Electric Press Brake (Full Electric Press Brake) and Press Brake (Hybrid power Press Brake) are currently the two mainstream technical directions in the market.
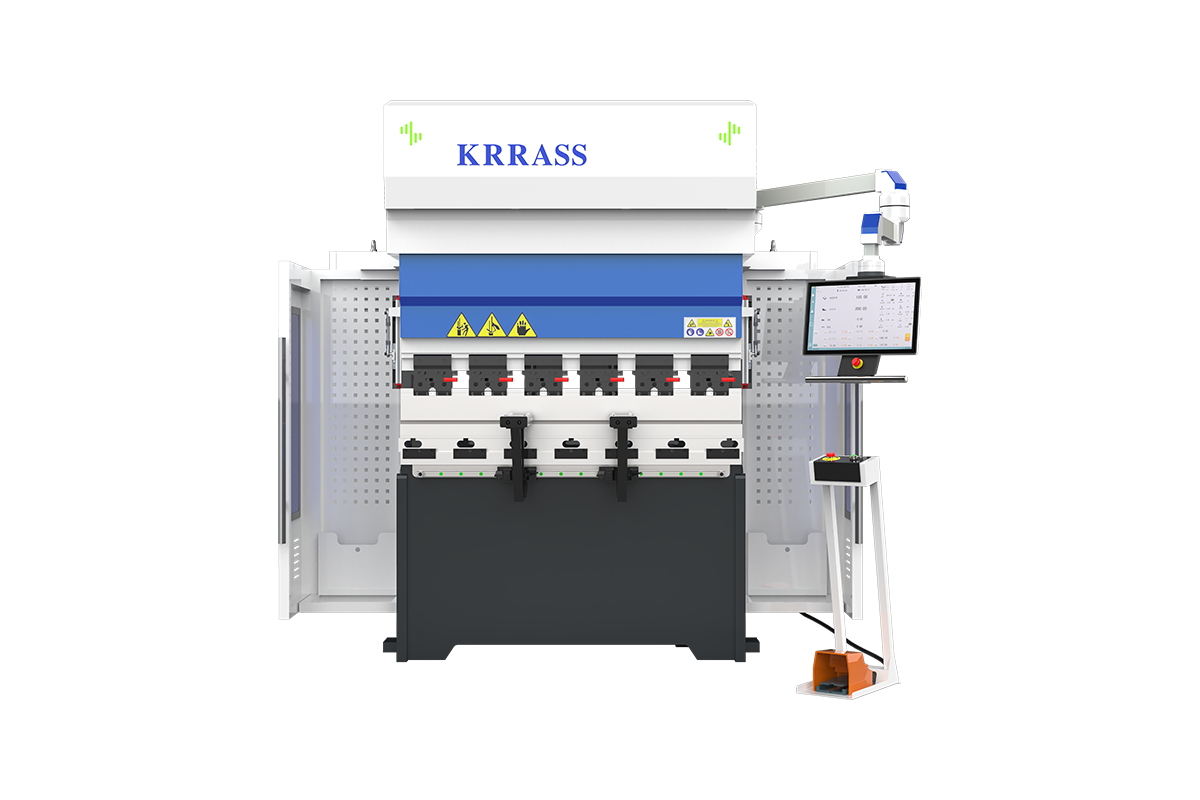
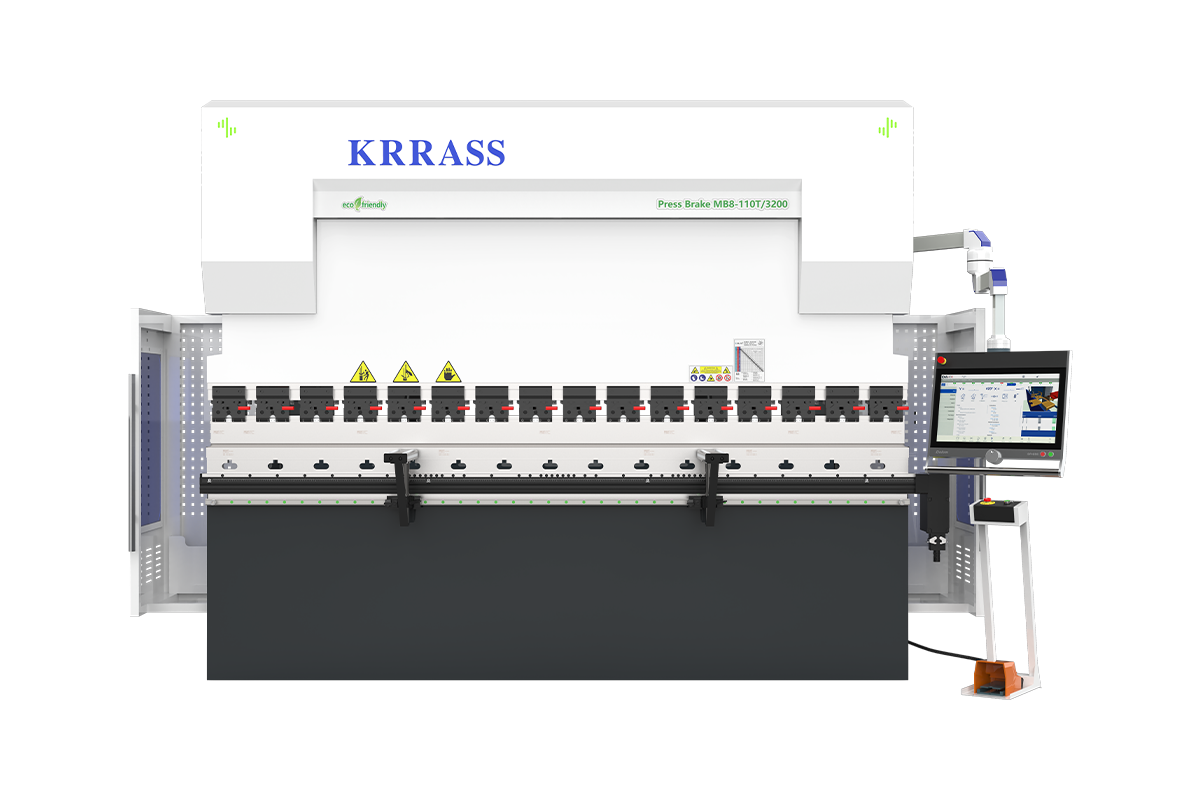
The accuracy of Electric Press Brake is ±0.01mm, energy saving is 40% to 60%, and there is no risk of oil contamination. Hydraulic Press Brake is suitable for large-tonnage processing. It has a low initial cost but complex maintenance. When making a selection, it is necessary to balance accuracy, energy consumption and budget.
With the continuous improvement of the manufacturing industry's demand for efficient, precise and environmentally friendly production, Hydraulic Press Brake, as the core equipment in the field of sheet metal processing, its technical path is also constantly innovating.
There are significant differences between the two in terms of driving mode, energy consumption, precision and applicable scenarios. This article will explore the characteristics and differences between the two from the perspectives of technical principles, application fields, and performance comparisons.
Table of Contents
I. Technical Principles and Core Differences
1. Electric Press Brake
Drive mode: It adopts a servo motor to directly drive the ball screw or rack and pinion system, and precisely controls the movement of the slider through electrical signals
Energy supply: Completely dependent on electricity, no need for hydraulic oil or hydraulic pump stations, and the structure is more simplified.
Control logic: High dynamic response is achieved through the numerical control system (CNC), and the bending Angle, speed and pressure parameters can be programmed and set.
2.Hydraulic Press Brake
Drive mode: Combining servo motor and hydraulic system, the motor drives the hydraulic pump to generate high-pressure oil, and the hydraulic cylinder pushes the slider to move
Energy supply: It relies on the dual energy conversion of electricity and hydraulic oil, and requires the configuration of hydraulic oil tanks, valves and pipeline systems
Control logic: The hydraulic flow and pressure are regulated through proportional valves or servo valves, but the response speed is greatly affected by the inertia of the hydraulic system
Summary of core differences: The Electric Press Brake achieves "zero transmission clearance" through direct electric drive connection, while the Hydraulic Press Brake relies on the hydraulic system to transmit power, resulting in energy conversion losses.
II. Performance Comparison Analysis
1.Accuracy and repeatability
Electric Press Brake: Directly controlled by servo motor, the positioning accuracy can reach ±0.01mm, with high repeat positioning accuracy, suitable for high-precision sheet metal processing (such as electronic components, medical devices).
Hydraulic Press Brake: Affected by the change of hydraulic oil temperature and the delay of valve response, the accuracy is usually ±0.1mm and needs to be calibrated regularly to maintain stability.
2.Energy consumption and environmental protection
Electric Press Brake: It consumes electrical energy only when the slider is in motion. The standby power consumption is close to zero. The comprehensive energy consumption is reduced by 40% to 60%, and there is no risk of hydraulic oil leakage, meeting the green manufacturing standards.
Hydraulic Press Brake: The hydraulic pump needs to operate continuously to maintain the system pressure, has high standby energy consumption, and there are problems of hydraulic oil replacement and contamination treatment when used for a long time.
3.Speed and Efficiency
Electric Press Brake: It has a fast acceleration and an idle speed of over 200 mm/s, making it suitable for flexible production with small batches and multiple varieties.
Hydraulic Press Brake: The hydraulic system has a large inertia and a relatively slow acceleration/deceleration response, but it still has the advantage of stability in bending with large tonnage (such as more than 2,000 tons).
4.Maintenance cost
Electric Press Brake: Simple structure, no hydraulic components. Daily maintenance only requires lubricating the guide rails and checking the electrical connections.
Hydraulic Press Brake: Hydraulic oil and filter elements need to be replaced regularly, valves and seals inspected and repaired, and the maintenance cost is relatively high.
III. Comparative Advantages
1.Electric Press Brake
Energy conservation and environmental protection: Driven by electricity, it has no risk of hydraulic oil pollution and is more environmentally friendly.
High-precision control: The numerical control system provides precise positioning and control, ensuring product consistency.
High efficiency and energy saving: The servo motor is powered as needed, reducing energy consumption and improving efficiency.
Low-noise operation: No hydraulic pump station is required, resulting in lower noise during operation.
Low maintenance cost: Reduce the wear of mechanical components and lower long-term maintenance expenses.
High degree of intelligence: Supports industrial Internet access, facilitating remote monitoring and management.
Strong flexibility: It is easy to adjust parameters to meet the requirements of different materials.
2.Hydraulic Press Brake
The hydraulic press brake adopts a fully welded steel structure, featuring high strength and rigidity. The slider synchronous mechanism forces synchronization through a torsion shaft to ensure precise movements.
Ease of operation: The slider stroke can be quickly adjusted by motorization and fine-tuned manually. It is equipped with a counter to display parameters in real time, offering flexible operation.
Applicable scenarios: Suitable for large-scale production and thick plate processing. The hydraulic transmission system can provide continuous and stable pressure, making it suitable for complex bending operations.
Maintenance cost: The structure of the hydraulic system is relatively simple, and the daily maintenance cost is low, but the hydraulic oil needs to be replaced regularly and the hydraulic components need to be maintained.
IV. Typical Application Scenarios
1.Application fields of Electric Press Brake
Precision sheet metal processing: 3C electronic product casings, aerospace components, optical instrument brackets and other scenarios with strict tolerance requirements
Rapid model change production: Suitable for small and medium-sized enterprises with scattered orders and diverse product types, it shortens the delivery cycle with high programming efficiency
Cleanroom: The oil-free feature makes it suitable for industries with high requirements for the production environment, such as food machinery and medical equipment.
2.Hydraulic Press Brake application fields
Heavy industry processing: Bending requirements for large thickness (over 6mm) and large tonnage (over 500 tons) of automotive longitudinal beams, ships, etc
Continuous high-intensity operation: The thermal stability of the hydraulic system is more suitable for long-term continuous stamping, such as in the production of building steel structures
Cost-sensitive scenarios: The initial procurement cost is relatively low, making it suitable for enterprises with limited budgets and no extreme requirements for precision.
V. Market Trends and Selection Suggestions
1.Technological development trends
Electric Press Brake is evolving towards higher tonnage (exceeding 1,000 tons) and intelligence (AI parameter self-optimization), gradually penetrating the heavy industry sector.
Hydraulic Press Brake optimizes energy efficiency through "variable frequency hydraulic pump" and "closed-loop control" technologies, attempting to narrow the performance gap with pure electric motors.
2.Key considerations for model selection
Processing requirements: Select Electric Press Brake for high precision and small batch; For large tonnage and high strength, choose Hydraulic Press Brake.
Initial cost: The Electric Press Brake equipment has a high initial investment but low maintenance cost, while the Hydraulic Press Brake equipment is the opposite.
Environmental protection regulations: In regions or industries where oil pollution emissions are strictly restricted, Electric Press Brake is preferred.
Vi. Comparative Analysis of Electric Press Brake and Hydraulic Press Brake
The main application fields of Electric Press Brake: small sheet metal processing fields such as chassis, electrical cabinets, control boxes in the IT and telecommunications industries, and fields with high requirements for processing efficiency and energy conservation and environmental protection. For instance, small electrical cabinets and control boxes that are in high demand by Huawei, China Telecom and China Mobile.
The main advantage of Electric Press Brake is its fast bending speed. Even if the Y-axis fast-forward speed is the same, due to its large acceleration, the overall processing time is saved compared with Hydraulic Press Brake.
The Electric Press Brake adopts servo motors and is more energy-efficient compared to electro-hydraulic servo bending machines, saving approximately 10,000 kilowatt-hours of electricity per year.
Electric Press Brake does not require the use of hydraulic oil and does not need to change the hydraulic oil regularly. It is environmentally friendly and green.
Electric Press Brake adopts servo motors, ensuring stable control and no impact on bending accuracy due to changes in oil temperature.
The main disadvantage of Electric Press Brake is its relatively high price, usually about 1.5 to 2 times that of an electro-hydraulic servo bending machine.
Comparative Analysis of KRRASS Electric Press Brake and Hydraulic Press Brake: Three-axle (X/Y/R) of 50-ton 1650mm Model
KRRASS Electric Press Brake Epp-50T1650 SCS800 6 Axis | KRRASS Hydraulic Press Brake PBS-50T1600 DA53T 4+1 | ||
Pressure (tons) | 50 | 50 | |
Table length (mm) | 1650 | 1600 | |
Y-axis slider stroke (mm) | 180 | 160 | |
Y-axis down fast forward speed (mm/s) | 200 | 180 | |
Y-axis working speed (mm/s) | 30 | 10 | |
Y-axis up fast forward speed (mm/s) | 200 | 110 | |
Energy consumption (kw) | 1 | 4.5 | It can save about 10,000 kilowatt-hours of electricity in a year. |
Hydraulic oil | No | Need | Green and environmentally friendly. |
Repeat positioning accuracy (mm) | 0.005 | 0.01 | |
stability | Intelligent Safety Light Curtain (Patent applied) Standard configuration | It is less adopted due to control method issues | |
Safety light curtain protection device Laser or photoelectric protection device | No | Optional |
Vii. Conclusion
Electric Press Brake and Press Brake each have their technical advantages and applicable boundaries. The former leads the future of precision manufacturing with high precision and low energy consumption, while the latter remains irreplaceable in the heavy industry sector due to its large tonnage and cost advantages. Enterprises need to select the most suitable technological path in light of their own production demands, budgets and sustainable development goals. With the further maturation of electric drive technology, the competition or integration of the two in some scenarios will become the core driving force for the upgrading of bending processes.