that the surface roughness and dimensional accuracy of the mold meet the requirements. Calibrate before installing the mold to ensure flatness and verticality. 2.
- Adjust process parameters: Reasonably set the bending force, bending radius and bending speed to avoid workpiece deformation caused by improper parameter settings.
4.Bending process factors
- When the number of processes for bending workpieces increases, the cumulative error caused by the deviation of each process will increase. In addition, the different order of arrangement of the processes will also have a great impact on the accuracy.
- The installation, adjustment and proficiency of the bending die in the process operation have an impact on the accuracy of the workpiece. If the installation is inaccurate, not only will the quality of the workpiece be reduced, but also a lot of waste will be caused. In addition,
- the accuracy of feeding during operation and the accuracy of blank positioning will affect the shape and size accuracy of the workpiece.
- The influence of workpiece shape and size on accuracy The deviation of bending parts with asymmetric shapes and large outer dimensions will increase significantly.
- The main reason for the impact of the press on the accuracy of the workpiece is the elastic deformation of the material:
- During the bending process of the material, the inner layer of the plate is subjected to pressure, while the outer layer is subjected to tensile stress. These two stresses cause the material to undergo plastic bending deformation, and there is always an elastic section in the process of transitioning from tensile stress to compressive stress. Since elasticity inevitably causes a tendency to straighten to the original position, the material rebounds after unloading.
- When sheet metal is bent, plastic deformation must be accompanied by elastic deformation. When the stress does not exceed a certain limit (proportional limit), stress and strain are directly proportional, so a part of the total deformation must be restored after unloading, that is, springback occurs.
5.Equipment factors:
The quality, structure, and precision of the Press Brake will also affect the processing accuracy. The higher the rigidity of the equipment, the higher the processing accuracy. At the same time, the accuracy and stability of the equipment will also have an important impact on the processing accuracy. For example, the hydraulic system, control system, transmission system and other components of the equipment need to ensure accuracy and stability.
In summary, the factors that affect the Press Brake processing accuracy mainly include materials, processes, equipment, etc. In the actual processing process, it is necessary to comprehensively consider these factors, and perform reasonable parameter settings and equipment maintenance to ensure the accuracy and stability of Press Brake processing.