Working Principle of Ironworker Machine: The hydraulic oil is pressurized by the hydraulic pump station and flows to each hydraulic cylinder, pushing the pistons to move, thereby converting hydraulic energy into mechanical energy to drive the punch and shears for punching and shearing operations. The hydraulic system has overload protection function. When the load exceeds the set value, it will automatically relieve pressure to prevent the equipment from being damaged due to overload.
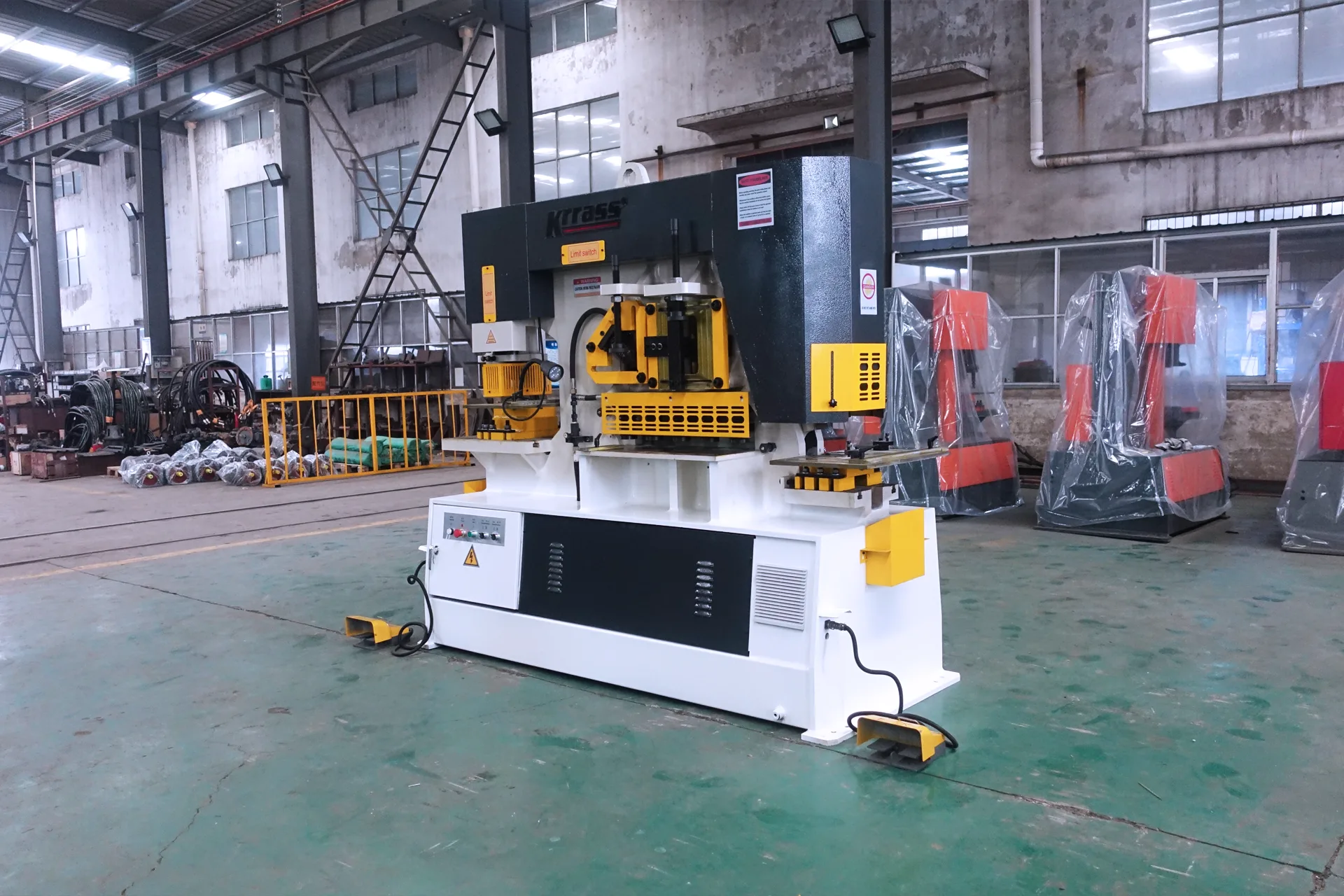
Table of Contents
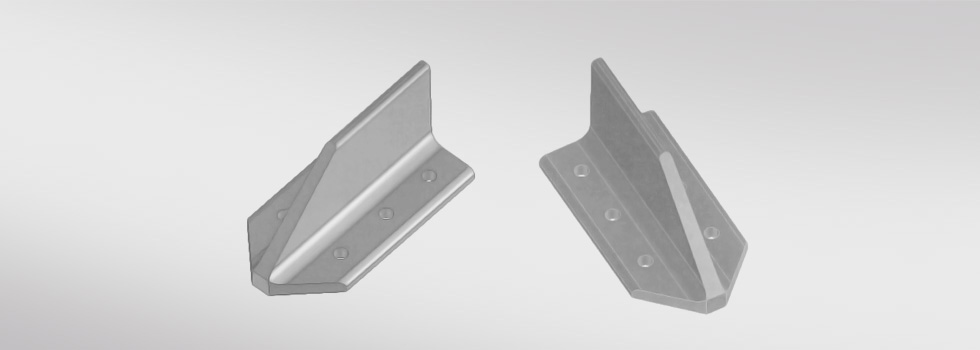

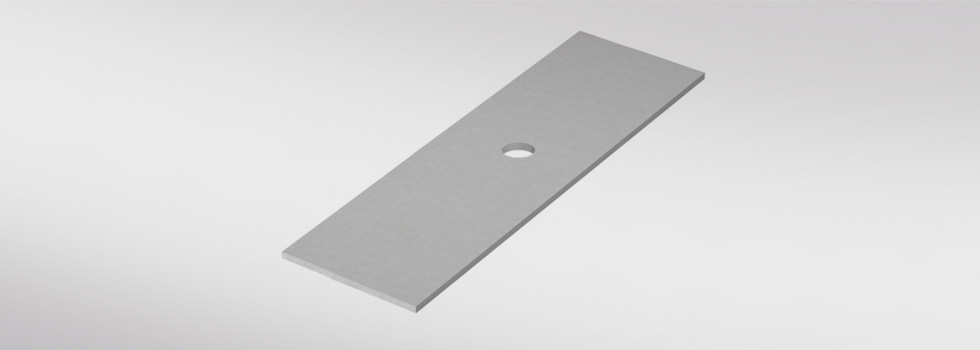
The structural composition of the Ironworker Machine
Ironworker Machine Power System: Mainly composed of a hydraulic pump station, motor, etc. The motor drives the hydraulic pump station to convert mechanical energy into hydraulic energy, providing power for various actions of the equipment.
Ironworker Machine Power System: Mainly composed of a hydraulic pump station, motor, etc. The motor drives the hydraulic pump station to convert mechanical energy into hydraulic energy, providing power for various actions of the equipment.
Ironworker Machine Control System: Used to control the operation of the hydraulic combined punching and shearing machine, including operation buttons, foot switches, PLC controllers, etc., which can achieve functions such as starting, stopping, speed regulation, and control of action sequences of the equipment.
Ironworker Machine Machine Body Structure: Usually adopts a fully welded steel plate structure, which has undergone stress relief treatment and fine processing, with high strength and rigidity, ensuring the stability of the equipment during operation.
Performance Characteristics of the Ironworker Machine
Strong processing capacity of The Ironworker Machine: It can process various metal materials, including plates, channel steel, angle steel, round steel, square steel, etc., and complete multiple processing procedures such as punching, shearing, and corner cutting. Some models can also perform plate bending and die shearing operations.
High precision of The Ironworker Machine : Hydraulic transmission features smooth transmission and high precision, which enables better control of precision indicators such as the verticality of punching and the straightness of shearing, resulting in higher quality of processed parts.
Easy operation of The Ironworker Machine: Equipped with a user-friendly operation interface and control devices, such as foot switches and buttons, operators can easily control the operation of the equipment and complete various processing tasks, reducing the technical requirements for operators.
Good safety of The Ironworker Machine: Usually equipped with multiple safety devices, such as interlocking guards for workstations, emergency stop buttons, and light curtains for protection, which can effectively prevent operators from accidents during equipment operation and ensure their personal safety.
Low noise of The Ironworker Machine: Compared with mechanical combined punching and shearing machines, hydraulic combined punching and shearing machines generate lower noise during operation, generally below 75 dB, improving the working environment.
Operating Instructions for the Ironworker Machine
(1) Before starting the machine, check if the transmission components, connecting screws and pin shafts are loose, and ensure that the electrical grounding is intact.
(2) Before operation, lubricate all parts and conduct a 2-3 minute trial run of the machine. Confirm there are no issues before putting it into operation.
(3) Do not operate beyond the load capacity. Do not shear quenched steel.
(4) During operation, wear appropriate labor protection equipment such as gloves. Do not wear sandals or slippers.
(5) During shearing and punching, frequently apply oil to the punch and die to prevent them from tilting.
(6) When feeding materials, pay attention to hand safety. When the press foot cannot press the material at the end of the sheet, do not perform shearing and punching.
Maintenance Tips for Ironworker Machines
(1) Operate strictly in accordance with the operating procedures to avoid equipment damage caused by improper operation.
(2) Before each startup, add lubricating oil at regular intervals, at fixed points and in fixed quantities as per the lubrication chart requirements. The oil should be kept clean and free of sediment.
(3) Regularly clean the equipment and apply anti-rust grease to the unpainted parts to prevent rusting.
(4) Replace the lubricating grease in the motor bearings regularly and frequently check whether the electrical parts are normal, safe and reliable.
(5) Regularly inspect whether the V-belts, handles, knobs, buttons and other components are damaged. Severely worn ones should be replaced promptly and spare parts should be reported for replenishment.
Application fields of Ironworker Machine
(1) Steel structure processing industry: The Ironworker Machine Used for processing connection holes of steel structure components and shearing of profiles, such as in the manufacturing of building steel structures and bridge steel structures.
(2) Mechanical manufacturing industry: During the manufacturing process of various mechanical equipment, parts can be processed by Ironworker Machine, such as processing of conveyor frame, agricultural machinery components, food machinery components, etc.
(3) Power and communication industry:The Ironworker Machine Applicable to the processing of components of high and low voltage towers and the manufacturing of communication tower frames, and can perform punching and shearing operations on the steel of the towers to ensure the accuracy and quality of the components.
(4) Automobile and trailer manufacturing industry: The Ironworker Machine Used for processing of automotive components, trailer spare parts, hinges, plate hooks, etc., able to meet the metal processing requirements in the manufacturing process of automobiles and trailers.
(5) Other industries: The Ironworker Machine Also applicable to the production and manufacturing of civilian facilities such as storage shelves, high-voltage power line towers, telecommunications towers, street lamps, advertising signs, elevators, ventilation ducts, etc.
Key points for selecting the Ironworker Machine
(1) Processing materials and thickness of The Ironworker Machine : Select the appropriate machine model based on the type of metal material to be processed (such as sheet metal, profile, etc.) and the maximum processing thickness to ensure that the equipment's punching pressure and shearing force can meet the processing requirements.
(2) Processing accuracy requirements of The Ironworker Machine: If high accuracy is required for processing, such as the verticality of punching or the straightness of shearing, a hydraulic Ironworker Machine with a higher precision grade should be selected.
(3) Functional requirements of The Ironworker Machine: Based on the actual processing requirements, choose the machine model with the corresponding functions, such as whether to need sheet bending, die cutting, or bevel cutting functions.
(4) Production efficiency of The Ironworker Machine: For enterprises with large-scale production, consider the working efficiency of the equipment, such as the number of strokes, cycle time, etc., to improve production efficiency and reduce production costs.
(5) Brand and after-sales service of The Ironworker Machine: Choose a well-known brand of hydraulic Ironworker Machine, as its product quality and after-sales service are usually more reliable. Understand the after-sales service content of the manufacturer, such as warranty period, repair response time, and spare parts supply.