The working principle of the Electric Press Brake is based on electrical energy drive. Through servo motors and precise mechanical transmission systems, electrical energy is converted into mechanical energy. It uses a numerical control system to precisely control the bending angle, depth and speed. Compared with hydraulic bending machines, Electric Press Brake is more environmentally friendly, has lower energy consumption, higher precision, lower noise, and relatively lower maintenance costs. It is suitable for precise bending of thin plates and is widely used in sheet metal processing and electronic product manufacturing, etc. The control system, according to the preset program or operator’s instructions, drives the motor to move the slider up and down, thereby achieving precise bending of the metal sheet. The advantage of motor drive lies in the accuracy and repeatability of control, ensuring high-quality bending results.
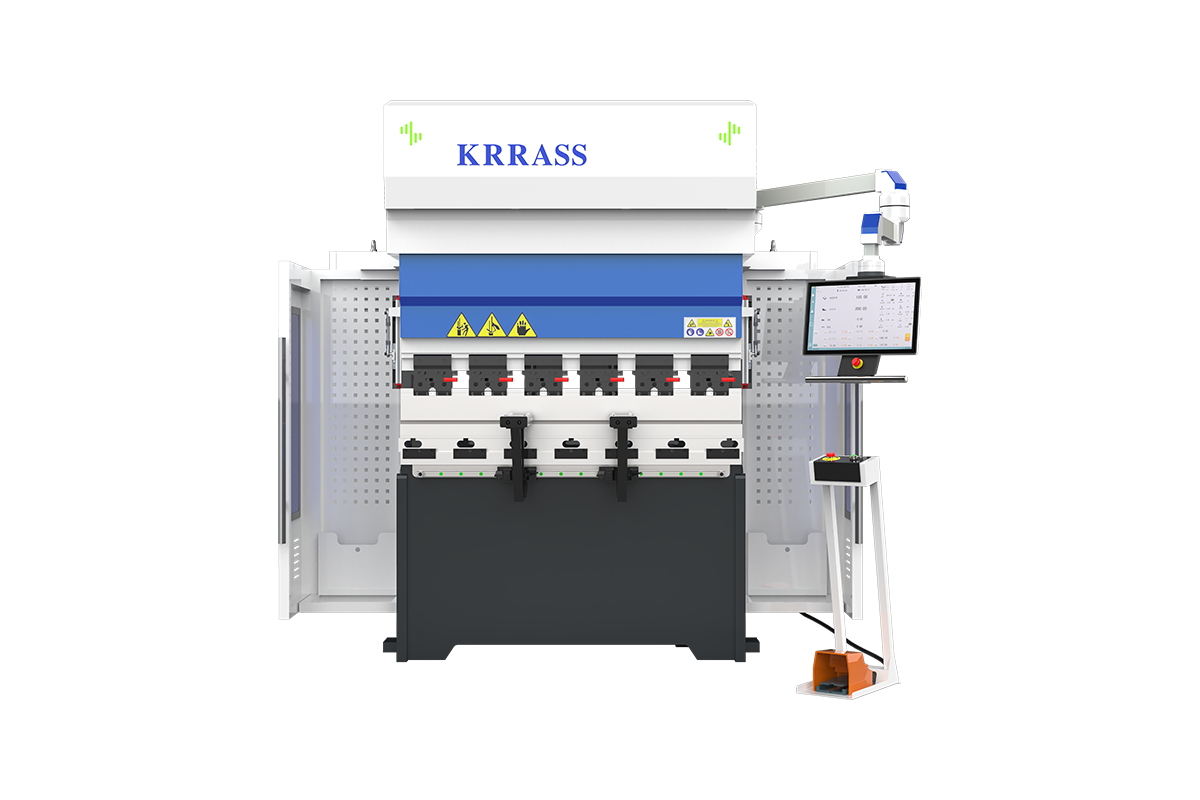
Table of Contents
The core components of Electric Press Brake:
Servo motor: provides power source, and realizes position and angle control during bending by precisely controlling power output. The high response speed and accuracy of servo motor are the key to ensure bending quality.
Guide rails and sliders: ensure smooth and precise movement of bending head or workbench, and ensure the stability of direction and position during bending.
Mechanical transmission system (screw, gear, synchronous belt, etc.): converts the rotational motion of the motor into linear motion, so that the bending head moves up and down. The high-precision transmission system ensures the accuracy of the bending angle.
Bending head: the part that actually performs the bending operation, through mechanical clamping and bending of metal sheets.
Control system (CNC system): operation interface and intelligent control core, control servo motor according to preset program or manual command to achieve precise bending.
Display panel/operation interface: convenient for operators to set parameters, monitor bending status, adjust program, etc.
Sensor: real-time monitoring of bending angle, position, pressure and other parameters, and feedback to the control system for dynamic adjustment and ensuring bending accuracy.
Power supply system: power supply to ensure stable operation of various electronic components.
Electric Press Brake Advantages:
Environmental protection and energy saving: Electric Press Brake does not require hydraulic oil, reduces oil pollution, and is more environmentally friendly.
Low energy consumption, high motor drive efficiency, can effectively reduce operating costs.
High precision and good repeatability: Due to the use of servo motors and CNC systems, the bending angle, position and depth can achieve higher precision. The precision of repeated bending is stable and suitable for batch processing.
Easy operation: The control system is user-friendly, the operation interface is friendly, and the operation is convenient.
Equipped with automated programs, it can achieve rapid debugging and multi-process automatic operation.
Low maintenance cost: The mechanical structure is simple, there are no vulnerable parts such as oil circuits and solenoid valves in the hydraulic system, and maintenance is more convenient.Reduce the problems caused by oil leakage and extend the life of the equipment.Low noise: Less noise during operation, improve the working environment.
Fast response speed: The servo motor has a fast response capability, fast bending speed, and improved production efficiency.
Higher safety: The electronic control system has multiple safety protection measures to improve work safety.
Importance of servo motor selection:
Driving bending movement: The servo motor provides precise power for the bending machine, controls the movement of the upper and lower dies or the left and right dies, and realizes the bending operation of the metal sheet. This driving method is more sensitive and accurate than the traditional hydraulic system.
High-precision position control: The servo motor can achieve fine angle and position control, ensure the accuracy of the bending angle, and meet the needs of complex or high-demand bending processes.
Realize fast response and adjustment: Because the servo system has high-speed response capability, the mold position and pressure can be quickly adjusted during the bending process, improving production efficiency and bending quality.
Energy recovery and energy saving: In some designs, the servo system can recover energy during the movement, reduce energy consumption, and improve overall energy efficiency.
Simplify mechanical structure and maintenance: Using servo motors instead of hydraulic systems reduces the complexity of hydraulic oil and oil circuits, and reduces maintenance costs and equipment failure risks.
Optimize Electric Press Brake optimization strategy:
- Choose high-performance drive components
Servo motor: Choose a servo motor with fast response speed and stable torque to ensure the accuracy and dynamic response of movement.
Transmission mechanism: Use high-rigidity and low-clearance transmission components, such as wire rope, ball screw, synchronous belt or gear transmission, to reduce transmission error. - Use precise transmission structure
Ball screw: It has high efficiency and high precision, which helps to achieve smooth and precise movement.
Synchronous belt or chain: When used for long-distance transmission, it improves transmission efficiency and durability.
Linear guide: Ensure the linearity of the motion path and reduce deviation. - Design a reasonable reduction device
Use an efficient reducer to ensure stable torque transmission while reducing energy loss.
Choose a suitable gear ratio to take into account speed and torque requirements. - Strengthen rigidity and shock absorption measures
Strengthen rigidity in structural design to reduce vibration and deformation.
Add damping structure at key parts to reduce vibration during movement. - Integrated closed-loop control
Use encoders and sensors to achieve feedback control, adjust motion parameters in real time, and ensure the accuracy of bending angles.
Adopt advanced control algorithms (such as PID, Model Predictive Control, etc.) to optimize motion trajectory. - Optimize lubrication and maintenance
Regularly lubricate transmission components to reduce friction and wear.
Design a structure that is easy to maintain and easy to detect and replace key components. - Digital simulation and testing
Perform motion simulation through CAD/CAM software to evaluate the performance of the transmission system in advance.
Perform dynamic analysis before actual design to optimize transmission parameters.
How to select the screw rod of Electric Press Brake?
The selection of the screw of the Electric Press Brake needs to comprehensively consider the load characteristics, accuracy requirements, motion parameters and structural design of the equipment. The following is a detailed selection process and key points:
1.Clarify the core parameters of screw selection
- Load analysis
Axial load: Determined by the bending force, it is necessary to calculate the axial force (Fₐ) of the maximum bending force transmitted to the screw through the mechanical structure.
Example: If the maximum pressure of the bending machine is 100kN and the mechanical transmission efficiency is 80%, the axial load of the screw Fₐ=100kN/80%=125kN.
Radial load: caused by the weight of moving parts such as sliders and molds and eccentric loads, it is necessary to avoid bending deformation of the screw due to radial force.
Dynamic load: Inertial force during acceleration/deceleration (F=ma), the slider mass (m) and maximum acceleration (a) need to be considered. - Accuracy requirements
Positioning accuracy: The bending angle accuracy of the bending machine to the workpiece is usually required to be within ±0.5°, and the corresponding positioning accuracy of the screw must reach 0.01~0.05mm/1000mm (such as C7 grade ball screw).
Repeatability: affects the consistency of the workpiece. It is recommended to select a lead screw with a repeatability of ≤±0.005mm. - Motion parameters
Maximum speed (v): determined by production efficiency, such as the maximum downward speed of the slider is usually 100~200mm/s.
Acceleration (a): affects dynamic response, generally 500~1000mm/s², and high-speed models require higher.
Lead (P): The larger the lead, the higher the speed, but the greater the torque demand. The commonly used lead is 10~20mm.
2.Screw type selection: ball screw vs trapezoidal screw
Type | Advantages | Disadvantages | Applicable Scenarios |
Ball screw | High efficiency (90%~95%), high precision, long life | High cost, high installation precision requirements | High precision, high speed Electric Press Brake |
Trapezoidal screw | Low cost, simple structure | Low efficiency (30%~60%), fast wear | Low precision, low speed or small bending machine |
Recommendation: Electric Press Brake prefers ball screw because it can meet the requirements of high precision and high efficiency.
- Determine the screw diameter (d₀)
Based on the axial load Fₐ, refer to the ball screw rated dynamic load (Cₐ) formula: Ca=Fa×31000L×fw×fh
Where:
L is the expected life (mm), generally 1 million to 5 million mm;
f_w is the load factor (1.5~2.5 for impact load);
f_h is the hardness factor (1 for ball screw hardness ≥58HRC).
Example: If Fₐ=125kN, L=3 million mm, f_w=2, then Cₐ=125×√[3]{3000}×2≈125×14.4×2=3600kN, and a screw with a rated dynamic load ≥3600kN should be selected (such as a ball screw with a diameter of 63mm and a lead of 20mm).
2. Check critical speed and stability
Critical speed (n_c): Avoid resonance during high-speed operation, the formula is: nc=L2997×d02
Where L is the screw support spacing (mm), it is necessary to ensure that the actual speed n < n_c (generally n < 0.8n_c).
Axial stability: When the aspect ratio (L/d₀) is large, the buckling load needs to be checked to avoid the screw from being compressed and bent.
3. Match the motor and transmission ratio
Motor torque (T): The calculation formula is: T=2π×ηFa×P+Tf
Where η is the screw efficiency (0.9 for ball screw), and T_f is the friction torque (about 0.1~0.2 times the load torque).
Transmission ratio (i): If the maximum speed of the motor is n_m, it must satisfy: i=v×60nm×P
Example: v=150mm/s, P=16mm, n_m=3000rpm, then i=3000×16/(150×60)=5.33, and the reduction ratio of i=5 can be selected. - Accuracy level and preload method
According to ISO standards, C5~C7 levels are suitable for general bending machines, and C3 levels are suitable for precision bending machines.
Preload method: Double nut preload can eliminate gaps, improve rigidity, and is suitable for high-precision scenarios; single nut without preload has low cost, but there is gap.
Key points of structural design and installation
- Support method: fixed at both ends (highest rigidity, suitable for long screws), fixed at one end + supported at one end (simple structure, suitable for medium and short screws).
- Lubrication and protection: The ball screw needs to be regularly smeared with lithium-based grease or use an automatic lubrication system, and a dust cover (such as a bellows, steel belt cover) should be installed to prevent dust from entering and affecting its life.
- Thermal expansion compensation: The long screw needs to consider the elongation caused by temperature changes, which can be installed by pre-stretching or reserving compensation gaps.
Selection Case Reference
Model: 70-ton Electric Press Brake, worktable length 2 meters, positioning accuracy ±0.03mm.
Screw selection: rolled ball screw (lower cost than ground screw, meets general accuracy), diameter × lead: 50mm×16mm, accuracy level: C7, support method: fixed at both ends + double nut pre-tightening; motor matching: servo motor power 7.5kW, reduction ratio i=4, maximum speed 2000rpm, meets the slider speed 200mm/s.
Precautions
- Load fluctuation: The load is not constant during the bending process, so the model should be selected according to the maximum load and the safety factor (1.5~2 times) should be considered.
- Rigidity matching: The rigidity of the screw rod should be coordinated with the rigidity of the frame and the slider to avoid the loss of accuracy due to deformation of the screw rod.