Press Brake are indispensable equipment for sheet metal machining, but we don’t know how to choose the brand. At present, the world’s highest production is in China, Turkey, and Belgium. Now Belgium LVD, MVD, and HACO have already manufactured in China. I hope the following details can help you.
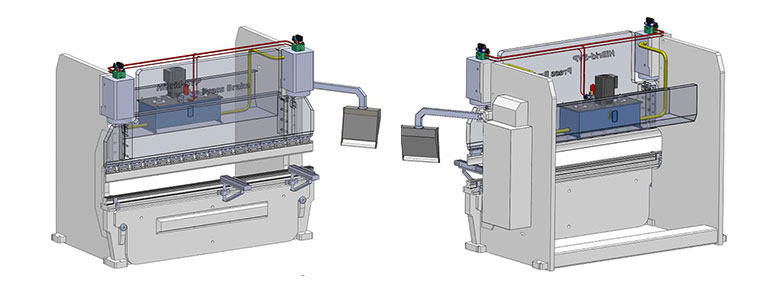
Table of Contents
1.How to choose the controller for Press Brake?
There are three major international brands of bending machine controllers to choose from, DELEM from the Netherlands, Cybelec from Switzerland, and ESA from Italy.
1.1 Netherlands DELEM controller
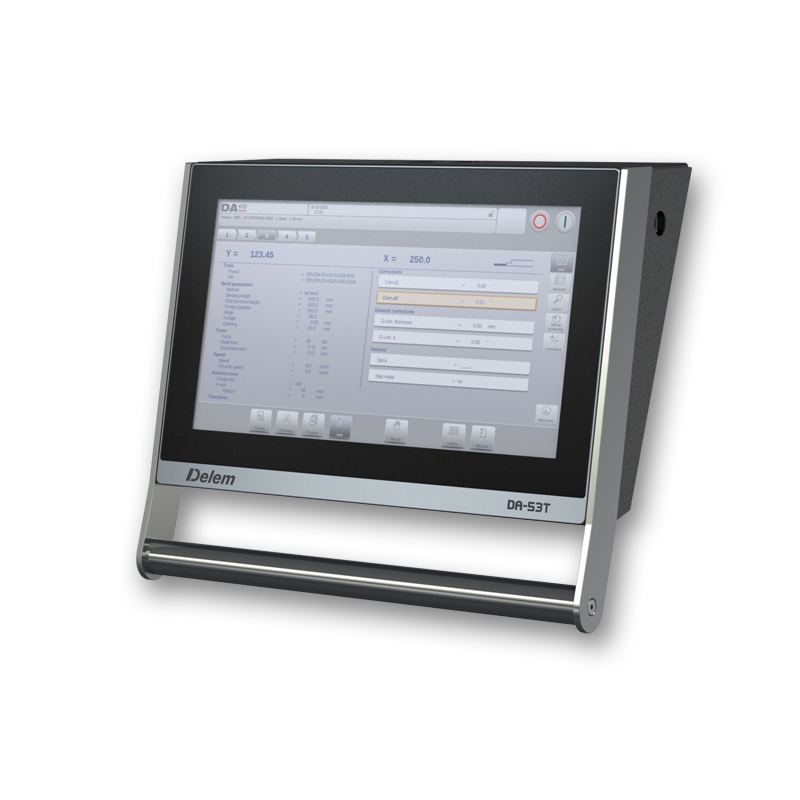
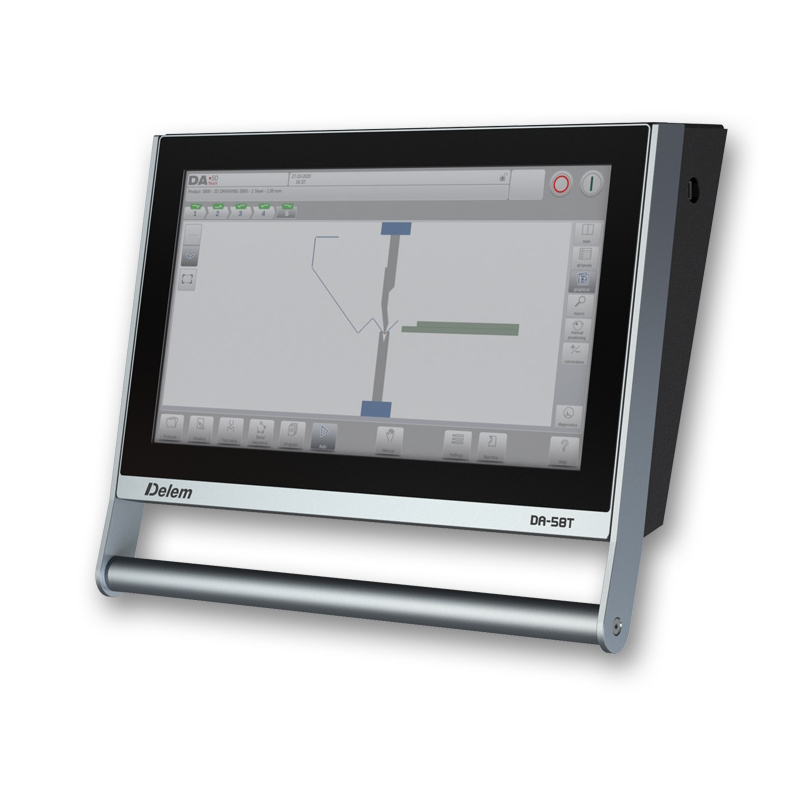
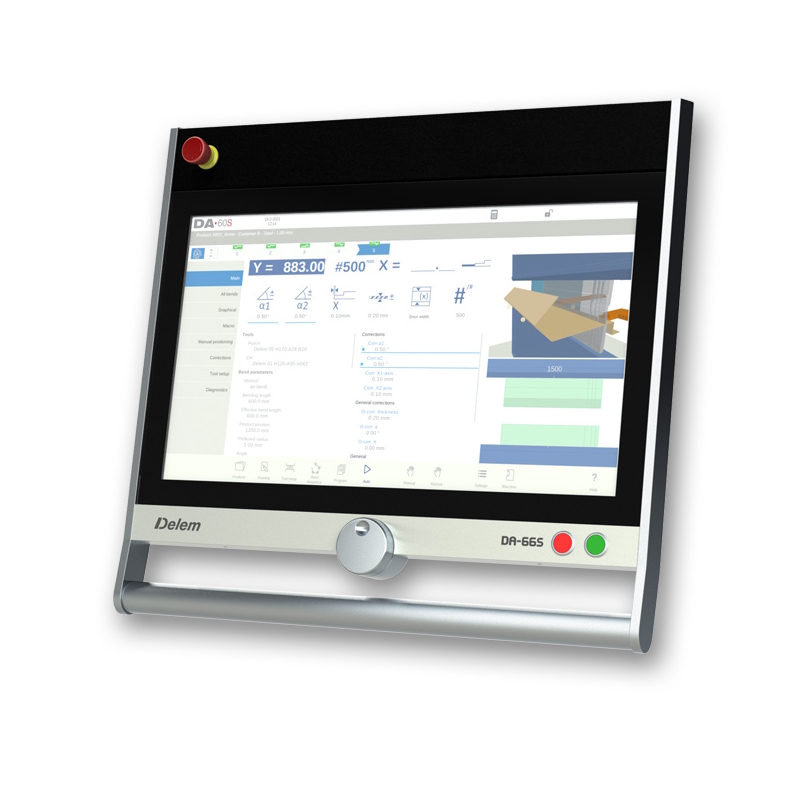
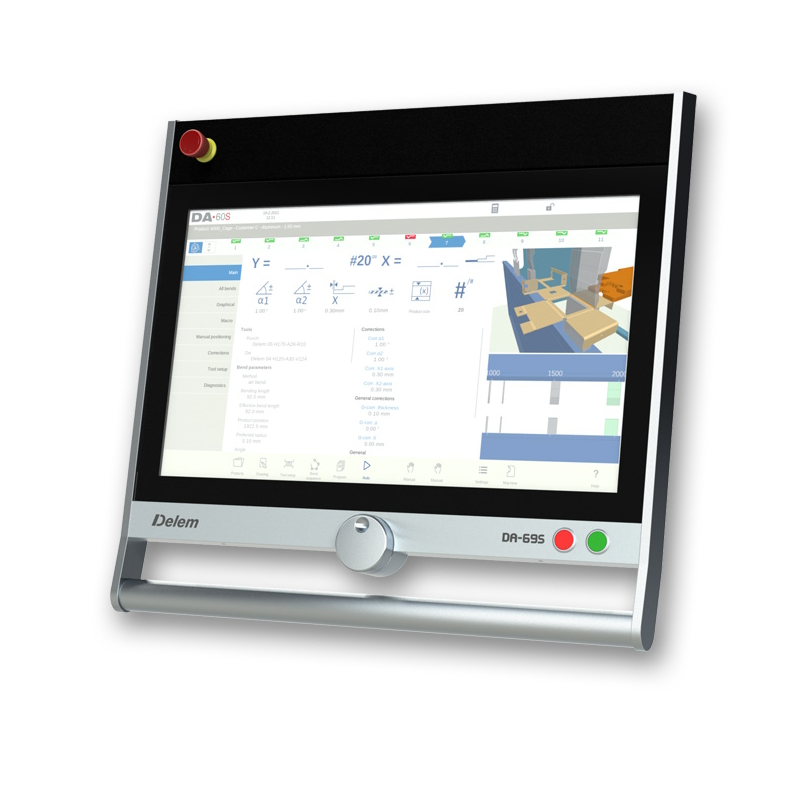
DELEM DA53Tx Controller
- Graphical programming: supports graphical programming. Through the intuitive graphical interface, operators can easily input information such as the shape and size of the bending workpiece, and the system can automatically generate the corresponding bending program. This greatly reduces the difficulty of programming, and even inexperienced operators can quickly get started, improving programming efficiency.
- Simple operation interface: equipped with a large-size color display and a user-friendly operation interface, the operation buttons are reasonably laid out and easy to operate. The system menu is concise and clear, and various functions can be quickly implemented through a few simple steps, reducing the operator’s operating errors and time costs.
- Program storage and call: A large number of bending programs can be stored, which is convenient for quick call when needed. This is very practical for companies that often carry out batch production or need to repeatedly process the same workpiece, and can significantly improve production efficiency.
- Axis control capability: It can accurately control the movement of multiple axes, such as the back gauge axis, slider axis, etc., to ensure the movement accuracy and synchronization of each axis during the bending process. This enables the bending machine to achieve high-precision bending operations and ensure the bending accuracy and quality of the workpiece.
- Automatic compensation function: With automatic compensation function, it can automatically adjust bending parameters such as bending angle and pressure according to factors such as the material, thickness, and length of the plate to compensate for possible errors. In addition, it can also compensate for factors such as mechanical errors and temperature changes of the machine tool, further improving the bending accuracy.
- Quick mold change function: It supports the quick mold change function. When the mold needs to be replaced, the system can automatically adjust the relevant parameters, reducing the mold change time and debugging time, and improving production efficiency.
- Multi-step bending function: It can realize multi-step bending operations. Multiple bending steps can be set in one program. The machine tool can automatically complete continuous bending actions according to the preset program without manual intervention, greatly improving production efficiency.
- Wide range of machine tool adaptability: It can be adapted to a variety of different brands and models of bending machines, with good compatibility. This gives enterprises greater flexibility in choosing bending machines and CNC systems, and can reasonably match them according to their own needs.
- Scalability: The system has certain scalability, and can easily add new functional modules or upgrade the system according to the development and production needs of the enterprise to meet the ever-changing production requirements.
- Fault diagnosis function: It has a complete fault diagnosis function and can monitor the operating status of the system in real time. When a fault occurs, the system will promptly send out an alarm signal and display detailed fault information to help maintenance personnel quickly locate and troubleshoot the fault, reducing the downtime of the equipment.
- Remote maintenance function: It supports remote maintenance function. Through network connection, the manufacturer’s technicians can remotely diagnose and maintain the system, solve the problems encountered by users in a timely manner, and improve the efficiency and quality of after-sales service.
DELEM DA58Tx Controller
- Advanced graphical programming: 2D graphical touch screen programming is used to automatically calculate the bending sequence and perform collision detection, generate CNC programs, and simulate the bending process, helping operators to intuitively understand the processing situation, reduce trial and error, and improve programming efficiency and processing accuracy.
- Large size and high resolution screen: Equipped with an 18.5-inch high-resolution color TFT display, the display is clear and easy to operate. The industrial-grade multi-touch technology makes the operation smoother and more accurate. You can quickly switch between product programming and actual production through the “hot key” touch.
- Multi-axis control capability: The standard configuration can control up to 4 axes, which can achieve precise control of the moving parts of the machine tool, such as left and right cylinder synchronization, back gauge position and workbench hydraulic compensation, etc., making the bending process more flexible and accurate, and adapting to the processing of complex-shaped workpieces.
- Multiple control functions: With convexity control function, the convexity of the workbench can be automatically adjusted according to factors such as plate thickness and length to ensure bending accuracy; support servo and inverter control, can accurately control motor movement, improve system response speed and stability; has advanced Y-axis control algorithm, suitable for closed-loop and open-loop valve control, optimize slider motion control, and improve bending accuracy and quality.
- Convenient interface and storage: Provide USB interface and peripheral device interface, convenient connection with external devices, realize program transmission, data backup and other functions; support Profile-t offline software, can be programmed and simulated on the computer, and then transfer the program to the controller to improve programming efficiency, and 1GB storage capacity and 256MB product and tool memory can store a large amount of programs and data.
- Excellent user experience: compact design, practical functions, ergonomics, easy operation; Delem touch navigation interface is friendly, the operation logic is consistent, reduce the learning cost of operators, and improve work efficiency; the machine tool runs stably and reliably, can achieve smooth and fast bending, reduce downtime, and improve production efficiency.
DELEM DA66S Controller
- Advanced programming and display functions: It uses a 24-inch high-resolution color TFT touch screen with clear display and easy operation. It provides a 2D graphical touch screen programming mode, which can automatically calculate the bending process and perform collision detection, which can effectively improve programming efficiency and processing safety. It also has a 3D all-round, multi-station mold display function, which can display the feasibility of the bending operation of the real machine tool in real time during the simulation and production process, helping operators to understand the processing situation in advance and avoid errors.
- Efficient control algorithm: Using more efficient algorithms to optimize the entire machine tool work can shorten the operation cycle and improve the machine tool work efficiency. At the same time, it makes the adjustment and control of the machine tool more convenient, and can achieve more accurate and fast bending operations.
- Good compatibility and scalability: It is compatible with the Modusys system, has modular scalability and adaptability, and can expand and upgrade functions according to different application requirements. It provides USB interface and peripheral device interface to facilitate connection with external devices, realize program transmission, data backup and other functions, and also supports user-specific applications, which can run in the multi-tasking environment of the control system.
- High-precision control: It can ensure bending accuracy and meet various high-precision bending processing requirements. Some supporting equipment such as Fagor grating rulers can accurately measure the slight deformation of the machine tool caused by the bending force and provide feedback compensation to ensure the bending accuracy of any thickness and material plate. In addition, CNC electric compensation V-axis, movable stopper and other devices also help to ensure that the bending accuracy is within the controllable range.
- Convenient operation and navigation: Based on advanced industrial touch screen technology, you can access the updated Delem user interface, which can directly navigate between programming and production. The function buttons are reasonably arranged and directly act on the positions that need to be processed, providing optimized ergonomic design throughout the production use process. Delem touch navigation interface is user-friendly, with consistent operation logic, which is convenient for operators to use.
- Powerful storage capacity: With 4GB storage capacity and 3GB product and tool memory, it can store a large amount of programs and data, which is convenient for users to manage and call bending programs for different products.
- Multiple auxiliary functions: Support Profile-s 2D offline software, which can be programmed and simulated on the computer, and then the program is transferred to the controller to further improve programming efficiency. In addition, it also has auxiliary functions such as sensor bending and correction interface, thickness measurement and compensation system, which can better meet different processing requirements.
- Safe and reliable: Built-in safety PLC, in line with CE safety standards, equipped with safety devices such as foot switch with emergency stop button, to provide safety protection for operators and equipment.
DELEM DA69S Controller
- Intuitive graphical programming: Using a 3D graphical programming interface, operators can intuitively present the bending process from a three-dimensional perspective and accurately input parameters such as workpiece size and bending angle. The system can automatically generate the optimal bending program, greatly reducing the difficulty and time of programming and improving programming efficiency.
- Ultra-large high-definition display: Equipped with a 24-inch ultra-large high-resolution color touch screen, the display is clear, the colors are bright, the touch operation is sensitive, the interface layout is ergonomic, the operation is convenient, and the misoperation is effectively reduced.
- Offline programming function: Supports offline programming software, which can complete the programming and simulation of complex workpieces on the computer in advance, and then transfer the program to the CNC system, saving machine tool debugging time and improving equipment utilization.
- Multi-axis precision control: It can accurately control the movement of multiple axes, such as the back gauge axis, the slider axis, etc., to ensure the high precision and synchronization of the movement of each axis, realize accurate bending operations, and ensure the bending accuracy and quality of the workpiece.
- Intelligent compensation function: It has advanced automatic compensation function, which can automatically adjust bending parameters such as angle and pressure according to factors such as plate material, thickness, length, etc. It can also compensate for machine tool mechanical errors, temperature changes, etc., to further improve bending accuracy.
- Real-time monitoring and feedback: Real-time monitoring of the machine tool operation status and various parameters in the bending process, such as pressure, position, angle, etc., and feedback the data to the system. The system adjusts the control strategy in time according to the feedback data to ensure the stability and accuracy of the bending process.
- Fast mold change and parameter adjustment: It supports fast mold change function. When changing the mold, the system can automatically identify the mold type and adjust the relevant parameters, reduce the mold change time and debugging workload, and improve production efficiency.
- Multi-step continuous bending: It can realize multi-step continuous bending operation, set multiple bending steps in one program, and the machine tool automatically completes the continuous bending action according to the preset program without manual intervention, which greatly improves production efficiency.
- Wide range of machine tool adaptability: It is compatible with a variety of different brands and models of bending machines. Enterprises have higher flexibility when choosing bending machines and CNC systems, and can reasonably match them according to their own needs.
- Fault diagnosis and alarm: It has a complete fault diagnosis function and monitors the system operation status in real time. When a fault occurs, the system will promptly send out an alarm signal and display detailed fault information to help maintenance personnel quickly locate and troubleshoot the fault and reduce equipment downtime.
- Remote monitoring and maintenance: It supports remote monitoring and maintenance functions. Through network connection, the manufacturer’s technicians can remotely diagnose, debug and upgrade the system, solve user problems in a timely manner, and improve the efficiency and quality of after-sales service.
1.2 Swiss Cybelec controller
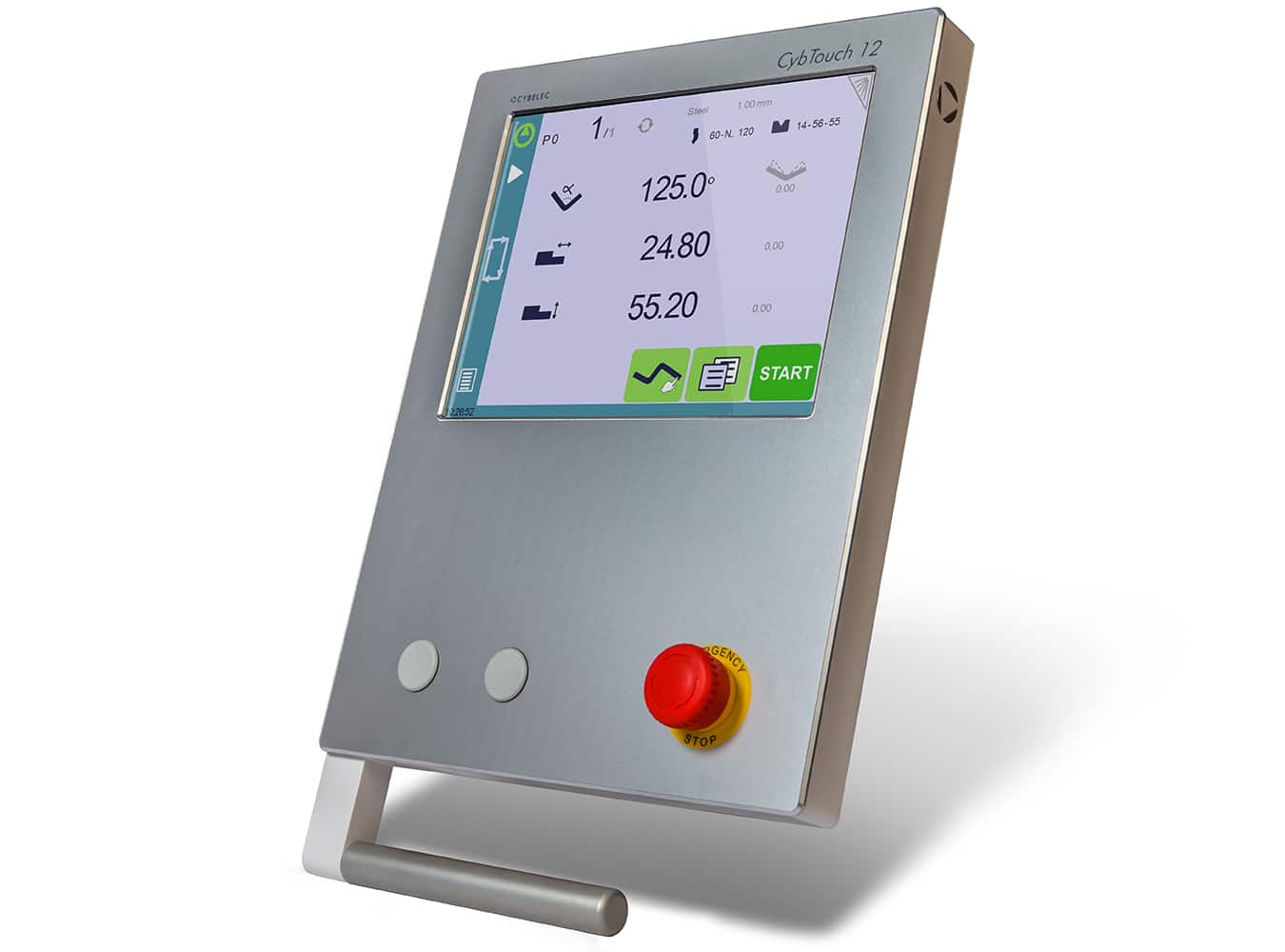
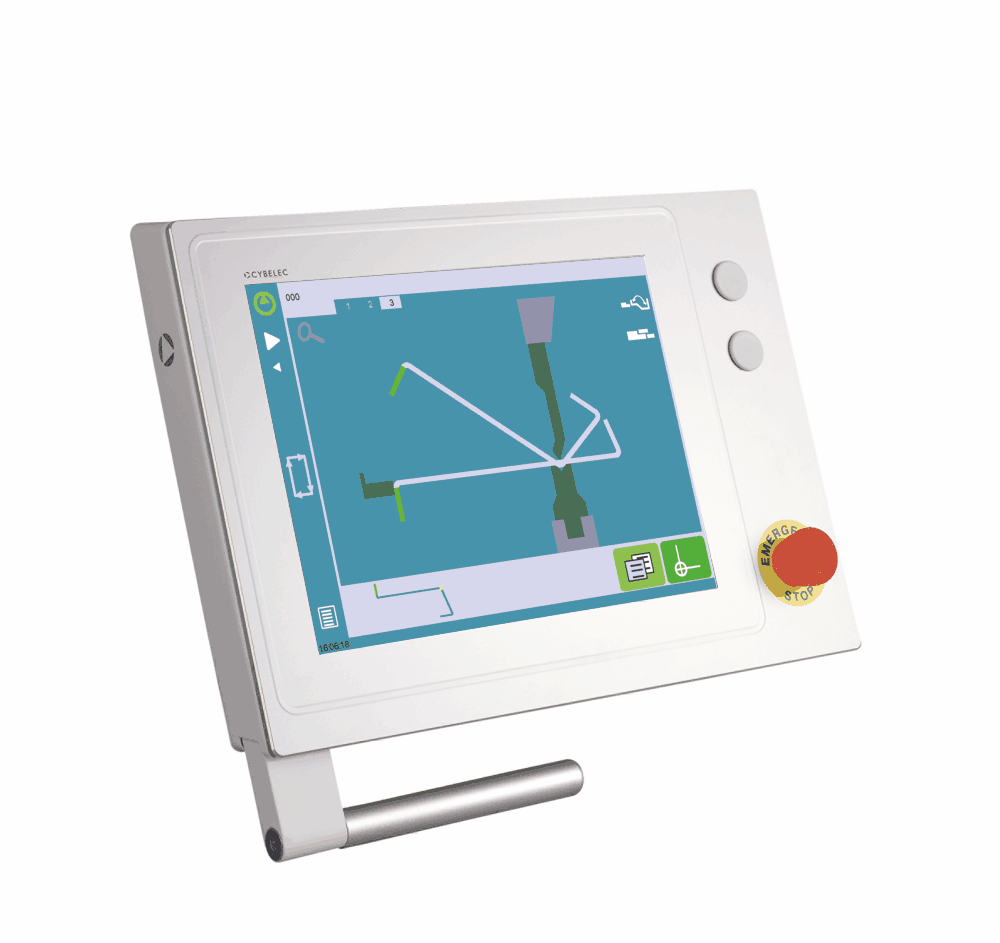
Cybelec Ct12 Controller
- Intuitive operation interface: Equipped with a 12-inch high-definition touch screen, the display is clear and the operation is convenient1. It adopts a full-screen touch human-machine interface and an ergonomic large button design, which conforms to the modern industrial design aesthetics4. The “EasyBend” page makes single bending processing extremely easy. The operator can intuitively depict the cross-sectional shape of the workpiece with his fingers, so that the design intention can be more clearly conveyed to the equipment.
- Convenient programming function: Supports digital programming and 2D graphic programming. Digital programming has dynamic text prompts to facilitate the operator to enter parameters. The 2D graphic programming function is powerful and can automatically give a bending plan without manually determining the bending order (option). It can also perform 2D bending simulation to help operators understand the processing situation in advance and avoid errors.
- Powerful computing power: It can automatically calculate the bending angle, main pressure and deflection compensation without manual tedious calculations and repeated debugging, and quickly and accurately provide the best bending parameters to ensure that every bend can achieve the desired effect. In addition, it also has the automatic calculation function of multiple bending steps, which can intelligently plan the optimal bending steps according to different workpiece requirements.
- Perfect data management: With the “one-key recovery” machine parameter function, parameter backup and recovery can be realized. Equipped with a USB interface for convenient data transmission and backup. Supports RF-Link connection function, which can refresh software backup data, and can use a computer or notebook to upgrade software and backup data through wireless interconnection.
- Thoughtful online help: It has rich online help functions and pop-up alarm prompts. Online help can provide continuous guidance for operators, and the interactive pop-up alarm prompt box can issue alarms in time at key nodes to remind operators to pay attention to potential problems, effectively avoiding wrong operations and accidents.
- High-precision control: The standard 5-axis electro-hydraulic servo machine tool (Y1-Y2-X-R-V) can accurately control the movement of multiple axes to ensure the movement accuracy and synchronization of each axis during the bending process. With the functions such as automatically calculated deflection compensation, high-precision bending operations can be achieved to ensure the bending accuracy and quality of the workpiece.
- Good compatibility: As a standard universal system, it has high compatibility and can be adapted to a variety of brands and models of bending machines to meet the equipment needs of different users.
Cybelec Ct15 Controller
- Intuitive operation interface: Equipped with a 15-inch high-resolution color touch screen, it has a clear display and is easy to operate, providing a good visual experience and a convenient interactive method. The interface design is concise and clear, in line with ergonomic principles, allowing operators to quickly get started, reducing training time and operating errors.
- Powerful programming function: Supports multiple programming methods, such as digital programming, graphic programming, etc. Digital programming has detailed dynamic text prompts, which is convenient for operators to accurately input parameters; the graphic programming function is more intuitive, and can automatically give bending plans without manually determining the bending order. It can also perform 2D bending simulation to help operators understand the processing situation in advance, avoid errors, and improve programming efficiency and processing accuracy.
- High-precision control: It can accurately control the movement of multiple axes, such as the slider axis and back gauge axis of the bending machine, to ensure the high precision and synchronization of the movement of each axis. Through advanced algorithms and control technologies, precise control of parameters such as bending angle, pressure, speed, etc. is achieved to ensure the bending accuracy and quality of the workpiece. In addition, it also has an automatic deflection compensation function, which can automatically adjust the deflection of the machine tool according to the material, thickness, length and other factors of the plate, further improving the bending accuracy.
- Perfect data management: It has parameter backup and recovery functions, and can easily transfer and backup data through the USB interface to ensure the safety and recoverability of machine tool parameters. It also supports RF-Link connection function, which can use a computer or notebook to upgrade software and backup data through wireless interconnection, facilitating equipment maintenance and management.
- Intimate online help: It has rich online help functions and pop-up alarm prompts. Online help can provide continuous guidance for operators to help them better understand and use the various functions of the system. The interactive pop-up alarm prompt box can issue alarms in time at key nodes to remind operators to pay attention to potential problems, such as tool wear, machine tool failure, etc., effectively avoiding wrong operations and accidents, and ensuring the safety of equipment and personnel.
- Good compatibility: As a standard universal system, it can be adapted to a variety of brands and models of bending machines, with high compatibility and versatility, can meet the equipment needs of different users, and provide users with more choices and convenience.
- Multi-language support: Supports multiple languages, making it easier for users from different countries and regions, reducing language barriers and improving the internationalization of the system.
1.3 Italian ESA Controller
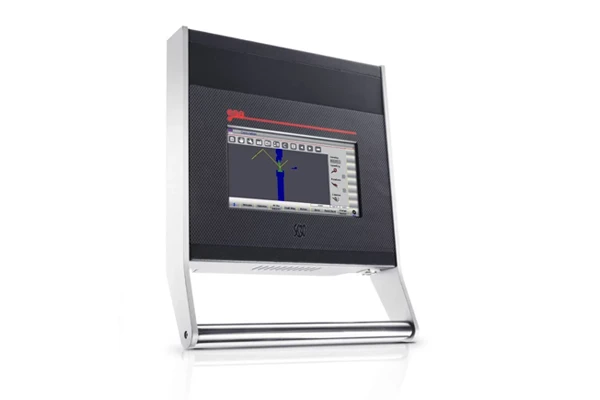
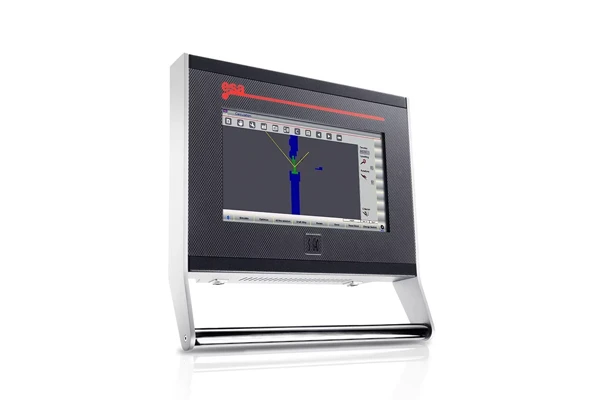
ESA 630 Controller
- Flexible number of control axes: standard can control (4 + 1) axes, the basic configuration is (y1 – y2 – x1 – r1) or (y1 – y2 – x1 – x2), etc., and can also customize input or output, freely define axis type, and the table compensation (v) axis is standard configuration, which can realize precise control of multiple moving parts of the machine tool.
- Intuitive operation interface: equipped with a 10-inch 1024×600 high-definition color touch control screen, clear display and convenient operation. The full touch screen design combined with the two-dimensional graphic programming interface can display and edit more bending data on one page, which is convenient for operators to set parameters and write programs.
- Powerful programming function: It has two modes of data programming and graphic programming, and is equipped with graphic programming software. It can automatically calculate the bending process and has anti-collision interference detection function, which can effectively avoid programming errors and equipment damage, making the bending process simpler and more efficient.
- Comprehensive calculation functions: It can perform expansion length calculation, upper/lower mold library graphics (supporting polygonal molds, telescopic molds, arc molds, gooseneck molds, etc.), graphical or numerical arc bending calculations, workbench deformation compensation, bending pressure calculations, rack deformation coefficient calculations, and angle correction databases, providing a strong guarantee for accurate bending.
- Rich auxiliary functions: It has a diagnostic page, alarm history, multiple language selections, and online help functions to facilitate operators to perform equipment maintenance and troubleshooting. In addition, the hardware configuration can be modified directly on the CNC, which is convenient and fast.
- Diverse communication interfaces: It has PLC safety communication function (communication with Pilz, Lazer, Safe, etc.), interfaces include RS232, CANbus, LAN, VGA, USB×2, etc., which can be easily connected and data transmitted with other devices, and also supports electric bending and dual-machine linkage functions, and dual-machine linkage does not require a synchronization card.
ESA 640 Controller
- Excellent operation interface: It adopts 15.6-inch LCD TFT SXGA color display, anti-glare resistive touch screen, supports multi-touch, clear display, sensitive and convenient operation1. The interface is based on Windows 10 operating system, and the full touch screen design is combined with a 2D graphic programming interface, which is simple and intuitive and easy to use.
- Powerful programming function: It has an interactive 2D graphic editor, which can easily input and edit workpiece and mold data. It can automatically identify the best bending sequence and can also perform offline programming on a standard PC to improve programming efficiency and reduce interference with production. In addition, it has an automatic bending sequence optimization function. Through the “touch design” CAD to draw the workpiece contour, the system automatically finds the best bending solution and checks for collisions.
- Multi-axis control capability: 4+1 axes can be controlled as standard, and can be expanded to 6+1 axes at most. It can accurately control and arbitrarily combine multiple axes of various types of bending machines, such as conventional mechanical and hydraulic bending machines, synchronous hydraulic bending machines, servo-controlled hydraulic single-cylinder bending machines, electric bending machines, tandem bending machines, etc.
- Rich interface configuration2: Equipped with 1 Ethernet port (expandable to 2), 2 RS-232 serial ports, 2 USB 2.0 ports, 4 analog inputs and 2 analog outputs and 1 CANopen port, it is convenient to connect and transmit data with other devices, and can connect external devices such as thickness detectors, process angle measurement units, robot interfaces, etc. to achieve more complex functions.
- Multi-language support: Supports 25 languages, which is convenient for users in different countries and regions and eliminates language barriers.
- Advanced compensation technology: With dynamic crowning (active crowning) function, the deformation of the machine tool during bending is detected in real time through strain gauges, potentiometers or other sensors, and compensated immediately through the CNC-controlled hydraulic cylinder to ensure that the bend always maintains a perfect straight line. At the same time, it is able to measure the bending angle and compensate “real time”, detect bending errors, correct the bending without removing the workpiece from the machine if the machine allows, and compensate for the springback of the material.
- Remote support function: The entire ESA S640 series provides remote diagnostic services, which allows manufacturers to determine the cause of the installed machine failure and change the CNC settings to restore the optimal operating state, facilitating the maintenance and management of the equipment.
- PLC programmable: Equipped with an open PLC, manufacturers can use IEC 61131-3 or “C” language to develop special machine functions, increasing the flexibility and scalability of the system.
The following aspects should be considered when choosing DELEM, ESA and Cybelec:
Convenience of operation
- DELEM: User-friendly interface, easy operation, mainly graphical programming interface, many models have touch screen, such as DA-58T has high-definition color TFT display and industrial multi-touch technology, intuitive operation, easy to use for workers without much operating experience.
- ESA: The operating interface is also relatively simple, such as ESA 640 uses a 15.6-inch color display and anti-glare resistive touch screen, based on Windows 10 system, 2D graphical programming interface is simple and intuitive, but its overall operation convenience is slightly inferior to DELEM4.
- Cybelec: It is highly professional, the operation is relatively complex, and it has certain requirements for operators. Operators need to have certain professional knowledge and experience to better play its functions.
Programming functions
- DELEM: It has powerful programming functions. For example, DA-58T can provide 2D graphics programming, automatic calculation of bending process and collision detection, etc. It can also automatically calculate the position of all axes and simulate the bending process2.
- ESA: It has an interactive 2D graphics editor that can automatically identify the best bending sequence and supports offline programming, which can improve programming efficiency.
- Cybelec: PC1200 2D and PC1200 3D offline programming software are powerful and can perform offline programming and bending simulation on the computer. However, the convenience of online programming may not be as good as DELEM and ESA4.
Control accuracy and performance
- DELEM: The use of high-precision control algorithms and high-performance processors can ensure high precision and high stability of machine tool processing. DA-69T and DA-66T are suitable for bending processes that require high precision.
- ESA: Taking ESA 640 as an example, the standard configuration can control 4 + 1 axes, which can be expanded to 6 + 1 axes at most. It has precise multi-axis control of various bending machines, and advanced compensation technologies such as dynamic crown shape to ensure bending straightness.
- Cybelec: The product can realize electro-hydraulic servo synchronous control. For example, DNC 880 is a high-end electro-hydraulic servo bending machine CNC system, based on modular architecture design, with high control accuracy and performance.
Price and cost performance
- DELEM: The product is usually expensive, but because of its comprehensive functions and good stability, it is cost-effective for companies with high requirements for performance and convenience and sufficient budget.
- ESA: The price is relatively moderate, the functions are relatively balanced, and a good balance is achieved between performance and price. It is a good choice for companies with limited budgets but want better performance.
- Cybelec: The price varies depending on the specific model. The high-end model is more expensive, but its precision and professionalism are strong. For professional sheet metal processing companies, if they can give full play to its functions, the cost-effectiveness can also be reflected.
2 How to choose the valve group for Press Brake?
When choosing a Press Brake valve group, you must choose the Deli brand. The Chinese brand has not yet reached the standard in terms of positioning contr When choosing a bending machine valve group, you must choose the Deli brand. The Chinese brand has not yet reached the standard in terms of positioning control accuracy. The German brands Rexroth and HAWE have their own characteristics, which can be considered from the following aspects:ol accuracy. The German brands Rexroth and Hawe have their own characteristics, which can be considered from the following aspects:
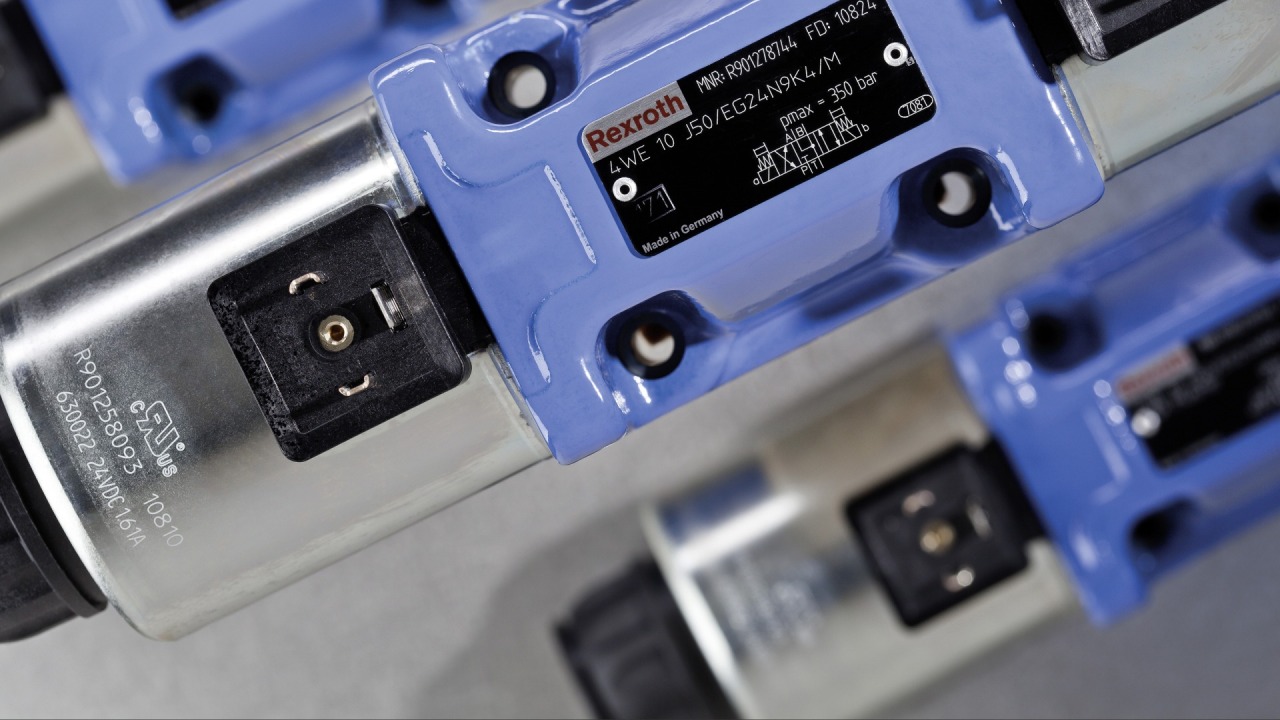
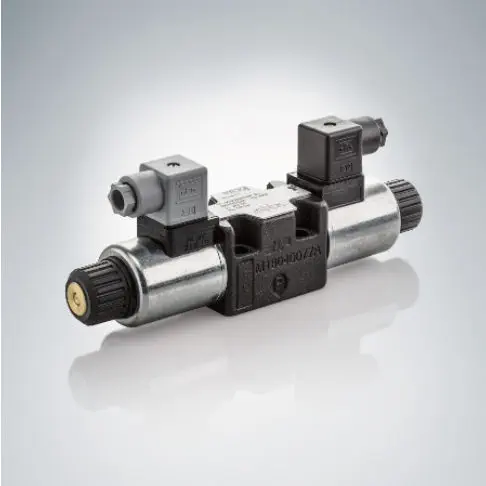
Performance
- Rexroth: It is a leading company in the global hydraulic industry, with advanced technology and rich product types to meet the needs of different scenarios. Its valve group has the advantages of high pressure resistance, low internal leakage, and strong interchangeability, and is suitable for demanding industrial environments. In terms of control accuracy, with advanced control algorithms and high-precision sensors, it can achieve precise flow and pressure control to ensure high-precision processing of the bending machine.
- HAWE: It is characterized by an all-steel structure of the valve body, high pressure (up to 700bar), small size, long life, no leakage, integration, and good reliability. Its valve group has stable performance under high pressure environment and can adapt to harsh working conditions. In terms of flow control, the design of the HAWE valve group can achieve relatively precise flow regulation to meet the flow requirements of the bending machine at different working stages.
Quality and reliability
- Rexroth: With a strict quality control system, its products have been rigorously tested and inspected, and have proven their reliability in millions of hours of operation. Its brand has a good reputation and is widely used in major projects around the world, such as the Shanghai World Expo and the National Grand Theater.
- HAWE: Passed ISO9001 quality certification and has the most advanced processing and testing equipment in the industry in Europe. Its products have exquisite manufacturing technology and reliable quality, and are widely used in the fields of mobile hydraulics and industrial hydraulics.
Installation and maintenance
- Rexroth: The new hydraulic valve series adopts ISO 7368 standard mounting holes, applies modular design concepts to hydraulic systems, increases flexibility for future modifications, and replaces the logic cover to adapt the function to new needs. Its products have a large market share, a complete after-sales service network, and maintenance personnel can easily obtain relevant technical information and spare parts, and the maintenance cost is relatively low.
- HAWE: The product structure is compact and the installation space requirement is relatively small, which is convenient for installation in the limited space of the bending machine. The maintenance of its products is also relatively simple. Due to the all-steel structure of the valve body, it is not easy to have corrosion and other problems, which reduces the maintenance workload. However, HAWE’s domestic market share is relatively small compared to Rexroth, and the after-sales service network in some areas may not be perfect, and the supply of spare parts may not be as timely as Rexroth.
Price
- Rexroth: As a leading brand in the industry, its product prices are usually higher. However, its products have excellent performance and reliable quality. Considering its service life and maintenance cost, it is still cost-effective for large enterprises or users with high requirements for equipment performance.
- HAWE: The price is relatively moderate compared to Rexroth, which can provide users with better performance and quality. At the same time, it has certain advantages in price. It is a good choice for users with limited budgets but who want to obtain high-performance valve groups.
In summary, if the enterprise focuses on brand awareness, technological advancement, control accuracy and the perfection of the after-sales service network, Rexroth is a better choice; if the enterprise has high requirements for the product’s high pressure resistance and compact structure, and hopes that the price is relatively moderate, HAWE has more advantages. In addition, users can also refer to other users’ experience and evaluation according to actual needs and budget to make a more appropriate decision.
3.Automation Selection
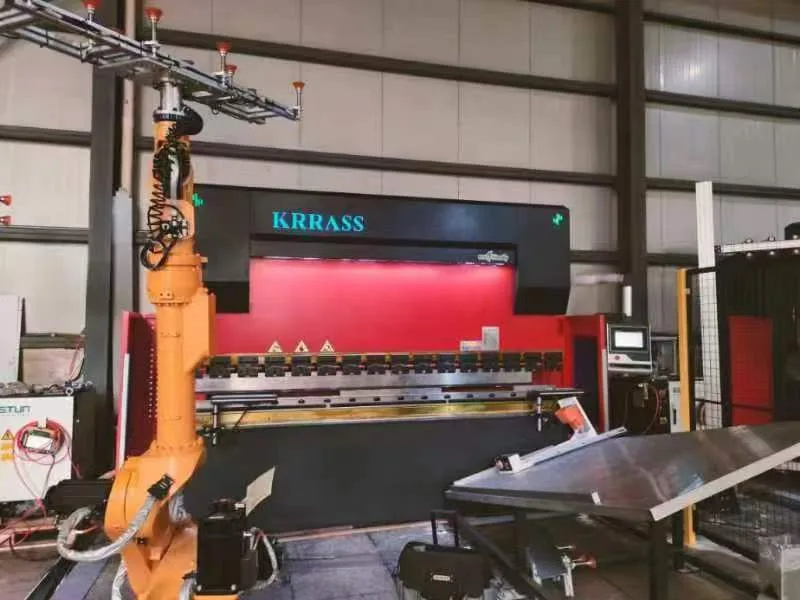
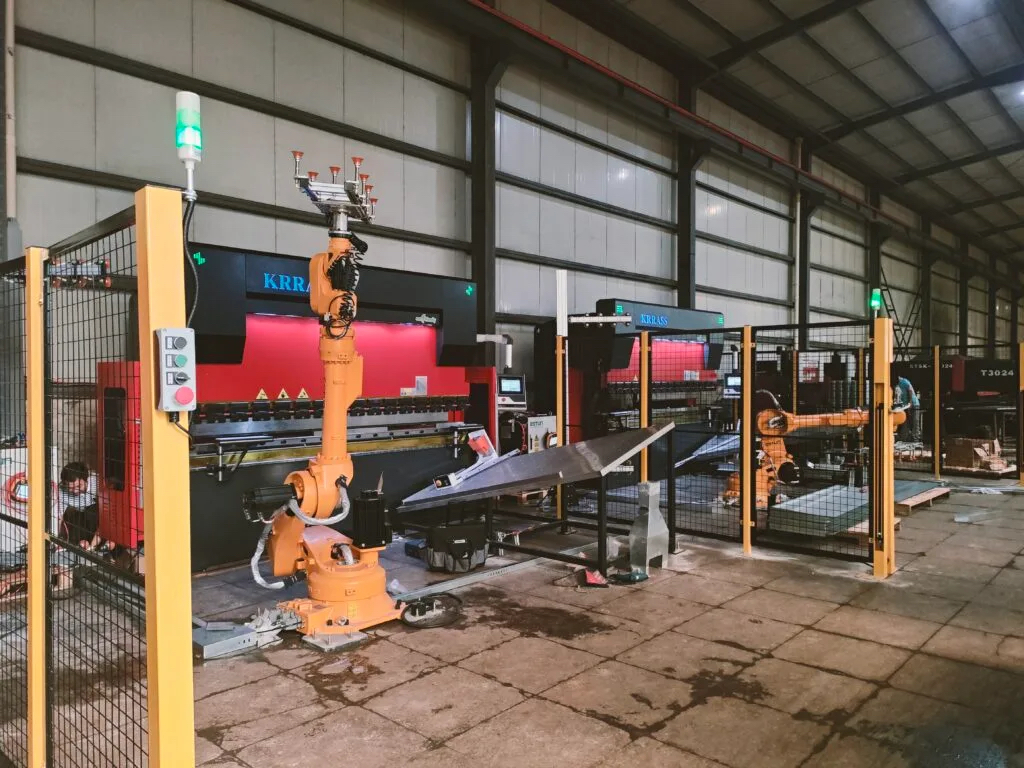
- High degree of CNC: With CNC electro-hydraulic synchronous design, the CNC system can accurately control the bending angle and position, can easily cope with complex-shaped workpieces, and reduce the impact of manual experience on bending accuracy and efficiency. It can also realize the rapid switching of workpieces of different shapes and sizes, improve production flexibility, reduce the difficulty of operation, and non-professionals can also easily get started.
- Advanced synchronous control technology: CNC electro-hydraulic synchronous technology can realize synchronous control during the bending process to ensure efficient and reliable production. It can not only improve production efficiency, but also greatly reduce the breakage rate of workpieces, reduce repeated operations, save production costs, and ensure the accuracy of bending angles and depths, laying a good foundation for subsequent processing.
- Strong flexible production capacity: The flexible bending unit adds industrial robots to the bending machine, which can realize multi-station and multi-process continuous processing. It can flexibly configure the number of stations and process arrangements according to actual needs, greatly meet different processing needs, and is suitable for batch production. It also provides convenience for small batch and multi-variety production, and can realize bending, punching, forming and other processes with one machine.
- The automatic stacking function is practical: the workpieces are automatically stacked after bending, and the industrial robot takes out the workpieces and accurately stacks them to the designated position after bending, which greatly reduces the labor intensity, reduces manual operation errors, improves the bending efficiency, and can achieve 24-hour uninterrupted production, and ensures that the workpieces are neat and orderly, which is convenient for subsequent transportation and management.
- Convenient mold replacement: Equipped with precision fast fixtures, the mold can be installed and replaced from the bottom and side of the fixture in both directions, effectively reducing the mold replacement time, improving production efficiency, and having a greater carrying capacity.
- The rear stopper system is accurate and stable: the novel and unique double linear guide structure is adopted to ensure excellent positioning accuracy, and the multi-stage gear design increases the positioning range.
- Accurate throat deformation compensation: The throat deformation compensation device can accurately measure the deformation and feedback compensation to ensure bending accuracy, and can also effectively prevent non-standard workpieces from colliding with the interference detection unit
- High mechanical compensation accuracy: The high-precision wedge compensation device is controlled by the CNC system to obtain precise compensation to ensure high-quality bending accuracy.
- The front support is flexible and practical: the mobile front support moves along the linear guide rail and can be docked at any position to assist the bending work and make the work more efficient.
- Energy-electric hybrid technology is energy-saving and efficient: it adopts the oil-electric hybrid servo motor pump control system with independent intellectual property rights, which has the advantages of energy saving, environmental protection, high efficiency and low noise. The servo motor only consumes electricity when bending the sheet, saving 50%-70% of the power consumption of traditional bending machines; it only requires 1/4 of the hydraulic oil of traditional CNC bending machines, reducing the pollution of waste oil treatment to the environment; the servo motor responds quickly, shortens the working cycle, and improves the efficiency of machine use; the noise is low, allowing workers to work in an environment without noise interference.
- The CNC system is powerful: for example, it adopts the Italian ESA 630 CNC system, which has a form-filling programming mode with real-time automatic checking, direct angle programming, automatic calculation of R-axis position, automatic calculation of mechanical compensation A-axis position, 2D graphic editing of upper and lower dies, preview of workpieces, programming and other functions. It can also automatically calculate the bending process and has a manual bending page. All programs and parameters can be saved in the local memory and copied to a mobile storage device, and complete offline programming software is provided.