Explore Press Brake star products and basic processes
Press Brake, a magical skill in sheet metal processing, can flexibly bend various shapes into the desired shape with just a few cuts. Among the many products that have a deep understanding of bending, we have selected three star products for introduction. First is the HAX series three-dimensional bending wire forming machine launched by RK Trading Company, model HAX-20, which is unique in that it can quickly twist steel wire into various complex shapes, showing excellent bending effects.
Next, let's take a look at the MB8-110T3200 DA53T 4+1 Axis CNC Press Brake type fastest stainless steel iron press brake launched by KRRASS. This machine cleverly feeds the flat plate to the machine and bends it efficiently. It is characterized by extremely fast speed, precise positioning, and the rhythmic sound it makes when working, which is impressive.
Next, we turn to Salvagnini's press brake. Although this high-end equipment performs well in small-batch production, it is difficult to cope with large-scale processing needs, so its application field is relatively limited. The level of technology shown in the video is amazing. "Bending workers will be silent when they see it, and sheet metal masters will cry when they see it."
Key knowledge points of CNC bending process: The core parameters of press brake include pressure and workbench length.
1.Main types of bending knives
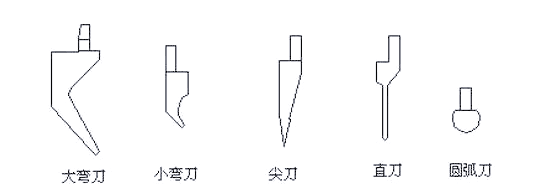
2.The application of straight knives in bending.
Straight knives are usually suitable for situations where only one bend is required and there is no need to consider the avoidance, as shown in the figure:
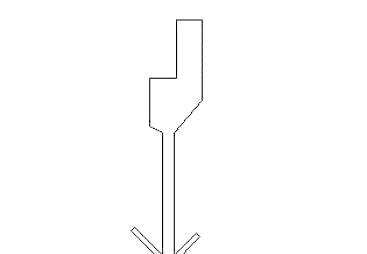
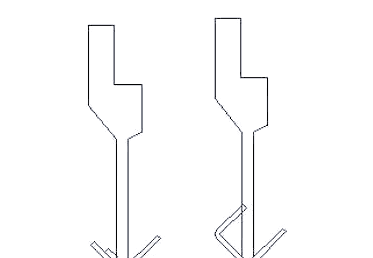
Figure 3 shows an obvious interference situation, in which the bending operation encounters difficulties. In order to deal with this situation, we need to consider using other types of bending knives to perform the operation. In the situation shown on the left side of Figure 3, it is possible to give priority to using a small curved knife for avoidance processing according to the actual situation, which can effectively solve the interference problem, as shown in Figure 4.
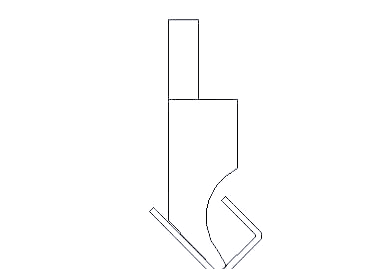
For the situation shown on the right side of Figure 3, it is more appropriate to use a sharp knife for avoidance. However, it should be noted that due to its sharp head design, the strength of the sharp knife is relatively weak, so it is not suitable for bending thick plates. Generally, for plates with a thickness of more than 1.5mm, the use of a sharp knife should be avoided. In such cases, we need to make adjustments in the process arrangement, such as placing the rivet nut process after the bending process to ensure smooth operation.
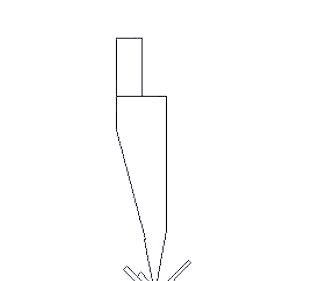
Sometimes, even if the small machete cannot avoid the position, we still need to use a larger machete to operate. This situation can be understood by referring to Figure 6:
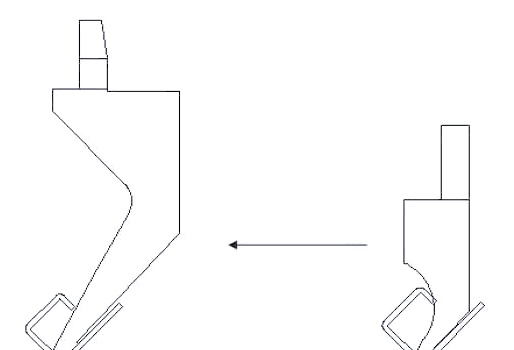
But sometimes there are situations where even a large machete cannot avoid the position, and additional process measures are needed. First, a pre-imprint is made on the bending line (as shown in Figure 7). The purpose of this is to be able to bend to a certain angle in the subsequent bending process to avoid collision with the tool. Next, the edge is pressed to 90 degrees (as shown in Figure 8). Usually, this stamping process is suitable for bending operations that cannot be completed in one go. In this way, when the second bend is performed, the bending line can be formed more accurately along the original bending mark, avoiding the problem of deviation caused by the second bend or improper control of the bending angle.
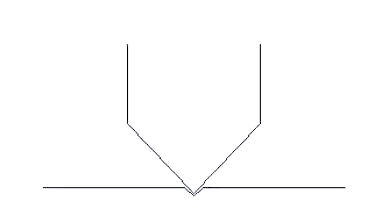
During the bending process, a mark is pre-pressed on the bending line. This operation is intended to provide a predetermined angle for subsequent bending, thereby effectively avoiding tool collision. This is an important step to ensure the smooth progress of the bending operation and improve the bending accuracy.
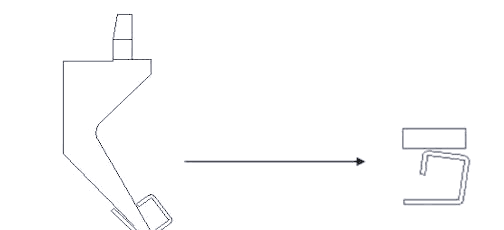
During the design process, we need to fully consider the advantages and disadvantages of the bending process. Although other processes may meet the requirements in some cases, direct bending usually works better and can control the size and angle more accurately. In addition, the bending machine is not only suitable for bending workpieces, but also for pressing dead edges. When arranging the process, we need to carefully weigh various factors to ensure the smooth progress and high-quality completion of the bending. It should be noted in particular that there are strict restrictions on the bending dimensions of workpieces with different plate thicknesses, and too small dimensions may cause quality problems. When selecting the lower die, it is generally recommended to select a knife groove that is 6 times the plate thickness, so as to ensure that the bending coefficient is consistent with the empirical value, thereby improving the quality stability of the product.
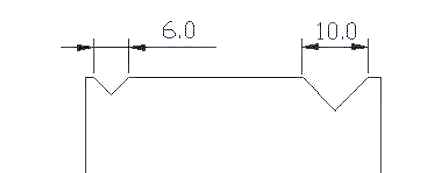
In the bending process, the use of too small a groove often leads to indentation problems. Usually, grooves below No. 6 will produce obvious indentations during bending, especially when the workpiece surface is untreated and the bending edge is small. This indentation not only affects the appearance, but may also cause rust problems. Therefore, such problems must be given full attention during design.
In addition, in the actual bending process, various complex situations will be encountered, and the impact of bending on other process links needs to be considered comprehensively. For different problems, specific analysis and reasonable arrangement of the process flow are required. At the same time, suppliers will also manufacture bending knives of specific shapes according to special needs, but it should be noted that the more complex the shape of the tool or the greater the curvature, the more rigidity may be affected, thereby shortening the service life of the tool.