Laser cutting machine: Laser cutting machine is an advanced processing equipment that uses a high-energy-density laser beam as a "cutting tool" to accurately cut materials. Its core principle is to generate a high-intensity laser beam through a laser. After being focused by the optical system, a very small focus is formed on the surface of the workpiece (the diameter is usually only a few microns to tens of microns). The energy density at the focus is extremely high (up to 10^6 - 10^8 W/cm²), which can instantly heat the material to thousands or even tens of thousands of degrees Celsius, causing the material to melt, vaporize or burn quickly, and use high-pressure gas (such as nitrogen, oxygen, compressed air, etc.) to blow the molten or vaporized material away from the cut, thereby achieving the cutting of the material. Compared with traditional mechanical cutting (such as sawing, shearing, milling, etc.), laser cutting machine has high cutting accuracy (positioning accuracy can reach 0.01mm level), smooth incision (no secondary processing required), fast cutting speed, wide material adaptability (can cut metals, non-metals, composite materials, etc.), strong flexibility (can cut complex shapes, and can achieve automated processing with CNC systems) and other significant advantages.
Hydraulic shearing machine: Hydraulic shearing machine has become the mainstream equipment for shearing of medium and thick plates due to its high efficiency, precision and stability. It is especially widely used in industrial fields with high precision requirements.
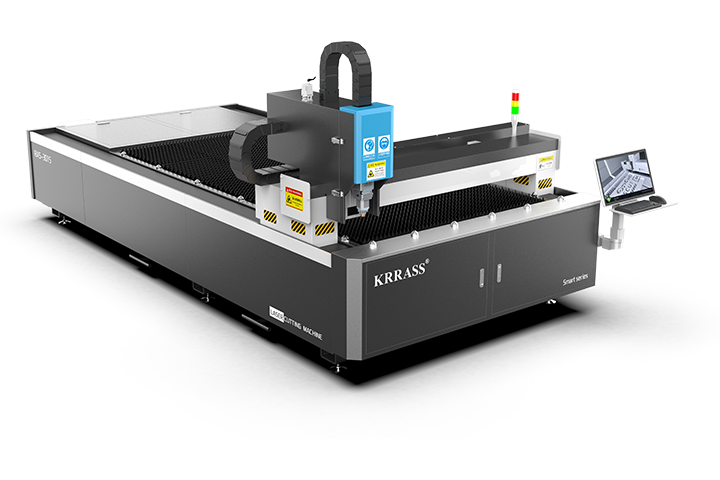
Fiber Laser Cutting Machine
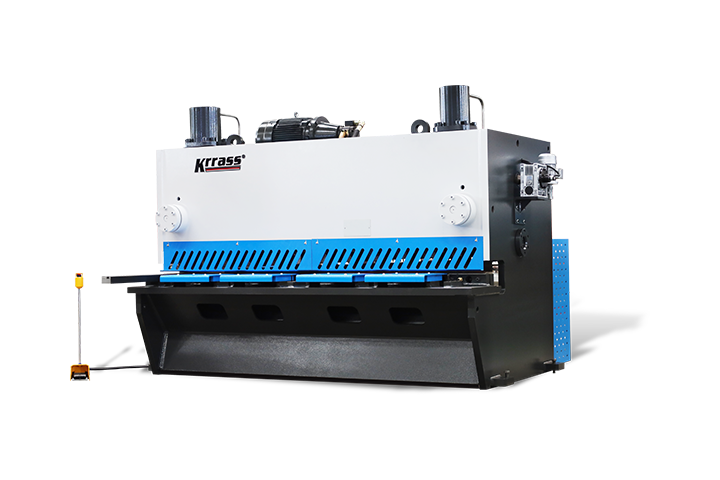
Hydraulic Guillotine Shearing Machine
Table of Contents
1.The advantages of Fiber Laser Cutting Machine
More and more people are replacing hydraulic shearing machines with laser cutting machines, mainly because laser cutting machines have significant advantages in processing efficiency, cutting accuracy, material utilization, processing flexibility, and safety. The specific advantages are as follows:
1.1 High processing efficiency: Laser cutting machine have a high degree of automation and can operate continuously for 24 hours. Operators only need to supervise the equipment. In contrast, hydraulic shearing machines have a low degree of automation and require multiple manual operations, resulting in lower processing efficiency.
1.2 High cutting accuracy: Laser cutting machine use laser beams for cutting, with narrow cuts ranging from 0.1 to 0.3 mm. The cutting accuracy is high, the cuts are smooth and flat, without burrs, and the heat affected zone is small, with minimal material deformation. hydraulic Shearing machines are prone to mechanical stress during cutting, resulting in relatively lower cutting accuracy, especially in scenarios with high precision requirements. Shearing machines are difficult to meet the needs for some complex patterns.
1.3 High material utilization: Laser cutting machines can automatically arrange materials using programming software, arranging any patterns on the sheet and even cutting in the unused materials without waste. This maximizes material utilization. In contrast, hydraulic shearing machines require manual cutting of patterns, making it difficult to achieve precise layout and prone to material waste.
1.4High processing flexibility: Laser cutting machines can cut various complex two-dimensional and even three-dimensional patterns. As long as the designed patterns are input into the computer, the machine can process according to the requirements, without being limited by the cutting patterns. Shearing machines are mainly used for linear cutting and are difficult to complete cutting tasks for some complex irregular patterns.
1.5High safety: During operation, hydraulic shearing machines require manual lifting of materials and positioning, which can easily lead to accidents such as cutting hands or foot injuries. Laser cutting machines use non-contact processing, and operators do not need to directly contact the cutting area, significantly reducing safety risks.
1.6Lower overall costs: Although the initial purchase cost of laser cutting machines is higher, due to their high processing efficiency, high material utilization, and reduced secondary processing, the overall operating costs are relatively lower in the long run. While the equipment cost of shearing machines is relatively lower, the costs in terms of labor costs and material waste are higher.
2.What materials are suitable for laser cutting machines and hydraulic shearing machines?
There are significant differences in the applicable materials for laser cutting machines and shearing machines, which are closely related to their working principles (laser cutting is non-contact thermal processing, while shearing machines are mechanical force shearing). The following are the classification and characteristics of the applicable materials for both:
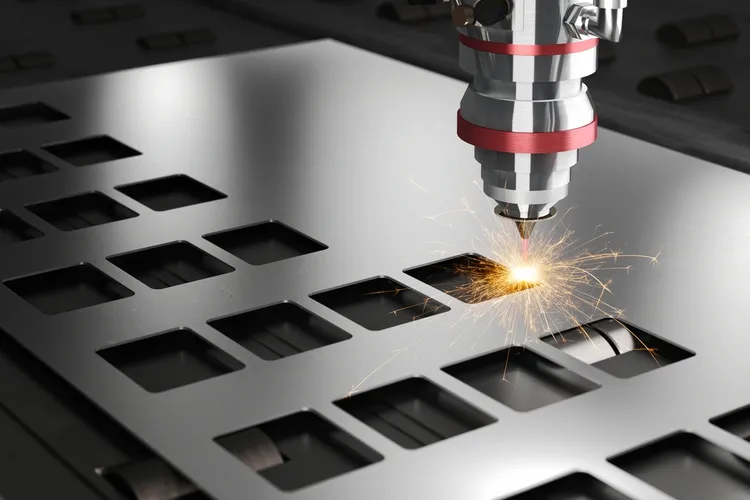
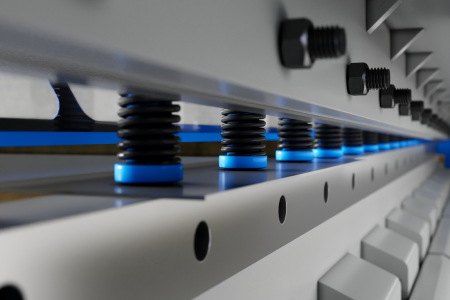
Summary Comparison Table:
Equipment Type | Core Applicable Materials | Processing Form Restrictions Typical | Application Scenarios |
Laser Cutting Machine | Metal (steel, aluminum, copper, etc.), Non-metal (plastic, wood, fabric, etc.) | Flat plate, pipe, can cut complex shapes | Precision parts, irregular parts, advertising decoration, electronic components |
Hydraulic Shearing Machine | Medium-thin plate metal (carbon steel, stainless steel, aluminum plate, etc.) | Only flat plate, can only perform straight-line cutting | Steel plate cutting, batch rectangular part shearing |
In summary, the Laser Cutting Machine is suitable for high-precision processing of multiple materials and complex shapes, while the Shearing Machine is suitable for batch linear cutting of single metal plates. These two machines are often used together in industrial settings (for example, after the Shearing Machine performs rough cutting, the Laser Cutting Machine then performs precise processing on the irregular parts).
3.What should be noted when choosing between Laser Cutting Machine and Hydraulic Shearing Machine?
When choosing between the Laser Cutting Machine and the Hydraulic Shearing Machine, it is necessary to make a comprehensive judgment based on one's own processing needs, equipment characteristics, and actual production scenarios. The core difference between the two lies in the processing methods (laser thermal cutting vs mechanical shearing), so the emphasis when making a choice also varies. The following are specific precautions:
3.1Key Considerations for Selecting a Laser Cutting Machine
A Laser Cutting Machine is suitable for complex shape cutting and high-precision processing, especially for handling non-metallic materials, thin sheet metals, and irregular parts. When choosing one, the following aspects should be given priority attention:
(1)Processing Requirements Match
Material Thickness:
Thin sheet (≤3mm): 1000W to 2000W fiber laser is sufficient;
Medium-thick sheet (3 to 20mm): 3000W to 6000W fiber laser;
Ultra-thick sheet (20mm or more): 8000W + high-power fiber laser (cost and efficiency need to be balanced).
Processing Shape and Precision:
Complex shapes (such as curves, hollowing, and irregular parts): Must select laser (hydraulic Shearing Machine cannot complete this);
High Precision Requirements (±0.02mm or less): Select small-power fiber laser (combined with high-precision guideways and servo systems).
(2)Equipment Performance Parameters
Laser Generator: Prefer brands with strong stability (such as IPG, Ruike, Chuangxin), avoid frequent power outages or power attenuation;
Motion System: Guide rails (Taiwanese Yusheng, Yitai) and lead screws determine the cutting stability, the repeatability positioning accuracy should be ≤±0.03mm;
Cooling System: Water cooler temperature control accuracy should be ±1℃ (especially for high-power equipment, to avoid overheating and damage to the laser head);
Software and Control System: Supports AutoCAD, DXF formats import, has automatic layout (saves materials) and path optimization functions (improves speed).
(3)Cost and Operating Efficiency
Initial Investment: Fiber laser (1000W) costs approximately 15 to 30 thousand yuan, high-power (8000W+) can reach millions of yuan, much higher than Shearing Machine;
Operating Cost: Electricity consumption (10 to 30 kWh per hour), consumables (lenses, cutting nozzles, gases) approximately 2000 to 5000 yuan per month, higher than Shearing Machine (mainly due to high electricity consumption);
(4)Additional Conditions
Space and Environmental Protection: Reserve 10 to 20 square meters of space, equip an exhaust and dust removal system (metal dust and non-metal exhaust gases need to be treated to avoid environmental violations);
After-sales Service: Prefer brands with local service points (such as Daqu, Huagong), ensure on-site repair within 48 hours (laser equipment failures have a significant impact on production);
Expandability: Whether it supports later upgrades (such as upgrading from 3000W to 6000W), whether it can be equipped with pipe cutting function (suitable for pipe material processing needs).
3.2Key Considerations for Selecting the Hydraulic Shearing Machine
Hydraulic Shearing Machine is suitable for simple linear shearing and batch processing of thick plates. When choosing, focus on the mechanical performance and shearing stability:
(1)Matching of processing requirements
Material type: Limited to metal plates (carbon steel, stainless steel, etc.), and must be flat plates (cannot shear pipe materials or special-shaped parts);
Material thickness and length:
Material thickness and length:
Thickness: Mechanical Shearing Machine is suitable for ≤ 6mm thin plates, hydraulic Shearing Machine can shear 6~20mm medium-thick plates, and ultra-thick plates (20mm and above) require a dedicated heavy-duty hydraulic shear;
Length: Select the cutting length based on the plate size (such as 1.6m, 2.5m, 4m), ensuring that the plate width is covered in a single cut (avoiding secondary cutting).
Processing accuracy: The Shearing Machine has lower shearing accuracy (±0.1mm to ±0.5mm), and is only suitable for simple straight cutting (such as steel plate cutting, pre-processing before simple bending);
(2)Equipment performance parameters
Drive method:
Mechanical Shearing Machine: Low cost (about 5-15 thousand yuan), suitable for thin plates and small-batch processing, but the shearing force is unstable (Prone to "corner collapse");
Hydraulic Shearing Machine: Uniform shearing force (suitable for thick plates), higher accuracy (about ±0.1mm), higher price (10-30 thousand yuan), recommended to be chosen first.
Tool holder and blade: The blade material should be high-speed steel or alloy tool steel (wear-resistant), the gap of the tool holder can be adjusted (suitable for different thickness materials, avoiding burrs);
Safety device: Must be equipped with a guard hand device and an emergency stop button (the mechanical shearing force is large, avoiding work-related injuries).
(3)Cost and operational efficiency
Initial investment: Much lower than Laser Cutting Machine (mechanical shear starts at 5 thousand yuan, hydraulic shear starts at 10 thousand yuan), suitable for small and medium-sized manufacturers with limited budgets;
Operating cost: Mainly electricity consumption (hydraulic shear about 5-10 degrees per hour), only regular replacement of blades is required (about 500-1000 yuan per month), maintenance is simple;
Efficiency adaptation: Only suitable for batch linear shearing (such as steel plate batch cutting), if the size or shape needs to be frequently changed, the efficiency is much lower than laser (requires manual adjustment of the tool holder, time-consuming).
(4)Additional conditions
Site requirements: The equipment weight is large (hydraulic shear can reach several tons), the ground bearing capacity should be ≥ 5 tons / square meter;
Brand and after-sales: Prefer to choose domestic mature brands (such as Yangzhou Forging Press, Shanghai Shearing), warranty period ≥ 1 year, support blade replacement and hydraulic system maintenance;
Manual reliance: Requires skilled workers to operate (adjusting the shearing gap, positioning the plate), the labor cost is high (laser can automate loading and unloading, reducing labor).
4.How to Determine Whether to Choose Laser or Hydraulic Shearing Machine?
Demand scenario | Choose the Laser Cutting Machine first | Choose the Shearing Machine first |
Processing shape | Complex graphics, curves, hollowing out, and irregular parts | Simple straight-line cutting (rectangles, squares, etc. regular shapes) |
Material thickness | Thin plates ( ≤ 10mm) are the main type, while medium-thick plates (requiring high power) are also taken into consideration. | Medium-thick plates (6~20mm) are the main type, especially for batch shearing of thick plates. |
Precision requirement | High (within ± 0.02mm, such as for precision parts) | Low (above ± 0.1mm, for rough cutting during material removal) |
Production batch size and variety | Small batch, multiple varieties (flexible model change) | Large batch, single variety (linear cutting with repetitive operations) |
Budget | Can bear a relatively high initial investment (150,000 +) | Budget is limited (within 100,000) |
When making a choice, it is necessary to closely focus on the core contradiction of the processing requirements: If the core is "complex shapes and high precision", and the budget is sufficient, choose the Laser Cutting Machine; if the main focus is "simple straight cutting and batch processing of thick plates", and the budget is limited, choose the Hydraulic Shearing Machine. When necessary, the two can be combined (laser processing for complex parts, Shearing Machine for batch straight parts), maximizing production efficiency.